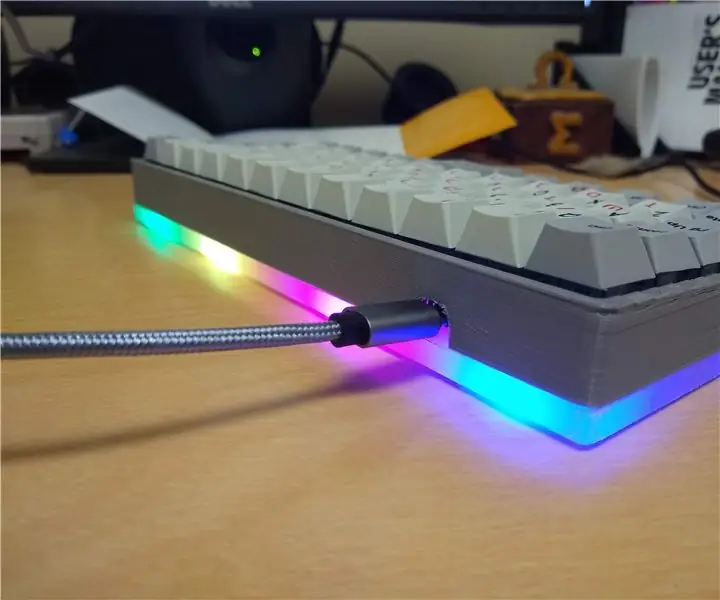
Tabla de contenido:
- Paso 1: 507 movimientos mecánicos
- Paso 2: Diseño y modelo 3D
- Paso 3: ACTUALIZAR 1/12/2020
- Paso 4: hardware
- Paso 5: Electrónica y programación
- Paso 6: ensamble la base
- Paso 7: agregue interruptores momentáneos
- Paso 8: agregue la placa de montaje y los interruptores de límite
- Paso 9: agregue motores paso a paso y engranajes
- Paso 10: agregar bastidores
- Paso 11: agregue barras de horas y minutos
- Paso 12: agregar lupas
- Paso 13: lecciones aprendidas
2025 Autor: John Day | [email protected]. Última modificación: 2025-01-23 14:39
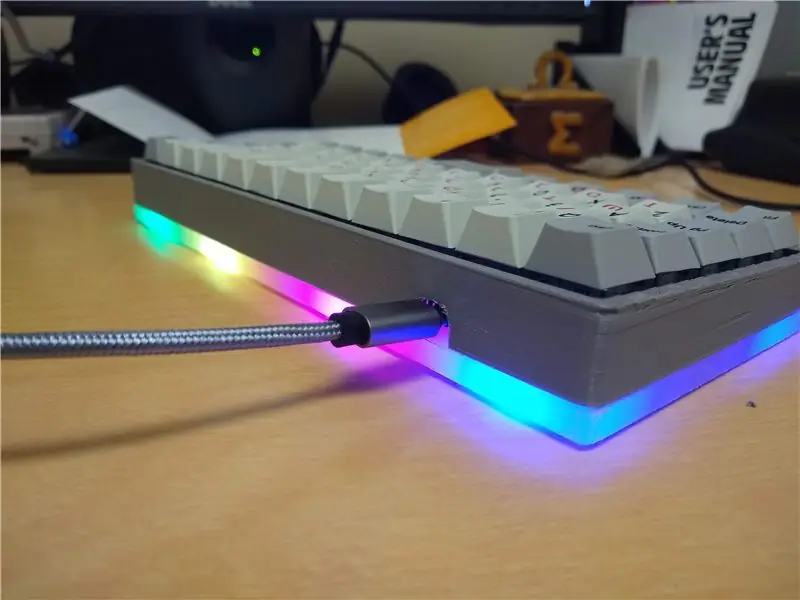
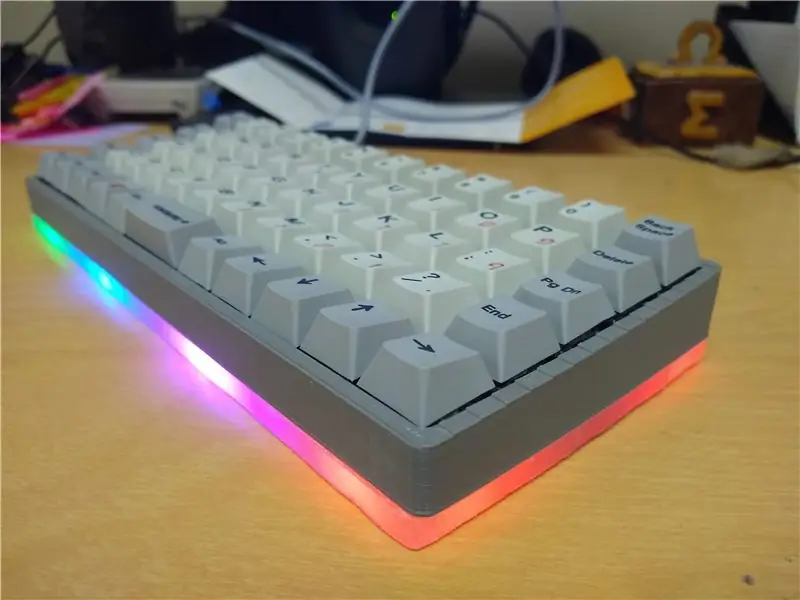
Proyectos Fusion 360 »
No importa lo que te diga Deepak Chopra, el tiempo es lineal. Ojalá este reloj esté un poco más cerca de la realidad que los circulares a los que todos estamos acostumbrados. Los intervalos de cinco minutos se sienten menos neuróticos que ser precisos hasta el minuto, y cada número se amplía, recordándole que debe concentrarse en el presente.
Hice esto usando casi todas las máquinas en Pier 9 (chorro de agua, chorro de arena, cortadora láser, impresora 3D, laboratorio de electrónica, etc.). Está hecho de aluminio 6061, herrajes de acero (tornillos, tuercas, rodamientos), engranajes impresos en 3D, un Arduino Uno, y los paneles de horas y minutos son de madera contrachapada cortada / grabada con láser.
