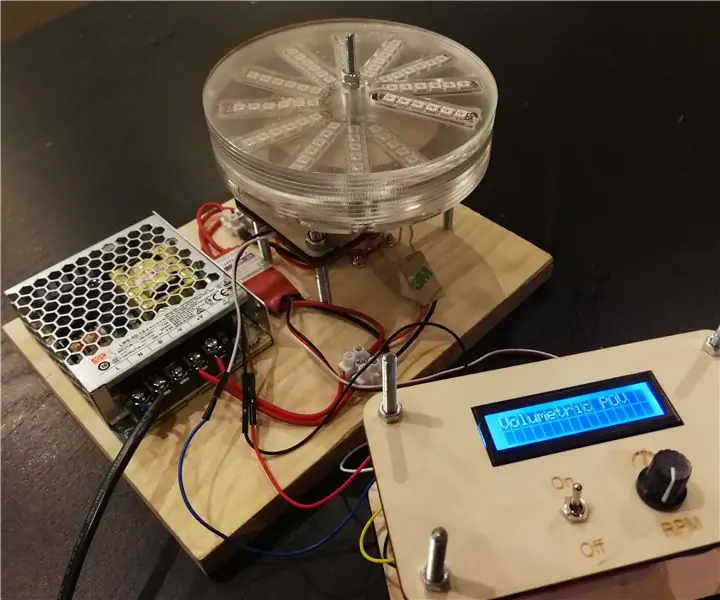
Tabla de contenido:
- Paso 1: Material y herramientas utilizados
- Paso 2: Unidad de controlador de motor para regular la velocidad de rotación
- Paso 3: Creación de la plataforma para la transmisión inalámbrica de energía
- Paso 4: Carcasa giratoria
- Paso 5: Cilindro giratorio con las tiras de LED
- Paso 6: lecciones aprendidas
- Paso 7: posibles mejoras
- Paso 8: Grita
2025 Autor: John Day | [email protected]. Última modificación: 2025-01-23 14:39
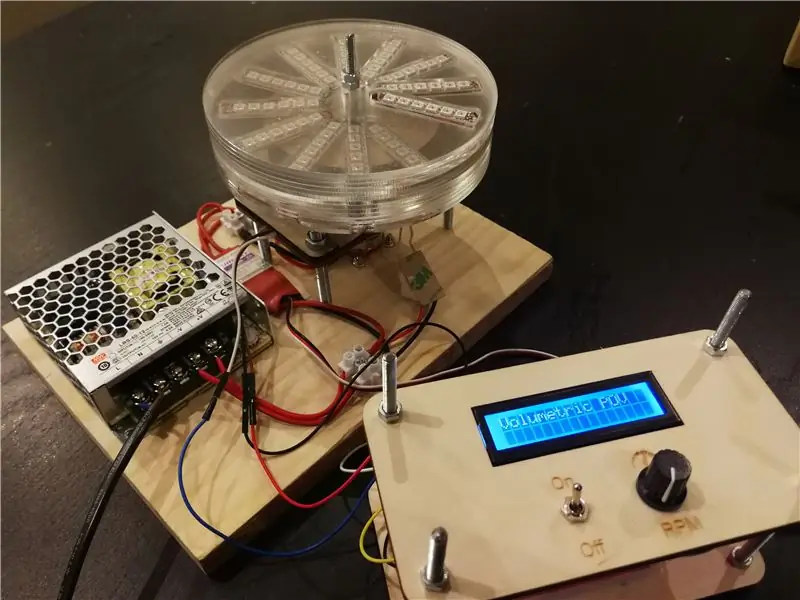
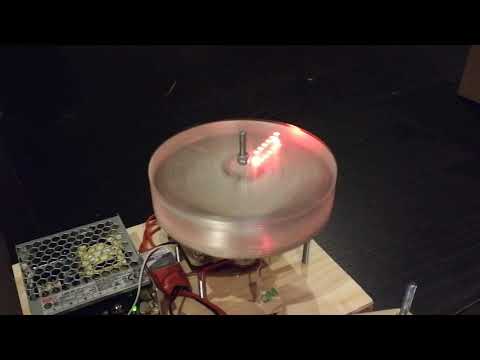

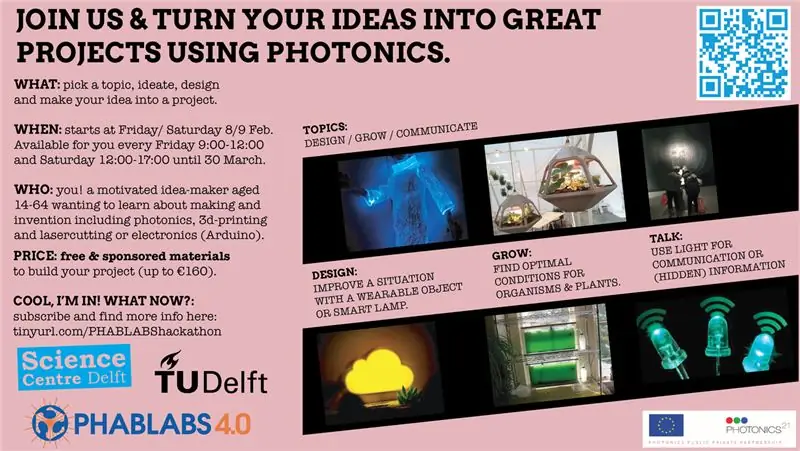
Hace unas semanas recibí una invitación de último minuto para participar en un PhabLabs Hackathon en el Science Center Delft en los Países Bajos. Para un aficionado entusiasta como yo, que normalmente puede dedicar solo una cantidad limitada de tiempo a retoques, vi esto como una gran oportunidad para programar un tiempo dedicado para convertir una de mis muchas ideas, dentro del alcance del Hackathon: Photonics, en un proyecto real. Y con las excelentes instalaciones del Makerspace en el Science Center Delft, era imposible rechazar esta invitación.
Una de las ideas que ya tuve durante un tiempo relacionada con la fotónica fue que quería hacer algo con Persistence of Vision (POV). Ya hay toneladas de ejemplos disponibles en línea de cómo construir una pantalla de punto de vista básica usando algunos componentes básicos: microcontrolador, ventilador / disco duro / motor antiguo y una cadena de leds conectados perpendicularmente al eje del dispositivo giratorio. Con una configuración relativamente simple, ya puede crear una imagen bidimensional impresionante, por ejemplo:
Otra variación de las pantallas POV conecta una cadena de leds paralelos al eje del dispositivo giratorio. Esto dará como resultado una pantalla POV cilíndrica tridimensional, por ejemplo:
En lugar de conectar la cadena de leds en paralelo al eje del dispositivo giratorio, también puede arquear la cadena de leds. Esto dará como resultado una pantalla POV esférica (globo), por ejemplo: https://www.instructables.com/id/POV-Globe-24bit-… El siguiente nivel es construir varias capas de cadenas de LED para crear una pantalla 3D volumétrica. Aquí hay algunos ejemplos de tales pantallas POV 3D volumétricas que utilicé como inspiración para este proyecto específico:
- https://www.instructables.com/id/PropHelix-3D-POV-…
- https://github.com/mbjd/3DPOV
- https://hackaday.io/project/159306-volumetric-pov-…
- https://hackaday.com/2014/04/21/volumen-the-most-a…
Como los creadores de los ejemplos anteriores proporcionaron información muy útil, tenía mucho sentido mezclar partes de sus proyectos. Pero como se supone que un Hackathon es un desafío, también decidí construir un tipo diferente de pantalla POV 3D volumétrica. Algunos de ellos usaban rotores y mucho pegamento caliente para evitar que los componentes volaran. Otros crearon PCB personalizados para su proyecto. Después de revisar algunos de los otros proyectos de 3D POV, vi espacio para algo de "innovación" o presentar algunos desafíos para mí:
- Sin experiencia previa en la creación de PCB personalizados y debido a la limitación de tiempo del Hackathon, elijo seguir un enfoque de prototipo más básico. Pero en lugar de crear rotores reales, tenía curiosidad sobre cómo se vería una pantalla POV 3D volumétrica cuando se usaba un cilindro construido con capas de plástico acrílico.
