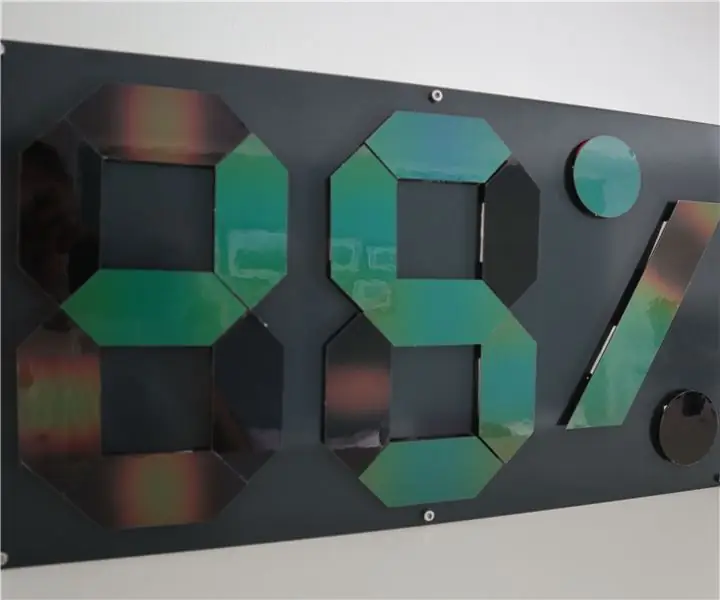
Tabla de contenido:
- Suministros
- Paso 1: hacer las placas de cobre
- Paso 2: Colocación de la hoja de cristal líquido
- Paso 3: Colocación del elemento TEC
- Paso 4: preparación de la placa de aluminio
- Paso 5: Adjuntar segmentos
- Paso 6: Colocación de los disipadores de calor y los soportes
- Paso 7: carga de código
- Paso 8: Locura de cableado
- Paso 9: preparación de la placa acrílica
- Paso 10: Proyecto terminado
2025 Autor: John Day | [email protected]. Última modificación: 2025-01-23 14:39
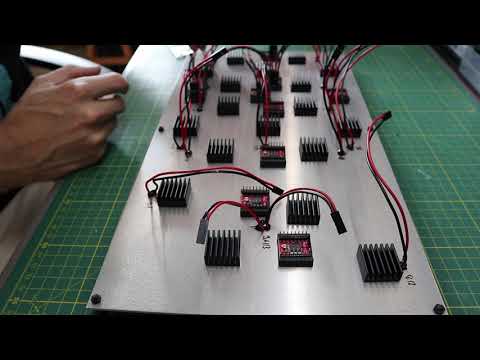
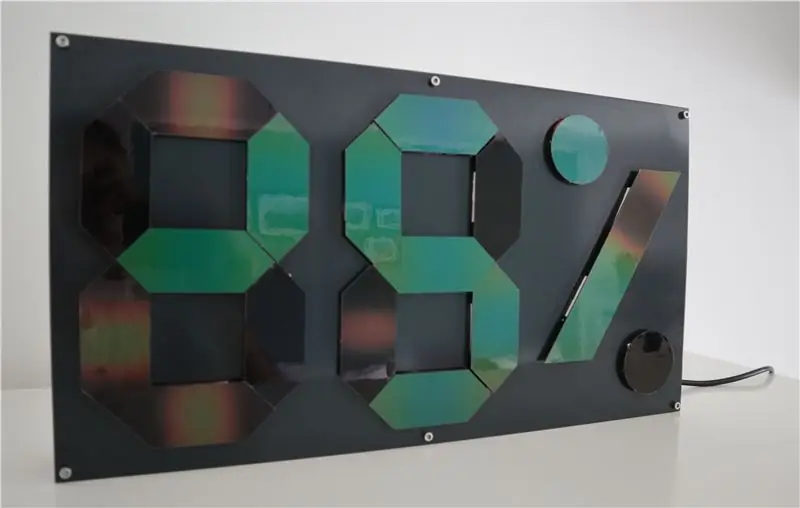

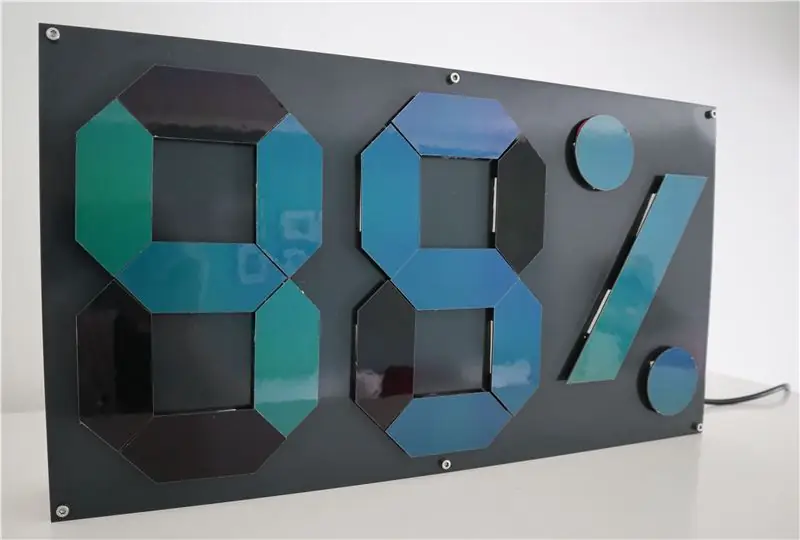
Llevo bastante tiempo trabajando en este proyecto. La idea original se me ocurrió después de construir un demostrador de controlador TEC en el trabajo para una feria comercial. Para mostrar las capacidades de calentamiento y enfriamiento de TEC, estábamos usando pintura termocrómica que cambia de negro a transparente.
En este proyecto, llevé la idea más allá y construí una pantalla de 7 segmentos de dos dígitos utilizando placas de cobre que están cubiertas con láminas termocrómicas basadas en cristales líquidos. Detrás de cada placa de cobre se encuentra un elemento TEC que controla la temperatura y, por lo tanto, cambia el color de la lámina de cristal líquido. Los números mostrarán la temperatura y la humedad de un sensor DHT22.