Por supuesto, sé que este proyecto no es accesible para casi todos los que no tienen la increíble suerte de tener acceso a una tienda como esta, pero espero que lo encuentre inspirador.
Fusion 360 es gratuito para estudiantes y aficionados, y ofrece un montón de apoyo educativo. Si quieres aprender a modelar en 3D el tipo de trabajo que hago, creo que esta es la mejor opción del mercado. Haga clic en los enlaces a continuación para registrarse:
Estudiante / Educador
Aficionado / Startup
También dirigí una serie de clases de seminarios web relacionados con proyectos de modelado 3D con partes móviles. En estos seminarios web, aprenderá las funciones de Fusion 360 como ensamblajes mecánicos avanzados (es decir, dos o más articulaciones interactuando) y renderizado. El último seminario web se centró en modelar este diseño de reloj en Fusion 360. Puede ver el video completo aquí:
Si está interesado, consulte los otros dos seminarios web de esta serie en los que aprenderá a diseñar una lámpara de perilla gigante y un reloj perpetuo con Arduino.
Paso 1: 507 movimientos mecánicos
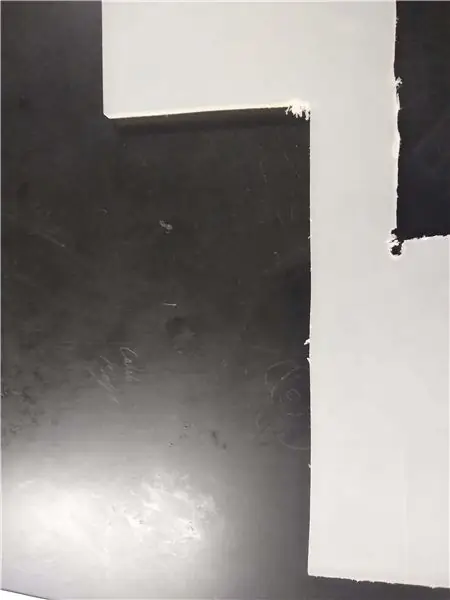
507 Mechanical Movements es una enciclopedia de mecanismos comunes de la década de 1860 que sirve como una buena referencia para este tipo de cosas. Este mecanismo se basa en el Movimiento 113, "Cremallera y piñón". Este será un proyecto largo, así que si tienes un mecanismo específico que te gustaría que hiciera, ¡no dudes en hacer una solicitud en los comentarios!
Paso 2: Diseño y modelo 3D
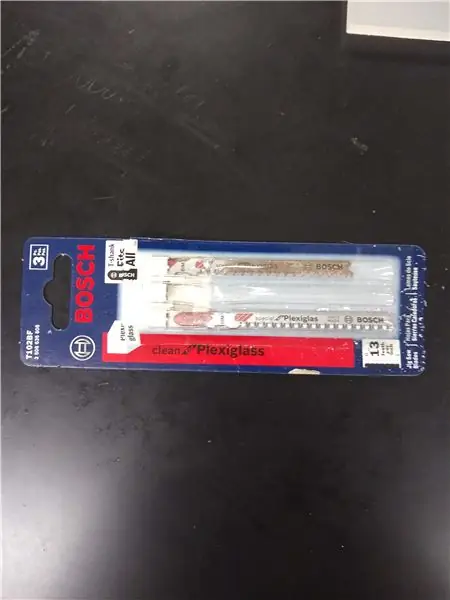
El video de arriba es una grabación de un seminario web que hice para la parte de diseño de piñón y cremallera del proyecto.
La parte más difícil de descifrar del diseño fue el conjunto de engranajes de piñón y cremallera. Las matemáticas para el diseño de engranajes pueden volverse bastante complicadas (de hecho, hay ingenieros que básicamente solo diseñan ensamblajes de engranajes por esta misma razón), pero basándome en un excelente tutorial de Youtube de Rob Duarte, hice mi propia plantilla que funciona con la última versión. del complemento Spur Gear para Fusion.
El video de arriba lo guía a través del proceso de hacer el ensamblaje de piñón y cremallera, pero si desea un tutorial más completo, únase a mí en el seminario web Design Now Hour Of Making in Motion el 5 de abril. Se grabará y publicaré el video aquí.

La plantilla (enlace a continuación) tiene todos los parámetros que se muestran arriba ya ingresados. No entraré en matemáticas aquí, pero si sigues las instrucciones, debería funcionar para ti.
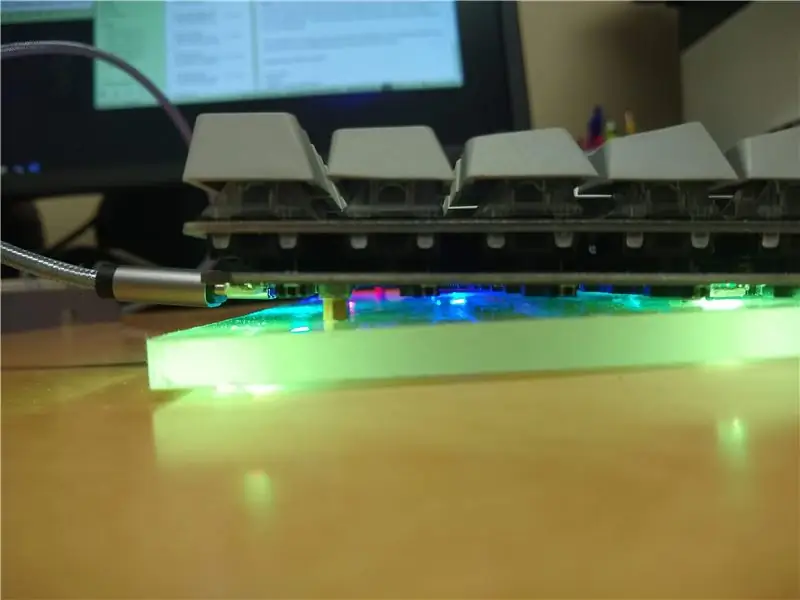
Utilice el complemento Spur Gear yendo a ADD-INS> Scripts y complementos…> Spur Gear> Ejecutar. Cuando obtenga la ventana que se muestra arriba, ingrese los parámetros. Number of Teeth no le permitirá usar un parámetro para el valor, así que asegúrese de que coincida con el valor de teethNum si lo cambia. También debe multiplicar los parámetros nombrados por 1 como se muestra arriba.