- Sin uso o uso mínimo de pegamento caliente para hacer que el dispositivo sea menos peligroso
Paso 1: Material y herramientas utilizados
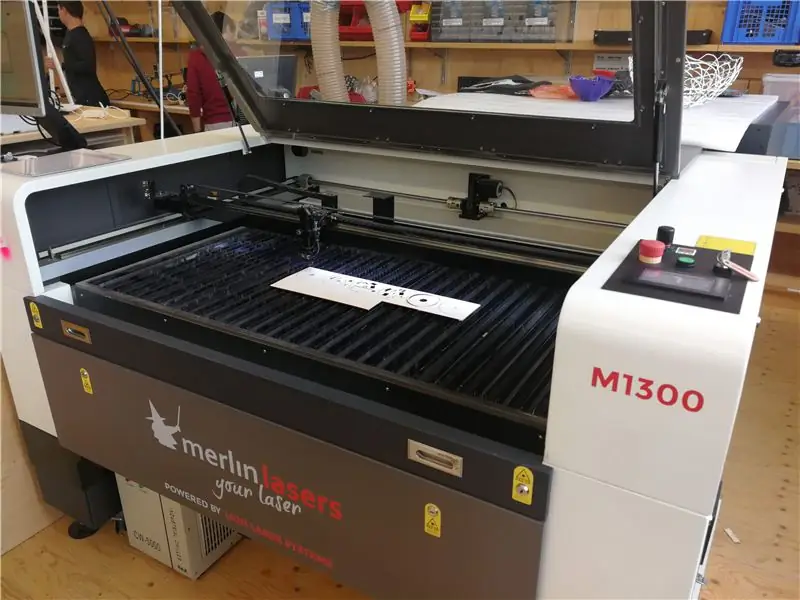
Para el controlador de motor
- Arduino Pro Micro 5V / 16Mhz
- Placa de pruebas pequeña
- 3144 Sensor de interruptor de efecto Hall
- Imán con diámetro: 1 cm, altura: 3 mm
- Interruptor de palanca - MTS-102
- Potenciómetro 10K
- Cables de puente Dupont
- 16 x tuercas M5
- Módulo de pantalla LCD con retroiluminación azul (HD44780 16 × 2 caracteres)
- Resistencia de 10K - Resistencia de extracción para el sensor de efecto Hall
- Resistencia de 220 ohmios: para controlar el contraste de la pantalla LCD
- Diámetro de la varilla roscada: 5 mm
- Madera contrachapada, Espesor: 3 mm
Para la base de la plataforma
- Trozo de madera de desecho (250 x 180 x 18 mm)
- Mean Well - 12V 4.2A - Fuente de alimentación conmutada LRS-50-12
- Cable de alimentación 220V
- Convertidor inalámbrico DC-DC - 5V 2A (transmisor)
- Turnigy D2836 / 8 1100KV Motor sin escobillas Outrunner
- Controlador de velocidad Turnigy Plush 30amp W / BEC
- Conectores de bloques de terminales
- 12 x Tuercas M6 para fijar la plataforma mediante varillas roscadas de 6 mm de diámetro.
- 3 x pernos M2 (18 mm de longitud) para asegurar el adaptador atornillado al motor sin escobillas
- 4 tuercas y tornillos M3 para asegurar el motor sin escobillas al trozo de madera de desecho
- Diámetro de la varilla roscada: 6 mm (4 x longitud 70 mm)
- Diámetro de la varilla roscada: 4 mm (1 x longitud 80 mm)
- Madera contrachapada, Espesor: 3 mm
Para la carcasa giratoria
- Convertidor inalámbrico DC-DC - 5V 2A (receptor)
- Adaptador de perno impreso en 3D (filamento PLA, blanco)
- Teensy 3.6
- Convertidor / cambiador de nivel lógico cuádruple IC 74AHCT125 (3 V a 5 V)
- Resistencia de 10K - Resistencia de extracción para el sensor de efecto Hall
- Condensador 1000uF 16V
- Diámetro de varilla roscada 4 mm
- Imán con diámetro: 1 cm, altura: 3 mm
- Madera contrachapada, Espesor: 3 mm
- Madera contrachapada, Espesor: 2 mm
- Hoja de acrílico, espesor: 2 mm
- Diámetro de la varilla de acero: 2 mm
- Tuercas y tornillos
- Tira de leds de 0,5 metros APA102C 144 leds / metro
Herramientas utilizadas
- Merlin Laser Cutter M1300: corte láser de madera contrachapada y lámina acrílica
- Ultimaker 2+ para impresión 3D con el adaptador empernado
- Estación de soldadura y soldadura
- Taladro de mesa
- Destornilladores
- Plyers
- Martillo
- Calibrar
- Sierra
- Llaves
- Tubo termoretráctil
Software utilizado
- Fusion 360
- Ultimaker Cura
- Arduino IDE y Teensyduino (que contiene Teensy Loader)
Paso 2: Unidad de controlador de motor para regular la velocidad de rotación
