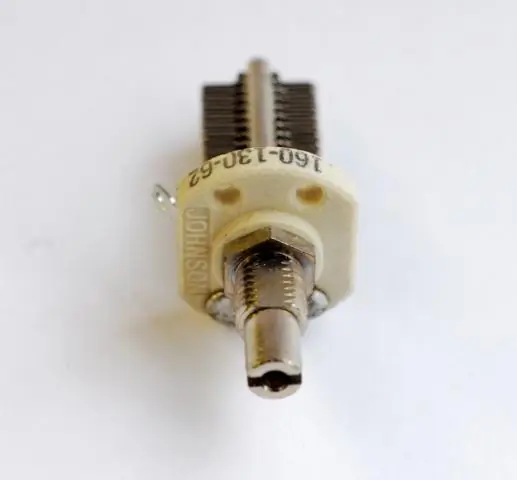
Tabla de contenido:
- Paso 1: marcar el centro para los orificios piloto
- Paso 2: Dibuja algunos círculos
- Paso 3: líneas de marcado para las placas del estator
- Paso 4: Cortar
- Paso 5: Marcar los agujeros para el estator
- Paso 6: marcar el círculo interior
- Paso 7: Cortar el arco
- Paso 8: Perforación
- Paso 9: girar con un taladro
- Paso 10: Dar forma a las placas del estator
- Paso 11: de esto a aquello
- Paso 12: Fabricación de sus propias lavadoras
- Paso 13: Acabado de sus lavadoras
- Paso 14: Conjunto de rotor y estator
- Paso 15: La Vivienda
- Paso 16: el aislante
- Paso 17: Tapas de frascos de plástico
- Paso 18: Terminar
2025 Autor: John Day | [email protected]. Última modificación: 2025-01-23 14:40
Estaba construyendo un juego de cristal para mi hijo, pero se detuvo. Cuando descubrí que no tengo un condensador variable en mi pila de basura, rescatar uno de una radio vieja no era una opción. Dado que la mayoría de las radios nuevas utilizan sintonización analógica. Y los que tienen condensadores variables de aire son muy raros y son artículos de coleccionista. Una vez leí un artículo sobre la construcción de un condensador variable de aire. Así que decidí construir la mía propia a partir de trozos de láminas de aluminio y de cosas que se encuentran fácilmente en la casa. Si tienes un taladro, unas tijeras, una lima y un poco de papel de lija. Puedes construir este fácilmente. No requiere mucha habilidad.:-) Hice la mía con láminas de aluminio de 1,5 y 2 mm de espesor. La carcasa es de un disipador de calor de aluminio, también me las arreglo para sacar 3 piezas de pernos con algunas tuercas de mi caja de basura. El casquillo de plástico que también actúa como aislante es de un bolígrafo de plástico y algunas tapas de frascos de plástico. También hice mis propias arandelas / espaciadores de la hoja de aluminio de 2 mm de espesor. Los contactos del rotor que también actúa como tensor. Eran de un temporizador de lavadora roto. Puede experimentar con el número de placas y con el tamaño de los espacios de operación agregando más placas y arandelas en el rotor y el estator.
Paso 1: marcar el centro para los orificios piloto
En este paso haremos las medidas, coloque la plancha de aluminio plana sobre su banco de trabajo. De un lado a otro, dibuja un cuadrado de 5 cm x 5 cm. Usar un objeto puntiagudo como un clavo o una lima. Toma el centro y haz un agujero con un clavo pequeño. Haga un agujero por cada 5 centímetros a lo largo de la línea recta como se muestra en la foto.
Paso 2: Dibuja algunos círculos
Aquí dibujaremos círculos en la hoja. Podemos dibujar círculos perfectamente usando una brújula. Si no tienes una brújula, puedes improvisar, clavando dos clavos pequeños en un pequeño trozo de madera. Inserte un clavo en el agujero que hizo en la hoja y gírelo. Es importante que los círculos no se superpongan. Para que tengamos suficiente espacio cuando las recortemos más tarde. Puedes hacer tantos círculos como quieras, si tienes suficiente hoja de aluminio. Es mejor tener un repuesto si hiciste un corte incorrecto. Que repetir el mismo proceso si te quedaste sin piezas a la mitad de tu proyecto.