Puede apreciar la ironía de tener un dispositivo que muestra la temperatura ambiente cambiando su propia temperatura;-)
Suministros
- 3 piezas, lámina de cristal líquido de 150x150 mm (29-33 ° C) (ver aquí).
- 17 piezas, placas de cobre, 1 mm de grosor (consulte las dimensiones a continuación)
- Placa de aluminio de 401 x 220 x 2 mm (gris / anodizado negro)
- Placa acrílica de 401 x 220 x 2 mm (blanca)
- 18 piezas, elemento peltier TES1-12704
- 9 piezas, controlador de motor dual TB6612FNG
- 6 piezas, Arduino Nano
- 2 piezas, ventilador de refrigeración de 40x40x10 mm
- 18 piezas, disipador de calor de 25x25x10 mm
- Fuente de alimentación de 12 V, 6 A
- Sensor de temperatura y humedad DHT22 (AM2302)
- 6 piezas, separadores de PCB de 40 mm de largo
Además, utilicé este epoxi termoconductor que era bastante barato y tiene una vida útil prolongada. Se utilizó un taladro y una herramienta dremel para hacer los agujeros necesarios en las placas de aluminio y acrílico. El soporte para los arduinos y los PCB del controlador del motor se imprimieron en 3D y se adhirieron con pegamento caliente. Además, utilicé montones de cables dupont para hacer todas las conexiones. Además, esta placa de circuito impreso con terminales de tornillo resultó muy útil para distribuir la fuente de alimentación de 12 V.
Atención: Aparentemente, muchas de las placas TB6612FNG tienen instalados los condensadores incorrectos. Aunque todos los vendedores especifican la placa para voltajes de motor de hasta 15 V, los condensadores a menudo solo tienen una clasificación de 10 V. Después de que exploté los condensadores en mis dos primeras placas, los desolé todos y los reemplacé por los adecuados.
Paso 1: hacer las placas de cobre
Para las placas de cobre utilicé un servicio de corte por láser en línea (ver aquí) donde pude cargar los archivos dxf adjuntos. Sin embargo, dado que las formas no son muy complicadas, el corte por láser no es obligatorio y probablemente existen técnicas de fabricación más baratas (por ejemplo, punzonado, aserrado). En total, se necesitan 14 de los segmentos, dos círculos y un guión para la pantalla. El grosor de las placas de cobre era de 1 mm, pero probablemente podría reducirse a 0,7 o 0,5 mm, lo que necesitaría menos potencia de calentamiento / enfriamiento. Usé cobre porque la capacidad calorífica y la conductividad térmica son superiores al aluminio, pero este último también debería funcionar razonablemente bien.
Paso 2: Colocación de la hoja de cristal líquido
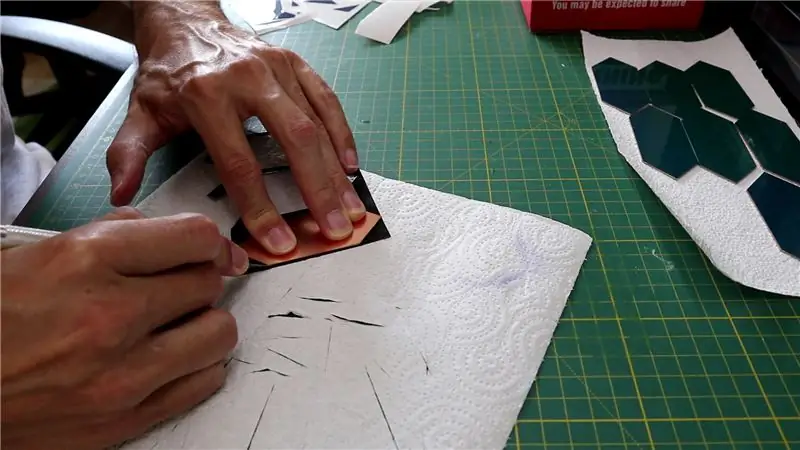
El componente clave de este proyecto es la lámina de cristal líquido termocrómico que obtuve de SFXC. La lámina está disponible en diferentes rangos de temperatura y cambia de color de negro a bajas temperaturas sobre rojo, naranja y verde a azul a altas temperaturas. Probé dos anchos de banda diferentes 25-30 ° C y 29-33 ° C y terminé eligiendo el último. Debido a que calentar con un elemento Peltier es más fácil que enfriar, el rango de temperatura debe estar ligeramente por encima de la temperatura ambiente.
La lámina de cristal líquido tiene un respaldo autoadhesivo que se adhiere muy bien a las placas de cobre. El exceso de lámina se cortó alrededor de la placa con un cuchillo exacto.
Paso 3: Colocación del elemento TEC
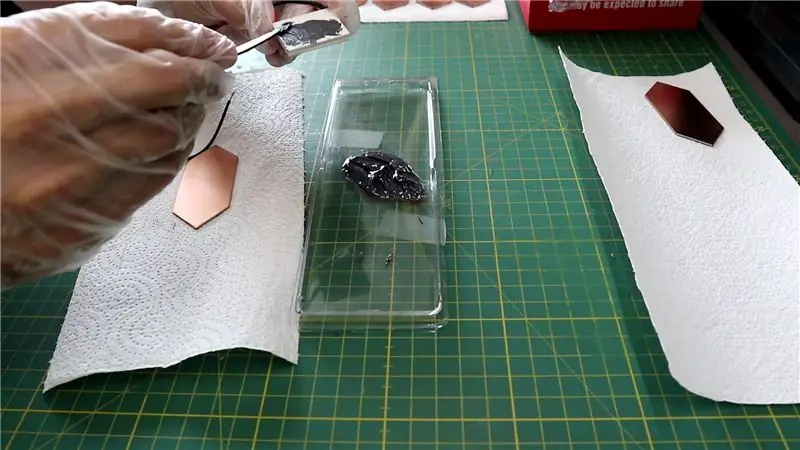
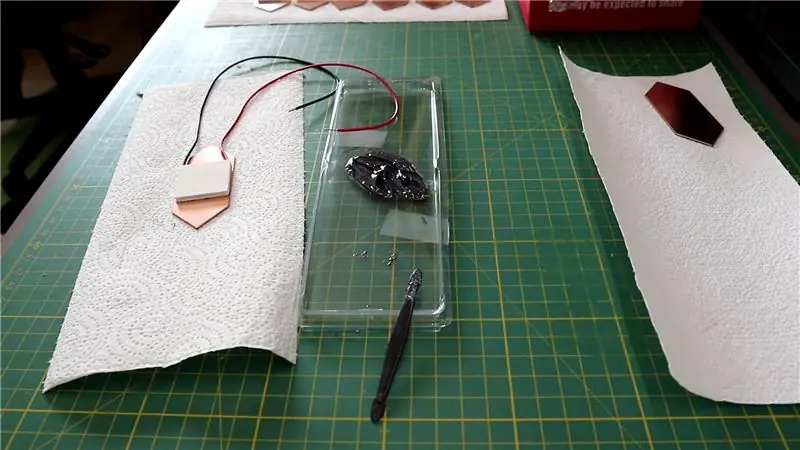
Los peltiers se unieron al centro de cada placa de cobre usando epoxi térmicamente conductor. Las placas son un poco más grandes que los peltiers por lo que quedan completamente escondidas detrás. Para la placa más larga que constituye el guión del símbolo de porcentaje, utilicé dos peltiers.
