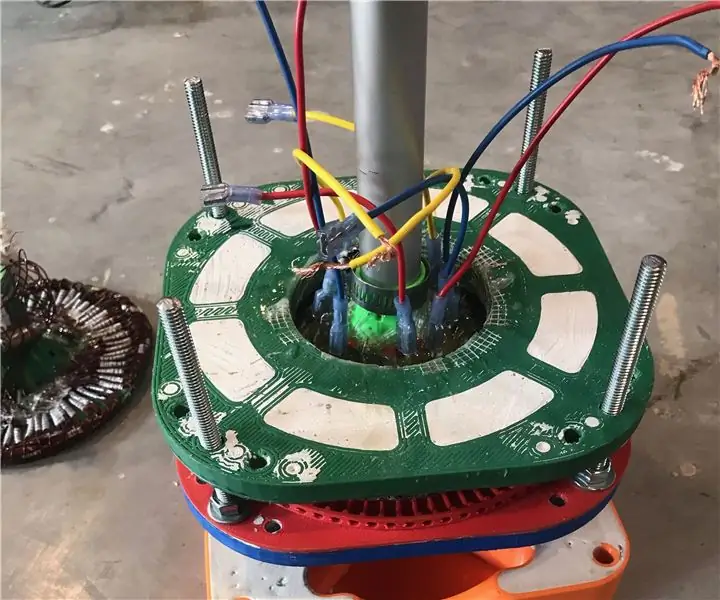
Tabla de contenido:
2025 Autor: John Day | [email protected]. Última modificación: 2025-01-23 14:39
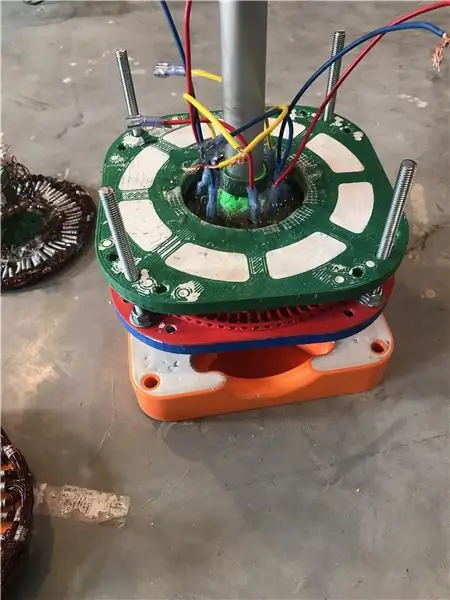
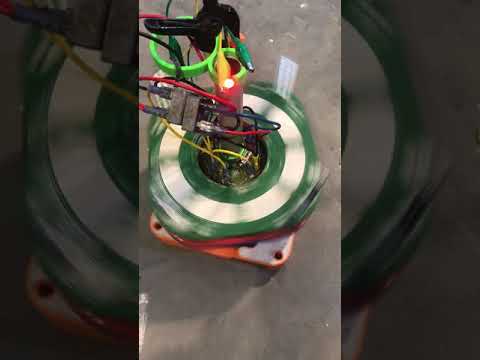
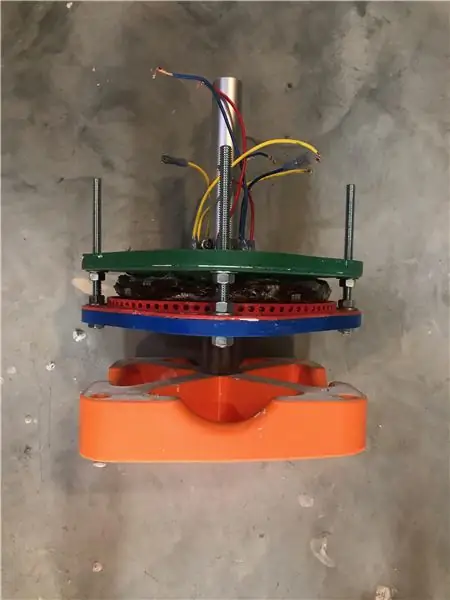
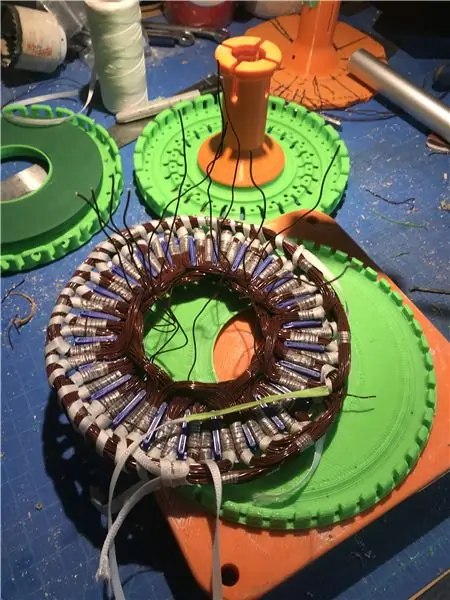
¡¡PARADA!! ¡¡¡LEÉ ESTO PRIMERO!!! Este es un registro de un proyecto que aún está en desarrollo, no dude en ofrecer apoyo.
Mi objetivo final es que este tipo de motor / alternador pueda convertirse en un diseño de código abierto parametrizado. Un usuario debe poder ingresar algunos parámetros, como par, velocidad, corriente, voltios / rpm, tamaños de imán comunes y quizás espacio disponible, y se debe generar una serie de archivos de corte.stl y.dxf imprimibles en 3D.
Lo que hice fue crear una plataforma que puede validar un diseño simulado, que luego puede evolucionar a un dispositivo más óptimo por comunidad.
En parte, esta es una de las razones por las que configuré esto con un dinamómetro. Un dinamómetro mide el par y la velocidad para permitir que se midan los caballos de fuerza o los vatios del eje. En este caso, he construido el alternador con un eje estacionario de paso, lo que simplifica la instalación de un sistema de dinamómetro, por lo que se puede configurar para ser impulsado como un motor por un RC ESC (espero), y medir el par en la salida, así como la velocidad, V y Amperios, lo que permite determinar la eficiencia del motor.
Para mis propósitos, puede ser impulsado por un motor de velocidad variable (excedente del taladro inalámbrico, con engranaje reductor), y se puede medir el par de torsión del eje, así como V y amperios, lo que permite generar una eficiencia real y las cargas esperadas de la turbina. para ser simulado.
En este modo espero usar un RC ESC capaz de frenado regenerativo, y quizás un Arduino para controlar la carga que lleva mi VAWT para lograr MPPT (Multi Power Point Tracking).
