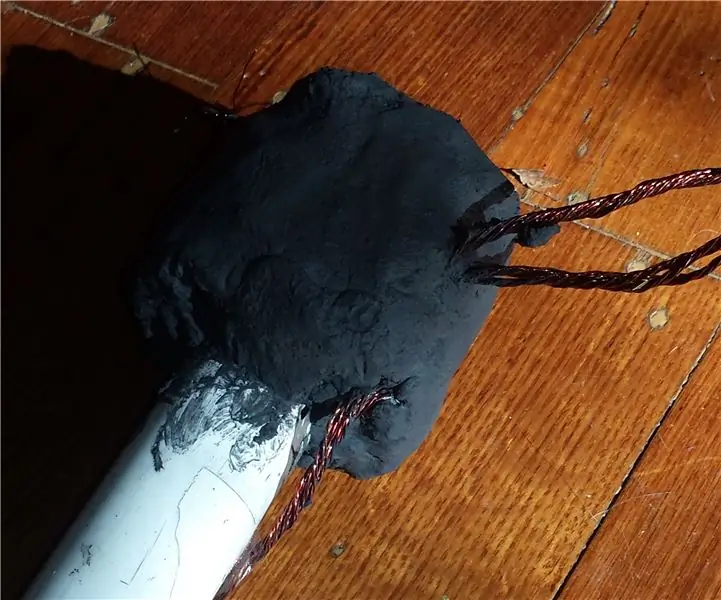
Tabla de contenido:
- Paso 1: ¿Qué es la ferrita?
- Paso 2: ¿Por qué no puedo encontrar nada para moldear mi propia ferrita?
- Paso 3: Ok, pero ¿cuáles son los usos de mi ferrita casera?
- Paso 4: pros y contras
- Paso 5: ¿Cómo se fabrica y qué necesito?
- Paso 6: Cómo usarlo en material sensible a la humedad o para sellar en dispositivos electrónicos
- Paso 7: ¿Cómo puede ayudar?
- Paso 8: ¡Actualiza
- Paso 9: ¡Actualiza! Quizás el último de todos…
2025 Autor: John Day | [email protected]. Última modificación: 2025-01-23 14:40
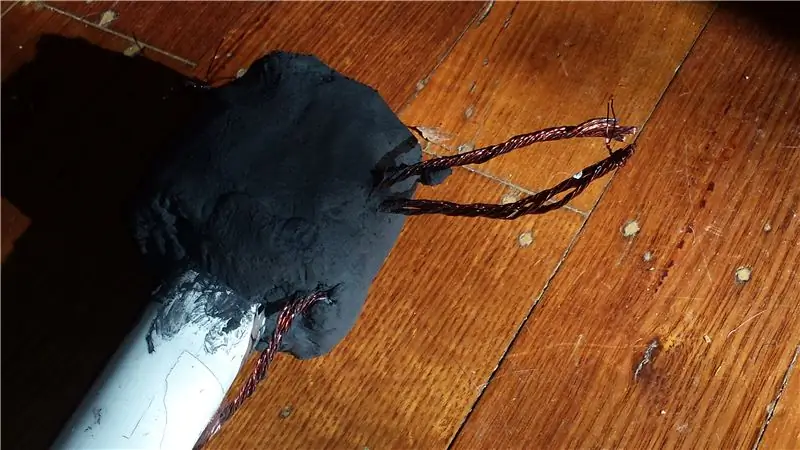
Actualización 2018-09-05: Lo hice de nuevo, ¡disfrútalo! Actualización 2015-07-03: Encontré la solución correcta, ¡revisa el último paso! ¿Cómo comenzó todo? Tal vez te preguntes, así que te lo haré saber;)
Es posible que haya visto mi Instructable para el calentador de inducción simple y con el primero sentí la necesidad de encontrar formas de mejorar la potencia de salida.
Las personas con mentalidad electrónica ya sabrán que la ferrita se usa ampliamente para pequeños transformadores, bobinas de choque e incluso antenas.
Con esta amplia variedad, es obvio que encontrará muchos tipos diferentes de ferrita diseñados para un trabajo específico.
Factores como el flujo magnético, la saturación del núcleo y el rango de frecuencia son solo algunos de los parámetros que pueden ser importantes para un rendimiento adecuado.
Lo que uso para mis necesidades ni siquiera puede ser considerado ferrita por un profesional, pero hace el trabajo bastante bien.
Este Instructable es un trabajo en progreso para mí, ya que lo actualizaré y completaré con imágenes "sobre la marcha", por lo que cada vez que haga un nuevo lote o pruebe una nueva receta, verá los resultados aquí, así que manténgase informado para actualizaciones
Si mi tiempo lo permite, haré la próxima ferrita durante el próximo fin de semana
Será a base de yeso y también tomaré algunas fotos y un video corto
Publique sus comentarios o mejoras y actualizaré el Instructable en consecuencia
Paso 1: ¿Qué es la ferrita?
La ferrita en el sentido comercial es una mezcla comprimida de principalmente óxido de hierro y aglutinantes.
Dependiendo de las propiedades necesarias, se añaden óxido de zinc e incluso metales de tierras raras.