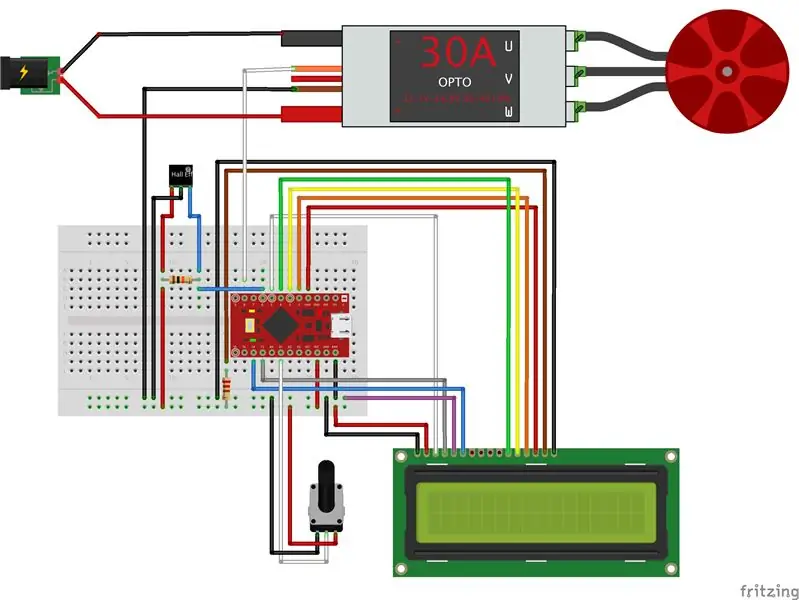
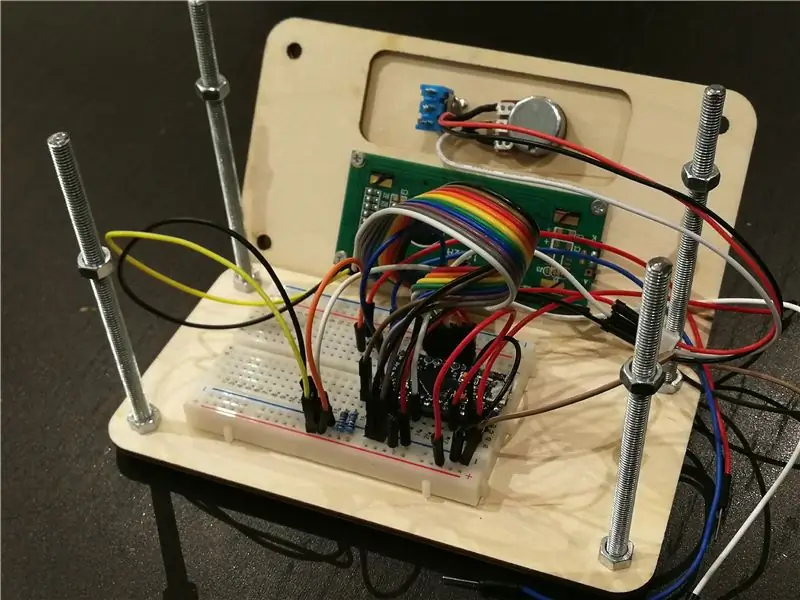
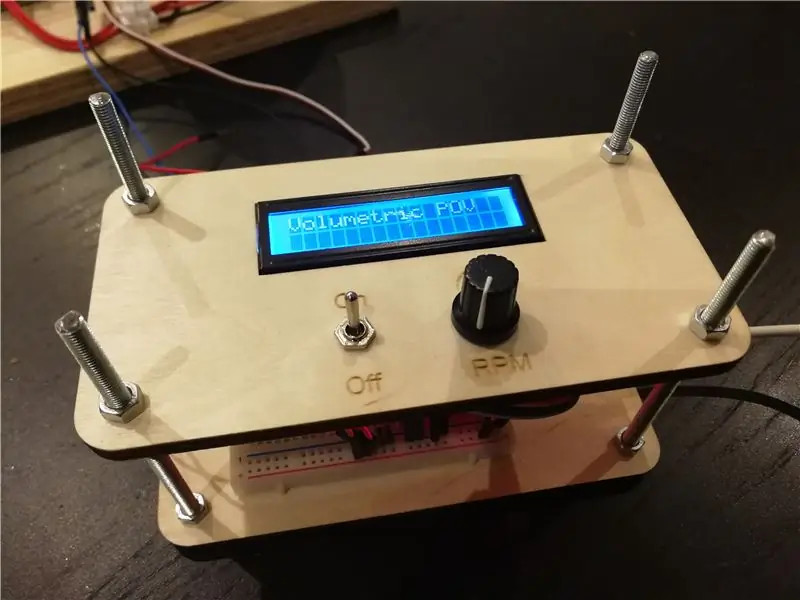
La unidad de controlador de motor envía una señal al controlador de velocidad electrónico Turnigy (ESC) que controlará el número de rotaciones proporcionadas por el motor sin escobillas.
Además, también quería poder mostrar las rotaciones reales por minuto del cilindro POV. Por eso he decidido incluir un sensor de efecto Hall y una pantalla LCD de 16x2 en la unidad de controlador del motor.
En el archivo zip adjunto (MotorControl_Board.zip) encontrará tres archivos dxf que le permitirán cortar con láser una placa base y dos placas superiores para la unidad del controlador del motor. Utilice madera contrachapada con un grosor de 3 mm. Las dos placas superiores se pueden colocar una encima de la otra, lo que le permitirá atornillar la pantalla LCD de 16x2.
Los dos orificios en la placa superior están diseñados para un interruptor de encendido / apagado y un potenciómetro para controlar la velocidad del motor sin escobillas (todavía no he cableado el interruptor de encendido / apagado). Para construir la unidad de controlador de motor, debe cortar la varilla roscada con un diámetro de 5 mm en 4 piezas de la altura deseada. Con las 8 tuercas M5, primero puede sujetar la base. Luego adjunté la placa de pruebas pequeña a la placa base con la etiqueta adhesiva de dos caras que se proporcionó con la placa de pruebas. El esquema adjunto muestra cómo debe cablear los componentes para que puedan funcionar con el código fuente (MotorControl.ino) adjunto a este paso. He usado una resistencia pull up de 10K para el sensor de pasillo. Una resistencia de 220 ohmios funcionó lo suficientemente bien como para hacer visible el texto en la pantalla LCD.
Asegúrese de aislar las clavijas del sensor de efecto Hall utilizando tubos termorretráctiles, tal como se muestra en las imágenes. El correcto funcionamiento del sensor de pasillo dependerá de un imán que se colocará en la carcasa giratoria en el paso 3.
Una vez completado el cableado, puede asegurar las 2 placas superiores con la pantalla LCD, el interruptor y el potenciómetro usando nuevamente 8 tuercas M5 como se muestra en las imágenes.
Dependiendo del modelo de su motor utilizado, es posible que deba ajustar la siguiente línea de código en el archivo MotorControl.ino:
acelerador = mapa (averagePotValue, 0, 1020, 710, 900);
Esta línea de código (línea 176) asigna la posición del potenciómetro de 10K a la señal del ESC. El ESC acepta un valor entre 700 y 2000. Y cuando el motor que usé para este proyecto comenzó a girar alrededor de 823, limité las RPM del motor limitando el valor máximo a 900.