MPPT se utiliza en el control de turbinas solares y eólicas, pero es un poco diferente para el viento. Con la energía eólica, un gran problema es que a medida que la velocidad del viento se duplica de 10 km / ha 20 km / h, la energía disponible del viento aumenta en el cubo, es decir, en 8 veces. Si hay 10 W disponibles a 10 km / h, entonces 80 W están disponibles a 20 km / h. Es genial tener más energía, pero la salida de los alternadores solo se duplica cuando la velocidad se duplica. Entonces, si tiene el alternador perfecto para un viento de 20 km / h, su carga puede ser tan fuerte que a 10 km / h ni siquiera arrancará.
Lo que hace MPPT es usar un interruptor de estado sólido de alta resistencia para desconectar y luego volver a conectar un alternador muy rápidamente. Le permite ajustar la cantidad de carga que lleva un alternador, y el Multi, del MPPT, significa que puede configurar diferentes cargas para diferentes velocidades.
Esto es muy útil, ya que todos los tipos de turbinas recolectan su energía máxima cuando la carga se adapta a la energía disponible o la velocidad del viento.
ASI QUE
Esta no es una receta, aunque creo que podría copiarse de lo que he publicado, y estaría encantado de proporcionar más información, pero sugiero que la mejor opción sería sugerirme mejoras, antes de que finalice el concurso de Circuitos y sensores., para que pueda considerar, responder y quizás mejorar este instructable.
Continuaré actualizando, revisando y agregando información, por lo que si es interesante ahora, es posible que desee verificar nuevamente en un momento, pero espero terminar un poco antes de que finalice el concurso de Sensores el 29/19 de julio.
Además, no soy una bestia particularmente social, pero me gustan las palmaditas en la espalda de vez en cuando, y esa es una de las razones por las que estoy aquí:-) Dime si te gusta ver mi trabajo y quieres ver mas por favor:-)
Este proyecto surgió porque quería una carga controlable para probar los diseños de mis turbinas, y quería que fuera fácilmente reproducible, para que otros también pudieran usarla. Con este fin, me limité a diseñar algo que pudiera construirse solo con una impresora FDM, sin necesidad de otras máquinas herramienta. No parece haber muchos productos comerciales que satisfagan la necesidad de un alternador sin engranajes de alta torsión, baja velocidad, aunque hay algunos de China. En general, no hay mucha demanda porque los sistemas de engranajes son muy económicos y la electricidad es muy barata.
Lo que quería era algo que produjera alrededor de 12V a 40-120 rpm y alrededor de 600-750W a 120-200 rpm. También quería que fuera compatible con los controladores PMA trifásicos económicos del mundo RC (controladores electrónicos de velocidad de ESC). Un último requisito fue que fuera un corredor (la caja o carcasa con imanes gira, mientras que el eje con el estator está estacionario), con un eje que atraviesa completamente la caja y un estator que se sujeta al eje.
Este instructivo es un trabajo en progreso y lo estoy publicando para que las personas puedan ver el proceso, no tanto porque creo que deberían copiarlo. Una cosa clave que cambiaría es que la placa de respaldo de alambre que construí no es lo suficientemente fuerte como para canalizar correctamente los campos magnéticos alrededor del anillo, por lo que una gran parte del flujo magnético pagado en esos imanes se desperdicia en la parte posterior. Cuando vuelva a hacer el diseño, lo que haré en breve, probablemente lo haga con las placas de respaldo magnéticas como placas de acero cortadas con cnc. El acero sería bastante económico, mucho más resistente y simplificaría la mayor parte de esta construcción. Fue interesante hacer los compuestos FDM / alambre / yeso como lo he ilustrado aquí, y con PLA cargado de hierro, las cosas también habrían sido diferentes. Sin embargo, decidí que quería algo que realmente durara, así que placas de acero.
He progresado mucho en esta versión, que usaré para probar este VAWT. Todavía no estoy del todo ahí en términos de rendimiento de bajo voltaje. Creo que mi potencia / par está en el estadio correcto, actualizaré a medida que avancen las cosas, pero en este punto lo que tengo tiene muchas posibilidades de ser la carga controlable que necesito. Cuando está en cortocircuito, parece ser capaz de proporcionar bastante resistencia al par, más que suficiente para probar la turbina. Solo necesito establecer un banco de resistencia controlado, y tengo un amigo que me está ayudando con eso.
Una cosa que abordaré brevemente es que, como muchas personas ahora, he tenido una impresora 3D (PLA con FDM) durante algunos años, de la que he disfrutado de 20 a 30 kg. Sin embargo, a menudo me resulta frustrante, ya que las piezas de cualquier tamaño / fuerza son caras y muy lentas de imprimir, o baratas, rápidas y endebles.
Sé cuántos miles de estas impresoras 3D existen, a menudo sin hacer nada porque lleva mucho tiempo o cuesta demasiado fabricar piezas útiles. Se me ocurrió una solución interesante para piezas más fuertes y más rápidas de la misma impresora y PLA.
Lo llamo una "estructura vertida", donde el objeto impreso (formado por 1 o más partes impresas, y a veces cojinetes y ejes), está hecho con huecos diseñados para ser vertidos llenos de un relleno líquido endurecedor. Por supuesto, algunas de las opciones obvias para un relleno vertido serían algo como epoxi cargado con fibra de vidrio cortada de hebra corta, que podría usarse para ensamblajes de alta resistencia y peso ligero. También estoy probando algunas ideas más ecológicas y de menor costo. El otro lado de este ensamblaje de "estructura vertida", es que la cavidad o vacío que se va a llenar, puede tener elementos de alta tensión de pequeño diámetro, ensartados pretensados en el "molde / tapón" impreso, lo que hace que la estructura resultante un compuesto en materiales, y en estructura, parcialmente Stressed Skin (la vaina de PLA), pero con un núcleo de alta resistencia a la compresión que también incluye elementos de alta resistencia a la tracción. Haré un segundo instructivo con esto, así que hablaré de ello aquí, solo para cubrir cómo se relaciona con esta compilación.