Generalmente se produce bajo presiones extremas y calor dando como resultado una cerámica como el finlandés.
Puede buscar en Wikipedia para obtener información más detallada, ya que no es tan relevante para este Instructable.
Paso 2: ¿Por qué no puedo encontrar nada para moldear mi propia ferrita?
Bastante sencillo:
Solo hay un puñado de fabricantes que tienen ferrita moldeable o mecanizable en su catálogo, ¡y tratan muy bien sus fórmulas!
Además, los precios no son realmente atractivos para personas como usted y como yo.
Incluso si encuentra un proveedor, debe indicar el propósito y las propiedades magnéticas que necesita o hacer sus propios cálculos basados en las hojas de datos suministradas.
Paso 3: Ok, pero ¿cuáles son los usos de mi ferrita casera?
Como dije al principio, necesitaba algo para mi calentador de inducción que no se sature con los campos magnéticos extremos involucrados y también quería algún tipo de protección para evitar interferencias.
Con la mezcla actual (al final de los pasos) logré ambos.
No puedo recomendarlo para el uso de bobinas de HF específicas o similares, ya que no tengo forma de verificar las propiedades y los campos magnéticos con mi equipo limitado, ¡lo siento!
Pero si fabrica sus propios electroimanes, bobinas de inducción o tiene la necesidad de dirigir líneas de campo magnético en general, podría ser justo lo que necesita.
También para el blindaje general de las frecuencias de HF, debería funcionar bastante bien, haciendo posible sellar completamente un circuito en la ferrita para que no puedan ocurrir fugas (o mejor, deberían ocurrir).
Por ejemplo:
Un perno de 8 mm en mi bobina con manto de ferrita tarda unos 90 segundos en ponerse al rojo vivo, con un manto de ferrita alrededor de la bobina de trabajo, el tiempo se reduce a menos de 30 segundos.
Paso 4: pros y contras
Bueno, como ocurre con todas las cosas nuevas, nunca son realmente perfectas;)
Empezaré con las cosas negativas primero:
* Es muy desordenado de producir, por lo que se recomienda usar guantes y mezclar al aire libre, ya que no desea limpiar el polvo de óxido de hierro en su cocina.
* No es fácil de mezclar ya que el óxido de hierro es muy fino y tiende a ignorar todas las uniones al comienzo de la mezcla.
* La mezcla aún no es perfecta, por lo que es posible que deba probar la mezcla en un lote pequeño para verificar si se ajusta a sus necesidades.
Ahora lo bueno:
* Puede darle la forma que necesite. * Se puede lijar o perforar cuando esté curado. * Es un buen escudo contra interferencias. * Una vez mezclado, es fácil de manipular y moldear. * No necesita equipo especial ni ingredientes costosos.
* Puede cambiar fácilmente la mezcla para ajustarla a sus necesidades.
Paso 5: ¿Cómo se fabrica y qué necesito?
Herramientas y cosas que debes tener: * Guantes de goma
* Un recipiente de mezcla adecuado: los utilizo para mezclar yeso
* Cuchara, espátula o similar para la mezcla.
* Un área que se limpia con un limpiador a presión o que no se ensucia un poco
Cosas para hacerlo más fácil:
* Un poco de paciencia;)
Ingredientes:
* Óxido de hierro: el tipo blck también conocido como Fe3O4, se usa comúnmente para colorear concreto y es bastante barato
* Yeso - Yeso de París, masilla de pared o algún tipo de resina según tus necesidades (este es el aglutinante)
* Agua si usa yeso o similar, de lo contrario consulte las instrucciones de su resina
* Óxido de zinc y otras cosas que encuentre al buscar composiciones de ferrita si siente la necesidad y las consigue a bajo precio, ¡totalmente opcional!
Cómo mezclarlo:
Primero algunas explicaciones;
Desea utilizar la menor cantidad posible de aglutinante, de lo contrario, las propiedades de su ferrita podrían no ser las esperadas.
Para aplicaciones de alta potencia, como una bobina de inducción, necesitará una capa gruesa de ferrita ya que, de lo contrario, el núcleo se saturará o podría calentarse; no hace daño usarlo demasiado grueso y siempre puede agregar más (alrededor) si la saturación es un problema, lo mismo por demasiado, ya que puede lijar o usar un archivo.
¡Mezcle solo lo que pueda manejar durante el tiempo de curado!
Tome una estimación aproximada de cuánto volumen final necesita para su proyecto y agregue otro 20% para ahorrar. Opto por la versión de yeso, ya que esta fue mi primera forma de hacerlo y porque es la más fácil.
Agregue el óxido de hierro en su recipiente de mezcla (póngase guantes ahora si se olvidó de ellos;)) seguido de aproximadamente un tercio en volumen de yeso. Mezcle bien mientras esté seco; para lotes más grandes, usar un frasco con tapa le ahorra mucho negro polvo volando alrededor!
Ahora agregue el agua y siga mezclando como lo haría con el yeso mormal para que no queden grumos.
No se preocupe si usó demasiada agua, ya que siempre puede agregar óxido y yeso.