Paso 3: Creación de la plataforma para la transmisión inalámbrica de energía
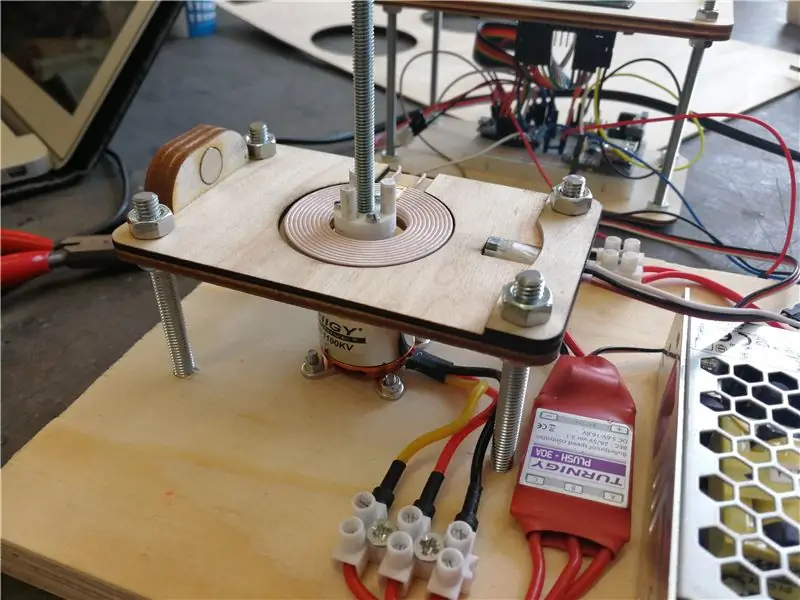
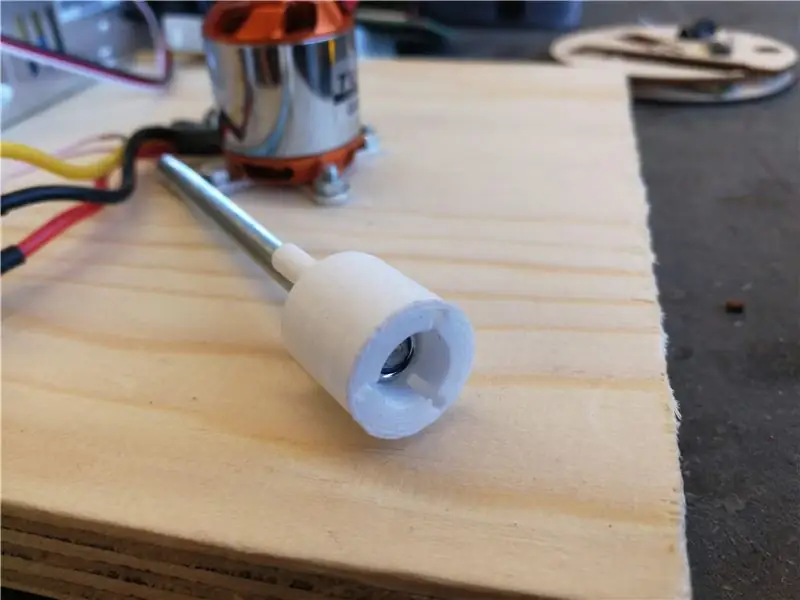
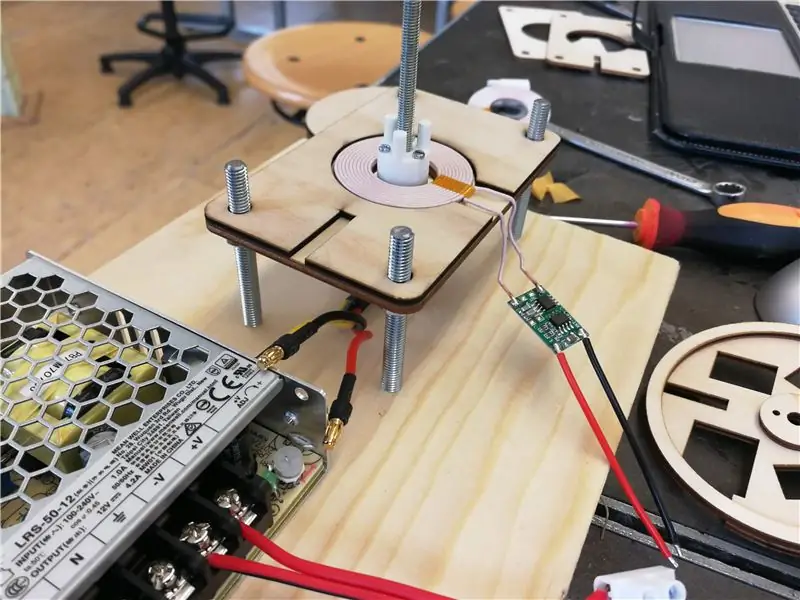
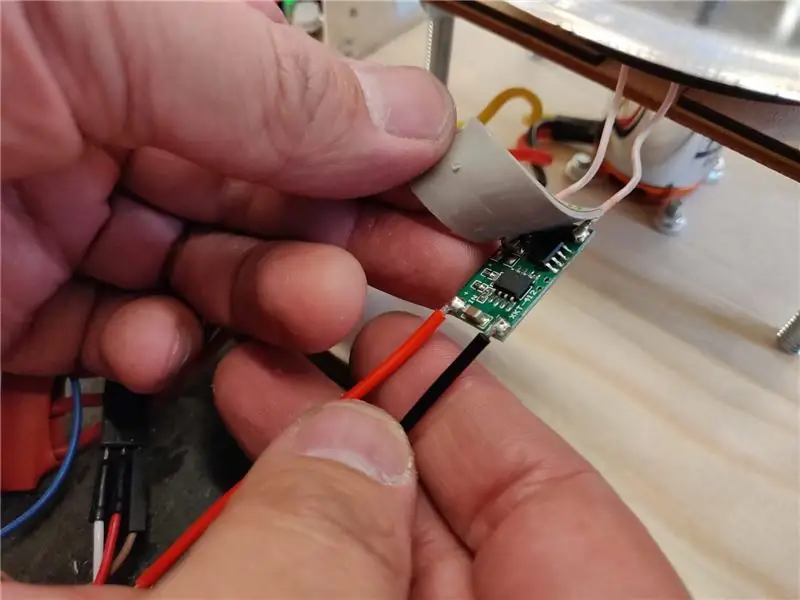
Hoy en día existen básicamente dos formas de alimentar dispositivos que necesitan rotar: anillos colectores o transmitir energía de forma inalámbrica a través de bobinas de inducción. Como los anillos colectores de alta calidad que pueden soportar altas RPM tienden a ser muy costosos y más propensos al desgaste, opté por la opción inalámbrica usando un convertidor DC-DC inalámbrico de 5V. De acuerdo con las especificaciones, debería ser posible transferir hasta 2 amperios usando un convertidor de este tipo.
El convertidor DC-DC inalámbrico consta de dos componentes, un transmisor y un receptor. Tenga en cuenta que la PCB conectada a la bobina de inducción de transmisión es más pequeña que la que recibe.
La plataforma en sí está construida con un trozo de madera de desecho (250 x 180 x 18 mm).
En la plataforma atornillé la fuente de alimentación Mean Well 12V. La salida de 12 V está conectada al ESC (vea los esquemas en el Paso 1) y al PCB de la parte transmisora del Convertidor CC-CC Inalámbrico.
En el archivo Platform_Files.zip adjunto, encontrará los archivos dxf para cortar con láser la plataforma de madera contrachapada con un grosor de 3 mm:
- Platform_001.dxf y Platform_002.dxf: debe colocarlos uno sobre el otro. Esto creará un área empotrada para la bobina de inducción de transmisión.
- Magnet_Holder.dxf: Corte con láser este diseño tres veces. Una de las tres veces, incluye el círculo. En los otros dos cortes con láser: retire el círculo para que no se corte. Después de cortar, pegue las tres piezas para crear un soporte para un imán (diámetro 10 mm, grosor: 3 mm). Usé pegamento para pegar el imán en el soporte del imán. Asegúrese de pegar el lado correcto del imán al soporte, ya que el sensor de pasillo solo funcionará con un lado del imán.
- Platform_Sensor_Cover.dxf: esta pieza le ayudará a mantener el sensor de pasillo conectado a la unidad de control del motor en su lugar, como se muestra en la primera imagen.