Paso 1: Lista de materiales y proceso
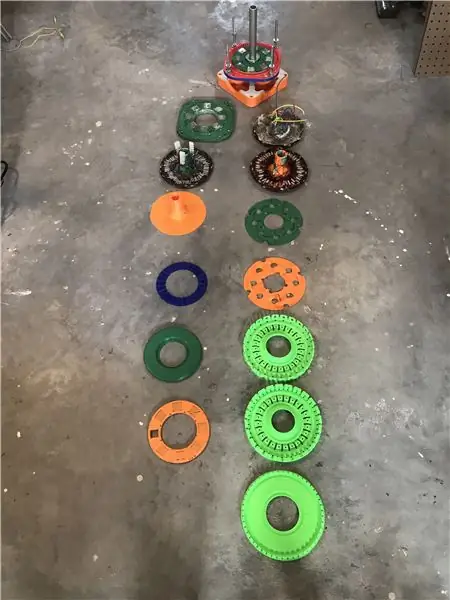
El PMA consta de 3 conjuntos, cada conjunto contiene o utiliza una variedad de piezas y materiales.
Desde arriba (lado del cojinete) hacia abajo (lado del estator), 1. Soporte de cojinetes y matriz de cojinetes superior
2. Estator
3. Matriz de imanes inferior
1. El portador de cojinetes y la matriz de imanes superiores
Para esto utilicé las piezas impresas en 3D enumeradas anteriormente
- Soporte de cojinete y mag superior de 150 mm y 8 polos CV5.stl,
- placa interior del lado del rodamiento
- placa exterior del lado del rodamiento
- Cojinete autoalineable de 1 "ID (como el que se usa en los bloques de almohada estándar ++ agregar enlace de Internet),
- 25 'de alambre de acero galvanizado de 24 g
- 15 'de alambre de acero galvanizado de 10 g
- 2 rollos de lana de acero gruesa
Opcionalmente, el alambre de acero pesado y la lana de acero podrían reemplazarse con placas de respaldo de acero, cortar con láser / chorro de agua o una placa de respaldo magnética impresa en 3D (pero un poco de alambre de acero pesado sigue siendo una buena idea, ya que resistirá la deformación plástica tiempo). Intenté moldear una placa de respaldo con epoxi cargado con polvo de óxido de hierro y tuve cierto éxito. La mejora del acoplamiento de flujo entre los imanes en la matriz lateralmente mediante el uso de una placa de respaldo más eficaz debería aumentar los voltios a bajas revoluciones por minuto. También es bueno tener en cuenta que este es el componente estructural principal, y la placa posterior transfiere las fuerzas de los imanes a los postes de elevación. Las fuerzas magnéticas que atraen las placas entre sí pueden ser de cientos de libras, y las fuerzas aumentan exponencialmente (al cubo, a la tercera potencia) a medida que las placas se acercan. Esto puede ser muy peligroso y se debe tener cuidado con las herramientas y cualquier otro objeto que pueda ser atraído por la placa ensamblada o su parte posterior.
Usé alrededor de 300 pies de alambre magnético recubierto de 24 g en los devanados que cubriré en detalle más adelante.
Paso 2: Fabricación de las placas magnéticas
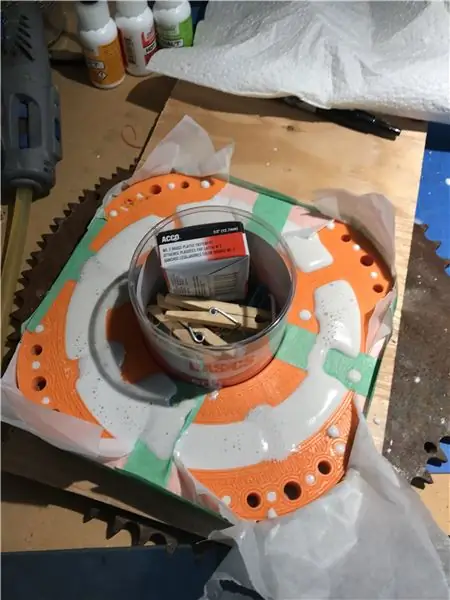
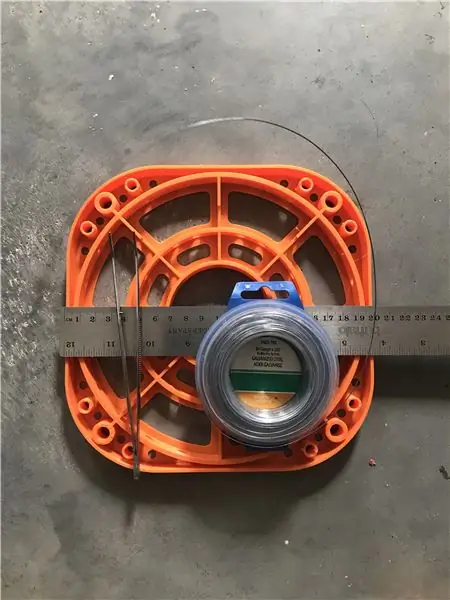
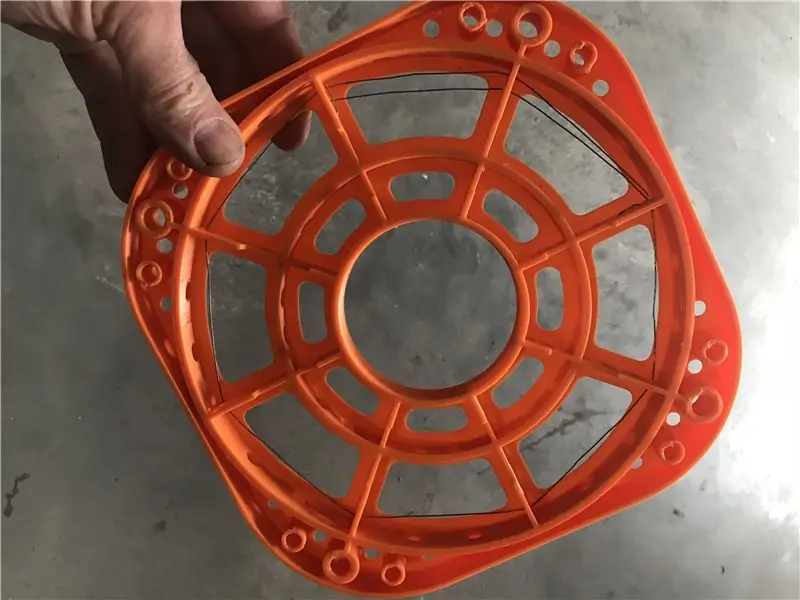
En este alternador de flujo axial, para minimizar el engranaje y maximizar la salida, estoy usando dos conjuntos de imanes, uno a cada lado de las bobinas del estator. Esto significa que no se necesita un núcleo magnético para atraer el campo magnético a través de los devanados de cobre, como lo hacen la mayoría de las geometrías de motor / alt. Hay algunos diseños de flujo axial que utilizan núcleos ferris, y es posible que intente algunos experimentos de esa manera en el futuro. Me gustaría probar algún material cargado de hierro imprimible en 3D.