Paso 3: líneas de marcado para las placas del estator
Usando un tri-cuadrado, dibuje una línea desde el borde de la hoja hasta el centro del arco. (El que apunta con un bolígrafo en la foto) Es importante hacer esto, porque necesitamos que cada parte tenga un tamaño uniforme. Y esto también nos sirve de guía cuando los recortamos.
Paso 4: Cortar
Con unas tijeras grandes y un agarre fuerte. Puede cortar fácilmente todas las piezas. Y luego aplana cada pieza con un mazo de goma. También puedes usar un martillo. Pero sé muy gentil.
Paso 5: Marcar los agujeros para el estator
Consigue una pieza y dibuja una línea desde el centro. Yendo a la esquina izquierda. Obtenga la línea central (de esquina a arco) y haga un agujero en ella. Marque esta pieza como patrón. Ponlo encima de otra pieza. Y haz un agujero en la segunda pieza debajo de él. Usando el agujero de la primera pieza como plantilla. Da la vuelta al patrón y haz el segundo agujero. Hacemos esto porque perforaremos todas las placas del rotor y del estator de una en una. No recomiendo apilar todas las piezas y perforarlas todas a la vez. La broca siempre tiende a doblarse. O puede hacerlo si tiene un taladro
Paso 6: marcar el círculo interior
Vuelve a improvisar una brújula para dibujar el círculo interior, cortando con unas tijeras desde ambos extremos, hasta el arco del círculo interior. Tenga mucho cuidado de no cortarlo hasta el centro.:-) cuando todas las piezas están cortadas. Vuelva a aplanarlos con un mazo de goma.
Paso 7: Cortar el arco
Aquí cortaremos el arco que aún conecta el rotor y las placas del estator. Siempre puedes cortarlo con tijeras, pero es más fácil y rápido si usas un cincel curvo. (el que usan los talladores de madera) Tengo uno, pero no quiero arruinarlo.:-) Así que hice uno con una pipa pequeña. Afile en un extremo con una lima. Y quitó la mitad. Para que quede como un cincel curvo. No se confunda al cortar. El rotor debe tener la parte con un agujero. (Aquí es donde las piezas de repuesto son útiles:-)
Paso 8: Perforación
Ahora que tenemos nuestro rotor y estator. Es hora de agrandar los agujeros. Con el uso de un taladro. Busque pernos (3 piezas) con tuercas (utilicé 12 piezas de tuercas porque quité la cabeza de cada perno para poder abrir mi varicap en ambos extremos). Usé una de 4 mm. broca. Encuentre pernos que se ajusten perfectamente a los orificios, especialmente para el rotor
Paso 9: girar con un taladro
En esta etapa haremos arcos perfectos de nuestras placas de rotor. Y para eliminar rebabas y bordes afilados. Con la ayuda de un taladro y una lima gruesa y un poco de papel de lija, apile todas las placas del rotor una frente a la otra formando un círculo. (Hacemos esto para evitar vibraciones cuando los giramos con un taladro) Insertar el perno y apretar la tuerca. Insertar el extremo del perno en el mandril del taladro. Como una broca normal. Encienda el taladro y use la lima para suavizar los lados de las placas del rotor. Tenga mucho cuidado de poner el taladro a baja velocidad. No presione el interruptor del taladro durante mucho tiempo. (la tuerca puede aflojarse) si esto sucede, invierta la dirección del taladro. Terminar con un papel de lija fino
Paso 10: Dar forma a las placas del estator
Daremos forma a las placas del estator en esta parte de mi instructable. Como lo que hicimos con nuestras placas de rotor. También apilaremos todas las placas del estator. Inserte los pernos en cada orificio y apriete las tuercas. Si tiene un tornillo de banco, mucho mejor. Si puede ver la foto con claridad. Coloreé las partes a quitar con un bolígrafo negro. O simplemente siga el arco y evite la cabeza del perno y la tuerca. Tenga paciencia, puede hacer esto con una lima gruesa. Recuerde que no es tan difícil trabajar con el aluminio.:-)
Paso 11: de esto a aquello
En esta etapa, sus piezas deben verse como la tercera pieza de esta foto. Bien hecho. En este punto también puedes quitar la pintura. Si tienen pintura. Y vuelva a comprobar si hay curvas o si alguna vez están torcidas.