Tenga en cuenta que esta mezcla se seca un poco más rápido y puede producir grietas en capas más gruesas, por lo que puede ser necesario trabajar en etapas pequeñas con nuevas mezclas para acumular (mantenga la mezcla seca y use solo con agua lo que necesita).
Ahora puede ponerlo en un molde o cubrir lo que necesita proteger.
Deje que se asiente en un ambiente húmedo para evitar grietas; simplemente lo envuelvo en una toalla húmeda (¡una muy vieja debido al óxido negro!).
Después de aproximadamente 2 horas, puede continuar dejándolo secar al aire libre.
¡El tiempo de curado final depende del espesor y la humedad!
Para la humedad, caliéntelo a unos 30 ° centígrados y colóquelo en un recipiente cerrado que estaba en su congelador para que se enfríe. Si no está completamente seco, verá una pérdida de niebla que se condensa en el interior de su recipiente.
Paso 6: Cómo usarlo en material sensible a la humedad o para sellar en dispositivos electrónicos
¡Solo hay una forma y esta asegurándose de que la humedad no llegue a ella!
Selle primero con pintura, resina, etc., o haga un molde para la ferrita y coloque la pieza en él una vez que esté completamente curada.
Si esa no es una opción, debe usar una resina moldeable o calcinable en lugar del yeso.
Para las composiciones 2K, esto significa que debe agregar la misma cantidad de óxido a ambos componentes de la mezcla.
Aunque el Fe3O4 no es tan reactivo, puede afectar el curado de las resinas 2K, así que primero haga un pequeño lote de prueba para asegurarse de que cura correctamente y no se calienta demasiado durante el curado.
Es muy difícil dar las proporciones de mezcla adecuadas ya que las propiedades de las distintas resinas difieren demasiado, pero voy bajando de una mezcla 50/50 hasta que noto que la mezcla se convierte en un problema o que el curado no es lo suficientemente bueno.
Pero por lo general no uso una mezcla de 35% de resina con 65% de óxido.
Paso 7: ¿Cómo puede ayudar?
Puede ayudar a perfeccionar la forma de hacer ferrita publicando sus comentarios y recetas probadas.
Agregaré más imágenes con mi próximo lote y agregaré otro paso para las mezclas recopiladas a partir de los comentarios para una referencia fácil para todos aquí.
Paso 8: ¡Actualiza

Me di cuenta por la cantidad de golpes que necesito apurar un poco las cosas para completar este instructable Después de experimentar con aditivos para reducir el riesgo de que se formen grietas durante el proceso de secado, decidí usar esta variación para un video sobre cómo hacer el ferrito.
Para darte una ventaja en la nueva receta, la resumiré aquí para que tengas una idea de lo que sucede en el video.
1. Prepárate con guantes y todo lo que necesites, verás las cosas en el video.
2. No intente seguir el video de inmediato, mírelo al menos dos veces y use el botón de pausa si soy demasiado rápido en el video.
3. ¡No lo hagas por dentro ya que el polvo negro va a todas partes!
4. Los ingredientes son:
Yeso de París - o cualquier otro yeso para modelar que tenga a mano (Yeso).
Óxido de hierro negro
Un poco de pegamento para papel de pared o, si no está disponible en su área, use pegamento para madera; esto ayuda a mantener la mezcla viable por más tiempo y ralentiza el proceso de secado, además, el producto terminado no se agrieta tan fácilmente.
Agua y algunas herramientas para mezclar y modelar: lo que funcione mejor para usted y la cantidad que gane.
5. El pegamento debe agregarse al agua primero y solo en pequeñas cantidades para el pegamento de papel de pared, el pegamento para madera debe agregarse en un volumen de aproximadamente el 15% al agua.
Podría omitir esta parte del video y preparar la mezcla de pegamento al agua por adelantado, ya que se necesita un tiempo con pegamento para papel de pared.
Haz una mezcla seca de yeso y óxido, lo hago con una cuchara.
Dependiendo de la mezcla, obtendrá un resultado bastante bueno o bastante malo en términos de estabilidad mecánica.
Intento usar 3-5 partes de yeso en 4 partes de óxido, una mezcla 50-50 parece funcionar bien, pero siempre trato de quedarme debajo para tener más ferrita que yeso en la mezcla.
Cuanto más óxido agregue, mejores serán las propiedades magnéticas del producto terminado, pero más difícil será trabajar con él y curarlo sin grietas.
Agregue agua (ya preparada con pegamento) seguida de su mezcla seca en un recipiente de mezcla adecuado y mezcle bien hasta que no queden grumos, mantenga la mezcla lo suficientemente espesa para trabajar pero no tan delgada que se escurra, a menos que haga un vaciado.
Una vez que comienzas a mezclar, el reloj corre, ya que solo tienes un tiempo limitado hasta que la mezcla se endurezca y se vuelva inutilizable.
Es mejor trabajar con lotes pequeños que pueda aplicar correctamente antes de que comience el secado inicial.
¡¡Importante!!:
¡Debe usar herramientas y recipientes limpios, ya que incluso pequeñas cantidades de mezcla curada estropearán su próximo lote!