Paso 4: preparación de la placa de aluminio
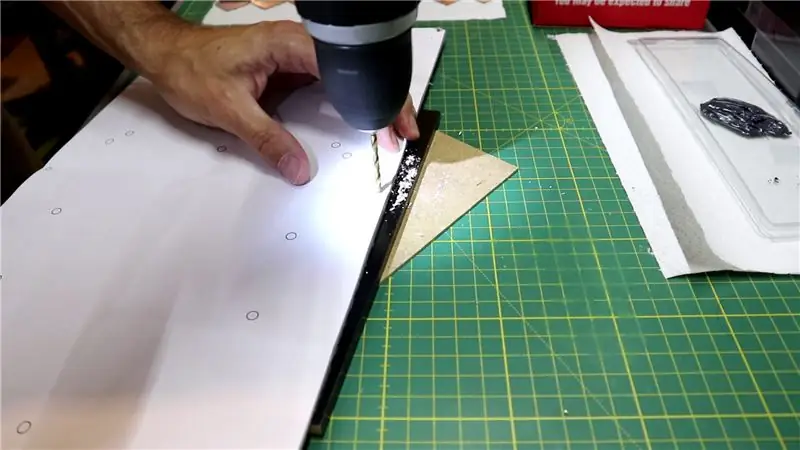
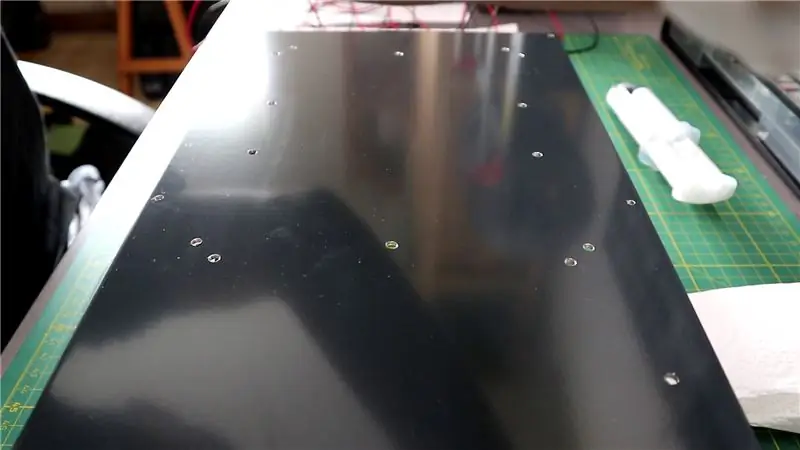
Para ahorrar algo de dinero, yo mismo hice todos los agujeros en la placa de aluminio. Acabo de imprimir el pdf adjunto en papel A3 y lo usé como plantilla de perforación. Hay un orificio para cada segmento por donde pasan los cables TEC y 6 orificios en los bordes para colocar la placa acrílica más tarde.
Paso 5: Adjuntar segmentos
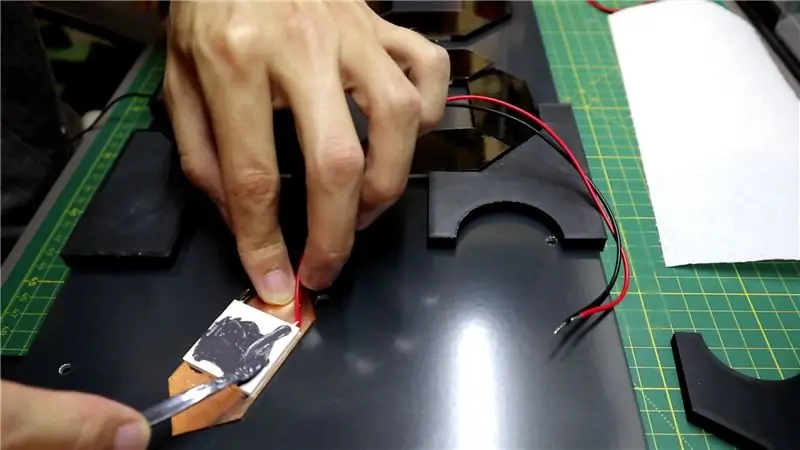
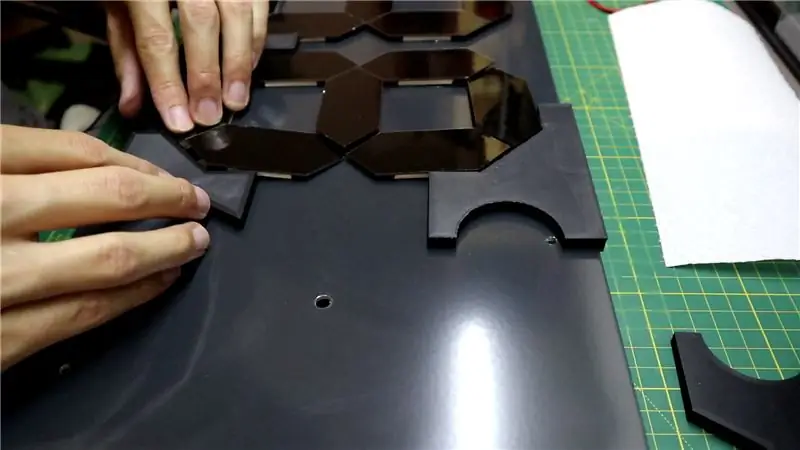
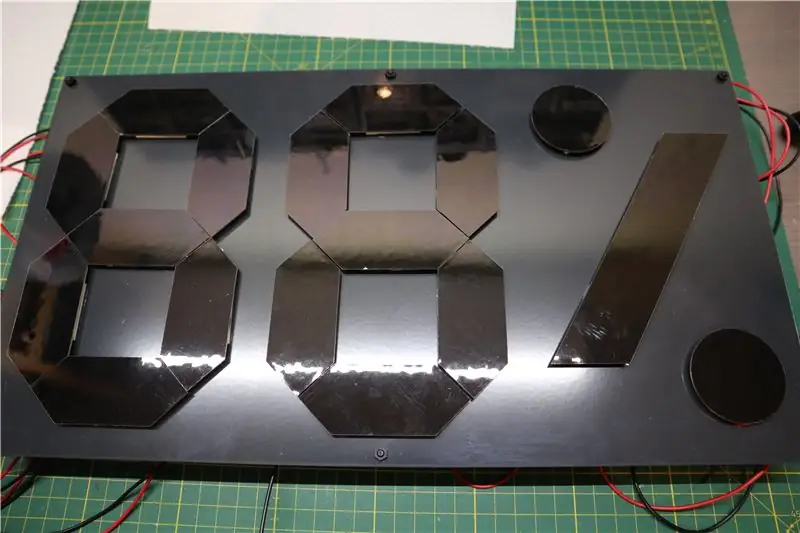
Una de las partes más difíciles de este proyecto fue unir los segmentos correctamente a la placa posterior. Imprimí en 3D varias plantillas que me ayudarían con la alineación de los segmentos, pero esto solo funcionó parcialmente porque los segmentos se deslizaban constantemente. Además, los cables empujan el peltier para que se suelte de la placa. De alguna manera logré pegar todos los segmentos en el lugar correcto, pero uno de los peltiers en el segmento del tablero tiene un acoplamiento térmico muy malo. Podría ser mejor usar almohadillas térmicas autoadhesivas en lugar de epoxi, aunque sospecho que puede aflojarse con el tiempo.