Tenga en cuenta que una vez que el equipo está hecho, puede editarlo como cualquier otro objeto en Fusion.
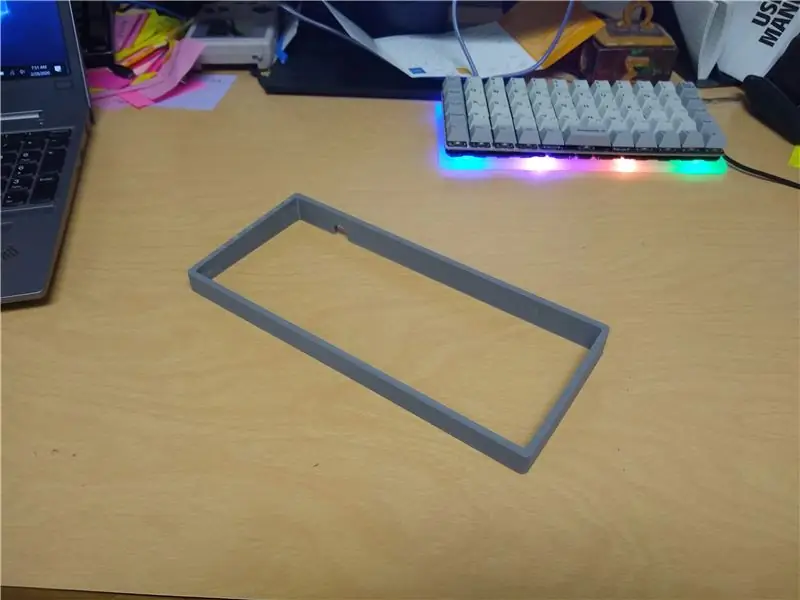
Como se muestra en la demostración en video, este es un ejemplo de cómo construiría un perfil de diente usando los parámetros.
Aquí están los enlaces a la plantilla que puede usar para hacer su propio piñón y cremallera en Fusion:
Plantilla con parámetros:
Después de que se resolvió el engranaje de piñón y cremallera, pasé mucho tiempo modelando motores, interruptores y otras partes electrónicas, y luego descubrí todos los detalles. Con el enlace de movimiento descrito anteriormente, pude obtener una buena imagen de cómo se vería en movimiento.
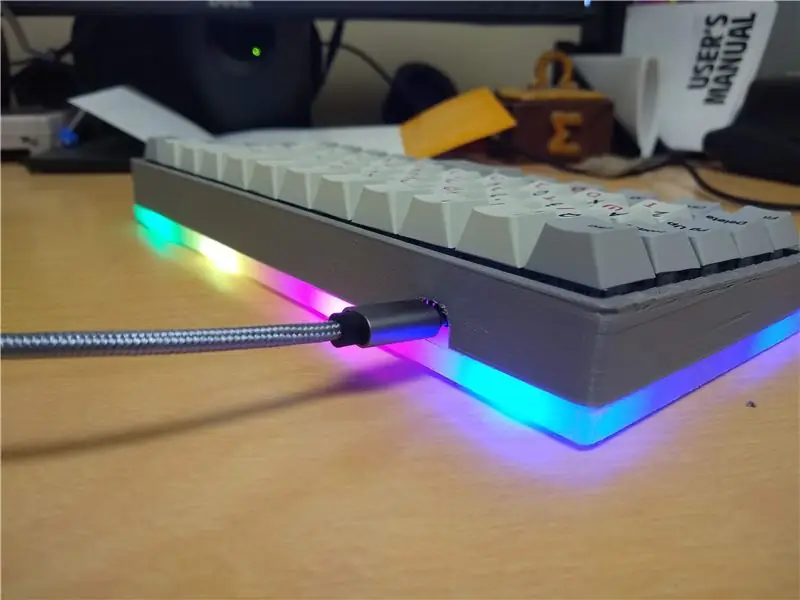
Puede acceder al archivo a través del enlace a continuación y jugar con él o incluso intentar hacer su propia versión del archivo. Hubo bastantes retoques y alteraciones después de que se hicieron las piezas, así que no espere poder cortar con láser todas las piezas y tener un producto terminado. ¡Este proyecto fue caro y tomó mucho tiempo! Si realmente quieres hacerlo y necesitas ayuda, solo comenta a continuación y haré todo lo posible para que empieces.
Diseño de reloj terminado:
Si aún no es usuario de Fusion 360, regístrese en mi clase gratuita de impresión 3D. Es un curso intensivo de Fusion para hacer, y la lección 2 tiene toda la información que necesita para obtener Fusion gratis.
Paso 3: ACTUALIZAR 1/12/2020
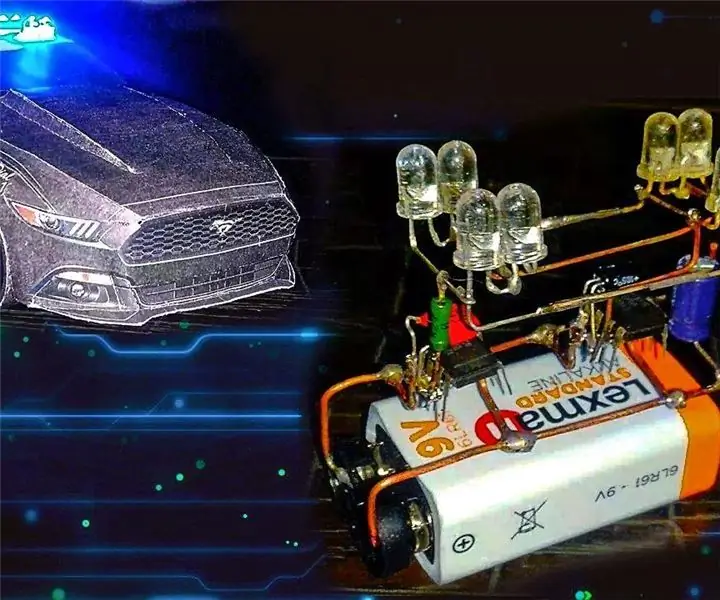
Después de hacer el primer prototipo, comencé de nuevo con algunas mejoras en el diseño. Uno de mis colegas del equipo de Electrónica diseñó un circuito personalizado para impulsar los motores, y hay sensores magnéticos que ayudan a detectar la posición (indexados a partir de imanes que se ajustan a presión en los rieles).