Hará que la mezcla se endurezca mucho más rápido y puede causar grumos en la mezcla cuando se cura más rápido que el resto.
Intento lavar mis herramientas y recipientes antes de que el yeso se endurezca por completo.
Como puede ver en el video, solo hago una pequeña cantidad para colocar la primera capa en la bobina.
Lo hago de esta manera para permitir un mejor secado ya que queremos evitar que se capture demasiada humedad antes de agregar la siguiente capa.
Debe tomarse su tiempo para dejar que se seque, ya sea de forma natural o mediante el uso de un deshidratador.
Si queda demasiada humedad antes de realizar el curado final en el horno, se producirán grietas masivas.
La mejor forma es dejar que el producto terminado se seque durante unos días antes de meterlo en el horno.
Si cubre partes sensibles a la humedad, es mejor agregar una capa de pintura como barrera; para obtener mejores resultados, lije la pintura rápidamente para obtener una superficie rugosa, ya que esto ayudará a que la mezcla se pegue.
En caso de que tenga prisa, pruebe las mezclas adhesivas flexibles para baldosas de su ferretería sin el pegamento en la mezcla.
Pero primero haga algunas pruebas a pequeña escala para verificar si su mezcla produce grietas mientras se seca. La cocina o la farmacia local (a precios razonables) funcionó. ¡Pero luego me di cuenta! Agarré mis últimas cucharadas de óxido negro y lo mezclé con silicato de sodio - Waterglass. Por supuesto, siendo yo, no tomé ninguna foto o video - dispárame … De todos modos intentaré explicarlo: el silicato de sodio es otro químico "olvidado" en términos de uso doméstico. Algunos todavía lo pueden saber por el experimento químico "Jardín químico". En la forma líquida concentrada está en algún lugar entre la leche entera y miel tibia en la consistencia y transparente como el vidrio. Una vez seco, se vuelve duro como una roca, una característica que se usa para reparaciones en madera, porcelana y otras cosas como baldosas resistentes al calor. agregando un poquito de agua a esa mezcla. Hice lo mismo con Con el óxido negro. Comenzó con algunas cucharadas de óxido y agregó el silicato de sodio en pequeñas cantidades. Crea muchos grumos y bolas pequeñas, por lo que hacer esto en un pequeño molino de bolas podría ser una buena idea (aparte de la limpieza) De todos modos, si revisa los videos sobre la fundición en arena grenn, verá que la mezcla se ve casi seca pero mantiene su forma cuando se presiona; intenté lo mismo, pero al final solo usé una forma de bloque y un martillo pequeño para compactarlo. (Esto recuerda mencionar que debo sacar la mezcla de ferrita del molde después de este paso (no lo hice y fue imposible quitar el material curado del molde). Después de esto, la pieza de prueba entró en el horno durante aproximadamente 90 minutos a temperatura máxima, esto crea una "ferrita" agradable y dura. Para conseguir que sea lo suficientemente duro como para ser utilizado en realidad, se coloca en un horno y se calienta lentamente hasta obtener un color naranja brillante. Después de eso, el enfriamiento se realizó en el horno, precalentado al máximo. una vez que la pieza estuvo colocada y se dejó enfriar completamente durante la noche. El resultado fue que 1. I w como incapaz de sacar la ferrita curada de la caja de metal que utilicé. Es tan difícil que no pude perforarlo. No se rompe ni se agrieta. Intentaré encontrar algo más de tiempo y óxido negro y hacer un video corto del proceso. Mientras tanto, todos los que sigan pueden experimentar ya que lo único que importa es simplemente humedecer el óxido con el silicato de sodio para que se adhiera correctamente. Durante la compactación se puede presionar un poco el exceso, lo que indica que se debe usar incluso menos silicato de sodio para la siguiente mezcla. La única desventaja es que hay que hacer un pequeño horno, fundidor de metal o horno para puede endurecer completamente la mezcla, que es básicamente como una cerámica una vez curada.