- Platform_Drill_Template.dxf: utilicé esta pieza como plantilla para perforar los agujeros en la pieza de madera de desecho. Los cuatro orificios más grandes de 6 mm son para las varillas roscadas de soporte con un diámetro de 6 mm para soportar la plataforma. Los 4 orificios más pequeños son para asegurar el motor sin escobillas al trozo de madera de desecho. El agujero más grande en el medio era necesario para el eje que sobresalía del motor sin escobillas. Como los pernos del motor y las varillas roscadas de la plataforma deben asegurarse en la parte inferior de la plataforma, es necesario agrandar esos orificios unos pocos mm de profundidad para permitir que las tuercas encajen.
Desafortunadamente, el eje del motor sin escobillas sobresalió del lado "incorrecto" para este proyecto. Pero pude revertir el eje con la ayuda de las siguientes instrucciones que encontré en Youtube:
Una vez que el motor y las varillas de soporte están asegurados, la plataforma se puede construir utilizando las piezas de la plataforma cortadas con láser. La plataforma en sí se puede asegurar con 8 tuercas M6. El soporte del imán se puede pegar a la plataforma en el borde como se muestra en la primera imagen.
El archivo adjunto "Bolt-On Adapter.stl" se puede imprimir con una impresora 3D. Este adaptador es necesario para unir una varilla roscada con un diámetro de 4 mm al motor sin escobillas utilizando 3 tornillos M2 con una longitud de 18 mm.
Paso 4: Carcasa giratoria
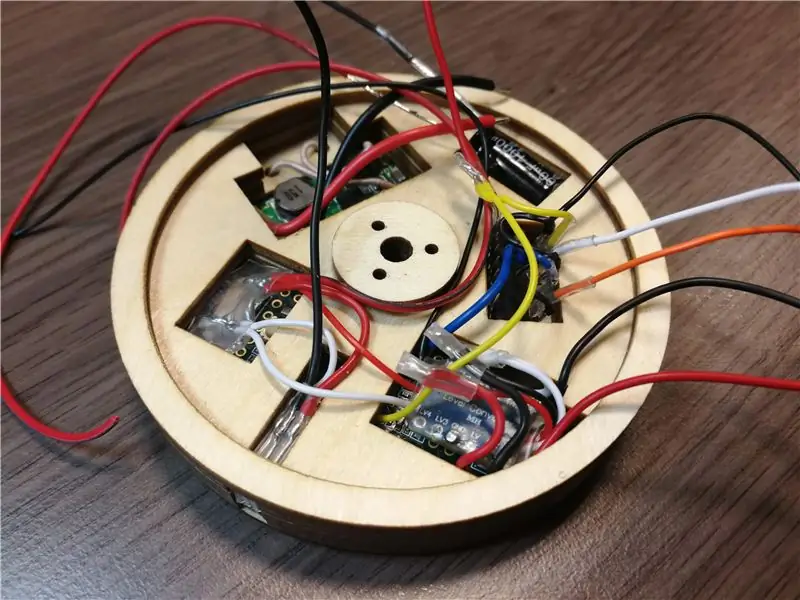
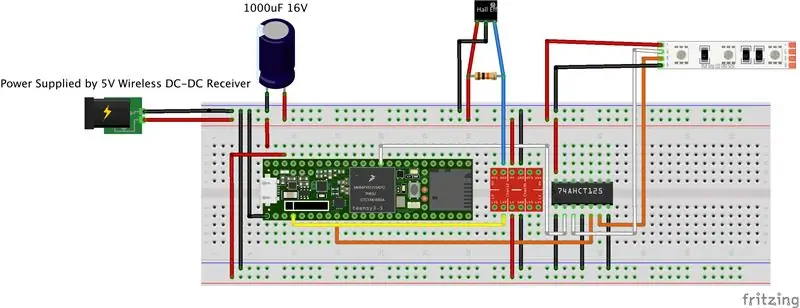
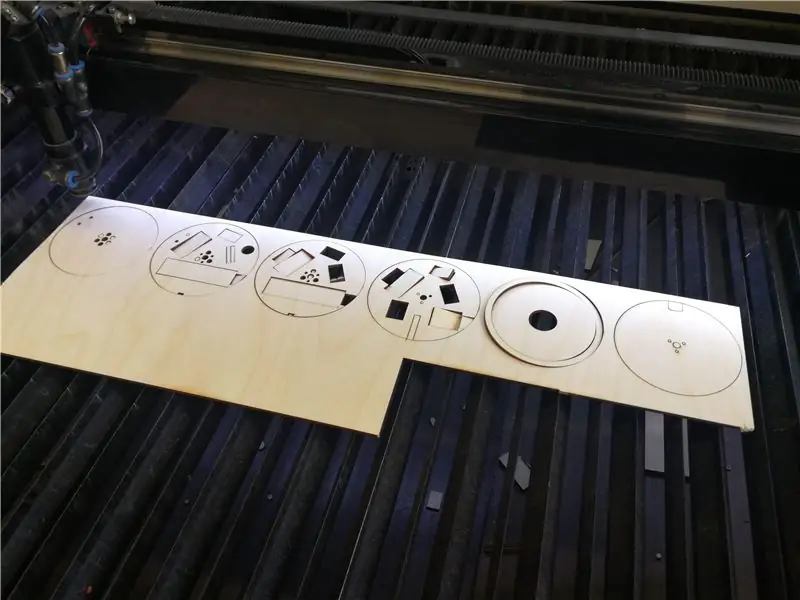
El archivo Base_Case_Files.zip adjunto contiene los archivos dxf para cortar con láser las 6 capas para construir la carcasa de los componentes que controlan la tira de led APA102C.
Las capas 1-3 del diseño de la carcasa están diseñadas para pegarse entre sí. Pero asegúrese de colocar un imán (diámetro 10 mm, altura: 3 mm) en el recorte circular en la Capa 2 antes de pegar las tres capas juntas. También asegúrese de que el imán esté pegado con el poste correcto en la parte inferior, ya que el sensor de efecto Hall colocado en la plataforma construida en el Paso 3 solo responderá a un lado del imán.
El diseño de la caja contiene compartimentos para los componentes enumerados en los esquemas de cableado adjuntos. Se requiere el IC 74AHCT125 para convertir la señal de 3.3V de Teensy a la señal de 5V requerida para la tira de led APA102. Las capas 4 y 5 también se pueden pegar. La capa superior 6 se puede apilar sobre las otras capas. Todas las capas quedarán en la posición correcta con la ayuda de 3 varillas de acero de 2 mm de diámetro. Hay tres orificios pequeños para las varillas de acero de 2 mm que rodean el orificio más grande para la varilla roscada giratoria de 4 mm unida al motor sin escobillas. Una vez que todos los componentes estén soldados de acuerdo con el esquema, se puede colocar la carcasa completa en el adaptador empernado impreso en el Paso 3. Asegúrese de que los cables abiertos estén correctamente aislados utilizando tubos termocontraíbles. Tenga en cuenta que el correcto funcionamiento del sensor Hall de estos pasos depende del imán colocado en el soporte del imán descrito en el paso 3.
El código de prueba de concepto adjunto 3D_POV_POC.ino iluminará algunos leds en rojo. El boceto da como resultado un cuadrado que se muestra una vez que el cilindro comienza a girar. Pero antes de que comience la rotación, los leds necesarios para simular un cuadrado se encienden por defecto. Esto es útil para probar el correcto funcionamiento de los leds en el siguiente paso.