Paso 12: Fabricación de sus propias lavadoras
Haga sus propias arandelas / espaciadores. De un calibre más pesado o de la misma hoja. Pero necesitará 2 uds. De arandelas / espaciadores para cada hueco. Recomiendo usar el mismo calibre que las placas del estator y del rotor, un calibre más ligero es mucho más fácil de cortar, cortar una tira de aluminio de aproximadamente 1 cm. amplio. Taladre agujeros con la misma broca que usó para las placas del estator y del rotor. Corta la tira en cuadrados. Asegúrate de que el agujero que perforaste esté en el centro. Inserte el perno con su cabeza hacia arriba. Luego corte las esquinas usando la cabeza del perno como guía, como se ve en la foto.
Paso 13: Acabado de sus lavadoras
Como lo que hiciste con las placas del rotor. Golpéalos suavemente para aplastarlos. Apílelos, inserte el perno, apriete la tuerca. Y de nuevo con el uso de un taladro darles vuelta y alisar con una lima y terminar con un papel de lija fino.
Paso 14: Conjunto de rotor y estator
Retire la cabeza de cada perno. Ponga una tuerca en un extremo de cada perno. Gire la tuerca hasta 5 cm. del perno sobresale de la tuerca. Tome uno de los pernos, insértelo en una placa del estator seguida de dos arandelas. Y nuevamente una placa de estator y dos arandelas. Repite este paso hasta que termines. Deje suficiente espacio para 2 pernos y dos arandelas y no olvide el eje donde colocar una perilla
Paso 15: La Vivienda
Hice la carcasa con un disipador de calor de aluminio rescatado de un chasis de televisión. Es más o menos de 2 mm. grueso. Coloqué el rotor y el estator encima. dejando una distancia de 1 mm. Entre el rotor y el estator. Marque los 3 orificios a perforar utilizando los orificios del rotor y del estator como plantilla. Luego, taladre todos los orificios con la misma broca utilizada para el rotor y la placa del estator. Luego lo corté en forma triangular y redondeé todas las esquinas.
Paso 16: el aislante
Busque algo que aísle el eje del rotor de la placa final / chasis. Como, por ejemplo, una manguera de goma de una línea de combustible de un automóvil. Ya que no tengo auto. Solo usé un bolígrafo de plástico como buje. Nota: busque el bolígrafo correcto antes de agrandar el orificio superior. No taladre hasta que tenga su buje:-)
Paso 17: Tapas de frascos de plástico
Corta dos plásticos de forma triangular de las tapas de los frascos. O cualquier plástico de su elección. Este plástico aislará el contacto del rotor de la carcasa de aluminio. Solo pegué mi contacto temporalmente. Luego lo cambiaré con un conector de cobre. Las que parecen arandelas como las que se utilizan para la conexión a tierra.
Ahora solo coloca los dos plásticos triangulares en ambos lados. Seguido de los dos de aluminio de forma triangular y ya está. Recuerde que si tiene dos placas de estator, debe tener tres placas de rotor. 4/5, 5/6 y así sucesivamente. Espero que este instructivo sea de mucha ayuda. Gracias:-)
Paso 18: Terminar
Aquí está el condensador variable terminado. Instalado en un receptor de onda corta de cristal.