Paso 9: ¡Actualiza! Quizás el último de todos…
Finalmente logré un progreso realmente decente:) Mis seguidores aquí ciertamente también experimentaron mucho, pero me tomó aproximadamente 2 años para finalmente ser golpeado por el poste de la cerca:) Resumamos lo que todavía sabemos primero: el óxido de hierro es lo suficientemente bueno para mucho Se pueden agregar muchos otros polvos minerales y metálicos para mejorar el rendimiento y tenemos la suerte de poder buscar la mayoría de ellos en Google y Wikipedia. Hacer un formulario tampoco es demasiado difícil … Pero hasta ahora hemos luchado para crear algo realmente duradero. Ya no…. Los núcleos de ferrita adecuados son cerámica horneada, lamentablemente la mayoría de nosotros no tendremos el equipo, sin mencionar el conocimiento para esto. Un aglutinante adecuado sería ideal y creo que encontré uno. ¿Algo que se pueda disolver en agua y que se seque como el vidrio? Silicato de sodio:) Puede hacerlo con lejía de arena para gatos de cristal, pero también pedirlo en Ebay o simplemente comprar sellador de concreto en su ferretería. o consígalo como líquido las preparaciones son sli Esta es la forma básica de hacerlo: Primero, verifique cómo se seca el líquido, así que mezcle un poco de polvo con agua o extienda su sellador directamente con un pincel sobre un cartón, notará que dependiendo de la concentración el líquido se seca Demasiado y terminará con un bonito crecimiento de cristales. Demasiado poco y solo obtendrá una cubierta ligeramente brillante en el cartón. Hágalo bien y terminará con una capa dura, como barniz. previamente secado uno debe construir una cubierta similar a un vidrio sin que crezcan cristales o se formen manchas blancas. Esta es la concentración que desea usar para unir la mezcla de ferrita. La preparación de la ferrita se reduce principalmente a asegurarse de que sea lo más fina posible y grumosa. Puede ponerlo a través de un colador fino si lo desea, pero el polvo de la ferretería o de la tienda de arte suele ser lo suficientemente bueno. El problema masivo con el óxido de hierro en forma de polvo es que las partículas generalmente se niegan a mojarse o aceptar cualquier " glu e "recubrimiento". La solución simple para este problema me dio muchos dolores de cabeza… Bueno, hasta que me di cuenta de lo simple que se puede hacer en la realidad si dejas de pensar demasiado complicado LOL Toma un recipiente preferiblemente que ya no se usa o simplemente una botella de refresco y llena el cantidad de mezcla de ferrita que necesita.¡Asegúrese de poder cerrarla y sellarla correctamente! Verá por qué prefiero las botellas de refresco aquí … Nunca debe llenar a más de 1/4 … Ahora agregue un poco de agua, preferiblemente destilada o al menos agua desmineralizada, no use agua corriente. Verá que nada realmente mezclas, así que agrega suficiente agua para permitir una buena agitación. Ok, no dije que lo agitas, pero ahora que lo viste, todavía apesta como resultado…. Agrega unas gotas de líquido para lavar platos y vuelve a intentarlo;) Si en duda agregue una cucharadita o dos. De repente el batido crea una lechada o si solía usar mucha agua un líquido negro. Pero no más grumos flotando alrededor, todo el polvo ahora está muy húmedo. Secando la ferrita … Quieres quitar el exceso agua jabonosa, así que es mejor dejar reposar la botella durante la noche. Ahora la mayor parte del agua se puede verter. Traté de sacar la mezcla de ferrita húmeda de varias maneras y, aparte de cortar la botella, las vibraciones parecen funcionar bien. Un motor de vibración de un controlador de juego viejo o un juguete desechado de su novia hará maravillas para hacer que la lechada se acabe Extiéndalo sobre un papel de horno con algunas toallas de papel para absorber el agua, o hágalo afuera y deje correr el agua. El resto se puede aplanar un poco y si necesita acelerar las cosas, déjelo secar. en el horno a 70-80 ° C - ¡no dejes que llegue al punto de ebullición ya que esto ensuciará el jabón y necesitamos esta funda de jabón! Una vez seco, rómpelo y sécalo nuevamente hasta que puedas triturarlo nuevamente polvo en un mortero o molinillo de café desechado: ¡tenga cuidado con el polvo y hágalo afuera! Nuestra