En este caso, he elegido una matriz de imanes de 8 polos en un círculo de aproximadamente 150 mm, utilizando imanes de tierras raras de 1 "x1" x0,25 ". Este tamaño era para asegurar que todas las piezas encajarían en una cama de impresión de 210 mm x 210 mm. En general, primero dimensioné este alternador entendiendo que cuanto mayor sea el diámetro, mejor en términos de voltios por rpm, lo hice tan grande como se ajustara cómodamente a mi cama de impresión. Para su información, hay más de una razón por la que más grande es mejor: más espacio para imanes, cuanto más lejos están los imanes del centro, más rápido viajan y hay más espacio para el cobre también. ¡Todas estas cosas pueden acumularse rápidamente! Sin embargo, una conclusión a la que he llegado es que en este rango de tamaño, un El sistema de flujo puede ser una mejor construcción de la casa. Los rotores pequeños no tienen mucho espacio y las cosas pueden ponerse bastante apretadas, especialmente si está haciendo un eje pasante como lo hice en este diseño. También si su imán (longitud radial) es pequeño en relación con el diámetro de su rotor, como en este, (aproximadamente 6 "de diámetro a un imán de 1"), entonces el viento ng se vuelve un poco extraño ya que el extremo interior devanado es solo aproximadamente la mitad de la longitud del exterior.
¡De vuelta a la instrucción! La forma en que he ensamblado las placas magnéticas de este alternador es pegar primero la placa magnética (verde) a la brida roja / placa de respaldo. Luego coloqué la placa magnética en unas pocas capas delgadas de madera contrachapada (de aproximadamente 0,75 de grosor), y coloqué ambas sobre una placa de acero pesado, para permitir que los imanes sujetaran el ensamblaje en su lugar. Luego, enrolle alambre de acero en el parte posterior de las placas magnéticas. Esto no salió como esperaba. El fuerte campo magnético tiró del cable hacia el centro de los imanes, y no logré doblar cada fila de cables para que encajaran perfectamente en el siguiente punto, sin empujar la primera vuelta. Tenía la esperanza de poder enrollar el cable y el flujo magnético lo bloquearía. A continuación, intenté cortar anillos de cable, y esto fue mejor, pero aún lejos de lo que había esperaba en términos de obtener una buena placa de respaldo consistente a partir del alambre. Son posibles formas más complejas de hacer esto, y podría valer la pena experimentar en el futuro. También intenté usar lana de acero, compactada en el campo magnético, como placa de respaldo o fundente ruta de retorno. Esto parecía funcionar, pero la densidad real del hierro no parecía ser muy alta, así que di No probé su efectividad, en parte porque creía que la estructura del cable era importante para las cargas mecánicas en las placas magnéticas. La lana de acero también puede valer la pena una investigación futura, sin embargo, es probable que las placas de acero cortadas con chorro de agua sean la próxima opción que probaré.
A continuación, tomé la parte naranja impresa en 3D y entretejí alambre a través y alrededor de ella, a lo largo de lo que me parecían ser las direcciones de carga más alta, perno a perno y perno al centro unas cuantas veces en cada esquina. También lo enrollo alrededor de los orificios de los pernos donde la varilla de rosca pasa como postes de elevación para mantener y ajustar el espacio entre las placas.
Después de estar satisfecho de que la placa magnética y la brida eran lo suficientemente buenas, y la placa de respaldo naranja estaba satisfactoriamente enhebrada con alambre de refuerzo, uní las dos con pegamento. Se debe tener cuidado ya que esta junta adhesiva deberá ser hermética al agua o estar cerrada. Tuve fugas las dos primeras veces, y es un desastre, desperdicia mucho yeso y es más estresante de lo necesario. Recomendaría mantener un poco de tachuela azul u otro chicle como adhesivo no permanente para reparar las fugas rápidamente. Una vez unidas las piezas, rellene con el material de refuerzo de su elección. Usé un yeso duro, modificado con cola de PVA. Se supone que el yeso debe alcanzar 10, 000 psi de compresión, pero no mucha tensión (de ahí el alambre). Me gustaría probar epoxi con vidrio picado y cabosil, o concreto y aditivos.
Una cosa útil sobre el yeso es que una vez que patea, tiene bastante tiempo donde es duro, pero frágil y las fugas o manchas pueden rasparse o desprenderse fácilmente.
En este diseño, hay dos placas magnéticas. Uno tiene un cojinete, una unidad de autoalineación de bloque de almohada estándar de 1 . Presioné el mío en la matriz de imanes desde el principio. Para la aplicación para la que lo diseñé, un segundo cojinete estará ubicado en la turbina sobre el alternador, por lo que Solo usé un rodamiento autoalineable. Esto fue un poco molesto al final. Estas partes también podrían ensamblarse con cada placa magnética con un rodamiento, si los cables de salida del estator se condujeran internamente a través del eje montado. Permite que las hélices contrarrotativas se monten en un eje / tubo común no giratorio.
