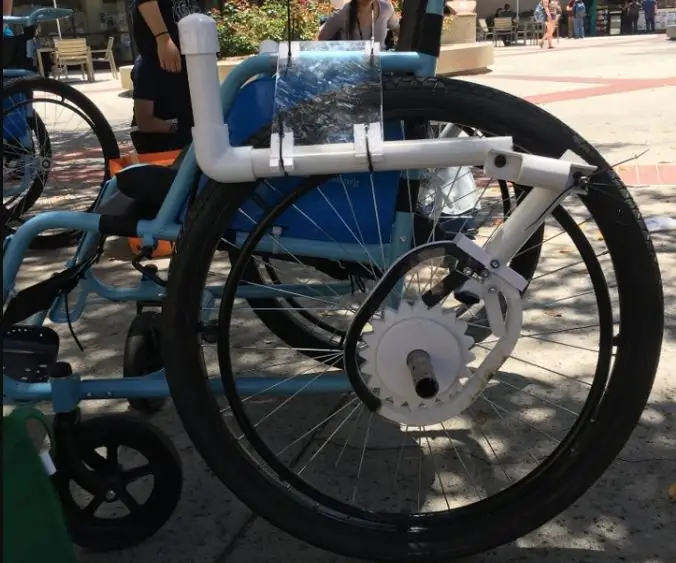
Tabla de contenido:
- Paso 1: Cree la tapa de la carcasa exterior para el cuerpo en SolidWorks
- Paso 2: Cree el cuerpo en SolidWorks
- Paso 3: cree la unión en SolidWorks
- Paso 4: Cree el brazo / manija de palanca en SolidWorks
- Paso 5: Cree el reposabrazos en SolidWorks
- Paso 6: cree el engranaje en SolidWorks
- Paso 7: Cree un trinquete en SolidWorks
- Paso 8: Cree la perilla de dirección en SolidWorks
- Paso 9: cree el montaje en tubería
- Paso 10: Comience el ensamblaje en SolidWorks
- Paso 11: Solicite las piezas de McMaster-Carr
- Paso 12: Obtenga las piezas de la ferretería
- Paso 13: Fabricación de las piezas
- Paso 14: Junte todas las piezas
- Paso 15: Prueba iterativa
- Paso 16: Página de contribuciones
2025 Autor: John Day | [email protected]. Última modificación: 2025-01-23 14:40
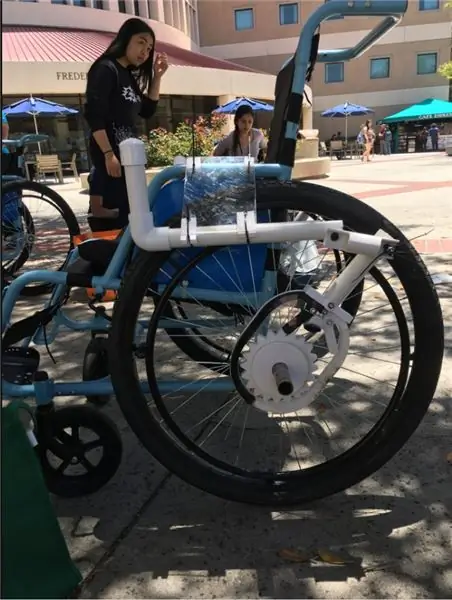
La silla de ruedas común contiene muchos defectos para quienes tienen debilidad en las extremidades superiores o recursos limitados. Nuestro equipo tuvo la tarea de diseñar un controlador de palanca de silla de ruedas para las sillas de ruedas de Free Wheelchair Mission que permitiera a los usuarios ir más lejos en sus sillas y ayudar a las personas con debilidad de las extremidades superiores a usar las sillas. El controlador de palanca de silla de ruedas Support System es un dispositivo rentable que reduce sustancialmente la necesidad de movimiento del hombro y aborda los niveles de fatiga utilizando controladores de palanca horizontales en lugar de verticales, lo que sería adecuado para pacientes debilitados y pacientes en áreas rurales. El típico conductor de brazo de palanca vertical se centra demasiado en los músculos de los brazos y los hombros, lo que puede causar complicaciones a los pacientes con debilidad de las extremidades superiores. Por lo tanto, nuestro equipo diseñó un controlador de palanca horizontal que tenía como objetivo el uso de los músculos del pecho para brindar comodidad a las personas que no pueden utilizar los músculos de los hombros.
Propuesta de mercado y valor
Una forma de abordar el dolor de hombro y la fatiga que se asocia con el uso de silla de ruedas en personas, particularmente de aldeas rurales con caminos no pavimentados, nuestro controlador de palanca tiene como objetivo aliviar el problema mediante el uso de movimientos hacia adelante / hacia atrás en lugar de un movimiento hacia arriba / abajo junto con un reposabrazos mejorado para mayor comodidad y apoyo. Debido a que las aldeas rurales y los caminos no pavimentados suelen ser muy rocosos y poco lisos, el paciente tendría que usar aún más fuerza en el brazo de palanca para mover su silla de ruedas a una cierta distancia en comparación con un camino suave. Por lo tanto, las personas con debilidades en las extremidades superiores en las áreas rurales se ven aún más obstaculizadas porque requieren más movimiento y fuerza para moverse de un lugar a otro, lo que causa problemas a medida que se debilitan continuamente a medida que continúan utilizando los músculos de los hombros en el día a día.. Por lo tanto, al implementar un controlador de palanca horizontal, las personas de áreas rurales con debilidades en las extremidades superiores no solo podrán moverse libremente, sino también de una manera que reduce el uso extenuante de los músculos del hombro, ya que usan la fuerza en su pecho.
Análisis de costos
Decidimos usar PVC, acrílico y ABS. Fue un compromiso de fuerza y costo. Los tres materiales son relativamente más baratos, pero lo suficientemente resistentes para funcionar correctamente. El costo estimado es de aproximadamente $ 170. Originalmente planeamos usar aluminio para la mayoría de los componentes de nuestro impulsor de palanca, como la carcasa exterior y las manijas de los brazos, porque el aluminio es más barato que el acero. Sin embargo, después de investigar, vimos que usar láminas gruesas y varillas de aluminio no sería ideal debido a los costos sobresalientes para obtener cantidades sustanciales de metal. En cambio, encontramos alternativas más baratas utilizando diferentes materiales para diferentes partes. Usamos una lámina acrílica grande para la carcasa exterior y cortamos con láser la lámina en partes más pequeñas, lo que costó alrededor de $ 25. En comparación, las láminas de aluminio grandes habrían costado más de $ 70. Además, también decidimos usar tubos de PVC para nuestros mangos de brazo en lugar de varillas de metal porque los tubos de PVC no solo son resistentes, sino también extremadamente baratos. Aunque las varillas de aluminio pueden haber sido más resistentes, habríamos gastado alrededor de $ 30 en cada lado de la silla de ruedas. En contraste, las tuberías de PVC tuvieron un costo de alrededor de $ 5. La mayor parte de nuestro costo proviene de la impresión ABS 3D. Debido a que imprimimos tres partes de nuestro sistema, el tiempo total para imprimir todas estas partes tomó un total de alrededor de 32 horas. Como resultado, con la tarifa por hora para usar la impresora 3D, el total ascendió a 130 dólares.