mezcla de ferrita jabonosa ahora se puede usar con todos los pegamentos y pinturas a base de agua, como el pegamento para madera PVA o la pintura estándar de la ferretería. que todas estas cosas tienden a encogerse bastante y solo proporcionan una dureza más o menos gomosa. ¡Sin embargo, el silicato de sodio se seca literalmente con una dureza de vidrio! característica principal del silicato de sodio: se sella muy bien, por lo que hacer una varilla de ferrita sería tan fácil como mezclando la ferrita con la mezcla de silicato de sodio suficiente para crear una sustancia parecida a una masilla, corte la cabeza de la jeringa y llénela herméticamente. Una vez presionada, tiene una varilla que puede dejar secar. en el exterior, en el mejor de los casos, el interior se sellará y permanecerá húmedo para siempre.por lo menos muchos meses y luego resquebrajarlo todo lentamente … Solo para que sepas mi nivel de frustración: para el último paso, desperdicié alrededor de 3 kg de óxido de hierro en una cantidad interminable de pequeños lotes y experimentos … Encontré dos formas en que muestran al menos un enfoque factible al problema. Número uno: acumulación de material. Para evitar que la humedad quede atrapada al secar o curar, puede ayudar a desperdiciar mucho.. Aquí crearía una plantilla de cartón, solo un anillo y las dos paredes del anillo. El diámetro exterior e interior debe estar un poco por encima / debajo de lo que necesita si las dimensiones son realmente vitales. Rellene una capa delgada en la parte inferior y séquela en el horno. a menos de 90 ° C, agrega otro y haz lo mismo. Para que esto funcione la mezcla debe estar lo más seca posible, busca cómo preparar "arena verde" y ya sabes a qué me refiero. Debería ser posible formar una bola en su mano y si intenta abrirla, debe obtener dos piezas con una línea de ruptura clara. La mezcla también se seca al aire, así que manténgala tapada, ¡mézclela de vez en cuando! Una vez que haya llenado lo suficiente, comience a alisar la superficie con el último o dos rellenos. Deje que se seque de nuevo durante unas horas en el horno. Sube la temperatura a 180 ° C durante dos horas. Esto debería resultar en un núcleo realmente duro y duradero que ahora puedes lijar o limar para quitar el cartón. Usar un molde de silicona ciertamente ayuda si quieres hacer más de un núcleo. Número dos: arriesgarlo todo … Para núcleos más pequeños o cualquier cosa lo suficientemente plana, puede probar de esta manera. Haga un molde de acrílico grueso, como un material de placa de al menos 4 mm. Hágalo de modo que tenga muescas para juntarlo todo como realmente lo hace No quiero pegarlo juntos. La placa inferior debe estar perforada con muchos orificios pequeños. Utilicé una malla de filtro de acero inoxidable como plantilla y taladré a través de los orificios de la rejilla. No desea orificios de más de 1 mm, preferiblemente debajo si Puede usar un cortador láser para crear su molde. Estos orificios son vitales para drenar el líquido mientras se mantiene la mezcla en el interior. Corte un poco de papel de filtro para cubrir la parte inferior y los lados del molde. Para la parte inferior, desea dos capas. Con una tapa de presión adecuada, pruebe si realmente puede encajar dentro sin espacios, debe estar lo más apretado posible Tiempo para una prueba: Con el papel de filtro en su lugar y el molde en una superficie que te permita secar, llena tu molde con algunos trozos de limón o naranja - pela primero por favor … Si presionas lo suficiente, el jugo debe salir orificios de drenaje, un poco de jugo alrededor de la tapa de la prensa también pero sin pulpa ni nada que salga de la parte superior. En este caso, puede limpiar su desorden y ser feliz. Si sale mucho material por el espacio alrededor de la tapa de la prensa, necesita para hacer uno nuevo y volver a intentarlo. Una vez seco y limpio, agregue nuevamente los papeles de filtro y luego llene con su mezcla de ferrita / silicato de sodio. Vuelva a asegurarse de que sea como buena arena verde, no grumosa, no líquida. Use un taco o similar. para tocar y presionar la mezcla para una compresión básica y para asegurarse de que todos los coreners tengan una compresión idéntica al - de nuevo como hacer un molde de arena Grees. Una vez que esté lo suficientemente lleno, agregue la tapa y proporcione la mayor presión posible. Por lo general, comienzo simplemente agregando pesos en la parte superior hasta que termine el peor escurrimiento. De lo que, dependiendo del tamaño, usé una pieza de madera y un martillo o un tornillo de banco para sacar lo que pueda. A veces puede ayudar limpiar el molde con un paño que tenga un poco de aceite, pero la mayoría de las formas básicas se deshacen muy fácilmente sin pegarse. el molde y ni siquiera intentes quitar el papel. La clave ahora es expulsar el agua restante sin dejar que el exterior se seque, así que si tienes dudas, ten una botella rociadora con agua destilada lista para evitar que el papel se seque. ¡Es necesario mantener el exterior húmedo hasta que todo esté listo! Para un núcleo pequeño, el horno es la opción preferida, pero con el núcleo en un pequeño soporte en un recipiente con un poco de agua en el fondo. forme una capa de vidrio y el calor sacará la mayor parte del agua del núcleo interno. Si tiene algo alto como un frasco de espagueti o puede elevar el núcleo y usar más agua es realmente útil. Como un número para partir, le daré un ejemplo que funcionó bastante bien para mí: el núcleo tenía aproximadamente 8 mm de grosor y era como un toroide con un diámetro exterior de 9 cm. Usé 250 ml de agua con el núcleo a casi 20 cm de altura en un frasco de espagueti. De esta manera, solo quedaba poco espacio para el "techo" de mi horno. Calor de aproximadamente 90-120 ° (mi horno aspira hacia abajo en este rango) se aplicó solo desde la parte inferior. Una vez que todo se evaporó, dejé el horno a la misma temperatura por otras 2 horas, sin dejar que el núcleo o el horno se enfriaran mucho, se sacó el núcleo de la jarra y se colocó en un colador de acero inoxidable al revés. se aumentó a 200 ° C durante otras 2 horas. El núcleo resultante tenía sólo un ligero cristal f ormaciones en el exterior que se eliminaron fácilmente con un papel de lija fino. No pude romperlo con la mano y una caída de unos 50 cm sobre una baldosa tampoco hizo ningún daño visible, incluso después de probarlo varias veces. Cuando se puso de pie no tuve problemas para romperlo. ¡El producto es bastante duradero, el silicato de sodio se disuelve en agua y otros productos químicos! Por lo tanto, una capa adecuada de pintura acrílica duradera o una capa de resina es imprescindible si desea evitar fallas prematuras. forma de crear un núcleo de ferrita casero más duradero. Posibles formas de mejorar aún más el curado y la dureza …. El silicato de sodio tiene muchas propiedades interesantes y que cura como el vidrio real es una buena ventaja. Encontrar los óxidos, polvos metálicos o incluso sal adecuados s conseguir que una ferrita funcione como se desea requiere mucha excavación y experimentación. La mejor opción para comenzar es buscar las composiciones enumeradas para los núcleos bien conocidos. Puede que no obtenga las proporciones exactas, pero una buena comprensión de qué materiales funcionan mejor para un dada frecuencia y saturación. Así que de nuevo les dejo los experimentos con esto a mis seguidores de confianza y espero que sigan donde traté de proporcionar los puntos de inicio. ¿Una bobina Rodin con un toroide de ferrita personalizado, tal vez?;) De todos modos … El silicato de sodio forma una estructura cristalina muy dura con el cemento. Agregar solo una pequeña cantidad de polvo de cemento portland fino e incluso menos lejía resultó en una solución de silicato de sodio que crea recubrimientos aún más duraderos. floración de cristales no deseada durante el curado y para evitar que el polvo de cemento se asiente rápidamente. En las pruebas terminaron con una solución de silicato de sodio realmente espesa y muy corrosiva, una pequeña cantidad de cemento y bastante lejía para obtener un PH neutro Los resultados mostraron un gran potencial, pero no me gusta el requisito de protección completa para el cuerpo y la cara y los riesgos que conlleva manipular soluciones corrosivas y mezclarlas. Otros usos excelentes que encontré mientras experimentaba…. Un hecho casi olvidado es que el silicato de sodio era y