Paso 3: creación del estator

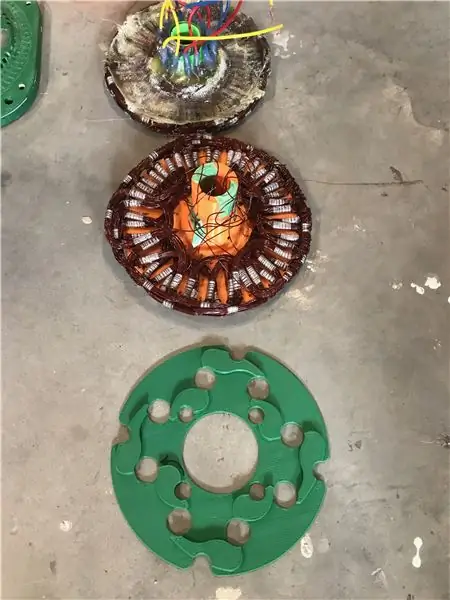
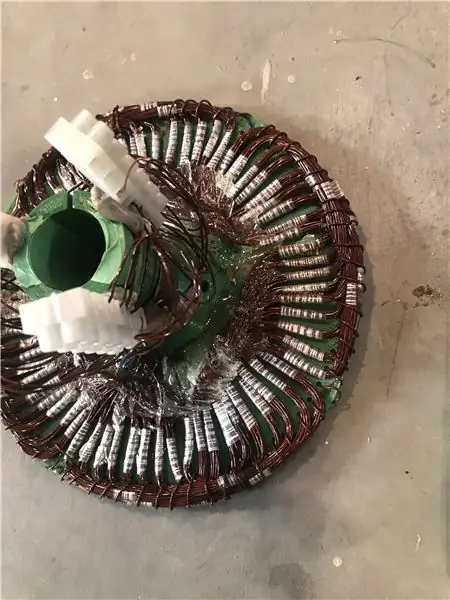
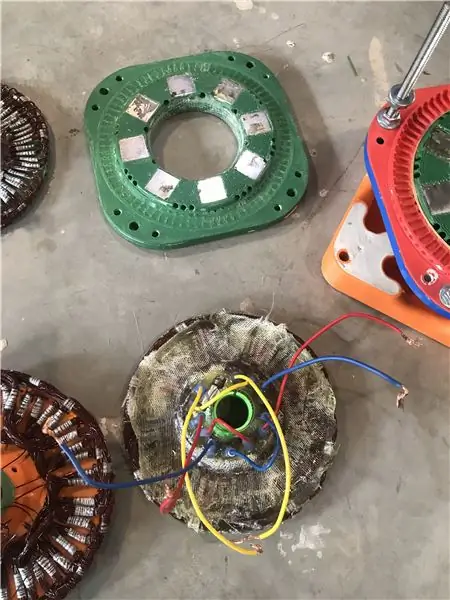
De acuerdo con mi tema de tratar de explicar lo que hice y por qué me pareció una buena idea en ese momento, el estator requerirá un poco más de espacio.
En un PMA, generalmente los devanados son estacionarios, mientras que los conjuntos magnéticos giran. Este no es siempre el caso, pero casi siempre. En un ensamblaje de flujo axial, con la comprensión de la "regla de la mano derecha" fundamental, se entiende que cualquier conductor que se encuentre con un campo magnético giratorio tendrá corriente y voltaje generados entre los extremos del cable, siendo proporcional la cantidad de corriente útil. a la direccion del campo. Si el campo se mueve paralelo al alambre (por ejemplo, en un círculo alrededor del eje de rotación), no se generará corriente útil, pero se generarán corrientes parásitas significativas, resistiendo el movimiento de los imanes. Si el cable corre perpendicular, se alcanzará el voltaje y la salida de corriente más altos.
Otra generalización es que el espacio dentro del estator, a través del cual pasa el flujo magnético mientras está en rotación, para una potencia máxima de salida, debe llenarse con la mayor cantidad de cobre, todo radialmente colocado, como sea posible. Esto es un problema para los sistemas de flujo axial de diámetro pequeño, ya que en este caso, el área disponible para el cobre cerca del eje es una fracción del área en el borde exterior. Es posible obtener un 100% de cobre en el área más interna encontrada por el campo magnético, pero dentro de esta geometría, eso solo lo lleva quizás al 50% en el borde exterior. Esta es una de las razones más importantes para mantenerse alejado de los diseños de flujo axial que son demasiado pequeños.
Como dije anteriormente, este instructivo no se trata de cómo lo haría de nuevo, sino de apuntar en algunas direcciones que parecen prometedoras y mostrar algunos de los baches que se pueden alcanzar en este camino.
Al diseñar el estator, quería hacerlo lo más flexible posible en términos de salida de voltios por rpm, y quería que fuera trifásico. Para una máxima eficiencia, minimizando las corrientes parásitas generadas, cualquier "rama" (cada lado de una bobina debe considerarse como una "rama") solo debe encontrar un imán a la vez. Si los imanes están muy juntos, o tocándose como es el caso en muchos motores rc de alto rendimiento, durante el tiempo que la "pata" pasa a través de la inversión del flujo magnético, se desarrollarán corrientes parásitas significativas. En aplicaciones de motor, esto no importa tanto, ya que el controlador energiza la bobina cuando está en las ubicaciones correctas.
Medí la matriz de imanes con estos conceptos en mente. Los ocho imanes de la matriz tienen cada uno 1 "de ancho y el espacio entre ellos es de 1/2". Esto significa que un segmento magnético mide 1.5 "de largo y tiene espacio para patas de 3 x 1/2" ". Cada "tramo" es una fase, por lo que en cualquier punto, un tramo ve un flujo neutro, mientras que los otros dos ven un flujo ascendente y un flujo decreciente. La salida trifásica perfecta, aunque al darle al punto neutro tanto espacio (para minimizar las corrientes parásitas) y al usar imanes cuadrados (o en forma de pastel), el flujo casi alcanza su punto máximo al principio, se mantiene alto y luego cae a cero rápidamente. Creo que este tipo de salida se llama trapezoidal y puede ser difícil para algunos controladores que entiendo. Los imanes redondos de 1 "en el mismo aparato darían más de una verdadera onda sinusoidal.
Por lo general, estos alternadores de fabricación casera se han construido utilizando "bobinas", haces de alambre en forma de rosquilla, donde cada lado de la rosquilla es una "pata" y se pueden unir varias bobinas, en serie o en paralelo. Las rosquillas están dispuestas en círculo, con sus centros alineados con el centro de la trayectoria del imán. Esto funciona, pero hay algunos problemas. Un problema es que, dado que los conductores no son radiales, una gran parte del conductor no pasa a 90 grados del campo magnético, por lo que se generan corrientes parásitas, que aparecen como calor en la bobina y resistencia a la rotación en la matriz de imanes.. Otro problema es que debido a que los conductores no son radiales, no se empaquetan tan bien. La salida es directamente proporcional a la cantidad de cable que puede caber en este espacio, por lo que la salida se reduce mediante "patas" no radiales. Si bien sería posible y a veces se hace en diseños comerciales, enrollar una bobina con patas radiales, unidas en la parte superior e inferior, requiere el doble de bobinado final que una bobina en serpentina donde la parte superior de una pata se une a la parte superior de la siguiente pierna apropiada, y luego la parte inferior de esa pierna se une a la siguiente pierna apropiada, y así sucesivamente.
El otro gran factor en los alternadores de flujo axial de este tipo (imanes giratorios por encima y por debajo del estator) es el espacio entre las placas. Esta es una relación de la ley del cubo, a medida que reduce la distancia entre las placas en 1/2, la densidad de flujo magnético aumenta en 8x. ¡Cuanto más delgado pueda hacer su estator, mejor!