Diseño de materiales y prototipos
- Tubería de PVC ~ $ 2.16
- Tapa de enchufe de PVC ~ $ 1.66
- Codo de PVC de 90 grados ~ $ 2.28
- Lámina acrílica ~ $ 24,98
- Engranajes ABS, trinquetes de ABS, perillas de ABS ~ $ 130
- Tornillos de acero ~ $ 6.92
- Bandas de goma ~ $ 3.18
- Adhesivo para manualidades E6000 ~ $ 4.29
Paso 1: Cree la tapa de la carcasa exterior para el cuerpo en SolidWorks
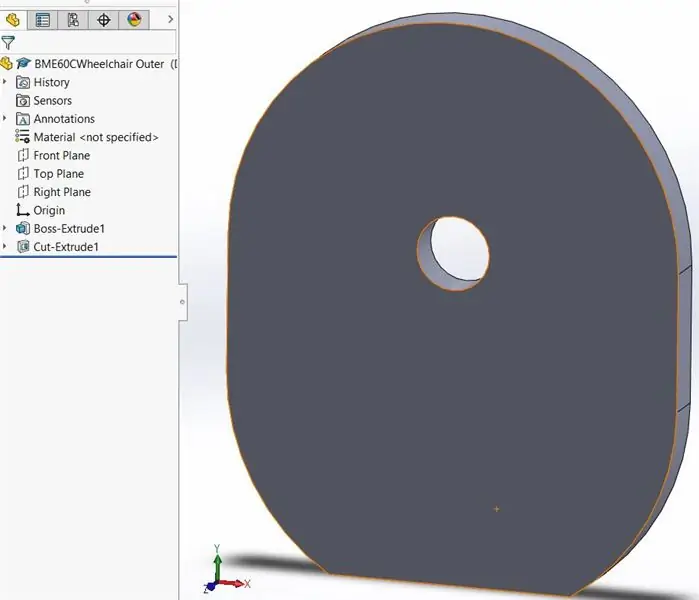
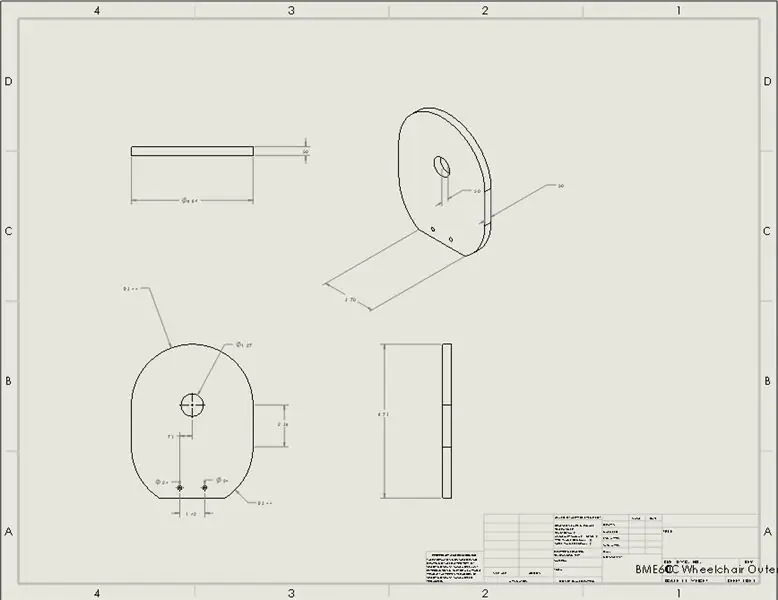
Antes de comenzar todo el proyecto, configure las dimensiones usando MMGS.
Con el plano frontal, cree un nuevo boceto y dibuje un círculo en el origen con un diámetro de 175 mm. Luego, dibuje dos líneas verticales en las tangentes del círculo que sean ambas de 60 mm. Después, dibuja arcos tangentes al final de ambas líneas y conéctalos con una línea horizontal. Luego, usando la función "recortar entidades", recorte la mitad inferior del círculo dentro de la región.
Una vez que se completa el boceto, el jefe extruye el boceto utilizando una extrusión ciega de 12,70 mm. Una vez que se completa la extrusión, abra un nuevo boceto y dibuje un círculo que se alinee con la parte superior de las líneas tangentes con el diámetro de 32.20 mm y corte la extrusión usando "a través de todos" para hacer un agujero.
Para hacer los dos círculos inferiores, abra un nuevo boceto y dibuje dos círculos con un diámetro de 6 mm y hágalos a 15 mm de la parte inferior y 58.84 mm del centro del arco tangente. Una vez que el boceto esté completo, use corte extruido usando "a través de todo" para hacer dos agujeros.
Paso 2: Cree el cuerpo en SolidWorks
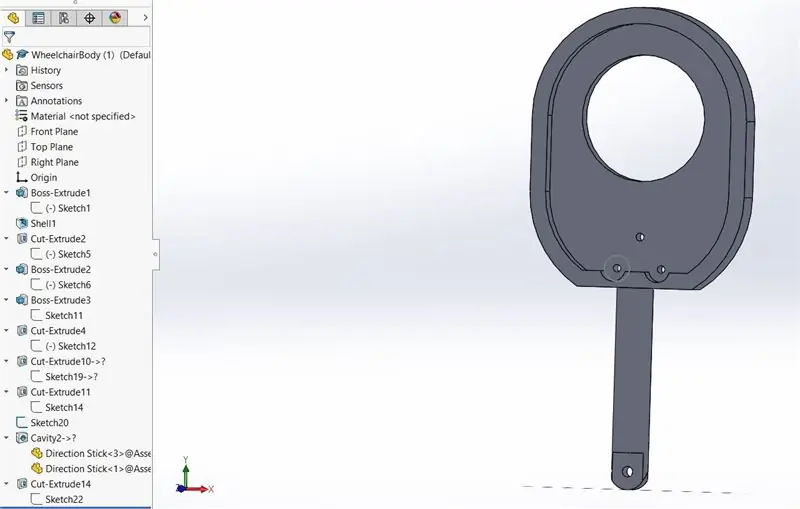
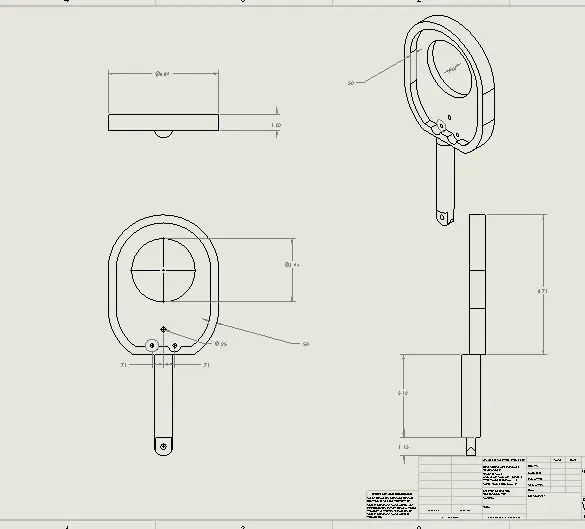
Para comenzar el cuerpo, repita el boceto como en la parte uno para crear la forma general del cuerpo y extrudirlo 25,40 mm. Una vez extruida la pieza, utilice la opción de revestimiento en una de las caras de la pieza con la dimensión 12,70 mm.
Después, abra un nuevo boceto y dibuje un círculo en el centro de la pieza con un diámetro de 100 mm que esté a 133,84 mm de la parte inferior y a 87,50 mm de distancia de los lados de la pieza. Una vez que el boceto esté completo, corte la extrusión usando "a través de todo" una vez más para crear un agujero.
Para crear la palanca, cree un nuevo boceto en el plano superior y gire la pieza hacia abajo. Comience el boceto haciendo un círculo con un diámetro de 28,74 mm en la base de la pieza anterior y extrudirlo 130 mm.
Una vez creada la palanca, cree un nuevo boceto en la base de la palanca. Dibuja dos líneas horizontales equidistantes del origen de 25,10 mm de largo. Después, conecte las dos líneas con arcos tangentes con una altura de 14 mm. Una vez que el boceto esté completo, extruya a ciegas el nuevo boceto 30 mm.
Con la pieza extruida más nueva, cree un nuevo boceto en el plano frontal y dibuje un círculo que esté a 14,95 mm de la parte superior y 12,55 mm del lateral. Luego, corte la extrusión a través de todo para crear un agujero.
Con el cuerpo completo, dibuje dos orificios en la parte inferior del cuerpo con diámetros de 6 mm y una distancia de 36 mm entre sí, 15 mm de la parte inferior y 58.84 mm de la parte superior de los arcos tangentes. Después, corte la extrusión a través de todo para crear dos agujeros.
En la parte inferior de la pieza, cree un nuevo boceto. Haz líneas rectas en ambos lados de 14,93 mm. Haga una línea horizontal de 28,74 mm para conectar las dos líneas. Dibuja un círculo que tenga un radio de 14,37 mm y alinéalo con el círculo del centro. Córtalo para hacer un semicírculo. Corte la extrusión a través de toda la figura en forma de rampa en la parte inferior de la pieza para dejar un borde redondeado.
* Para prepararse para la cavidad, cree un nuevo boceto en el plano posterior. Dibuja un círculo con un radio de 20,57 mm a 15 mm de la parte inferior y 58,84 del arco tangente lateral. Después de ensamblar todas las piezas juntas, edita la pieza dentro del ensamblaje y usa la función de cavidad para crear los semicírculos.
En el plano frontal, haz un nuevo boceto. Dibuja un círculo en el centro con un diámetro de 6,35 mm entre el círculo grande y los dos círculos pequeños cerca de la parte inferior. Haga el círculo a 40,13 mm de la parte inferior y 33,70 mm del arco tangente en los lados. Después, corte la extrusión a través de todo para crear un pequeño círculo en el centro.
* Este paso continuará más adelante después de ensamblar todas las piezas.