Todos los componentes del modelo tienen números de pieza, la mayoría son de McMaster Carr o DigiKey. Este es un diseño mucho mejor porque evita el problema de las estanterías debido al peso del riel cuando está completamente extendido, y porque la indexación del sensor magnético asegura la posición correcta cada vez que los motores se mueven.
Ensamblaje completo de Fusion 360:
Paso 4: hardware
- Paneles: aluminio 6061 de 6 mm de espesor (presumiblemente, el contrachapado también funcionaría)
- Panel de números: madera contrachapada de 3 mm
- Arduino Uno:
- Escudo de motor Adafruit:
- Motores paso a paso de 5 V: https://www.adafruit.com/products/858 (recomendaría usar motores de 12 V en lugar de estos)
- Finales de carrera (4):
- Interruptores momentáneos (2):
Paso 5: Electrónica y programación
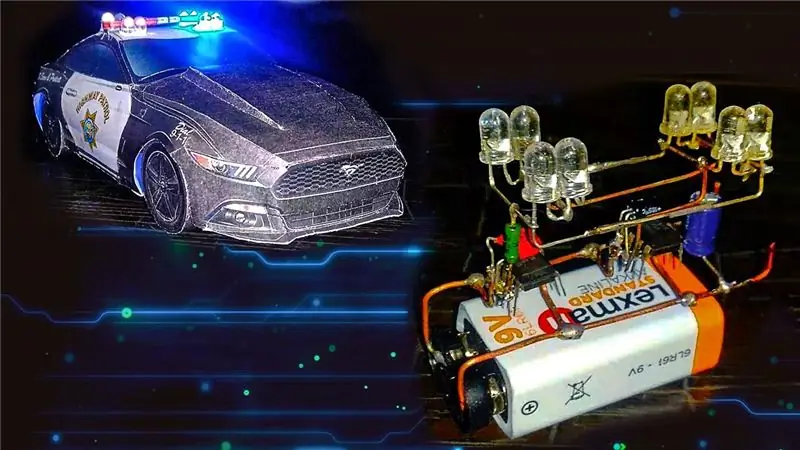

La electrónica está hecha con un Arduino Uno y un Adafruit Motor Shield.
Aquí está la idea básica de cómo quiero que funcione:
- Cuando se enciende la unidad, los motores paso a paso hacen retroceder los bastidores hasta que se activan los interruptores de límite del lado izquierdo. Esto establece la posición en cero. Luego, los creadores de pasos mueven los bastidores hacia adelante hasta que 1 esté centrado en el panel de horas y 00 esté centrado en el panel de minutos.
- Una vez centrados la hora y los minutos, las rejillas avanzan en el tiempo. Una posición completa se mueve en la parte inferior a máxima velocidad cada 5 minutos y una posición completa se mueve en la parte superior cada hora.
- Los interruptores momentáneos (pines 6-7) para mover los bastidores hacia adelante una posición (aproximadamente 147 pasos), luego continúan con el conteo del reloj.
- Los movimientos de horas y minutos tienen contadores que envían las barras de regreso a los interruptores de límite de la izquierda y los restablecen a cero una vez que la hora ha pasado de las 12 y los minutos han pasado de 55.
Todavía no tengo claro qué debo hacer exactamente con el código. Lo tengo funcionando en teoría con el siguiente código que obtuve de Randofo. Este código mueve la barra de minutos hacia adelante un paso cada 200 ms (creo) una vez que se activa uno de los interruptores de límite. Funciona, pero estoy bastante lejos de mi profundidad más allá del trabajo básico que he hecho aquí. Esto parece un problema bastante fácil para un usuario experimentado de Arduino, pero solo hago un proyecto con uno tal vez una vez al año, y cada vez que lo hago, básicamente me olvido de todo lo que aprendí en el último proyecto.