Con esto en mente, hice una plantilla de bobinado de 4 lóbulos, configuré un sistema para medir aproximadamente 50 pies de hilos de alambre y envolví la plantilla 6 veces, creando haces de cables de aproximadamente 6 mm de diámetro. Los encajo en el anillo espaciador azul, atándolos a través de los orificios para que los extremos del cable salgan por la parte posterior. No fue fácil. Me ayudó un poco haber pegado cuidadosamente los paquetes con cinta adhesiva para que no se soltaran, y tomándome mi tiempo y usando una herramienta de formación de madera suave para empujar los cables en su lugar. Una vez que todos estuvieron atados en su lugar, el anillo espaciador azul se colocó en la más grande de las tinas de formación de color verde claro, y con la ayuda de la herramienta de formación de rosquillas de color verde oscuro, en el otro lado de la tina de color verde claro, se presionó cuidadosamente con un tornillo de banco. Esta tina de formación tiene una ranura para que se asienten los alambres de amarre. Esto requiere tiempo y paciencia mientras gira con cuidado alrededor de 1/5 de vuelta, presiona, gira y continúa. Esto hace que el disco sea plano y delgado, al tiempo que permite que los devanados de los extremos se apilen. Puede notar que mi devanado de 4 lóbulos tiene "patas" rectas, pero las conexiones internas y externas no son redondas. Se suponía que esto les facilitaría el apilamiento. No funcionó tan bien. Si lo volviera a hacer, haría que los devanados de los extremos interior y exterior siguieran trayectorias circulares.
Después de dejarlo plano y delgado, y los bordes empaquetados, enrolle una cinta plana alrededor del borde para compactarlo, y otra hacia arriba, hacia abajo y alrededor de cada pata y luego a la que está al lado también. Una vez hecho esto, puede quitar los cables de amarre y cambiar a la tina de prensado más pequeña, y volver al tornillo de banco y presionarlo lo más delgado y plano posible. Una vez que esté plano, retírelo de la tina de prensa. En lugar del complejo proceso de encerar cuidadosamente y recubrir moldes como este con compuestos de liberación, generalmente solo uso un par de capas de envoltura elástica (de la cocina). Coloque un par de capas en el fondo del molde y coloque la fibra de vidrio sobre la envoltura elástica. A continuación, agregue el tubo de montaje del estator, que se ajusta a la parte superior de la tina de formación de color verde claro, pero tiene la capa de envoltura elástica y fibra de vidrio entre ellos. Luego, vuelva a colocar el devanado del estator en su lugar para empujar hacia abajo tanto la envoltura elástica como la fibra de vidrio y bloquear el tubo de montaje del estator en su lugar. Luego regresa al tornillo de banco y presiona plano nuevamente. Una vez que encaja bien en la bañera, con la envoltura elástica y la fibra de vidrio intercaladas, se agrega un paño de fibra de vidrio (con un orificio en el centro para el tubo de montaje del estator).
Ahora está listo para verter el material de unión, se usan comúnmente resina epoxi o poliéster. Antes de hacer esto, es importante una preparación cuidadosa, ya que una vez que comienza este proceso, realmente no puede detenerse. Usé una placa base impresa en 3D que había hecho anteriormente, con un orificio de 1 "en el centro y una placa plana alrededor. Usé una pieza de 16" de tubo de aluminio de 1 ", sobre el que encajaría el tubo de montaje del estator y quedaría sostenido perpendicular a la placa plana. La cuba de formación verde, el devanado del estator y el tubo de montaje del estator se deslizaron hacia abajo para asentarse en la placa plana. Antes de mezclar epoxi, primero preparé 4 piezas de envoltura retráctil y coloqué cuidadosamente una quinta pieza en la placa plana. verde oscuro formando una rosquilla, por lo que tendría las arrugas mínimas en la cara contra el devanado del estator. Después de mezclar el epoxi y verterlo sobre la tela de fibra de vidrio, coloqué cuidadosamente la envoltura elástica alrededor del tubo de 1 "y coloqué el verde formando un anillo encima de él. También preparé un par de rotores de freno viejos, que dieron algo de peso, y se sentaron muy bien en la rosquilla de formación verde. Después de esto, puse una olla invertida encima de los rotores de freno, y encima de la olla apilé alrededor de 100 libras de material. Dejé esto durante 12 horas y salió con un grosor de 4-6 mm.