Paso 3: cree la unión en SolidWorks
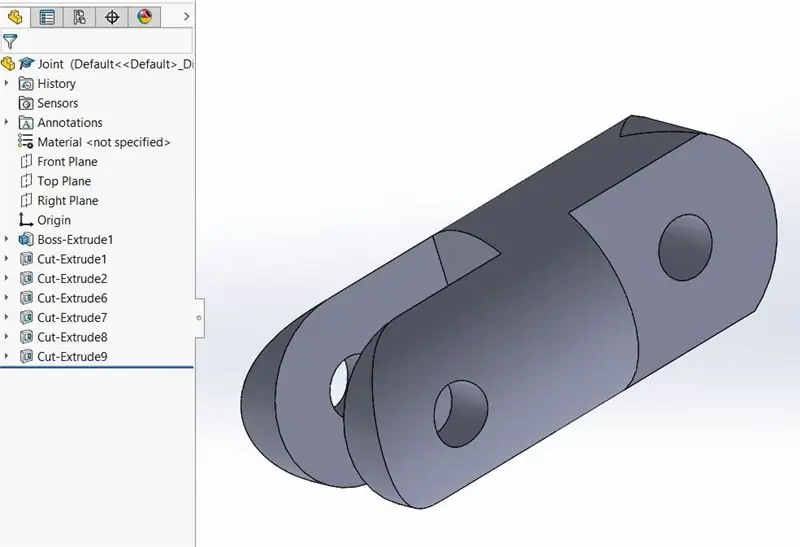
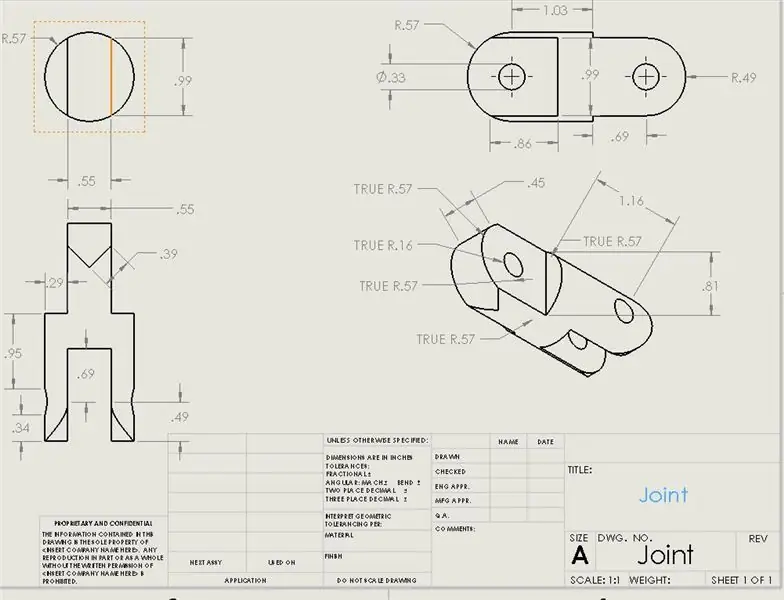
Para comenzar la unión, comience creando un nuevo boceto en la placa frontal y dibuje un círculo con un diámetro de 28,74 mm. Extruir a ciegas el círculo que se acaba de esbozar de 120 mm.
Luego, rote la pieza y dibuje en la parte posterior. Dibuja dos líneas verticales con una longitud de 25,10 mm y 7,37 mm desde el borde del círculo. y corte extruido utilizando "ciego" y una profundidad de 30 mm para ambas regiones.
A continuación, mirando desde el plano derecho, dibuje un círculo en la región que acabamos de cortar. El diámetro debe ser de 8,38 mm con una distancia de 12,55 mm desde el borde superior y 14,95 mm desde el borde lateral. Haga un corte ciego de 30 mm.
En el plano de la derecha, haga líneas rectas en ambos lados que sean de 15.05 mm. Haga una línea vertical de 28,74 mm para conectar las dos líneas. Dibuja un círculo que tenga un radio de 14,37 mm y alinéalo con el círculo del centro. Córtalo para hacer un semicírculo. Corte la extrusión a través de toda la figura en forma de rampa en la parte inferior de la pieza para dejar un borde redondeado.
Después, mirando desde el plano posterior, dibuje dos líneas verticales con una longitud de 25,10 mm y 7 mm desde el centro. Realice un corte ciego con una profundidad de 35 mm.
En el plano derecho, dibuje un círculo en la parte derecha con el centro a 17.24 mm de distancia del borde izquierdo de la parte corte ciego extruya a través de todo para crear un círculo
En el plano derecho, repita la figura en forma de rampa en el lado izquierdo de la pieza.
Paso 4: Cree el brazo / manija de palanca en SolidWorks
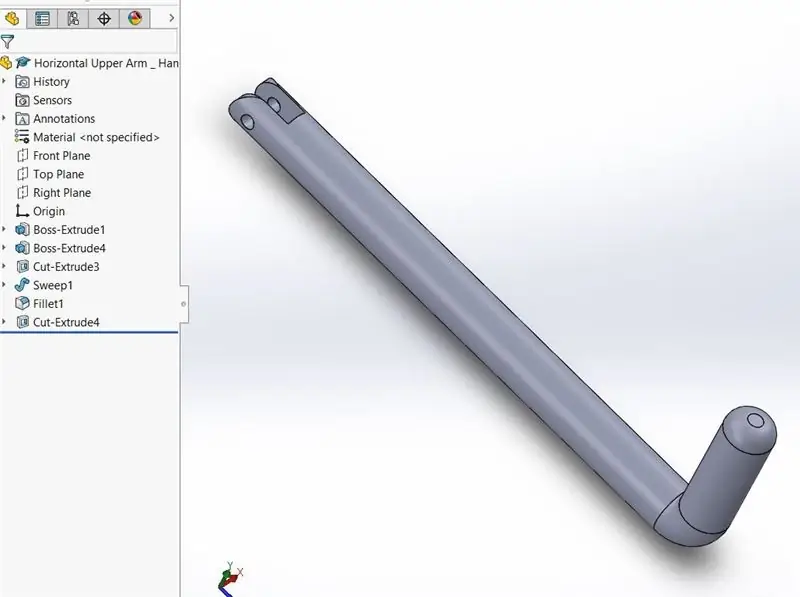
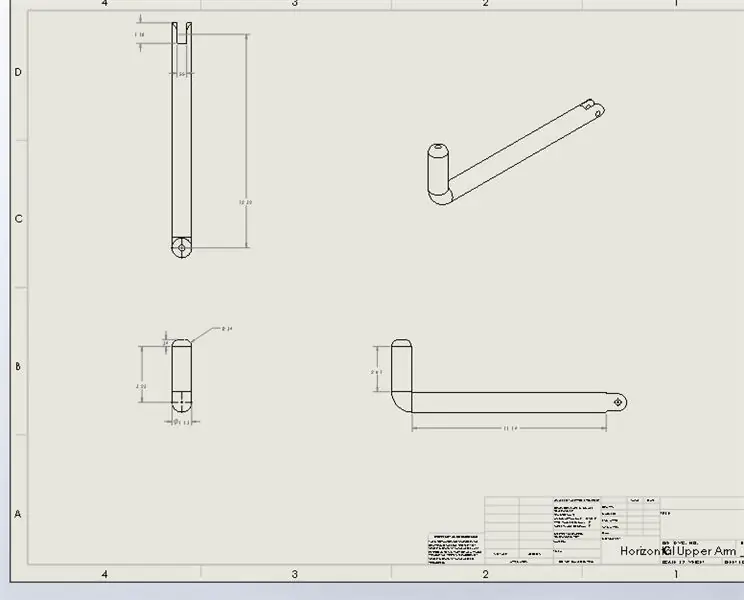
En el plano frontal, dibuje un círculo con un diámetro de 28,75 mm en el origen. Boss lo extruye 275 mm.
A continuación, vaya al plano posterior y dibuje dos líneas verticales con una longitud de 25,10 mm con una distancia de 7 mm desde el centro. Extruya las dos líneas para que haya un espacio en el medio con una dimensión de extrusión de 35 mm.
En la pieza que acabamos de extruir, esboce un círculo con un diámetro de 8,40 mm con una distancia de 17,76 mm desde el centro del círculo hasta el borde y 12,56 mm desde la parte inferior de la pieza. Corta la extrusión a través de todo para crear un agujero.
En el plano derecho, cree una línea corta con una longitud de 9,24 mm que se conecte con el extremo izquierdo de la pieza. Dibuja un arco con un radio de 30 mm. Luego, dibuja una línea vertical que conecte el otro extremo del arco con la longitud de 76,39 mm. Una vez completado el boceto, barra el boceto.
Después, filetee la parte superior de la parte que acabamos de barrer 10 mm.
