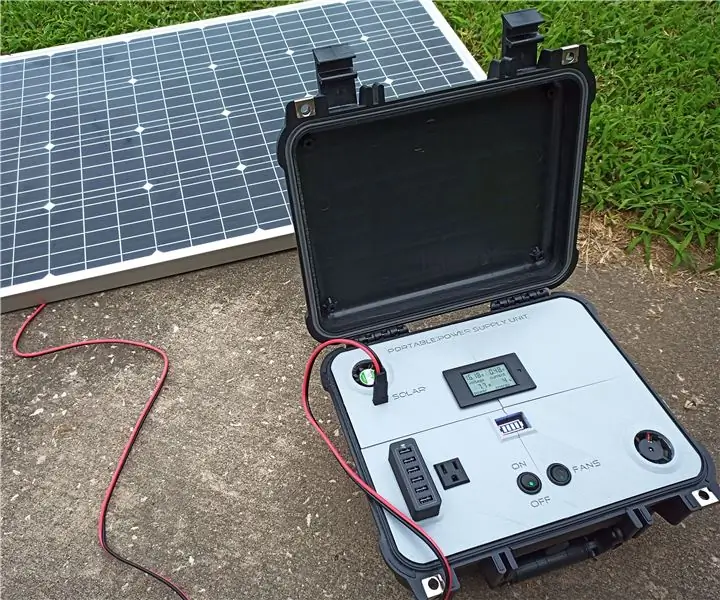
Tabla de contenido:
2025 Autor: John Day | [email protected]. Última modificación: 2025-01-23 14:39
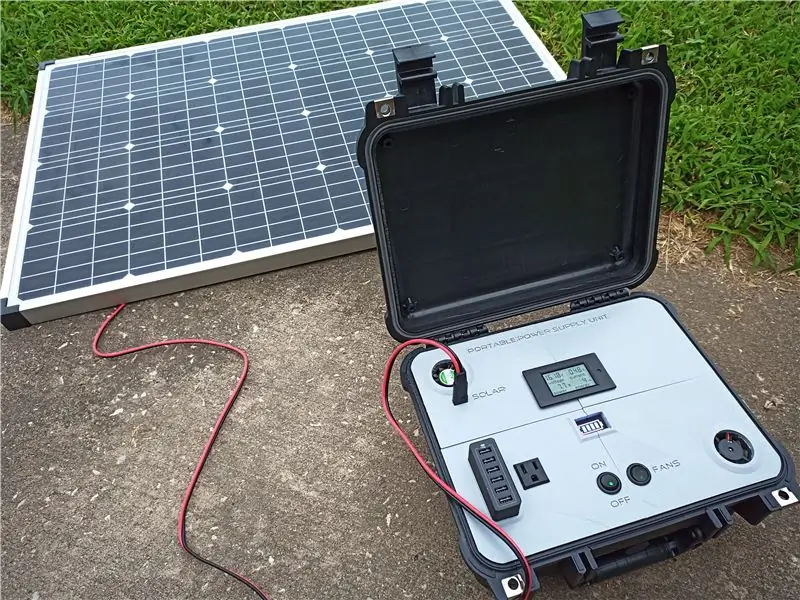
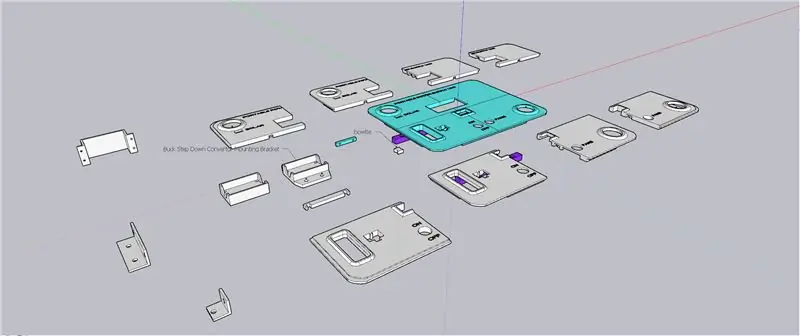
La inspiración para este proyecto provino de querer un método para recargar las baterías de mis drones en el campo. Otro buen momento de uso sería para acampar. Esta construcción no es necesariamente la alternativa más barata. Hay muchos productos disponibles comercialmente que ofrecen mucho por un precio razonable. Tenía alrededor de la mitad de los componentes necesarios simplemente sentados. Además, quería hacer algo en el pasado, así que decidí construir en lugar de comprar. Si no tiene ninguno de los artículos en la sección de materiales y costos, espere gastar más de 400 dólares estadounidenses por el total. Esa cantidad puede comprar una configuración decente ya terminada. De lo contrario, si el dinero y el tiempo es algo que desea utilizar a cambio de una fuente de alimentación portátil que funcione junto con la experiencia, entonces esta construcción es perfecta.