Paso 6: Colocación de los disipadores de calor y los soportes
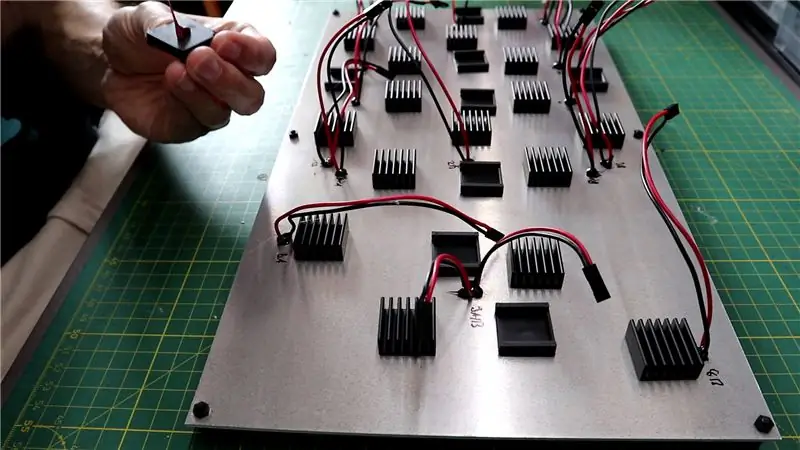
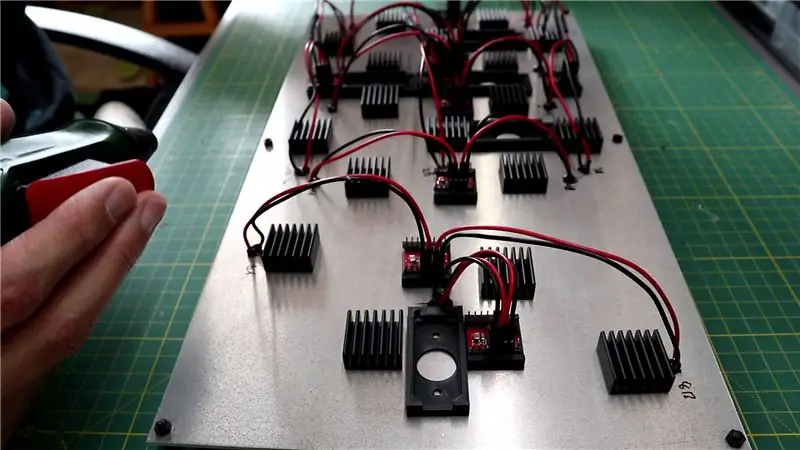
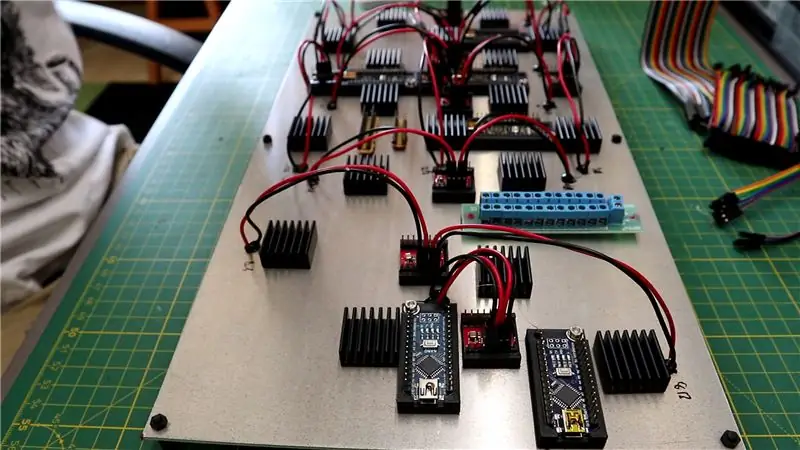
Mi idea original era usar la placa de aluminio como disipador de calor para los peltiers incluso sin ventilador. Pensé que la temperatura total de la placa solo aumentaría ligeramente ya que algunos segmentos se enfrían mientras que otros se calientan. Sin embargo, resultó que sin disipadores de calor adicionales y sin ventilador de enfriamiento, la temperatura seguirá aumentando hasta un punto en el que las placas de cobre ya no se pueden enfriar. Esto es especialmente problemático ya que no utilizo termistores para controlar la potencia de calefacción / refrigeración, pero siempre uso un valor fijo. Por lo tanto, compré pequeños disipadores de calor con una almohadilla autoadhesiva que se unieron a la parte posterior de la placa de aluminio detrás de cada peltier.