Por último, en el plano de la derecha, traza líneas rectas horizontales a ambos lados de la pieza con el agujero que creamos de 17,78 mm de largo. Haga una línea vertical de 25,10 mm para conectar las dos líneas. Dibuja un círculo que tenga un radio de 12,56 mm y alinéalo con el círculo del centro. Córtalo para hacer un semicírculo. Corte la extrusión a través de toda la figura en forma de rampa en la parte inferior de la pieza para dejar un borde redondeado.
Paso 5: Cree el reposabrazos en SolidWorks
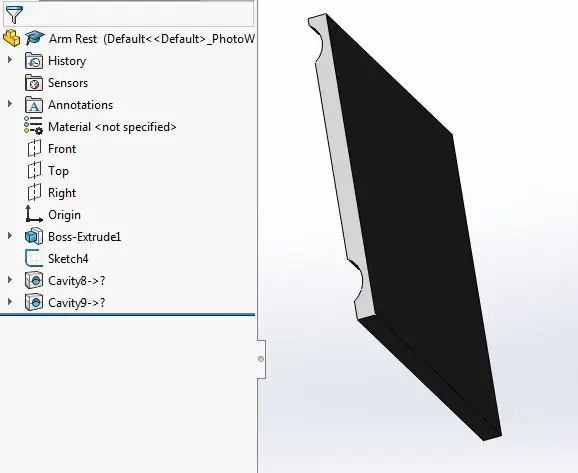
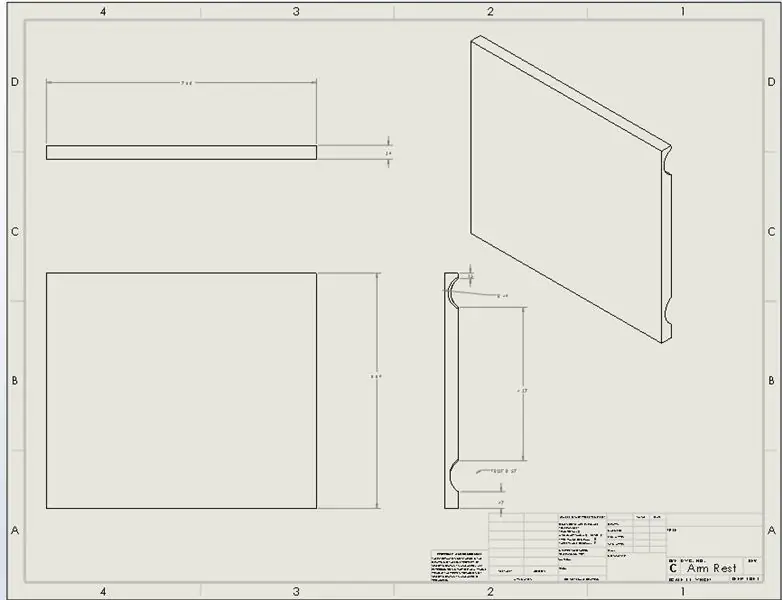
En el plano frontal, dibuje un rectángulo con una altura de 170 mm y una longitud de 195 mm y haga una extrusión ciega de 10 mm.
* Después del ensamblaje, use la función de cavidad para crear las muescas en el prisma rectangular
Paso 6: cree el engranaje en SolidWorks
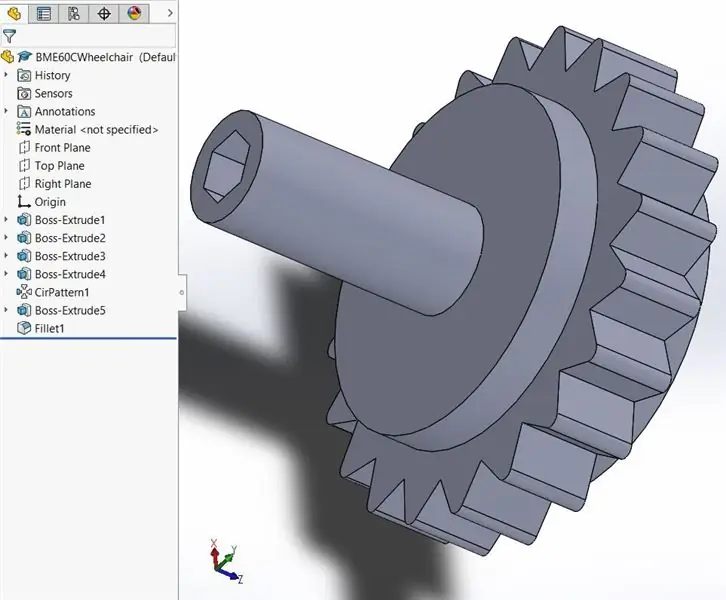
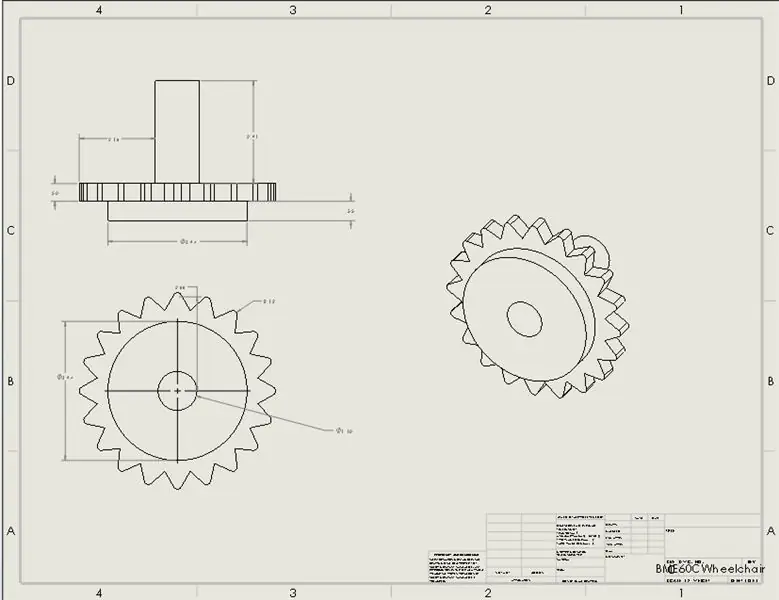
Para comenzar el engranaje, cree un nuevo boceto en el plano frontal y dibuje dos círculos desde el mismo punto con los diámetros de 25,40 mm y 31,75 mm. Luego, extruya la protuberancia utilizando una extrusión ciega a 30 mm.
Una vez realizada la extrusión, cree otro boceto en el plano frontal y dibuje otro círculo con un diámetro de 31,75 mm y extruya 20 mm.
A continuación, dibuje en el plano frontal un círculo con un diámetro de 100 mm y extrudirlo de 12,70 mm.
En la parte superior de la pieza que acabamos de extruir, dibuja un triángulo equilátero con lados de 30 mm. Extruya el triángulo 12,70 mm.
Una vez finalizada la extrusión, utilice la función de patrón circular para tener 20 triángulos uniformes alrededor de la pieza. Luego, empalme todos los bordes de los triángulos.
En el plano frontal, dibuje otro círculo con un diámetro de 100 mm y extrúyalo 13,97 mm.
Para crear el orificio en el medio del engranaje, dibuje un círculo en el plano posterior con un diámetro de 27,94 mm y corte la extrusión hasta la superficie.
Paso 7: Cree un trinquete en SolidWorks
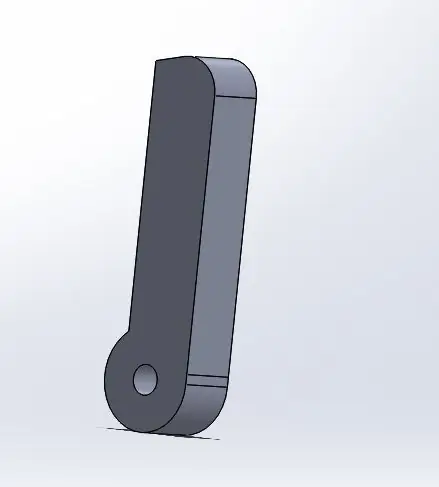
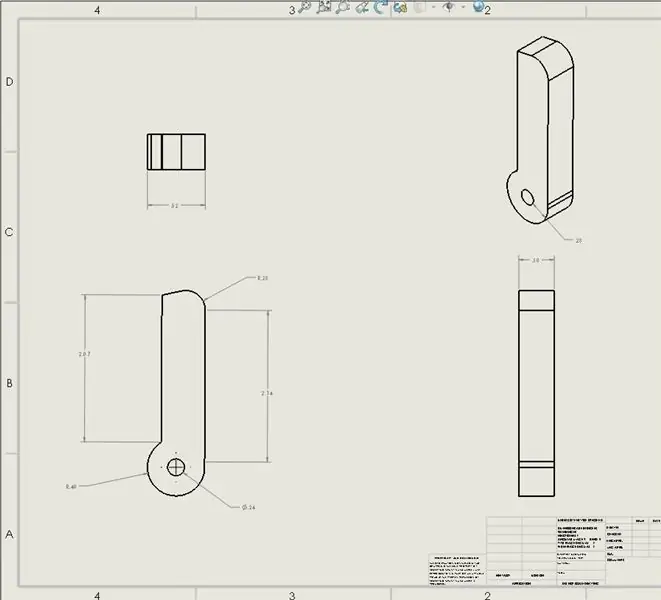
En el plano frontal, dibuje una línea vertical con una longitud de 2.07 pulgadas. Luego, dibuja un arco con un radio de 0.40 pulgadas conectando con la parte inferior de la línea vertical. Además, dibuje una línea horizontal conectada con el borde superior de la línea vertical. Usando dimensiones inteligentes, haga clic en el borde superior y luego en la línea vertical y establezca el ángulo en 78,00 grados.