/*************************************************************
Demostración de Motor Shield Stepper por Randy Sarafan
Para más información, ver:
www.instructables.com/id/Arduino-Motor-Shi…
*************************************************************/
#include #include #include "utilidad / Adafruit_MS_PWMServoDriver.h"
// Cree el objeto de la pantalla del motor con la dirección I2C predeterminada
Adafruit_MotorShield AFMS = Adafruit_MotorShield (); // O créelo con una dirección I2C diferente (digamos para apilar) // Adafruit_MotorShield AFMS = Adafruit_MotorShield (0x61);
// Conecte un motor paso a paso con 200 pasos por revolución (1.8 grados)
// al puerto del motor # 2 (M3 y M4) Adafruit_StepperMotor * myMotor1 = AFMS.getStepper (300, 1); Adafruit_StepperMotor * myMotor2 = AFMS.getStepper (300, 2);
int delaylegnth = 7;
configuración vacía () {
// iniciar la conexión en serie Serial.begin (9600); // configurar pin2 como entrada y habilitar la resistencia pull-up interna pinMode (2, INPUT_PULLUP);
// Serial.begin (9600); // configurar la biblioteca serial a 9600 bps
Serial.println ("¡Prueba paso a paso!");
AFMS.begin (); // crear con la frecuencia predeterminada 1.6KHz
//AFMS.begin(1000); // O con una frecuencia diferente, digamos 1KHz myMotor1-> setSpeed (100); // 10 rpm}
bucle vacío () {
// lee el valor del botón en una variable int sensorVal = digitalRead (2); sensorVal == BAJO; int delayL = 200; if (sensorVal == LOW) {Serial.println ("Minutos ++"); // myMotor1-> paso (1640, HACIA ATRÁS, DOBLE); for (int i = 0; i step (147, BACKWARD, DOUBLE); // analogWrite (PWMpin, i); delay (delayL);} Serial.println ("Hours ++"); myMotor1-> step (1615, ADELANTE, DOBLE);
// myMotor2-> paso (1600, HACIA ATRÁS, DOBLE);
myMotor2-> paso (220, ADELANTE, DOBLE); // retraso (retrasoL); } demás {
//Serial.println("Double coil steps ");
myMotor1-> paso (0, ADELANTE, DOBLE); myMotor1-> paso (0, HACIA ATRÁS, DOBLE); }}
Paso 6: ensamble la base
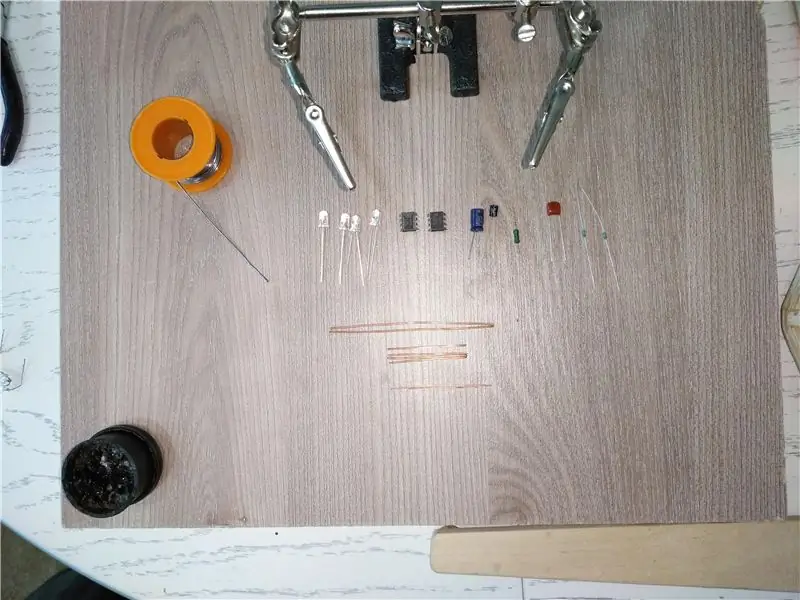
La base está hecha de dos placas con espaciadores que las mantienen juntas. Los tornillos se sujetan a la placa a través de orificios roscados. La pieza número 6 de este dibujo es otra pieza impresa en 3D: un espaciador que también sirve como base para el terminal de alimentación de los motores paso a paso.
Paso 7: agregue interruptores momentáneos
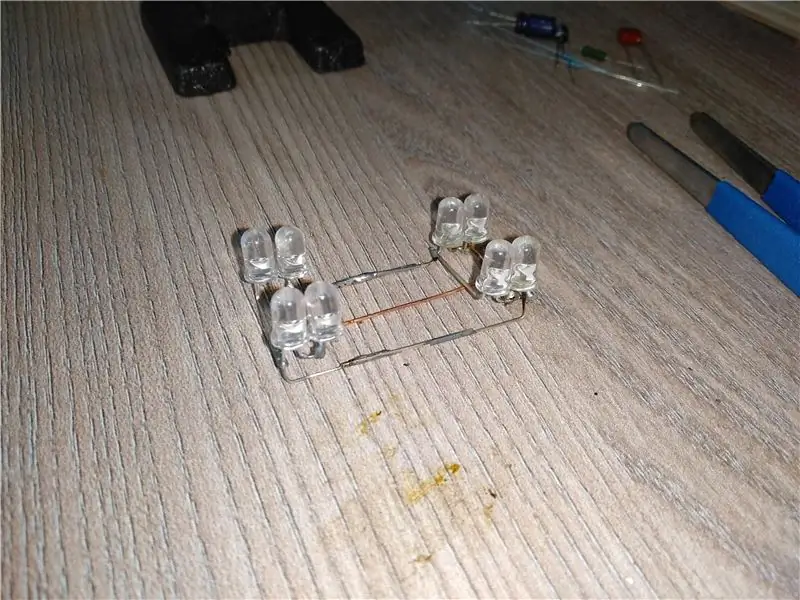
Los interruptores momentáneos, Arduino y los interruptores de límite se sujetan a la placa frontal, por lo que acceder a los componentes electrónicos para realizar cambios es fácil: simplemente retire la placa posterior y podrá alcanzar todo.
Paso 8: agregue la placa de montaje y los interruptores de límite
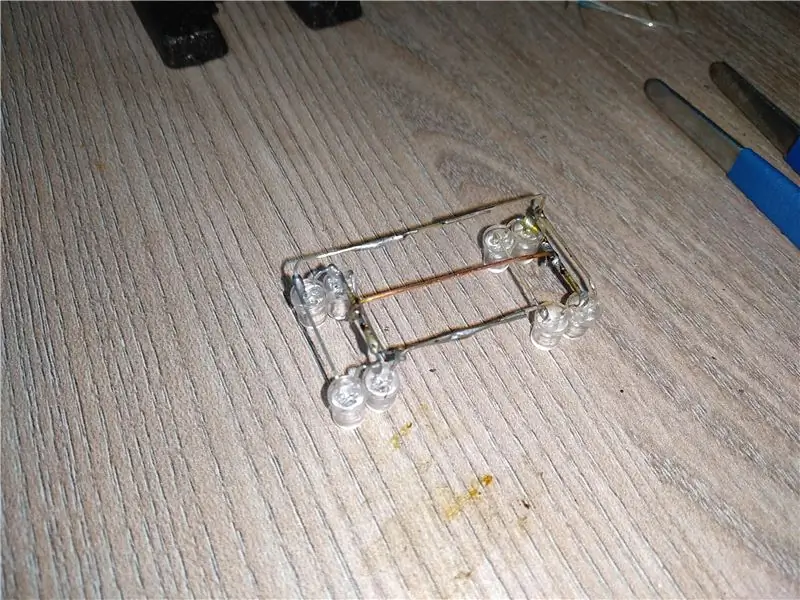
La placa de montaje contiene los interruptores de límite y el conjunto de cojinetes para los bastidores. Esta parte también puede permanecer junta al editar la electrónica.