Paso 5: Cilindro giratorio con las tiras de LED
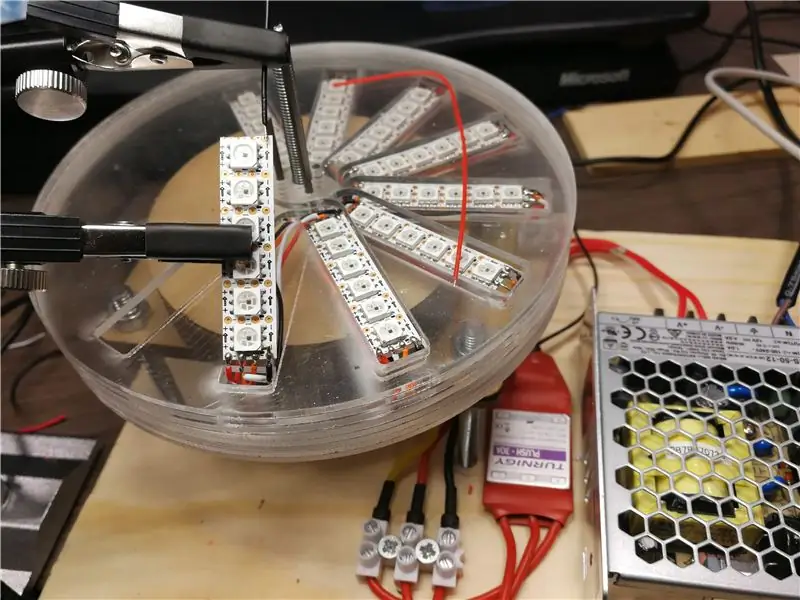
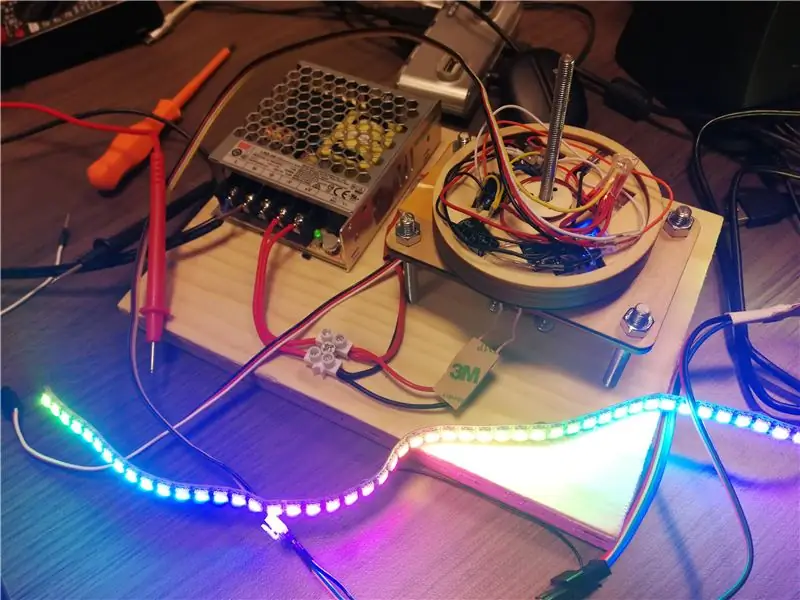
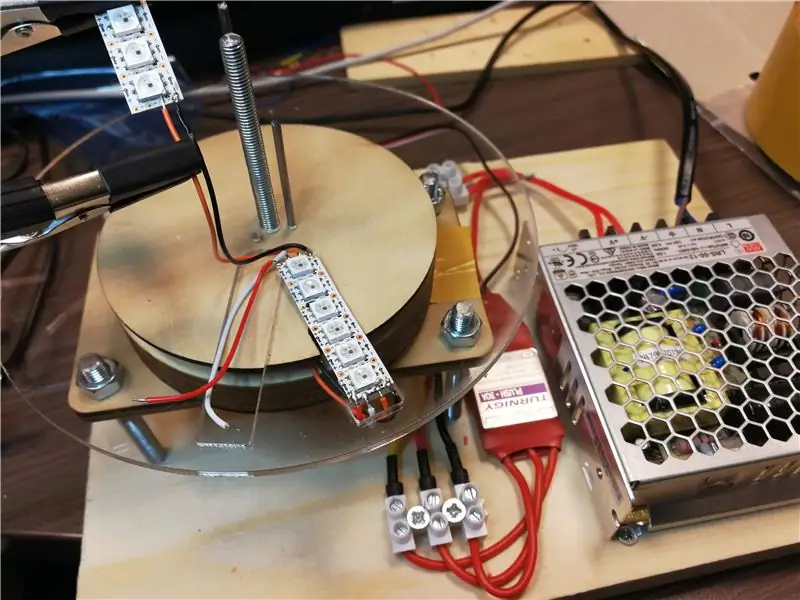
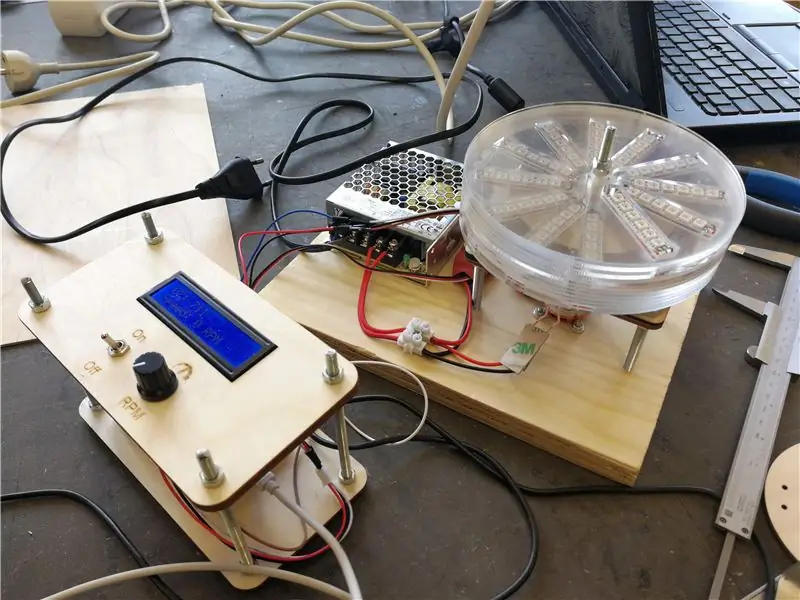
El Rotor_Cylinder_Files.zip adjunto contiene los archivos dxf para cortar una lámina acrílica de 2 mm de grosor. Los 14 discos resultantes son necesarios para construir el cilindro transparente para este proyecto POV. Los discos deben apilarse unos sobre otros. El diseño de los discos cilíndricos permite soldar 12 tiras de led juntas como una tira de led larga. A partir del disco uno, es necesario unir a un disco una pequeña tira de leds que contiene 6 leds utilizando las pegatinas adhesivas de la tira de leds. Suelde los cables a la tira de LED primero antes de unir las tiras de LED al disco con las pegatinas adhesivas. De lo contrario, corre el riesgo de que la pistola de soldadura derrita el disco acrílico.