Una vez establecido el ángulo, dibuje otra línea vertical que se conecte con la línea inclinada con una longitud de 2,14 pulgadas. Luego, empalme el borde de esta línea con la línea horizontal con un radio de 0.28 pulgadas.
Una vez que el boceto esté completo, extruya el saliente usando una extrusión ciega de 0.5 pulgadas. Para crear el agujero en el medio, dibuje un círculo que tenga un radio de 0.12 pulgadas en el centro de la pieza y use corte extruido a través de todo.
Paso 8: Cree la perilla de dirección en SolidWorks
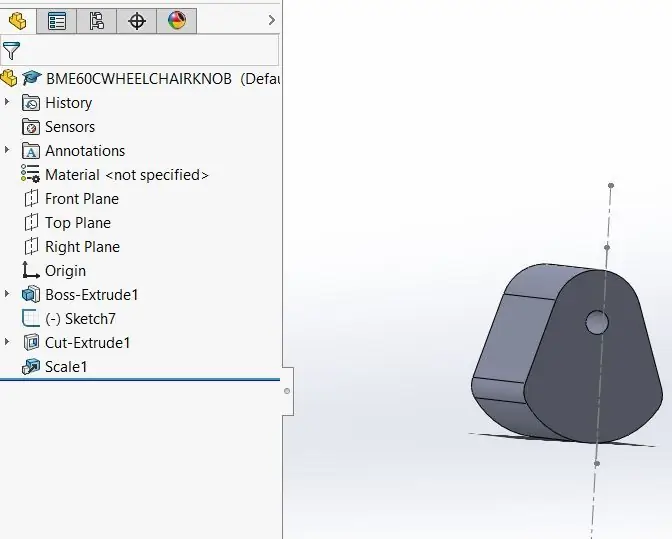
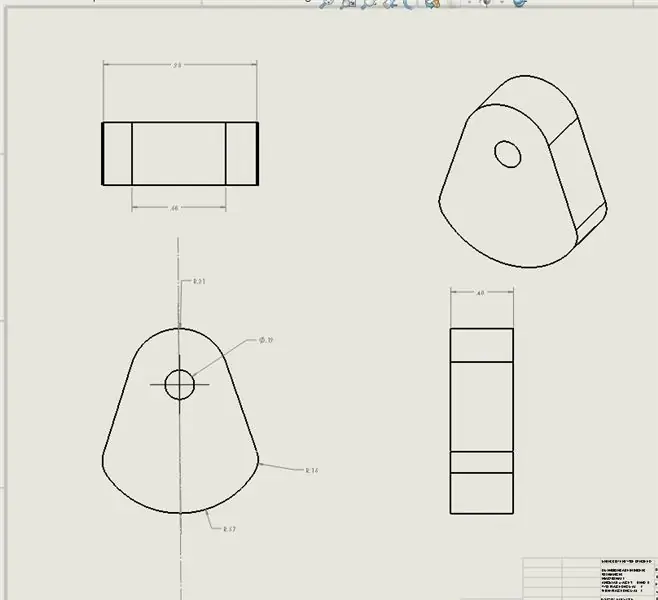
En el plano frontal, dibuje una línea central vertical. Luego, en la parte superior de la línea central, dibuje un arco con un radio de 10 mm. Luego, en ambos lados dibuje líneas inclinadas con una longitud de 18,26 mm. Luego, dibuje un arco en ambos lados con un radio de 5 mm. Para conectar ambos lados, dibuje otro arco con un radio de 18 mm. Extruya el boceto utilizando una extrusión ciega de 12,70 mm.
Para crear un agujero, dibuje un círculo con un diámetro de 5,90 mm que tenga el centro a 8 mm del origen. Utilice corte extruido hasta la superficie.
Escale la parte sobre el centroide con un factor de escala de 0,8 mm.
Paso 9: cree el montaje en tubería
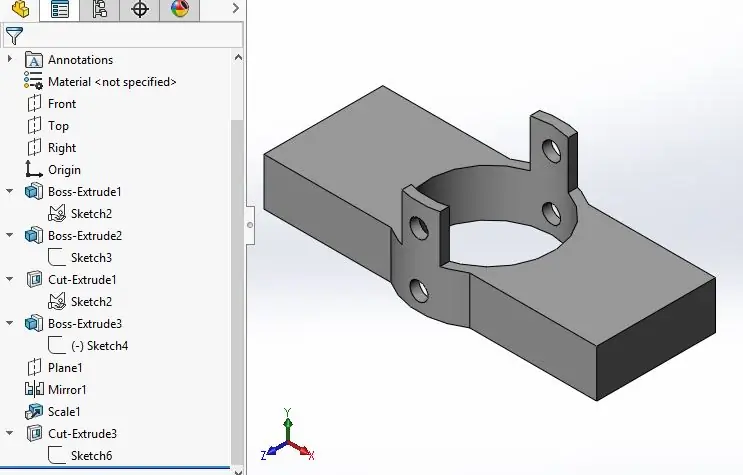
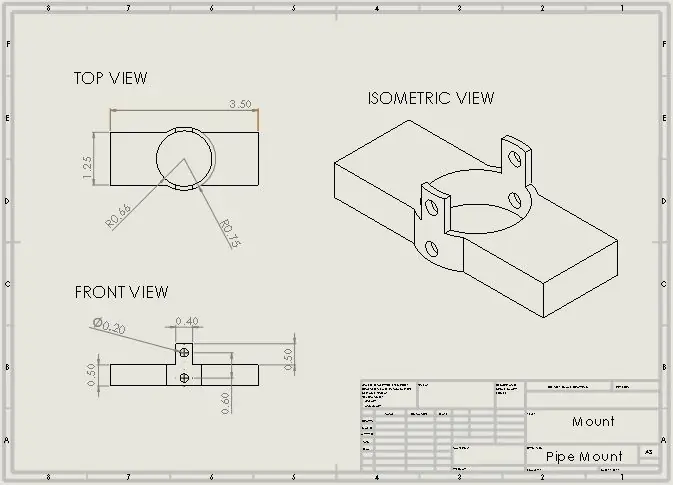
Para crear el soporte de tubería que sujetará el brazo de palanca al cuerpo del engranaje, comience con un boceto de dos círculos. El círculo interior debe tener el diámetro de la tubería de PVC para que pueda deslizarse fácilmente a su alrededor, por lo tanto, debe ser de 1.3125 pulgadas. El círculo exterior debe ser de aproximadamente 1,5 pulgadas. Asegúrese de que los dos círculos sean concéntricos y extruya la parte entre los dos círculos en 0,5 pulgadas. Luego, dibuje un rectángulo que coincida con la cara inferior de la carcasa exterior del engranaje. Este sería un rectángulo de 3,5 pulgadas por 1,25 pulgadas. Centre este rectángulo alrededor del círculo estableciendo el borde largo del rectángulo a 1,75 pulgadas del centro del círculo y el borde corto del rectángulo a 0,63 pulgadas del centro del círculo. Extruye el rectángulo por 0,5 pulgadas. Debido a que algunas partes del rectángulo se encuentran dentro del círculo interior, corte y extrudir el círculo interior para despejarlo. A continuación, desde el plano superior de la pieza, dibuje una línea central desde el círculo hasta la parte exterior del borde extruido. Desde este punto central en el borde extruido, dibuje un rectángulo que vaya 0.2 pulgadas a ambos lados. Extruye este pequeño rectángulo por 0,5 pulgadas. Cree un plano de referencia frontal a través del centro de la pieza y utilice la función de espejo para crear un rectángulo extruido idéntico en el otro lado del círculo.