Las especificaciones de mi construcción:
- 4S (serie) 20P (paralelo) Banco de baterías de 16,8 V (93,6 vatios hora)
- 4S 40A BMS
- Inversor de 300 vatios
- 6 puertos de carga USB
- 1 tomacorriente de 120 V para EE. UU.
- Panel solar de 100 vatios
- Controlador de carga de 11 amperios
Este dispositivo puede cumplir con sus propias especificaciones de acuerdo con cómo desea construirlo y qué desea que incluya. Si desea una batería de mayor capacidad, o más salidas, una mayor potencia de salida (inversor más grande), etc., debe tener en cuenta la dimensión de esos objetos antes de comprar el estuche. El estuche que utilicé lo elegí por el precio, la disponibilidad y el sello a prueba de agua. Si tiene la intención de replicar todo exactamente, simplemente compre lo que se enumera a continuación.
No tengo ninguna afiliación con los sitios web que están vinculados, solo soy un consumidor de ellos. Tiendo a comparar precios en Internet por un tiempo antes de hacer compras y descubrí que estos son el mayor valor por la cantidad más pequeña en dólares en el momento en que los compré en comparación con lo que estaba disponible. Para obtener los precios más bajos para la mayoría de los artículos, recomendaría comprar directamente en China. El único inconveniente es que se espera que la entrega llegue en uno o dos meses en promedio. He hecho cientos de pedidos desde Aliexpress.com solo este año y recibí exactamente lo que esperaba a veces en tres semanas.
Materiales y costo
Baterías (80) 18650 celdas
Tiras de níquel.1,.12, O.15 de espesor
4S BMS
Alambre de silicona de calibre 14
El cable de silicona de calibre 26 debe tener dos colores diferentes
(2) Interruptores basculantes Solo necesita un interruptor si desea instalar un sensor / controlador de temperatura para controlar automáticamente los ventiladores.
Controlador de temperatura digital
Conectores XT60 (no soldados) O conectores XT60 (ya soldados)
Ventiladores (2) 12V DC
Indicador de bateria
Medidor digital
Cargador USB de seis puertos
Convertidor reductor de dinero
Estuche Si va con otro estuche, estos diseños no encajarán en él. Pelican tiene archivos que puede descargar para que el software CAD incorpore sus propios diseños de placa frontal.
Sellador de silicona
Panel solar, controlador de carga e inversor
1 KG de Filamento PETG o ABS
Surtido de tornillos M1-M5
Tubo retractil
Cinta VHB
Tubería retráctil de 300 mm
(16) Imanes de 10 X 3 mm