Paso 9: agregue motores paso a paso y engranajes
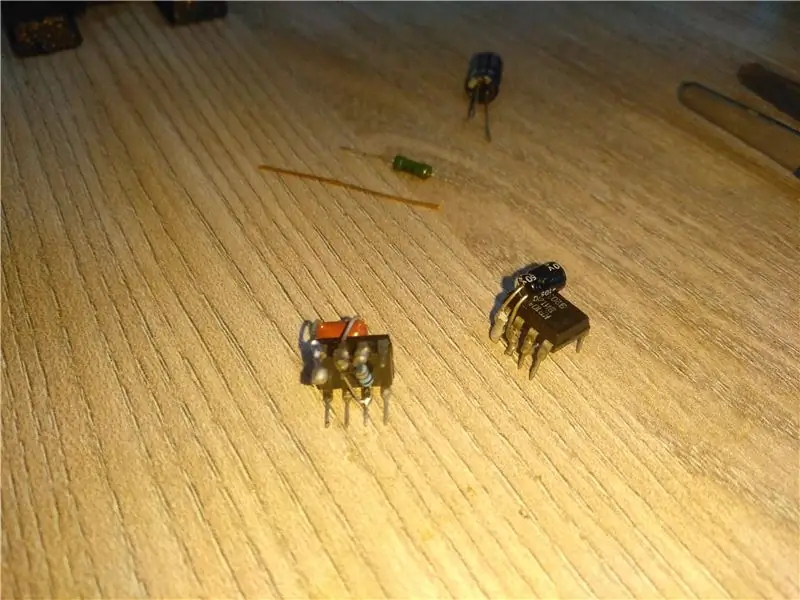
Los motores paso a paso se sujetan al panel con tornillos M4 a través de orificios roscados, y los engranajes impresos en 3D se ajustan a presión en los postes del motor. Usé una abrazadera de gatillo para ajustarlos y enjuagarlos.
Paso 10: agregar bastidores
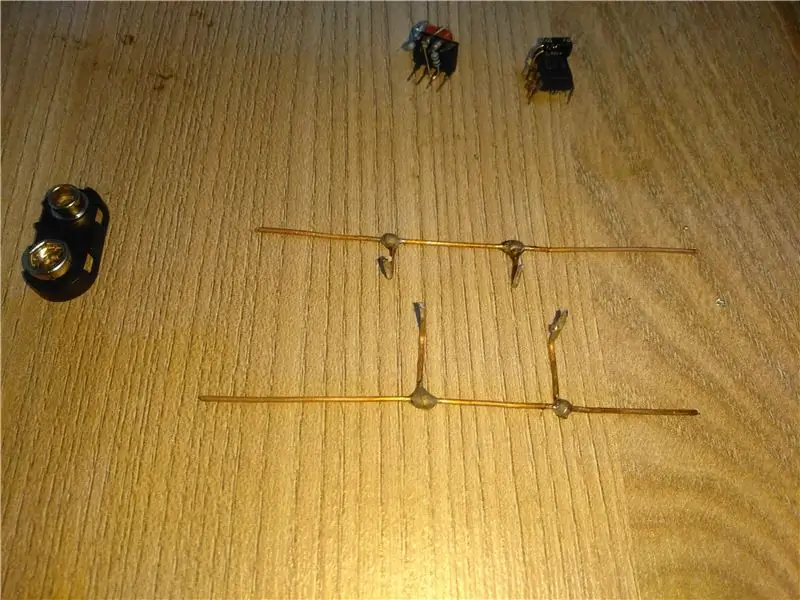
Las rejillas tienen ranuras cortadas que se apoyan en los dos cojinetes de bolas. Hay un pequeño espacio (0,1 mm) entre los cojinetes y las ranuras, lo que permite que el bastidor se mueva libremente.
Los cojinetes están intercalados entre espaciadores personalizados impresos en 3D para obtener el ajuste exacto que necesitaba. Hay una placa de rejilla en la parte delantera que actúa como una arandela que mantiene las rejillas en su lugar.
Paso 11: agregue barras de horas y minutos
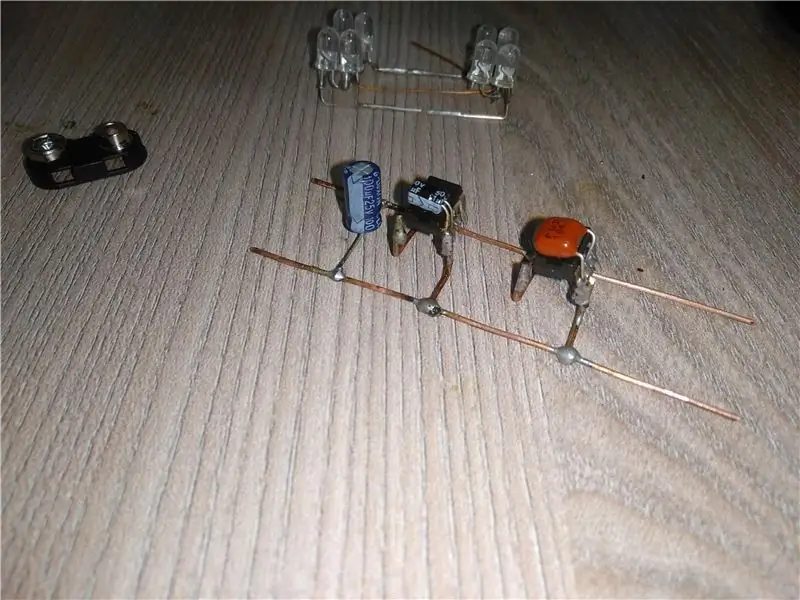
Las barras de horas y minutos se sujetan a los racks con espaciadores de 12 mm creando un espacio que deja espacio entre las barras y los racks.