todavía se usa ampliamente para sellar chimeneas agrietadas. Por lo tanto, si notó un problema en su vieja chimenea de ladrillo en su cabaña favorita, haga una mezcla de cemento con aproximadamente el 50% de el agua reemplazada por sellador de cemento y su próximo invierno verá salir el humo por la chimenea a través de las grietas dentro de su cabaña. Aunque usé esto para reparar grietas en mi fundición casera de mierda … Hice un pequeño experimento con un trozo de madera, usando una cámara de vacío lo empapé completamente con sellador de concreto, lo puse en el horno para que se seque completamente (me detuve cuando la báscula no mostró más reducción de peso), luego lijé La capa masiva de cristales en el exterior. La cosa no solo era dura como una roca, sino que también se veía muy bien en las áreas que traté de pulir. El agua y la mayoría de los productos químicos no lo afectaron de ninguna manera. Y bueno, tratando de quemarlo en mi tambor tampoco funcionó. Se agrietó, se carbonizó, pero fue como poner un ladrillo en el fuego … Pero lo mejor que intenté fue hacer lo imposible. ¿Alguna vez trataste de reparar una pieza de porcelana agrietada? ahora … Sí, todos tiramos algo hecho de ceram ic que causó muchos problemas con un ser querido … Hice un mal uso de un plato viejo que ya era el último que quedaba del set. Vaya, lo dejé caer en las baldosas … Bueno, no, no traté de sacar todos los piezas juntas, solo lo que se requería para volver a juntar la placa sin agujeros o piezas faltantes. Debería haber intentado golpear con un martillo para obtener dos o tres piezas, pero lo entendí, aunque una vez pensé que dejar caer es la mejor manera … Pero demostró que Si pierde el tiempo suficiente alineando todo en un plato en su horno, puede hornear el plato pieza por pieza. Algunas capas finales en ambos lados para obtener un acabado fino y rellenar las piezas pequeñas que faltan y el plato sobrevive al lavavajillas …
Recomendado:
¡Más de 8 millas, los primeros pines portátiles magnéticos universales !: 5 pasos
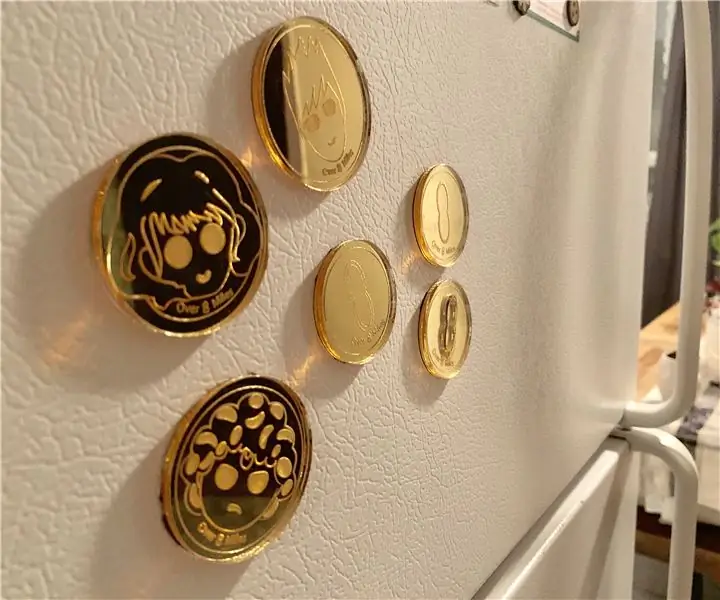
Más de 8 millas ¡Primeros pines portátiles magnéticos universales !: ¡Hola! Mi nombre es Georgina Yeboah y recientemente creé estos pines magnéticos basados en los personajes de mi webcomic Over 8 Miles. Puede encontrar el enlace a la página principal del webcomic debajo de esta introducción y el enlace de Tapas. Hice estos pines como un as
Campos de juego digitales: incluidos los niños con discapacidad visual: 13 pasos (con imágenes)
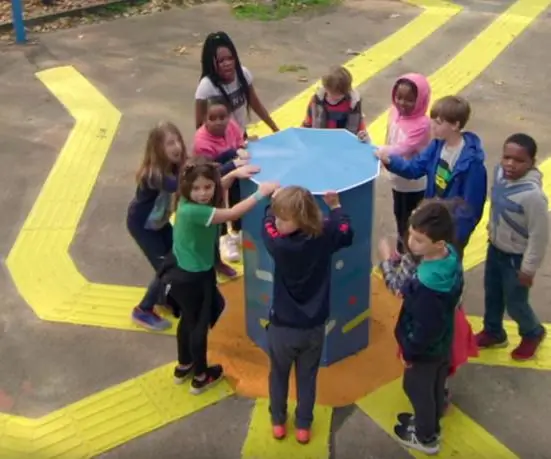
Campos de juego digitales, incluidos para niños con discapacidad visual: este Instructable comienza con un proyecto anterior, para construir una sola plataforma de presión, y luego lleva esto más allá para mostrar cómo este simple proyecto tecnológico se puede expandir para hacer que todo un patio de recreo sea digital. Esta tecnología ya existe en forma de
Mejorar los auriculares internos (auriculares): 6 pasos
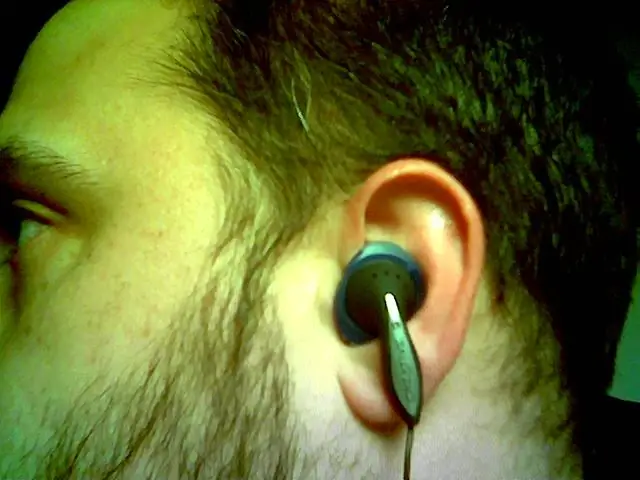
Mejorar los audífonos intrauditivos (Ear-Buds): Esos audífonos nunca caben en mis oídos. Pero hay una solución simple para eso
Haga su propia bolsa para computadora portátil XO: 11 pasos (con imágenes)
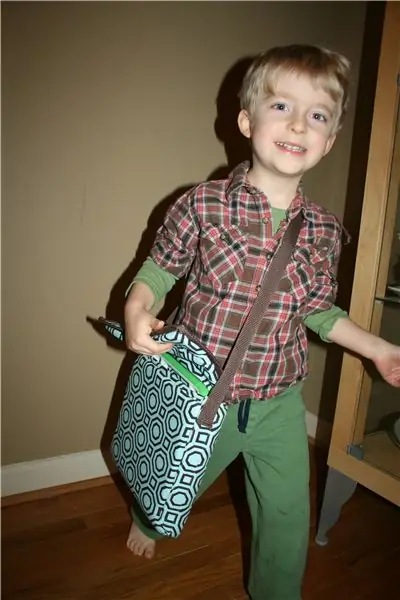
Haga su propia bolsa para computadora portátil XO: el producto final es una bolsa para computadora portátil personalizada para una computadora portátil OLPC XO, pero estas instrucciones probablemente podrían modificarse para muchos dispositivos electrónicos portátiles. El núcleo de la bolsa está hecho de espuma de alta densidad reforzada con cartón. La bolsa es t
Haga su propia bolsa de fieltro para EeePC / Netbook por aproximadamente $ 8 (y ahorre $ 91 en lugar de comprarla en Redmaloo): 5 pasos (con imágenes)
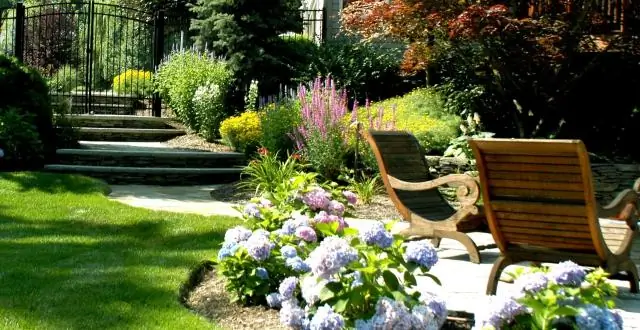
Haga su propia bolsa de fieltro agradable para EeePC / netbook por aproximadamente $ 8 (y ahorre $ 91 en lugar de comprarla en Redmaloo): este instructivo le mostrará cómo hacer su propia computadora portátil, muy bonita y de buen aspecto, o incluso una mejor bolsa para netbook. Almacenará su netbook, le dará un mousepad, la sensación de usar algo único, agradable y hecho a mano y la sensación de goos de