Paso 4: Pruebas y sensores
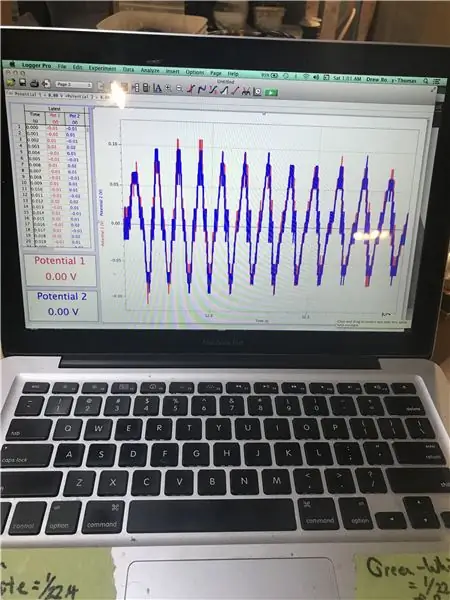
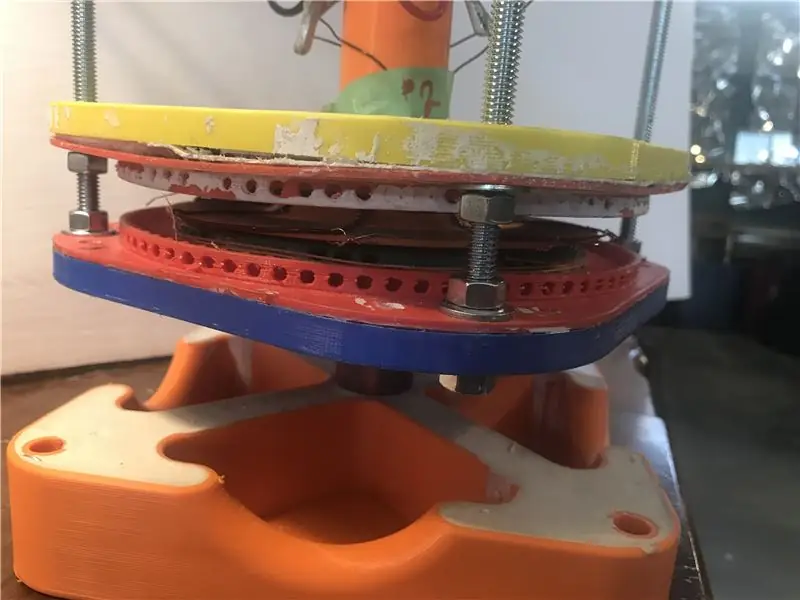
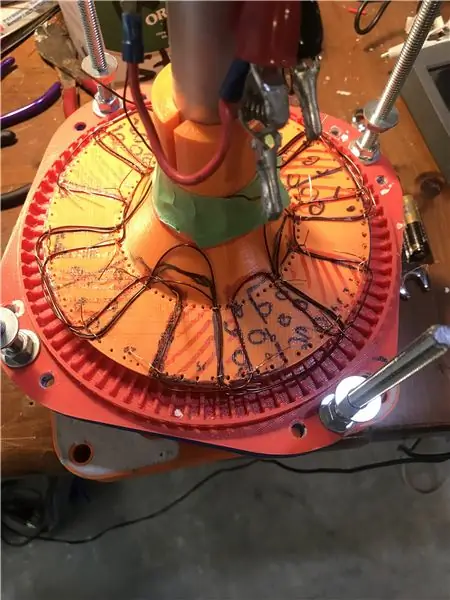
Hay una serie de entradas y salidas medibles del alternador, y medirlas todas al mismo tiempo no es fácil. Soy muy afortunado de tener algunas herramientas de Vernier que lo hacen mucho más fácil. Vernier fabrica productos de nivel educativo, no certificados para uso industrial, pero muy útiles para experimentadores como yo. Utilizo un registrador de datos Vernier, con una variedad de sensores plug and play. En este proyecto, utilizo sondas de corriente y voltaje basadas en hall para medir la salida del alternador, un sensor óptico para dar la velocidad del alternador y una celda de carga para medir la entrada de par. Todos estos instrumentos se muestrean unas 1000 veces por segundo y se graban en mi computadora portátil, utilizando el registrador Vernier como un dispositivo de acceso directo. En mi computadora portátil, el software asociado puede ejecutar cálculos en tiempo real basados en las entradas, combinando datos de par y velocidad para proporcionar potencia del eje de entrada en tiempo real en vatios y datos de salida en tiempo real en vatios eléctricos. No he terminado con esta prueba, y sería útil la aportación de alguien que tenga una mejor comprensión.
Un problema que tengo es que este alternador es realmente un proyecto paralelo, por lo que no quiero dedicarle mucho más tiempo. Tal como está, creo que puedo usarlo para una carga controlable para mi investigación de VAWT, pero eventualmente me gustaría trabajar con personas para refinarlo, de modo que sea una combinación eficiente para mi turbina.
Cuando comencé a investigar sobre VAWT hace unos 15 años, me di cuenta de que probar VAWT y otros motores primarios es más complejo de lo que la mayoría de la gente cree.
Un problema principal es que la energía representada en un fluido en movimiento es exponencial a su velocidad de movimiento. Esto significa que a medida que duplica la velocidad de un flujo, la energía contenida en el flujo aumenta 8 veces (se expresa en cubos). Esto es un problema, ya que los alternadores son más lineales y, en general, si duplica las rpm de un alternador, obtiene aproximadamente el doble de vatios.
Este desajuste fundamental entre la turbina (dispositivo de recolección de energía) y el alternador (potencia del eje a energía eléctrica útil) dificulta la elección de un alternador para una turbina eólica. Si elige una combinación de alternador para su turbina eólica que generará la mayor cantidad de energía disponible con vientos de 20 km / h, es probable que ni siquiera comience a girar hasta 20-25 km / h, ya que la carga en la turbina del alternador será demasiado alta.. Con esa combinación de alternador, una vez que el viento supera los 20 km, la turbina no solo capturará una fracción de la energía disponible en el viento de mayor velocidad, sino que la turbina puede sobrepasar la velocidad y dañarse porque la carga proporcionada por el alternador no es alta. suficiente.
En la última década, una solución se ha vuelto más económica debido a la caída del precio de la electrónica de control. En lugar de tratar de igualar un rango de velocidades, el diseñador calcula la velocidad máxima a la que debe operar el dispositivo y elige un alternador en función de la cantidad de energía y la velocidad ideal para la turbina a esa velocidad, o un poco más.. Este alternador, si está conectado a su carga, normalmente proporcionaría demasiado par en el rango de baja velocidad, y la turbina sobrecargada no capturará toda la energía que podría tener si estuviera cargada correctamente. Para crear la carga adecuada, se agrega un controlador que desconecta momentáneamente el alternador de la carga eléctrica, lo que permite que la turbina se acelere a la velocidad adecuada, y se reconectan el alternador y la carga. A esto se le llama MPPT (Seguimiento de múltiples puntos de potencia). El controlador está programado de manera que a medida que cambia la velocidad de la turbina (o aumenta el voltaje del alternador), el alternador se conecta o desconecta, aproximadamente mil veces por segundo, para que coincida con la carga programada para esa velocidad o voltaje.