Paso 12: agregar lupas
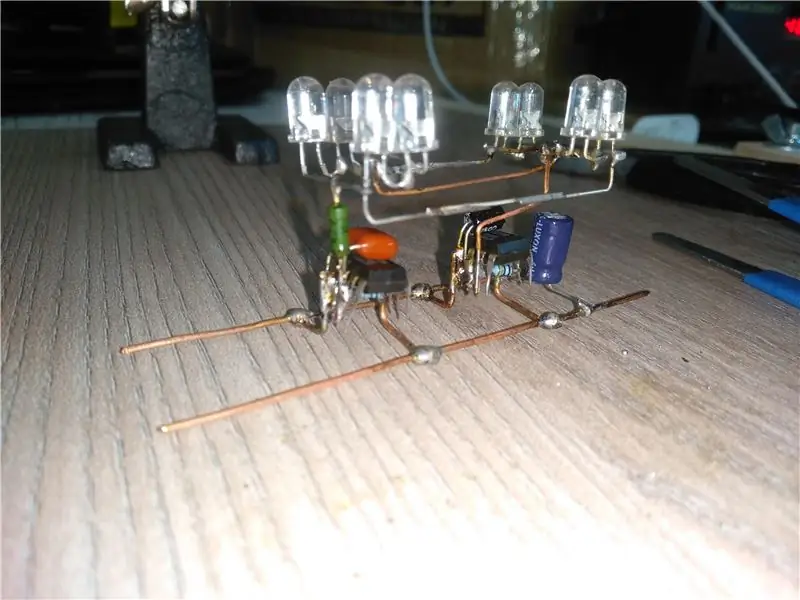
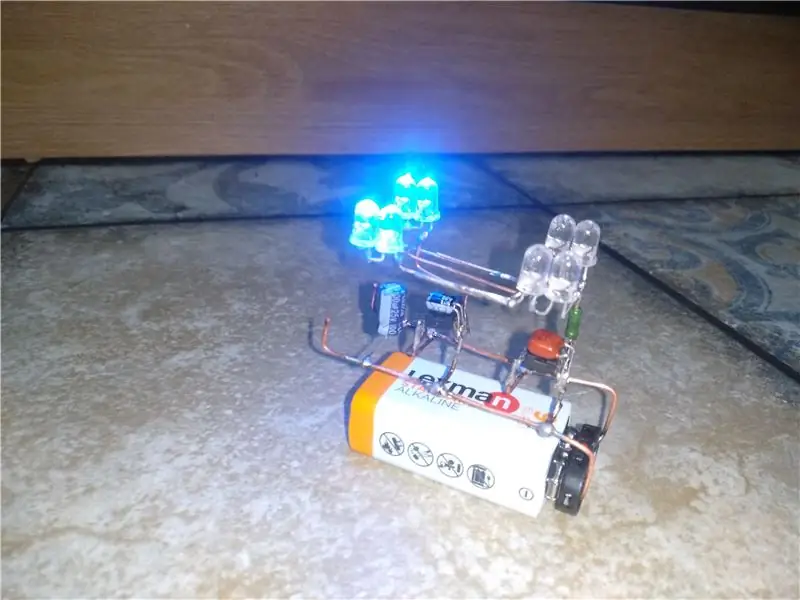
Las lupas son lupas de bolsillo baratas que encontré en Amazon. Están desplazados desde la parte delantera de las barras con espaciadores de 25 mm.
Paso 13: lecciones aprendidas
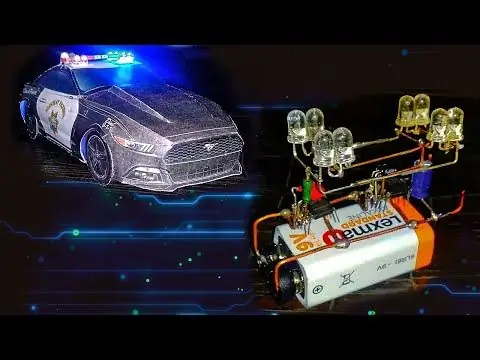
Aprendí mucho sobre el movimiento lineal con este proyecto. La tolerancia que usé entre los cojinetes y las ranuras en los bastidores fue demasiado, así que si tuviera que hacerlo de nuevo, creo que probablemente lo cortaría por la mitad. La brecha en los lados de las brechas también era demasiado grande.
Los motores funcionan, pero cuanto más se alarga el voladizo, más tienen que trabajar. Probablemente iría con steppers de 12V en lugar de 5V.
La reacción también debería haber sido mayor, tal vez 0,25 mm. Los engranajes estaban presionando los bastidores con demasiada fuerza con los primeros engranajes que probé.