Después de eso, los soportes impresos en 3D para los controladores de motor y los arduinos también se unieron a la parte posterior de la placa con pegamento caliente.
Paso 7: carga de código
Cada arduino solo puede controlar hasta dos controladores de motor, ya que necesitan dos pines PWM y 5 pines IO digitales. También hay controladores de motor que se pueden controlar a través de I2C (ver aquí) pero no son compatibles con la lógica de 5 V de los arduinos. En mi circuito hay un arduino "maestro" que se comunica con 5 arduinos "esclavos" a través de I2C que a su vez controlan los controladores del motor. El código para los arduinos se puede encontrar aquí en mi cuenta de GitHub. En el código para los arduinos "esclavos", la dirección I2C debe cambiarse para cada arduino en el encabezado. También hay algunas variables que permiten cambiar la potencia de calefacción / refrigeración y las constantes de tiempo correspondientes.
Paso 8: Locura de cableado
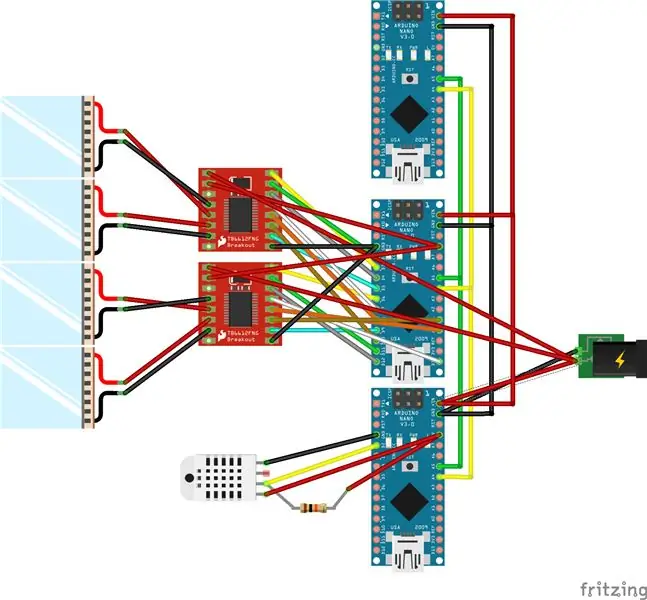
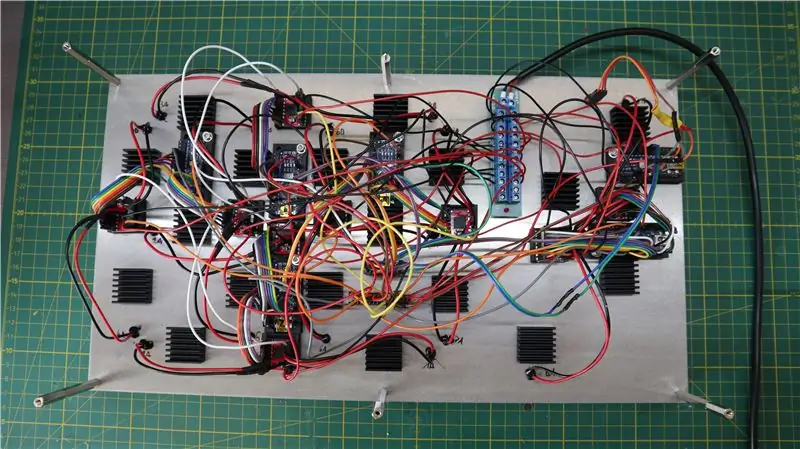
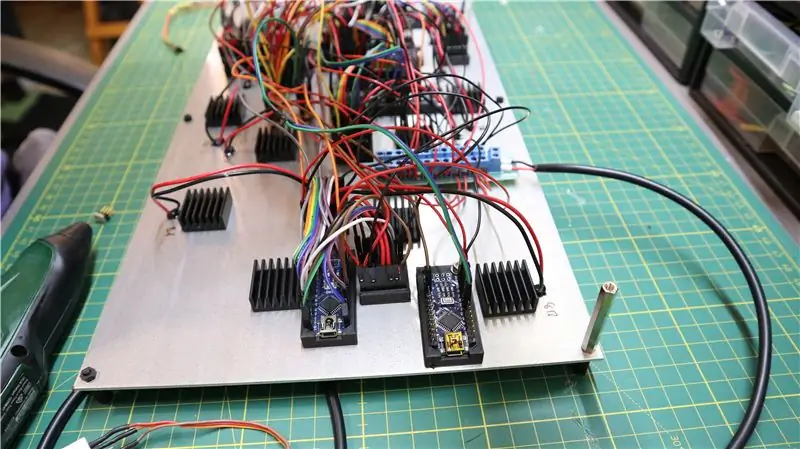
El cableado de este proyecto fue una pesadilla total. He adjuntado un diagrama de fritzing que muestra las conexiones para el arduino maestro y un arduino esclavo único como ejemplo. Además, hay un pdf que documenta qué TEC está conectado a qué controlador de motor y arduino. Como puede ver en las imágenes, debido a la gran cantidad de conexiones, el cableado se vuelve muy complicado. Usé conectores dupont siempre que fue posible. La fuente de alimentación de 12 V se distribuyó mediante una placa de circuito impreso con terminales de tornillo. En la entrada de alimentación, conecté un cable de CC con cables sueltos. Para distribuir las conexiones de 5 V, GND e I2C, equipé algunos prototipos de PCB con conectores de clavija macho.