Al imprimir piezas en 3D, siempre es una buena idea escalar todo ligeramente para evitar interferencias al colocar la pieza en el ensamblaje. En este caso, toda la parte se amplió en 1,05. Finalmente, dibuje dos círculos de 1/4 de pulgada de diámetro colocados en la cara frontal del centro de la pieza con uno en el rectángulo pequeño y otro en el lado del círculo. Asegurándose de que los dos círculos estén relacionados verticalmente, luego se pueden cortar a través de toda la parte, cortando cuatro círculos en total. Estos serían orificios en los que se pueden colocar los pernos para conectar el PVC al cuerpo principal de la carcasa del engranaje.
Paso 10: Comience el ensamblaje en SolidWorks
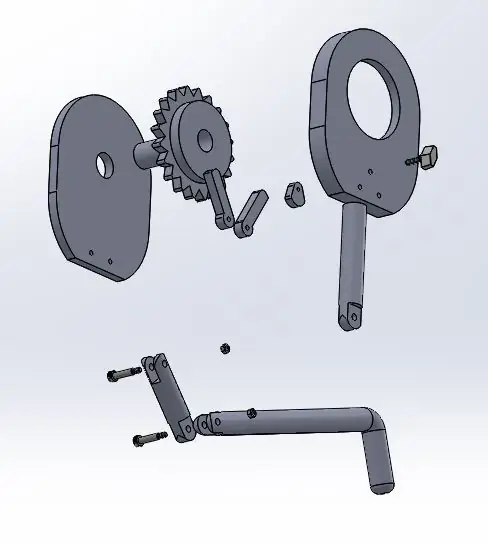
Primero, inserte todas las piezas que se crearon en los pasos anteriores junto con la perilla exterior, los tornillos y las tuercas, haciendo que el cuerpo de la silla de ruedas sea el componente básico.
Comience por acoplar el cuerpo y el engranaje haciendo clic en el borde del engranaje y el borde del cuerpo y use un compañero concéntrico. Luego, haga clic en la cara del engranaje y el cuerpo para crear una relación de posición coincidente.
Luego, empareje el cuerpo y la perilla de dirección haciendo clic en la cara de la perilla de dirección y el cuerpo para hacer una relación de posición coincidente.
Ahora, haga coincidir la perilla exterior y el cuerpo de la silla de ruedas haciendo clic en la cara de la perilla exterior y el cuerpo para crear una posición coincidente.
Cree una relación de posición concéntrica haciendo clic en la cara del cuerpo y la cara del botón exterior.
Luego, cree una relación de posición concéntrica haciendo clic en la cara de la perilla de dirección y el borde del cuerpo.
Ahora haga clic en las caras del cuerpo y el trinquete para crear una relación de posición coincidente y repita para el otro trinquete.
Cree una relación de posición tangente haciendo clic en la cara de la perilla de dirección y el trinquete y repita para el otro trinquete.
A continuación, cree una relación de posición coincidente haciendo clic en la cara del cuerpo y la carcasa exterior y cree una relación de posición concéntrica haciendo clic en la cara del cuerpo y el borde de la carcasa exterior. Luego haga que la cara del cuerpo y la cara de la carcasa exterior sean paralelas.
Cree un ángulo límite que tenga un valor máximo de 78 grados y un valor mínimo de 35 grados para la cara del cuerpo y la cara del trinquete y repita para el otro trinquete
Después, relacione la articulación y el cuerpo haciendo clic en la cara de ambos para crear una relación de posición concéntrica. A continuación, cree una relación de posición de ancho centrada para ambas caras de la unión y el cuerpo.
Luego, cree una relación de posición concéntrica para el borde del brazo de palanca y el borde de la junta. Cree otra relación de posición de ancho centrada para ambas caras de la junta y el brazo de palanca.
Haga otro acoplamiento concéntrico para la cara de la junta y el tornillo. Luego, cree una relación de posición tangente haciendo clic en la cara de la unión y la cara del tornillo.
En el plano de la derecha, dibuje dos líneas de eje para futuras referencias de acoplamiento, siendo la primera línea donde el cuerpo se encuentra con la articulación y la segunda donde la articulación se encuentra con el brazo de palanca.
A continuación, cree una relación de posición concéntrica haciendo clic en la cara del brazo de palanca y el segundo tornillo. Una vez acopladas, cree otra relación de posición tangente con ambas caras de ambos componentes.
Con el primer eje dibujado anteriormente, haga coincidir el borde de la primera tuerca y el eje para crear una relación de posición concéntrica.
Utilice una posición coincidente para la cara del primer tornillo y la primera tuerca y repita para el segundo tornillo y la tuerca.
Haga una relación de posición concéntrica con el borde de la segunda tuerca y el segundo eje.
Cree otra relación de posición concéntrica con la cara del cuerpo y la cara externa del primer tornillo. Además, cree una relación de posición coincidente para estas partes.
Haga una coincidencia concéntrica para la cara del trinquete y la cara externa del tercer tornillo.
Cree una relación de posición coincidente con la cara del cuerpo y la cara externa del tercer tornillo.
A continuación, cree otra relación de posición concéntrica haciendo clic en la cara de la carcasa exterior y la cara exterior del tercer tornillo y hágalos coincidir.
Haga una relación de posición concéntrica haciendo clic en la cara del cuerpo y la cara del trinquete y hágalos coincidir. Repita para el otro trinquete.
Haga una relación de posición concéntrica haciendo clic en la cara de la perilla de dirección y la perilla exterior.
Por último, empareje la cara del cuerpo y el borde de la perilla de dirección para crear un emparejamiento concéntrico.
Paso 11: Solicite las piezas de McMaster-Carr
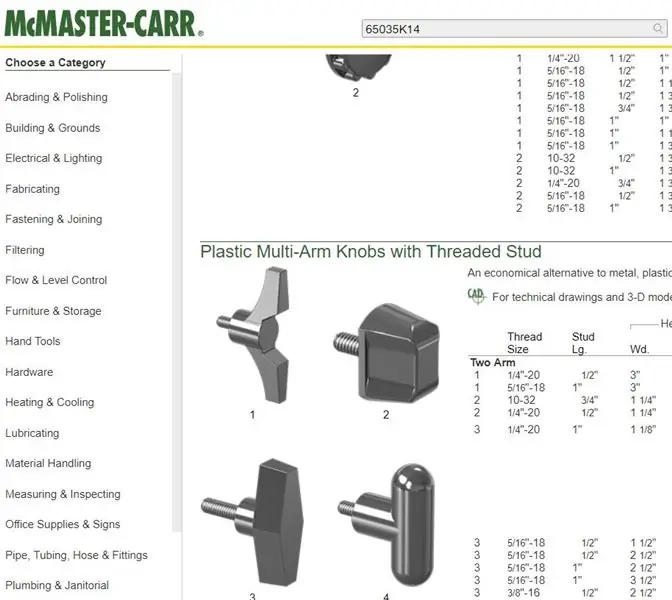
Solicite la perilla de plástico de dos brazos (perilla exterior), el tornillo de hombro de aleación de acero, las tuercas hexagonales de acero y las bridas para cables de McMaster-Carr. Los números de artículo son 65035K14, 92981A205, 90592A016 y 70215K61, respectivamente.
Paso 12: Obtenga las piezas de la ferretería
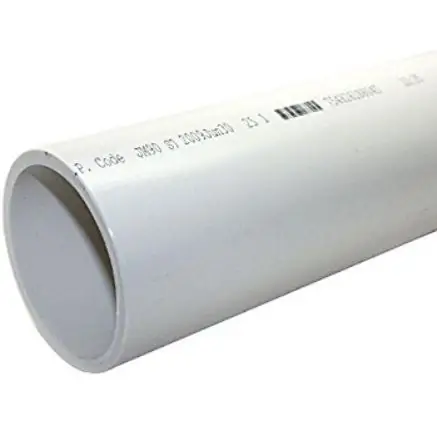
En una ferretería local, obtenga lo siguiente:
- Lámina acrílica de 18 "x 24" x.220"
- Adhesivo transparente (Adhesivo E6000)
- Tapa de enchufe de PVC de 1 (2)
- Tubería de PVC de extremo plano de 1 x 10 '
- Codo de PVC de 90 grados de 1 (2)
Paso 13: Fabricación de las piezas
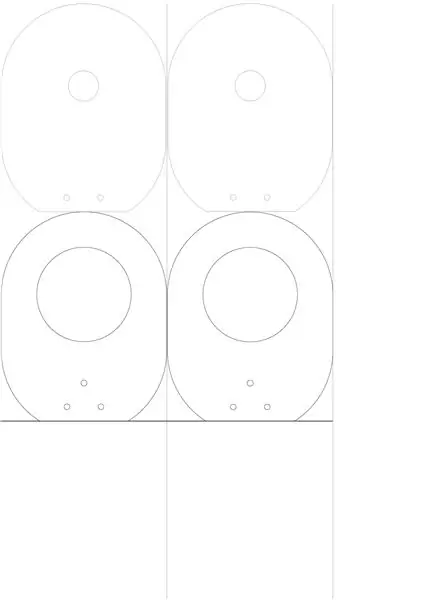
Piezas impresas en 3D: prepare las piezas de SolidWorks y conviértalas en archivos STL. A partir de ahí, coloque las piezas en el software Makerware y disponga las piezas necesarias para imprimir (carcasa del cuerpo, engranajes, pieza de montaje, trinquetes, perilla de dirección, muescas del reposabrazos *). Si las piezas no encajan en la base de la impresora, espere para volver a imprimir. Al imprimir, asegúrese de agregar soportes y balsas para evitar que las impresiones fallen.