Una vez que el disco n. ° 13 se apila sobre el cilindro transparente, la varilla de acero de 2 mm utilizada para mantener todas las capas en las posiciones correctas ahora también se puede cortar a la longitud correcta, alineada con la parte superior del disco n. ° 13 del cilindro. El disco n. ° 14 se puede usar para mantener las varillas de acero de 2 mm en su lugar con la ayuda de dos tuercas M4.
Debido a la cantidad de tiempo necesaria para construir todo el dispositivo, todavía no he podido programar pantallas 3D visualmente interesantes más estables dentro del período de tiempo del hackatón. Esa es también la razón por la que el código proporcionado para controlar los leds sigue siendo muy básico para probar el concepto, mostrando solo un cuadrado rojo en 3 dimensiones por el momento.
Paso 6: lecciones aprendidas
Teensy 3.6
- Pedí un Teensy 3.5 para este proyecto, pero el proveedor me envió un Teensy 3.6 por error. Como estaba ansioso por terminar el proyecto dentro del plazo del hackathon, decidí seguir adelante con Teensy 3.6. La razón por la que quería usar Teensy 3.5 era por los puertos, son tolerantes a 5V. Este no es el caso del Teensy 3.6. Esa es también la razón por la que tuve que introducir un convertidor lógico bidireccional en la configuración. Con un Teensy 3.5 esto no habría sido necesario.
- Problema de aumento de energía: al encender el dispositivo, hay un aumento de energía a través del módulo de carga inalámbrico dc-dc para alimentar el Teensy 3.6. Desafortunadamente, la aceleración es demasiado lenta para que el Teensy 3.6 se inicie correctamente. Como solución temporal, actualmente tengo que encender el Teensy 3.6 a través de la conexión micro USB y luego enchufar la fuente de alimentación de 12 V que alimenta el transmisor inalámbrico dc-dc. Una vez que el receptor inalámbrico dc-dc también está suministrando energía al Teensy, puedo desconectar el cable USB. La gente ha compartido su truco con un MIC803 para el problema del aumento lento de potencia aquí:
Módulo de pantalla LCD
Comportamiento errático en energía externa. La pantalla funciona correctamente cuando se alimenta a través de USB. Pero cuando enciendo la pantalla LCD a través de la placa de pruebas usando los 5V suministrados por el BEC o una fuente de alimentación independiente, el texto comienza a codificarse después de unos segundos después de que se supone que el texto debe cambiar. Todavía necesito investigar qué está causando este problema
Mecánico
Para probar la unidad de controlador de mi motor para medir las RPM reales, dejo que el motor gire con el perno en el adaptador, el perno y la carcasa base conectados al motor. Durante una de las pruebas iniciales, los tornillos que conectan el soporte del motor al motor se desenroscan debido a las vibraciones. Afortunadamente, noté este problema a tiempo, por lo que se evitó un posible desastre. Resolví este problema atornillando un poco más los tornillos al motor y también usé unas gotas de Loctite para asegurar los tornillos aún más
Software
Cuando exporta bocetos de Fusion 360 como archivos dxf para el cortador láser, las líneas de apoyo se exportan como líneas regulares
Paso 7: posibles mejoras
¿Qué hubiera hecho de manera diferente en función de la experiencia que obtuve con este proyecto?
- Usar una tira de leds que contenga al menos 7 leds en lugar de 6 leds por capa para obtener visualizaciones textuales más agradables
- Compre un motor sin escobillas diferente donde el eje ya sobresalga del lado correcto (inferior) del motor. (por ejemplo: https://hobbyking.com/de_de/ntm-prop-drive-28-36-1000kv-400w.html) Esto le ahorrará la molestia de cortar el eje o empujar el eje hacia el lado correcto como yo tenía que hacer ahora.
- Dedicar más tiempo a equilibrar el dispositivo para minimizar las vibraciones, ya sea mecánicas o modelarlo en Fusion 360.
También he estado pensando en algunas mejoras potenciales, que podría considerar si el tiempo lo permite:
- Uso real de la funcionalidad de la tarjeta SD en Teensy para crear animaciones más largas
- Aumente la densidad de las imágenes mediante el uso de leds más pequeños (APA102 (C) 2020). Cuando comencé este proyecto hace unas semanas, las tiras de led que contenían estos pequeños leds (2x2 mm) no estaban disponibles en el mercado. Es posible comprarlos como componentes SMD separados, pero solo consideraría esta opción si está dispuesto a soldar estos componentes en una PCB personalizada.
- Transfiera imágenes 3D de forma inalámbrica al dispositivo (Wifi o Bluetooth). Esto también debería permitir programar el dispositivo para visualizar sonido / música.
- Convierta animaciones de Blender a un formato de archivo que se pueda usar con el dispositivo
- Coloca todas las tiras de led en la placa base y enfoca la luz hacia las capas de acrílico. En cada capa diferente se pueden grabar pequeñas áreas para reflejar la luz cuando se omite en los leds. La luz debe enfocarse en las áreas grabadas. Esto debería ser posible creando un túnel que guíe la luz o usando lentes en los leds para enfocar la luz.
- Mejora de la estabilidad de la pantalla volumétrica 3D y regulación de la velocidad de rotación separando la base giratoria del motor sin escobillas mediante el uso de engranajes y una correa de distribución.
Paso 8: Grita
Me gustaría agradecer especialmente a las siguientes personas:
- Mi fantástica esposa e hijas, por su apoyo y comprensión.
- Teun Verkerk, por invitarme al Hackathon
- Nabi Kambiz, Nuriddin Kadouri y Aidan Wyber, por su apoyo, asistencia y orientación durante todo el Hackaton.
- Luuk Meints, un artista y compañero participante de este Hackaton que fue tan amable de darme un curso rápido de introducción personal de 1 hora a Fusion 360 que me permitió modelar todas las partes que necesitaba para este proyecto.