Paso 9: preparación de la placa acrílica
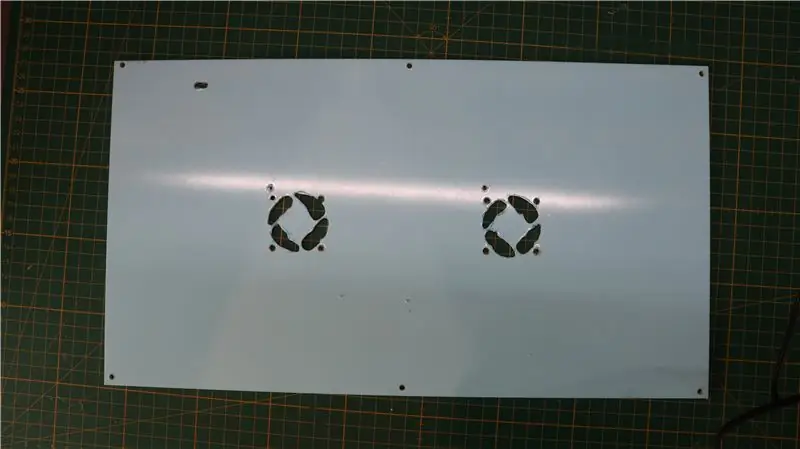
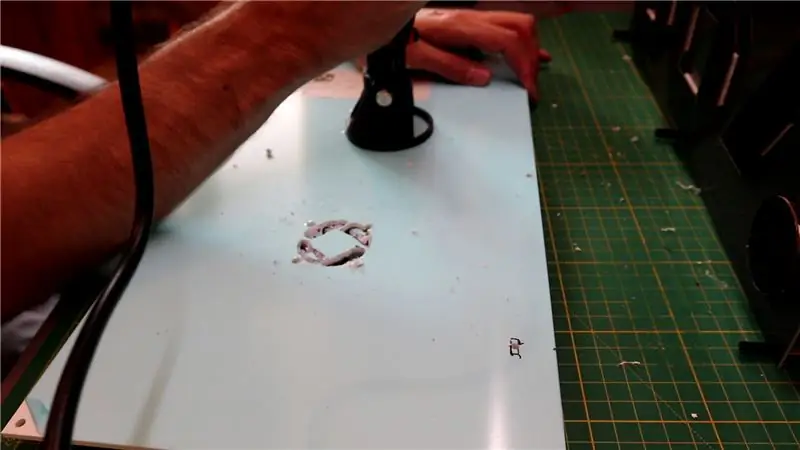
A continuación, perforé algunos agujeros en la placa acrílica para que se pueda unir a la placa de aluminio a través de separadores de PCB. Además, hice algunos recortes para los ventiladores y una hendidura para el cable del sensor DHT22 con mi herramienta dremel. Después de eso, los ventiladores se colocaron en la parte posterior de la placa acrílica y los cables se introdujeron a través de algunos orificios que hice. La próxima vez probablemente haré la placa mediante corte por láser.
Paso 10: Proyecto terminado
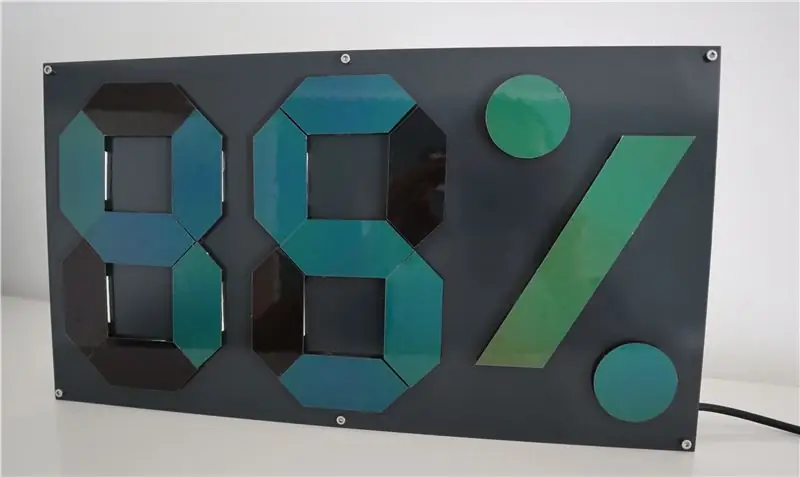
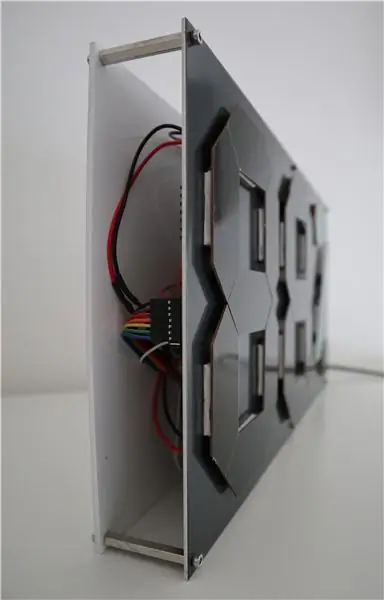
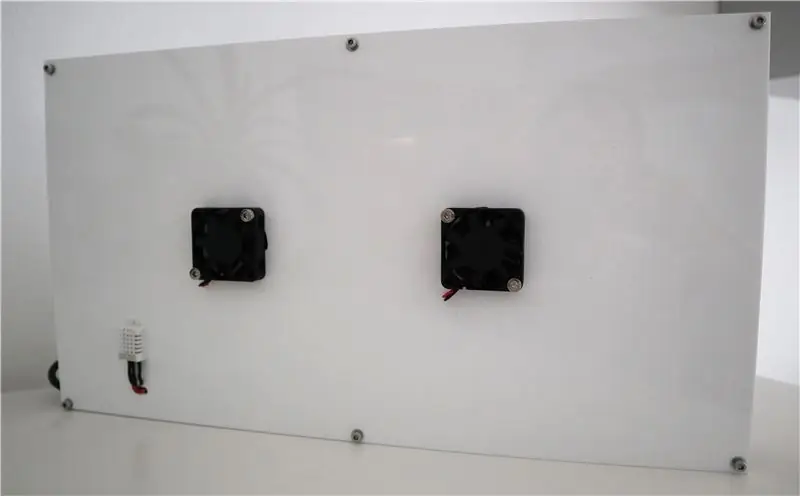
Finalmente, la placa acrílica y la placa de aluminio se unieron entre sí utilizando separadores de PCB de 40 mm de largo. Después de eso, el proyecto está terminado.