Recomendado:
Reloj despertador inteligente: un reloj despertador inteligente hecho con Raspberry Pi: 10 pasos (con imágenes)
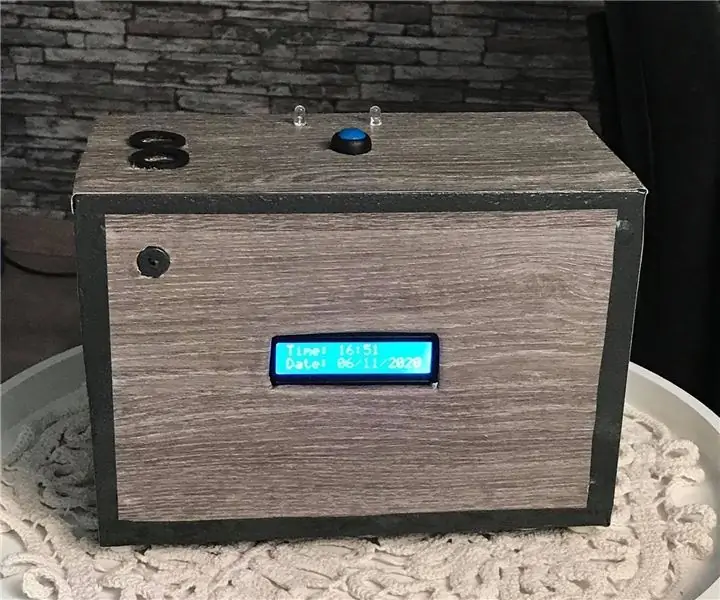
Reloj despertador inteligente: un reloj despertador inteligente hecho con Raspberry Pi: ¿Alguna vez has querido un reloj inteligente? Si es así, ¡esta es la solución para usted! Hice Smart Alarm Clock, este es un reloj que puede cambiar la hora de la alarma de acuerdo con el sitio web. Cuando suene la alarma, habrá un sonido (zumbador) y 2 luces
Reloj Vortex: un reloj de pulsera con espejo infinito: 10 pasos (con imágenes)
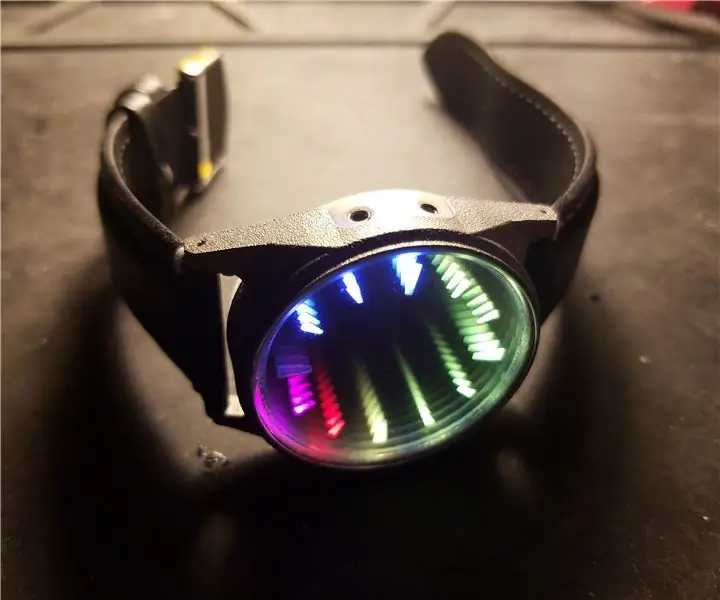
Vortex Watch: un reloj de pulsera con espejo infinito: el objetivo de este proyecto era crear una versión portátil de un reloj con espejo infinito. Utiliza sus LED RGB para indicar el tiempo asignando horas, minutos y segundos a las luces roja, verde y azul respectivamente y superponiendo estos tonos t
Reloj de red ESP8266 sin ningún RTC - Reloj Nodemcu NTP Sin RTC - PROYECTO RELOJ DE INTERNET: 4 Pasos
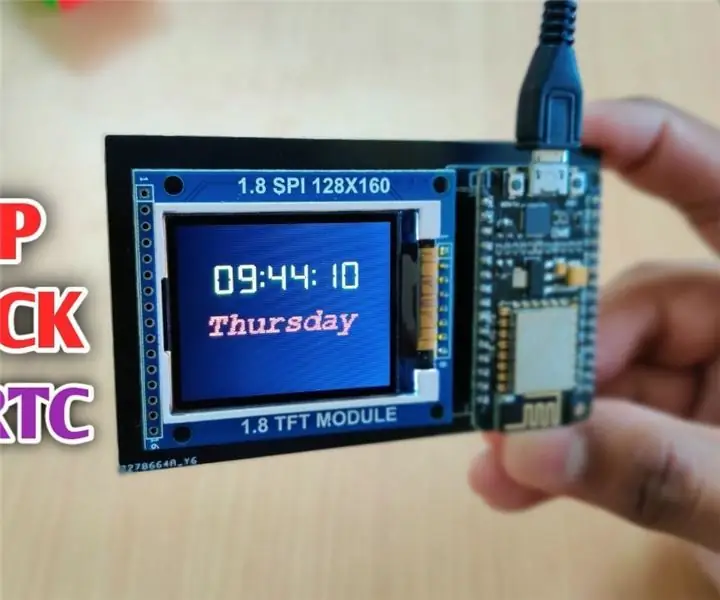
Reloj de red ESP8266 sin ningún RTC | Reloj Nodemcu NTP Sin RTC | PROYECTO DE RELOJ DE INTERNET: En el proyecto se realizará un proyecto de reloj sin RTC, se tomará tiempo de Internet usando wifi y lo mostrará en la pantalla st7735
Fader LED analógico alterno discreto con curva de brillo lineal: 6 pasos (con imágenes)
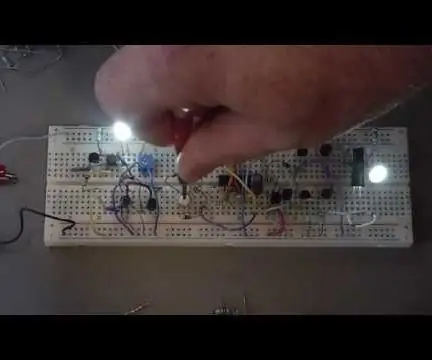
Fader LED analógico alterno discreto con curva de brillo lineal: la mayoría de los circuitos para atenuar / atenuar un LED son circuitos digitales que utilizan una salida PWM de un microcontrolador. El brillo del LED se controla cambiando el ciclo de trabajo de la señal PWM. Pronto descubrirá que al cambiar linealmente el ciclo de trabajo
Reloj lineal con Arduino + DS1307 + Neopixel: reutilización de hardware: 5 pasos
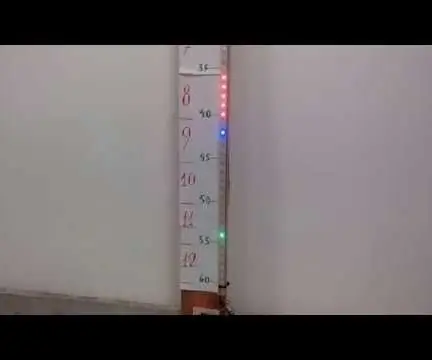
Reloj lineal con Arduino + DS1307 + Neopixel: reutilización de hardware .: De proyectos anteriores me quedaba un Arduino UNO y una tira de LED Neopixel, y quería hacer algo diferente. Debido a que la tira de Neopixel tiene 60 luces LED, pensada para usarla como un gran reloj, para indicar las Horas se usa un segmento rojo de 5 LED (60 LED