Recomendado:
Controlador Arduino HRV (Intercambiador de aire doméstico) con economizador de aire: 7 pasos (con imágenes)
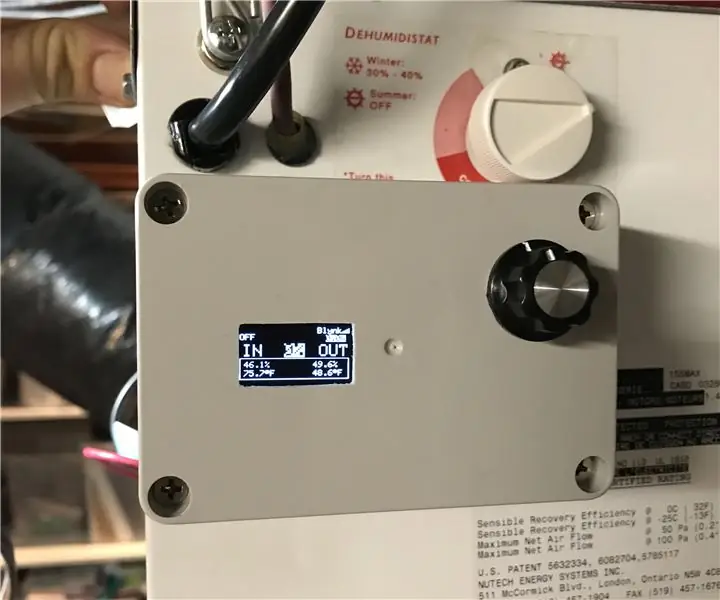
Controlador Arduino HRV (Intercambiador de aire doméstico) con economizador de aire: Controlador Arduino HRV con economizador de aire Así que mi historia con este proyecto es que vivo en Minnesota y mi placa de circuito está frita en mi LifeBreath 155Max HRV. No quería pagar los $ 200 por uno nuevo, siempre quería algo con un economizador de aire sin
Altavoz Bluetooth portátil hecho de madera de desecho: 9 pasos (con imágenes)
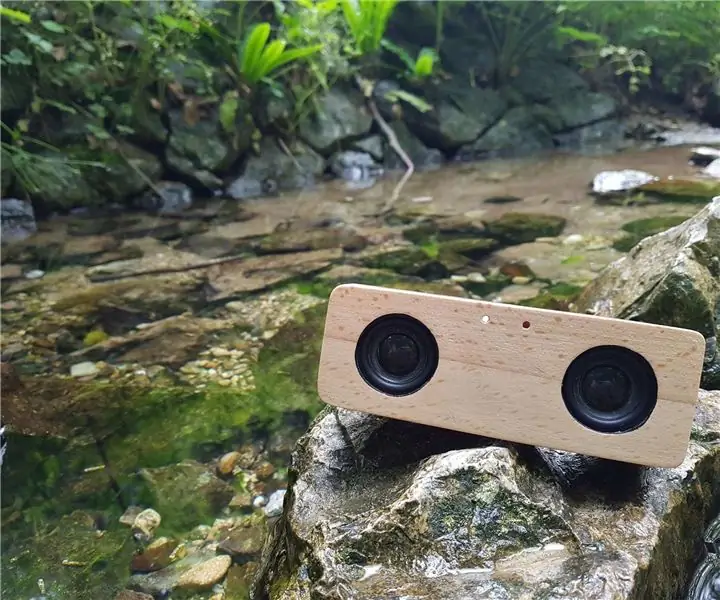
Altavoz Bluetooth portátil hecho de madera de desecho: Hola a todos, ha pasado mucho tiempo desde la última vez que publiqué aquí, así que pensé en publicar mi proyecto actual. En el pasado, hice algunos parlantes portátiles, pero la mayoría de ellos estaban hechos de plástico / acrílico, ya que es fácil de trabajar y no requiere
¡Aire más frío! por menos dinero! ¡Sobrealimentación del aire acondicionado!: 14 pasos (con imágenes)
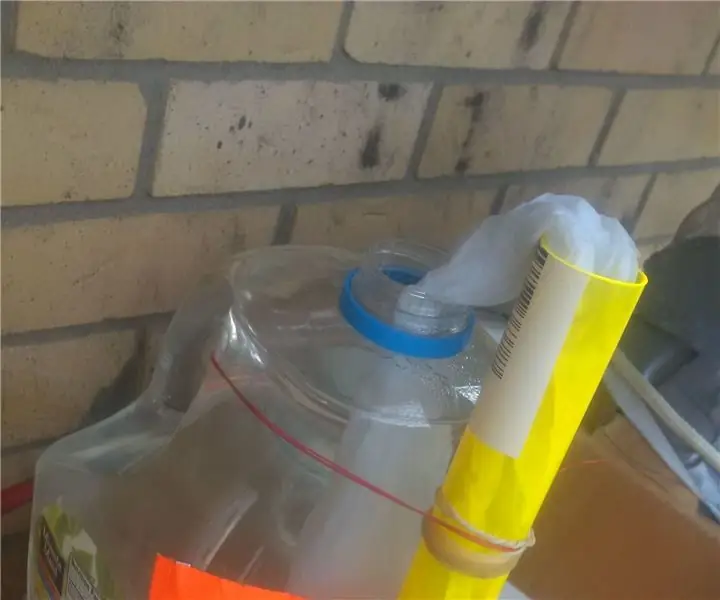