Cuando se conecta a la fuente de alimentación, los segmentos mostrarán la temperatura y la humedad, alternativamente. Para la temperatura, solo el punto superior cambiará de color mientras que el guión y el punto inferior también se resaltan cuando se muestra la humedad.
En el código, cada segmento activo se calienta durante 25 segundos mientras simultáneamente enfría los segmentos no activos. Después de eso, los peltiers se apagan durante 35 segundos para que la temperatura pueda estabilizarse nuevamente. Sin embargo, la temperatura de las placas de cobre aumentará con el tiempo y se necesita algún tiempo hasta que los segmentos cambien completamente de color. Se midió que el consumo de corriente para un solo dígito (7 segmentos) era de aproximadamente 2 A, por lo que el consumo de corriente total para todos los segmentos probablemente esté cerca del máximo de 6 A que puede proporcionar la fuente de alimentación.
Ciertamente, se podría reducir el consumo de energía agregando termistores como retroalimentación para ajustar la potencia de calefacción / refrigeración. Ir un paso más allá sería utilizar un controlador TEC dedicado con bucle PID. Esto probablemente debería permitir un funcionamiento constante sin mucho consumo de energía. Actualmente estoy pensando en construir un sistema de este tipo utilizando controladores Thorlabs MTD415T TEC.
Otra desventaja de la configuración actual es que se puede escuchar la salida PWM de 1 kHz de los controladores del motor. También sería bueno si uno pudiera deshacerse de los ventiladores porque también son bastante ruidosos.
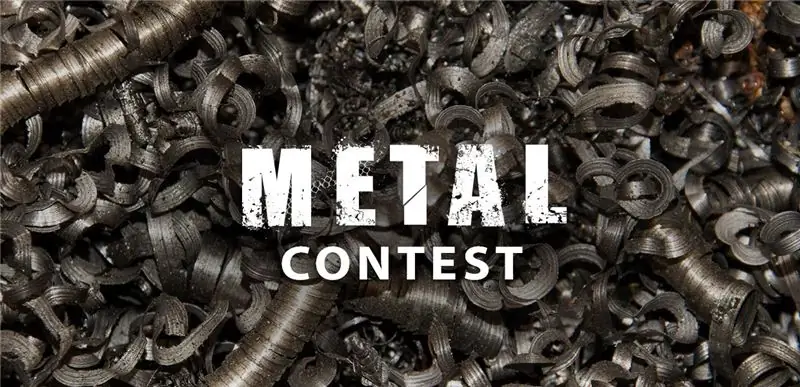
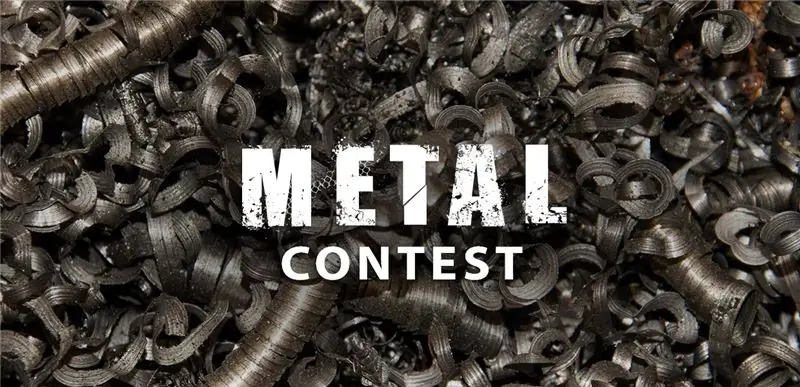
Primer premio en el concurso de metales
Recomendado:
Medidor de temperatura y humedad de IoT con pantalla OLED: 5 pasos (con imágenes)
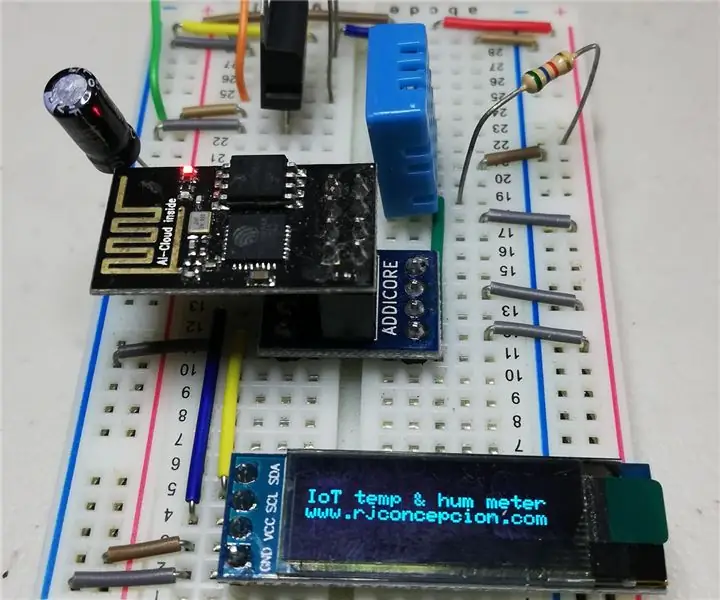
Medidor de temperatura y humedad de IoT con pantalla OLED: verifique la temperatura y la humedad en una pantalla OLED en cualquier momento que desee y al mismo tiempo recopile esos datos en una plataforma de IoT.La semana pasada publiqué un proyecto llamado Medidor de temperatura y humedad de IoT más simple. Ese es un buen proyecto porque puedes c