Piezas cortadas con láser: Con el acrílico de 18 "por 24", se pueden fabricar las placas frontal y posterior de la carcasa exterior del cuerpo. Esto se puede hacer tomando la cara frontal de ambas placas en SolidWorks y guardándolas como un archivo DWG. Luego, estos se pueden cargar en el software de corte por láser (en este caso Epilog) en el que se puede configurar su orientación como se muestra en la imagen. Se cortarán dos de cada uno del acrílico, y del material restante, se cortarán dos rectángulos. Los rectángulos servirán como reposabrazos.
Piezas cortadas a mano: tome los tubos y córtelos en diferentes longitudes (dos de 4.5 pulgadas para el mango, dos de 4.5 pulgadas para la junta, dos de 6.5 pulgadas para la palanca y dos de 13.25 pulgadas para el brazo). A partir de ahí, corte las piezas del brazo de 13.25 pulgadas en un extremo (30 o 35 mm) por el medio del otro lado de la tubería y taladre un orificio de 1/4 a 15 mm de los bordes de la tubería. Corte y taladre dos de los Piezas de unión de 4.5 pulgadas de la misma manera pero en ambos lados de la tubería de PVC de unión. Haga lo mismo (corte y taladro) en un lado del brazo de palanca, tubería de 6.5 pulgadas.
* Se pueden utilizar las muescas del reposabrazos o todo el reposabrazos del paso anterior.
Paso 14: Junte todas las piezas
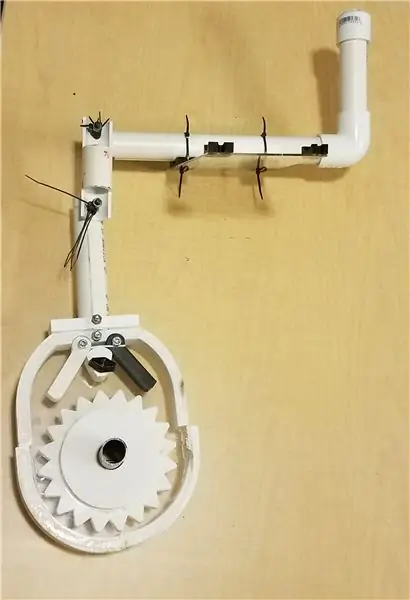
Montaje del cuerpo:
Tome las piezas exteriores del cuerpo cortadas con láser y las piezas de la carcasa impresas en 3D. Tome un lado de la carcasa exterior y pegue las piezas de la carcasa en consecuencia a los bordes de la carcasa. Luego, tome una banda de goma y envuélvala alrededor de los dos trinquetes. Coloque los trinquetes en sus respectivas ubicaciones y use el perno parcialmente roscado y colóquelo a través del orificio del cuerpo y los trinquetes. Luego, tome la perilla de dirección y la perilla de plástico. Coloque la perilla de plástico a través de la carcasa exterior y gire las dos juntas con la carcasa exterior entre las dos. Finalmente, coloque el engranaje en su respectivo orificio y coloque la tapa superior de la carcasa exterior sobre el engranaje y pegue la carcasa a la carcasa exterior superior. Déjalo reposar y secar. Recuerde también asegurar los dos pernos parcialmente roscados con las tuercas hexagonales después de colocar y pegar la tapa superior a la carcasa.
Tome el tubo de PVC de palanca de 6.5 pulgadas y péguelo en la parte inferior del cuerpo. A partir de ahí, déjalo reposar y secar. Tome la pieza montada y deslícela a través del tubo hasta que quede plana en la cara inferior del cuerpo. Tome una broca de 1/4 de pulgada y taladre los orificios en la tubería y a través del cuerpo en sus respectivos lugares. Asegure los pernos con una tuerca hexagonal.
Montaje del reposabrazos:
Con el reposabrazos, simplemente coloque y pegue las muescas en las 4 esquinas del reposabrazos. Luego, taladre dos orificios (orificios de 5/32 '') a cada lado de las muescas y coloque bridas a través de ellos. Las muescas más grandes se pueden alinear y atar con cremallera al tubo de PVC de 13 pulgadas del brazo de palanca. La sangría más pequeña debe alinearse y luego colocarse en el brazo de la silla de ruedas antes de su uso.
Montaje del brazo de palanca:
Coloque la tapa en el tubo del mango de 4.5 pulgadas y coloque el codo de manera segura en el otro lado. Con la otra abertura del codo, coloque el tubo del brazo de 13 pulgadas y conéctelo a un lado de la junta (tubo de 4.5 pulgadas) con un perno de hombro. En el otro lado de la junta, tome otro perno de hombro y únalo con la pieza del brazo de palanca (tubo de 6.5 pulgadas). Tome una tuerca hexagonal y asegure el perno de hombro. Debido a que los pernos de hombro están parcialmente roscados, las uniones en las que está unido pueden ser endebles. Para hacer las uniones más apretadas y seguras, coloque alrededor de cinco cierres alrededor de cada perno de hombro para apretar cada unión.
Paso 15: Prueba iterativa
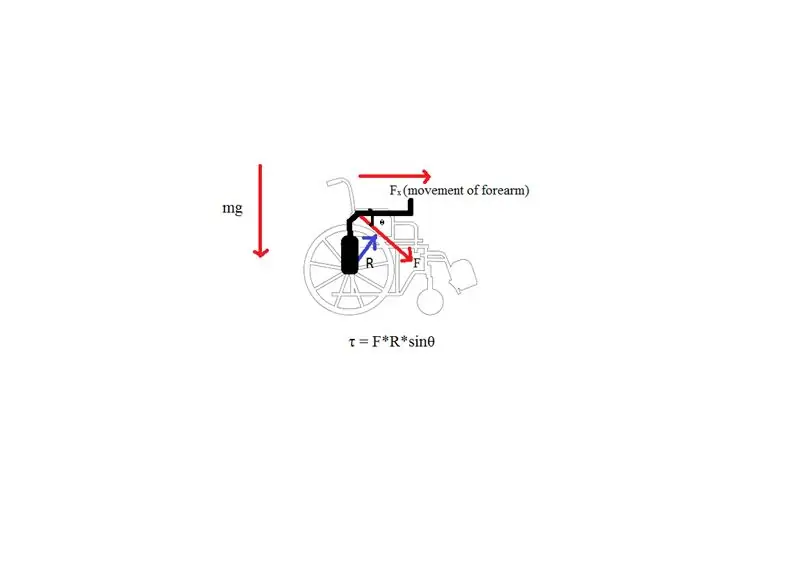
Para realizar la prueba, asegúrese de tener acceso a una de las sillas de ruedas.
Coloque el brazo de palanca en la rueda. Asegúrese de que las partes encajen donde se supone que deben ir y asegúrese de que ciertas partes estén paralelas a las partes respectivas de la silla de ruedas, como el reposabrazos. Asegúrese de que los orificios perforados en el tubo de aluminio y el cuerpo del brazo de palanca estén alineados. Si las piezas son desproporcionadas, retroceda y realice algunos cambios de dimensión.
Una vez que las dimensiones y relaciones sean correctas, haga que un probador se siente en la silla de ruedas y use el brazo de palanca. Como se muestra en el diagrama de cuerpo libre, el probador empujará hacia adelante horizontalmente para crear una fuerza diagonal que se usaría para crear un torque e impulsar la silla de ruedas hacia adelante. Analizar cualquier problema: fragilidad de la junta, exceso o falta de espacio horizontal, rotura de piezas, etc.
Analiza problemas y rediseña de nuevo.
En nuestro prototipo, la silla de ruedas se movía, pero a un ritmo lento. La parte del cuerpo no terminó de pegar a tiempo, por lo que el brazo de la palanca se rompió durante nuestra prueba de funcionamiento. Además, la articulación puede haber sido demasiado grande y floja, y puede que no haya suficiente espacio horizontal y movimiento en el brazo de palanca, lo que restringe la cantidad de fuerza ejercida por empuje.