¡Aire más frío! por menos dinero! ¡¡Sobrealimentación del acondicionador de aire !!: Puede obtener un enfriamiento mejorado y reducir los costos de energía con este método. Un acondicionador de aire funciona comprimiendo un refrigerante gaseoso hasta que se condensa en el condensador (lo adivinó) en el lado exterior. Esto libera calor al exterior. Entonces cuando eso
Obtenga mucho dinero por baterías de desecho: 3 pasos (con imágenes)
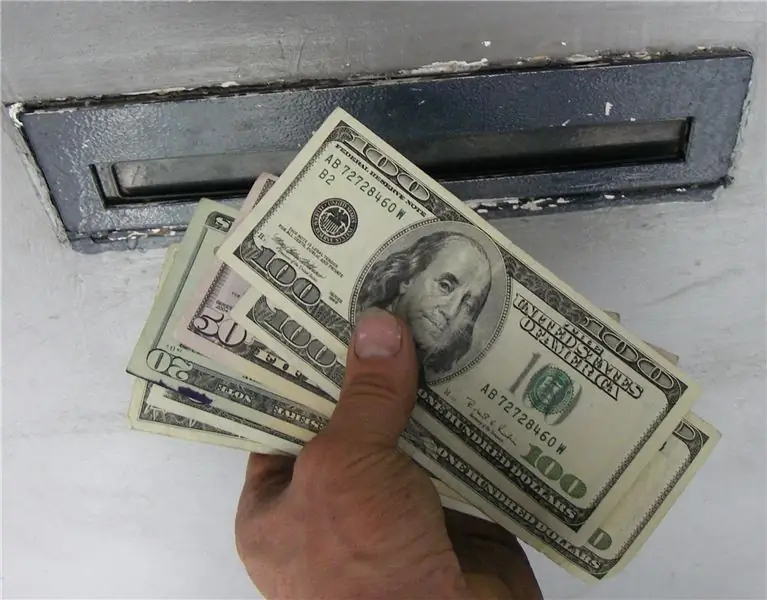
Obtenga mucho dinero por baterías de desecho: Me acaban de pagar $ 300 en efectivo por dos docenas de baterías viejas de plomo-ácido. He aquí cómo. Muchos lectores se preguntan: ¿De dónde saco las baterías agotadas? Los coches nuevos estropean las baterías bastante rápido porque el coche
Reparación de un condensador: condensador variable de aire pequeño en el transmisor: 11 pasos
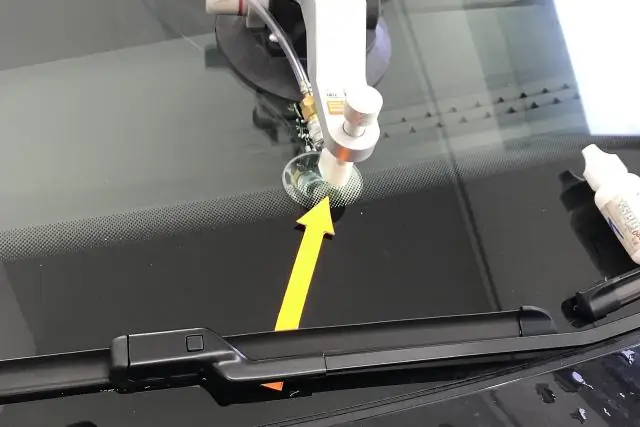
Reparación de un condensador: condensador variable de aire pequeño en el transmisor: Cómo reparar un condensador variable de aire de cerámica y metal pequeño como los que se encuentran en los equipos de radio antiguos. Esto se aplica cuando el eje se ha soltado de la tuerca hexagonal o "pomo" presionado. En este caso la tuerca que es un destornillador-ajuste