Pantalla termocrómica de temperatura y humedad - Versión de PCB: 6 pasos (con imágenes)
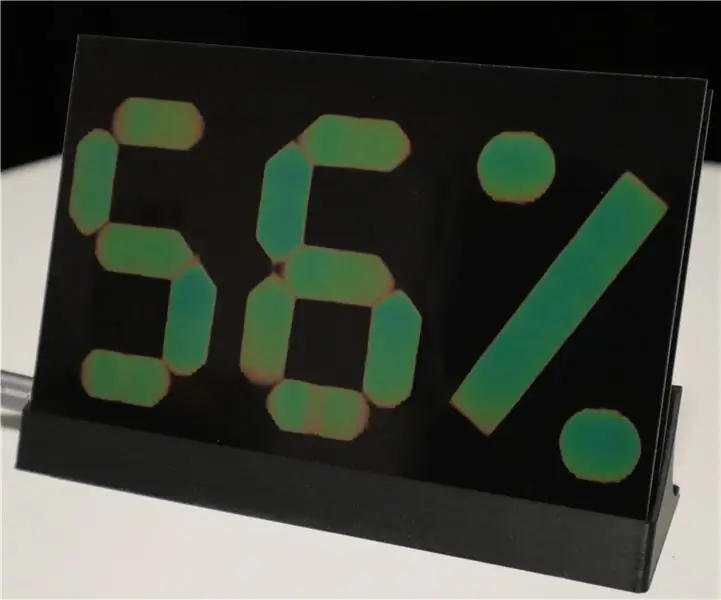
Pantalla termocrómica de temperatura y humedad - Versión de PCB: Hace un tiempo hicimos un proyecto llamado Thermochromic Temperature & Pantalla de humedad donde construí una pantalla de 7 segmentos con placas de cobre que fueron calentadas / enfriadas por elementos Peltier. Las placas de cobre se cubrieron con una lámina termocrómica que cha
¡Automatizando un invernadero con LoRa! (Parte 1) -- Sensores (temperatura, humedad, humedad del suelo): 5 pasos
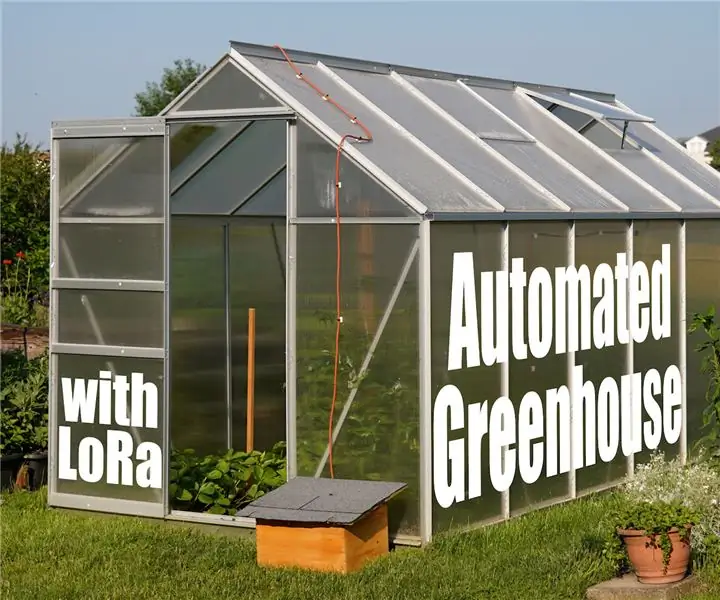
¡Automatizando un invernadero con LoRa! (Parte 1) || Sensores (temperatura, humedad, humedad del suelo): en este proyecto les mostraré cómo automaticé un invernadero. Eso significa que les mostraré cómo construí el invernadero y cómo conecté la electrónica de potencia y automatización. También te mostraré cómo programar una placa Arduino que usa L
Pantalla de humedad de temperatura de 24 horas Arduino: 3 pasos (con imágenes)
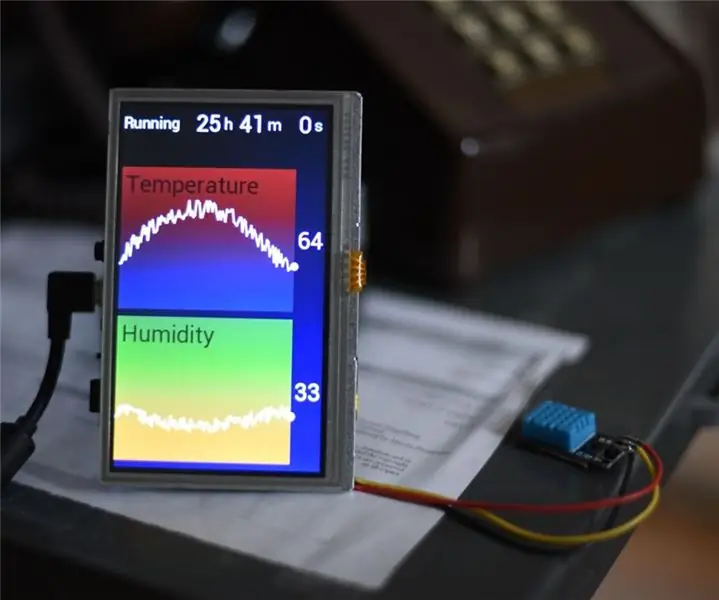
Pantalla de humedad de temperatura de 24 horas Arduino: el DHT11 es un gran sensor para comenzar. Es barato y fácil de conectar a un Arduino. Informa la temperatura y la humedad con aproximadamente un 2% de precisión, y este instructable utiliza un Gameduino 3 como pantalla gráfica, que muestra 24 horas de historial. W
Controle sus electrodomésticos con su control remoto de TV (control remoto por infrarrojos) con pantalla de temperatura y humedad: 9 pasos
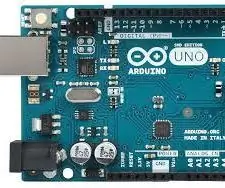
Controle sus electrodomésticos con su control remoto de TV (control remoto por infrarrojos) con pantalla de temperatura y humedad: hola, soy Abhay y es mi primer blog sobre Instructables y hoy le mostraré cómo controlar sus electrodomésticos con el control remoto de su televisor construyendo esto. proyecto simple. gracias al laboratorio atl por el apoyo y el suministro de material