Recomendado:
Panel lateral transparente de bricolaje de un monitor reciclado: 8 pasos (con imágenes)
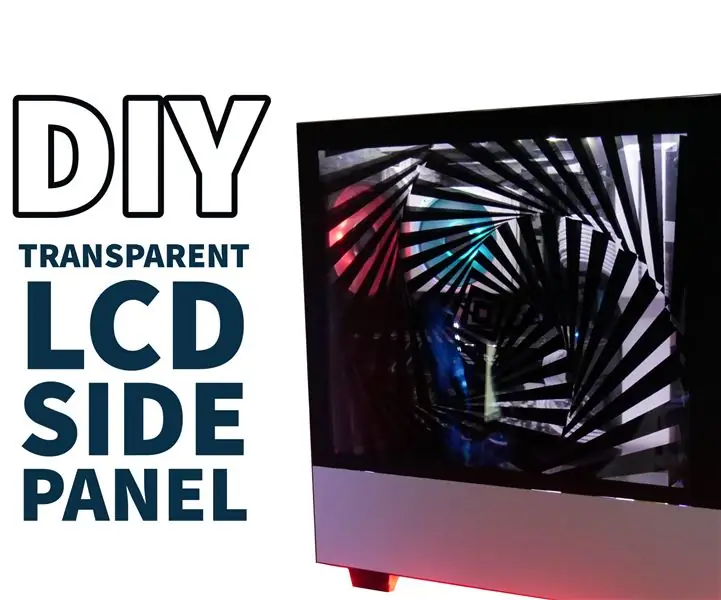
Panel lateral transparente de bricolaje de un monitor reciclado: Vi un video realmente genial de una carcasa de PC llamada " Snowblind ", que tenía una pantalla LCD transparente como panel lateral. Me sorprendió lo genial que era. El único problema era que era muy caro. ¡Por lo tanto, intenté hacer el mío! En esto yo
Grabador de código de barras de Apple (Photonics Hackathon Phablabs): 3 pasos
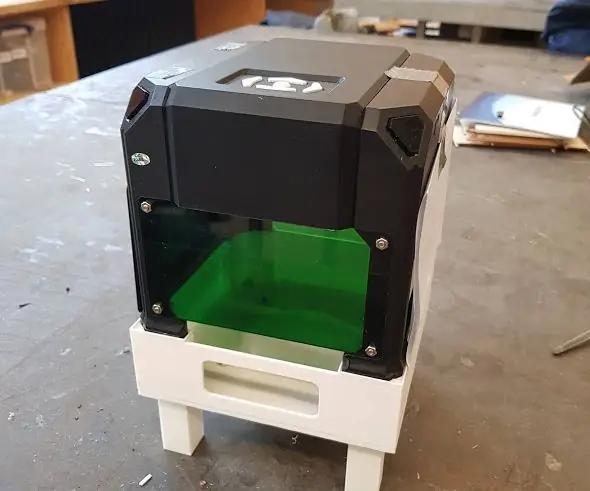
Grabador de código de barras de Apple (Photonics Hackathon Phablabs): Hola a todos: Como parte de nuestro desafío Phablabs Photonics, se nos pidió que creáramos un dispositivo capaz de reemplazar las pegatinas de las frutas. ¿También odias las pegatinas de frutas? ¿Y le gustaría hacer un cambio respetuoso con el medio ambiente? Entonces nos gustaría ins
Smartphone transparente: 4 pasos (con imágenes)
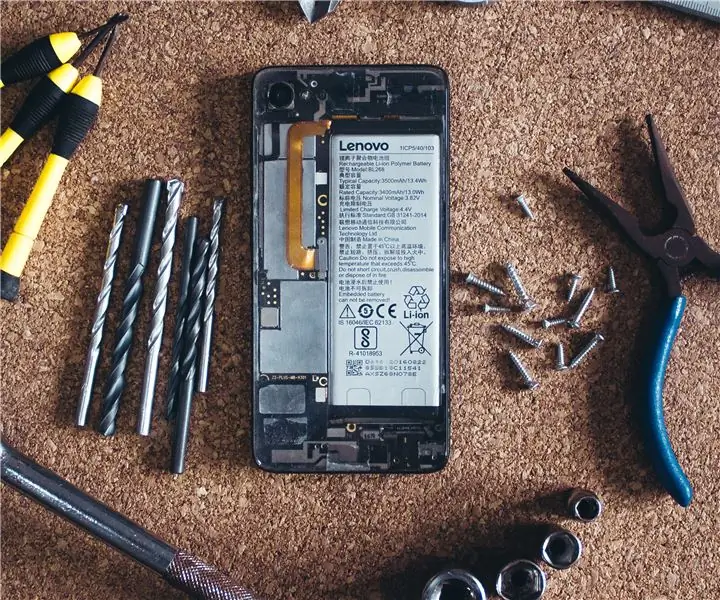
Smartphone transparente: Inscríbase en mi curso de 'Electrónica en pocas palabras' aquí: https: //www.udemy.com/electronics-in-a-nutshell/? … También consulte mi canal de youtube aquí para ver más proyectos y tutoriales de electrónica : https://www.youtube.com/channel/UCelOORs7UioZ4TZF…A
Placas holográficas - Photonics Challenger Hackathon PhabLabs: 6 pasos
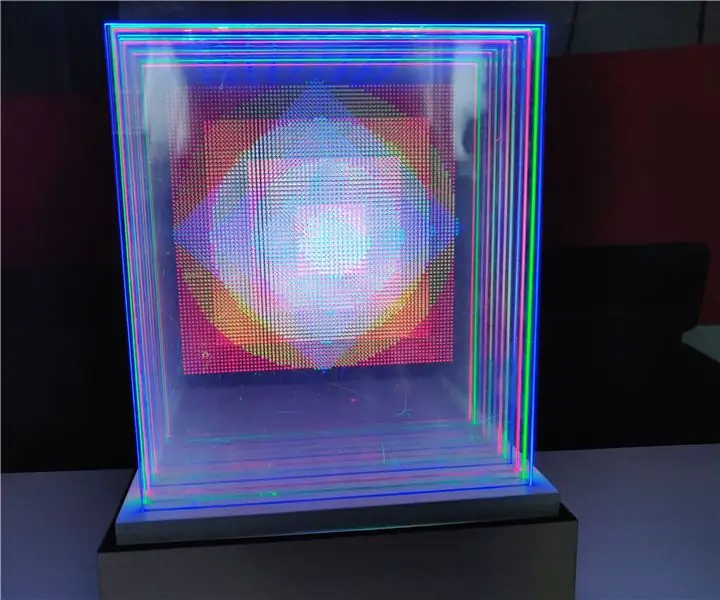
Placas holográficas - Photonics Challenger Hackathon PhabLabs: A principios de este año me pidieron que participara en el PhabLabs Photonics Hackathon en el Science Center Delft en los Países Bajos. Aquí tienen un gran espacio de trabajo con muchas máquinas que podrían usarse para crear algo que yo soy normal
Enorme matriz LED transparente flexible por menos de $ 150. Fácil de hacer: 8 pasos (con imágenes)
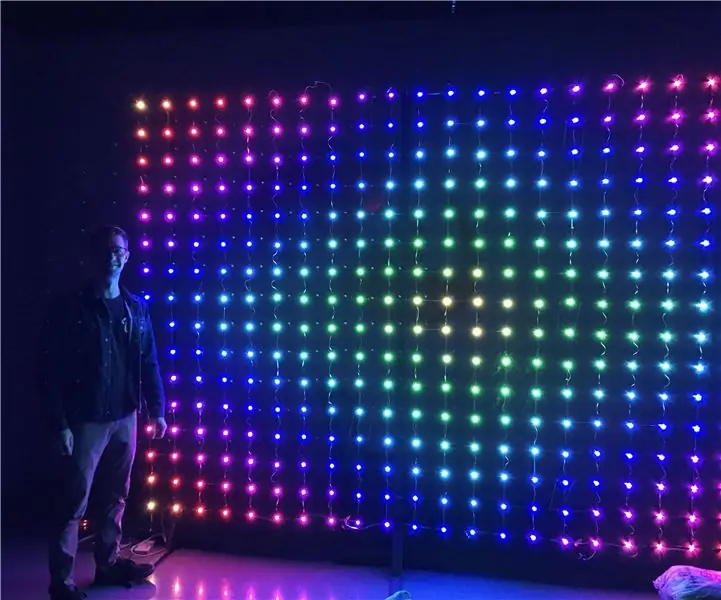
Enorme matriz LED transparente flexible por menos de $ 150. Fácil de hacer: quiero comenzar diciendo que no soy un profesional, no tengo ningún título en electrónica. Simplemente disfruto trabajando con mis manos y resolviendo cosas. Lo digo para animar a todos los no profesionales como yo. Tienes la capacidad de