Paso 16: Página de contribuciones
Contribuciones individuales para el sistema de apoyo
Gerente de proyecto: Sophia Ynami 12732132
- La directora del proyecto, Sophia Ynami, era responsable de asegurarse de que todos los miembros del grupo fueran responsables de sus respectivos deberes y de que todas las tareas se completaran de manera oportuna. Ayudé en el proceso de ensamblaje final y probé e hice ajustes al dispositivo antes de la ejecución final.
Fabricante: Yvonne Szeto 94326050
- El fabricante, Yvonne Szeto, fue el encargado de preparar los diferentes componentes para el montaje. Fui responsable de cortar con láser las materias primas, perforarlas e imprimirlas en 3D en diferentes partes. También ensamblé los diferentes componentes juntos.
Ingeniero de materiales: Willis Lao 15649487
- El ingeniero de materiales, Willis Lao, fue responsable de decidir qué materiales usar para cada componente del proyecto y de ordenarlos / recogerlos de McMaster Carr / Home Depot. También contribuí a los Instructables escribiendo la introducción, el análisis de costos, el proceso paso a paso de creación de piezas y el ensamblaje.
Probador: Matthew Maravilla 25352925
- El probador, Matthew Maravilla, fue responsable de supervisar y analizar el método de prueba iterativo, incluida la prueba del brazo de palanca y el informe de los cambios de dimensión o pieza a ajustar. También fui responsable del esquema y la mayoría de los Instructables.
Diseñador principal: Anthony Cheuk 30511803
- El diseñador principal, Anthony Cheuk, fue responsable de idear un diseño factible teniendo en cuenta los diferentes materiales que se podrían utilizar y preparar los archivos y el diseño listos para la fabricación (impresión 3D y corte por láser).
Recomendado:
Silla de ruedas con acelerómetro para personas con discapacidad física: 13 pasos
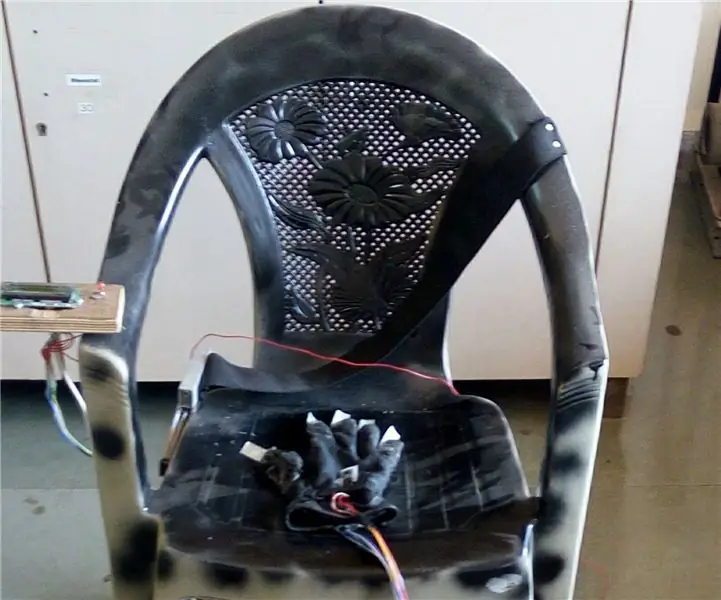
Silla de ruedas con acelerómetro para personas con discapacidades físicas: En nuestro país de 1.300 millones de habitantes, todavía tenemos más del 1% de la población de personas mayores o discapacitadas, que necesitan apoyo para la movilidad personal. Nuestro proyecto tiene como objetivo cumplir con su requisito de movilidad con tecnología inteligente. El problema
Silla de ruedas para perros: 4 pasos
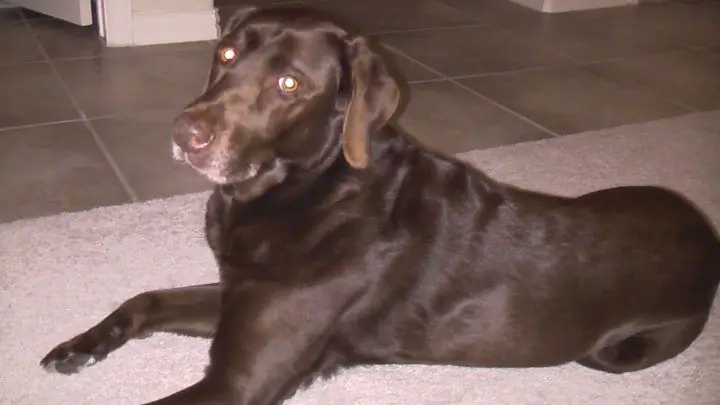
Silla de ruedas para perros: Hola, hoy voy a mostrarte cómo hacer una silla de ruedas para perros para tu perro. Se me ocurrió esta idea al buscar en Internet para ver formas en las que la gente puede disfrutar más de los perros mayores. Realmente no necesitaba uno porque mi perro tiene 2 años, pero mi perro tía tiene 8 años
D4E1 - Bricolaje - Tecnología de asistencia: Bandeja ajustable para silla de ruedas: 7 pasos (con imágenes)
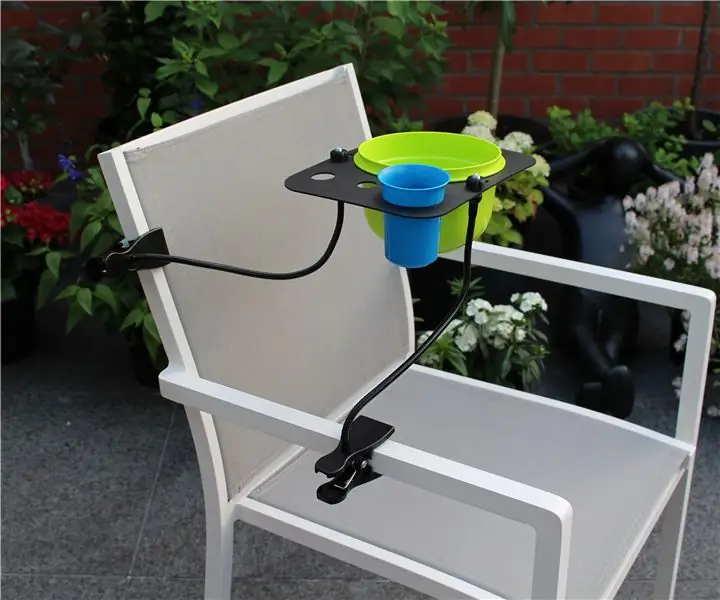
D4E1 - Bricolaje - Tecnología de asistencia: Bandeja ajustable para silla de ruedas: Kjell tiene una discapacidad congénita: cuadriparesia discinética y no puede comer solo. Necesita la ayuda de un monitor, un terapeuta ocupacional, que lo alimente. Esto viene con dos problemas: 1) El terapeuta ocupacional está detrás del volante
Ayuda de crochet para silla de ruedas: 18 pasos
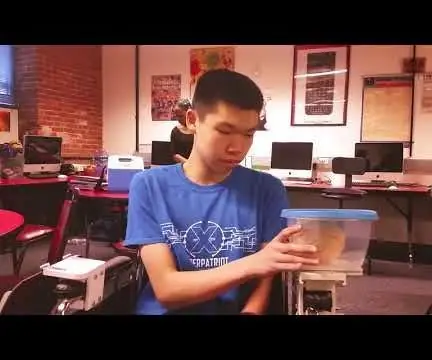
Ayuda de crochet para silla de ruedas: una persona con una lesión cerebral adquirida que no puede usar una de sus manos tiene dificultades para sostener su hilo para tejer y tejer a ganchillo. También tiene dificultad para distribuir el hilo sin que se enrede en su silla de ruedas. Tejer es una
Reposacabezas para silla de ruedas: 17 pasos
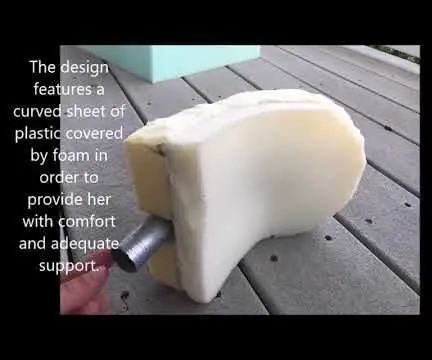
Reposacabezas para silla de ruedas: Introducción Una persona de Seven Hills tiene problemas con el reposacabezas para silla de ruedas. En momentos de mucha ansiedad y estrés, tiene convulsiones espásticas. Durante estos episodios, su cabeza puede verse forzada por el costado y la parte inferior del reposacabezas. Esta posi