Recomendado:
Cómo hacer un sensor de tasa de flujo de aire preciso con Arduino por menos de £ 20 Ventilador COVID-19: 7 pasos
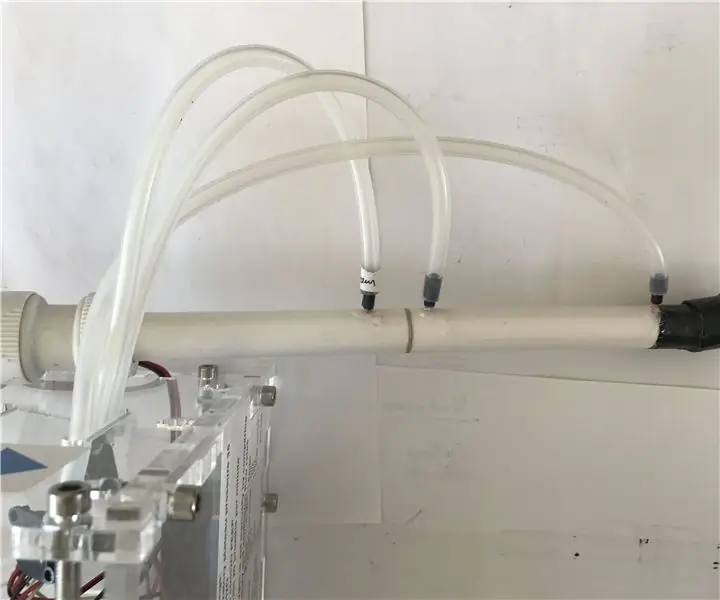
Cómo hacer un sensor de caudal de aire preciso con Arduino por menos de £ 20 Ventilador COVID-19: consulte este informe para conocer el diseño más reciente de este sensor de flujo de orificio: https://drive.google.com/file/d/1TB7rhnxQ6q6C1cNb. ..Este instructivo muestra cómo construir un sensor de tasa de flujo de aire usando un sensor de presión diferencial de bajo costo y fácilmente un
Medición de flujo con medidores de flujo de agua (ultrasónicos): 5 pasos (con imágenes)
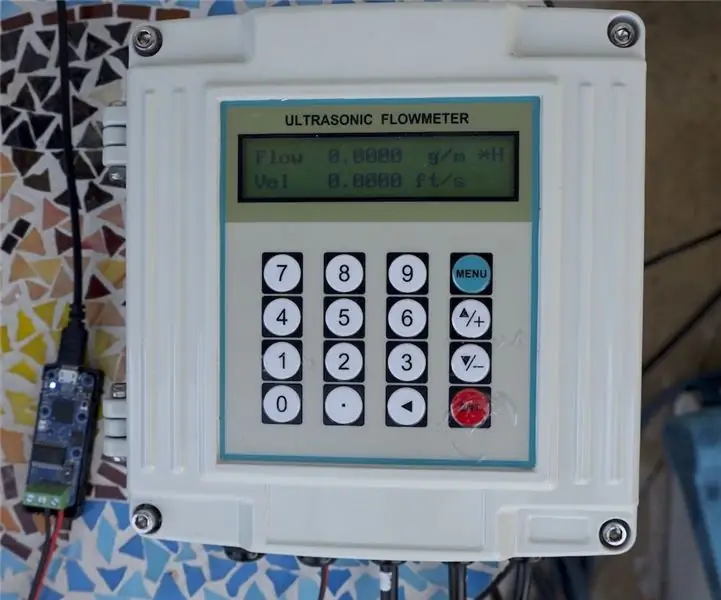
Medición de flujo con medidores de flujo de agua (ultrasónicos): El agua es un recurso fundamental para nuestro planeta. Los seres humanos necesitamos agua todos los días. Y el agua es necesaria para una variedad de industrias y los seres humanos la necesitamos todos los días. A medida que el agua se ha vuelto más valiosa y escasa, la necesidad de un control eficaz y del hombre
Medición de la velocidad del flujo: 7 pasos (con imágenes)
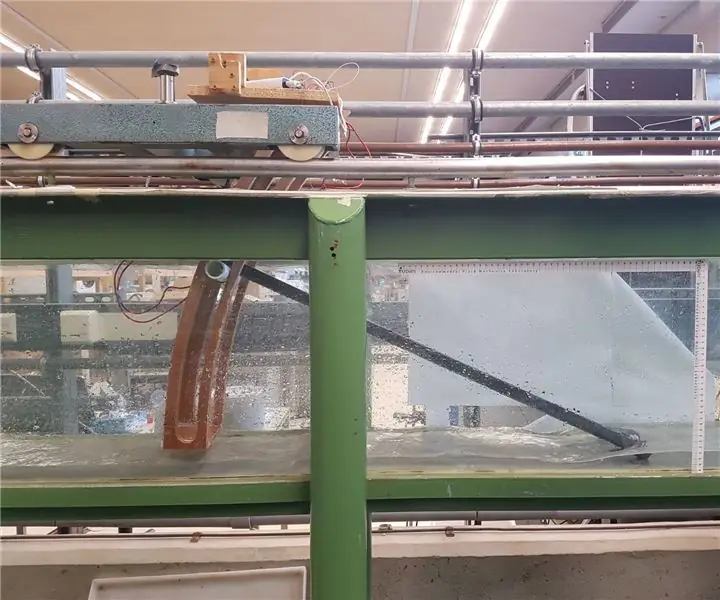
Medición de la velocidad del flujo: con este dispositivo puede medir la velocidad de una corriente que fluye libremente. Lo único que se necesita es Arduino y algunas habilidades básicas de elaboración y, por supuesto, un flujo de flujo libre. No es la forma más práctica de medir la veloci
Autoexcite un alternador sin ningún generador de CC, banco de condensadores o batería: 5 pasos (con imágenes)
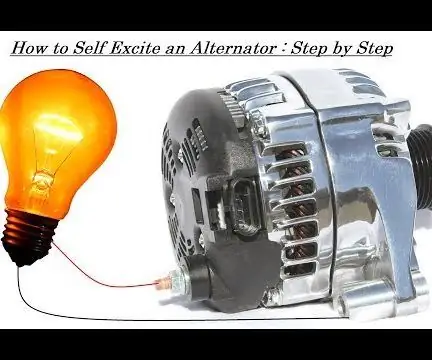
Autoexcite un alternador sin ningún generador de CC, banco de condensadores o batería: ¡Hola! Este instructivo es para convertir un alternador excitado en campo en uno autoexcitado.La ventaja de este truco es que no tendrá que alimentar el campo de este alternador con una batería de 12 voltios, pero en su lugar se encenderá solo para que usted
Sensor de flujo de agua de bajo costo y pantalla ambiental: 8 pasos (con imágenes)
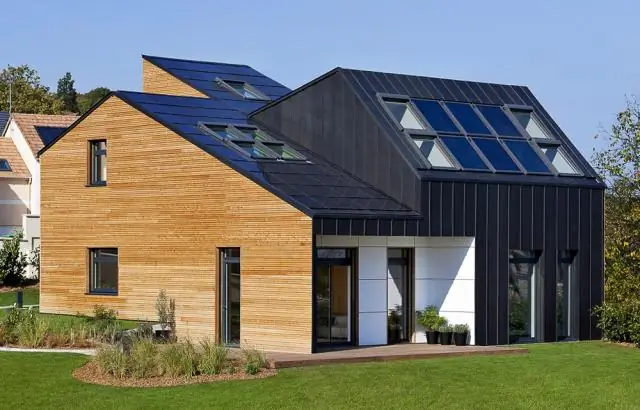
Sensor de flujo de agua de bajo costo y pantalla ambiental: el agua es un recurso precioso. Millones de personas no tienen acceso a agua potable y hasta 4000 niños mueren a diario por enfermedades contaminadas con agua. Sin embargo, seguimos desperdiciando nuestros recursos. El objetivo general de th