Super pegamento
Costo total $ 550 +/- incluido el panel solar, que la mayoría de los productos comerciales venden por separado y, dependiendo de la capacidad de la batería que compre, puede reducirse significativamente. También depende de la oferta y la demanda, por lo que los precios pueden cambiar.
Herramientas necesarias
Impresora 3D Soldador
Soldar
Pistola de calor o antorcha pequeña
Soldador por puntos de batería
Pelacables
Herramienta engarzadora de alambre con manguitos terminales
Pequeño Flathead
Llaves hexagonales de 2,5 mm, 3 mm, 4 mm
No se requiere Wowstick, pero es útil tenerlo si realiza muchos proyectos con tornillos pequeños.
Cargador de batería C4 18650
Multímetro digital
Taladro
Juego de brocas
Paso 1: banco de baterías
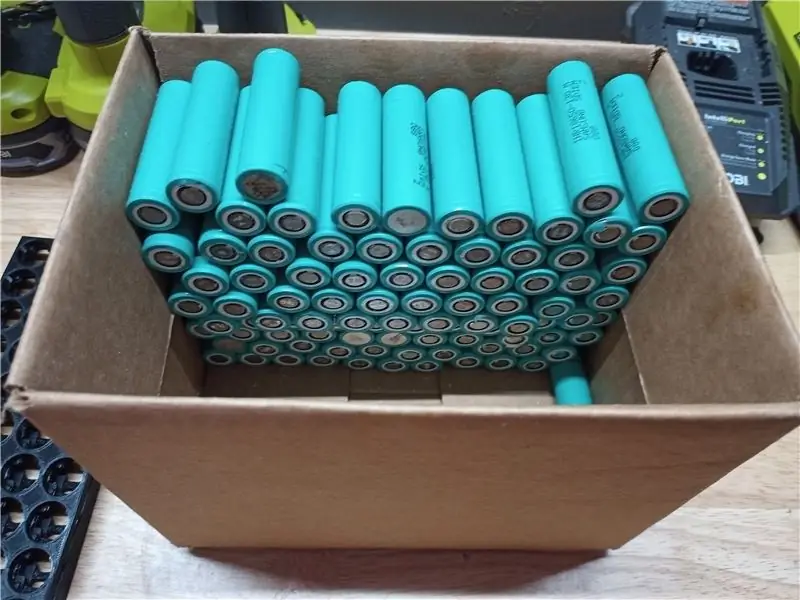
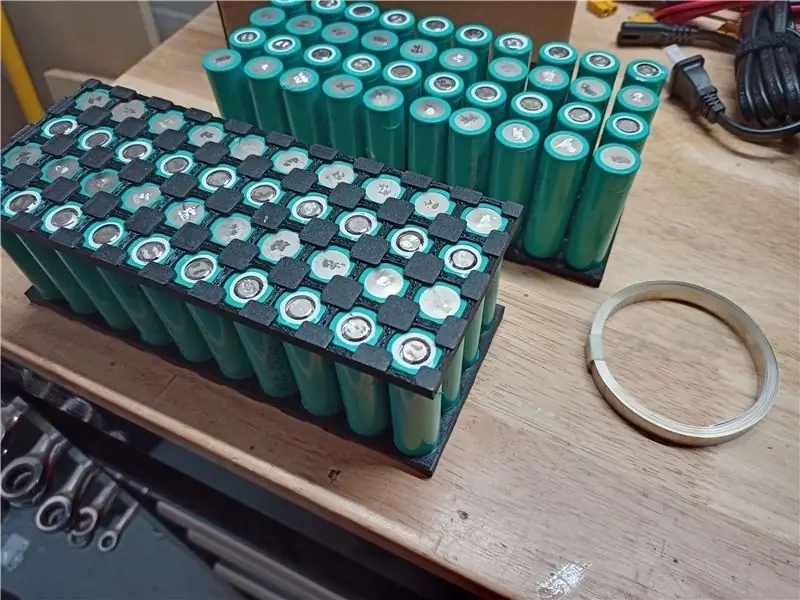
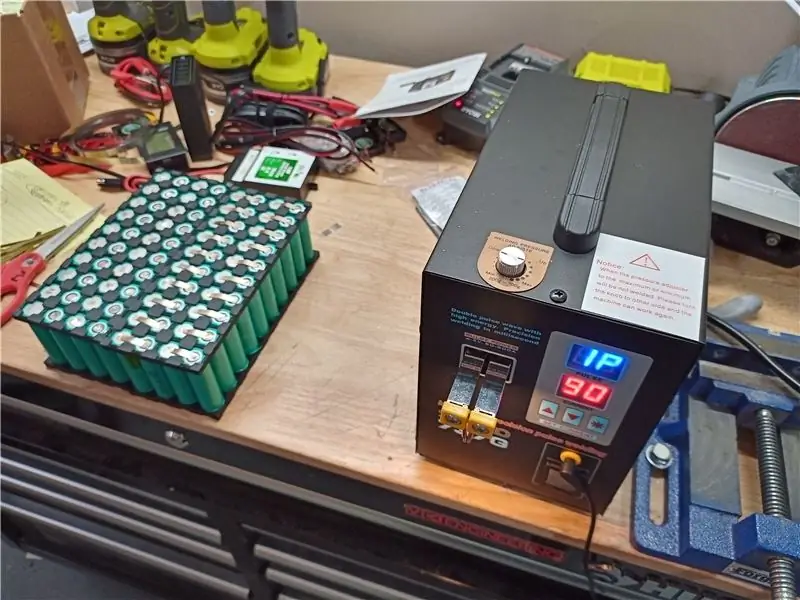
Este paso es realmente un proyecto completamente diferente en sí mismo. Compré baterías usadas que tenían cicatrices de soldadura por puntos anteriores, así que usé una herramienta giratoria y una pequeña rueda de corte para pulirlas. Una vez que se hayan limpiado ambos extremos en todas las celdas, se recomienda cargarlas con un cargador inteligente como el C4 que se enumera en la sección de herramientas.
Para obtener buenos tutoriales sobre cómo ensamblar sus propios bancos de baterías, así como sobre cómo conectar BMS, recomiendo Jehu Garcia y Ebike School Channels. Si ha realizado el ensamblaje del banco de baterías, tiene experiencia con baterías de soldadura por puntos y cableado BMS, probablemente pueda pasar a Impresión y ensamblaje.
Una vez que todas las celdas estén cargadas, pruebe el voltaje de cada celda. Todo lo que esté por debajo de los 3,6 voltios debe desecharse. En promedio, tenía celdas de alrededor de 4 voltios cada una. Los multímetros varían mucho en su apariencia. Tal vez consulte el manual para encontrar el icono, símbolo o letra exactos para la prueba de voltaje de CC. En mi medidor para verificar el voltaje, cambié el multímetro digital a una configuración de CC de 6 V y apliqué el negro al negativo y el rojo al positivo.
Para organizar las celdas, coloque las baterías en una de las placas 18650 4S 10P impresas. Sin embargo, una fila hasta el final debe tener el mismo extremo hacia arriba (positivo o negativo). La siguiente fila debe tener el extremo opuesto hacia arriba (positivo o negativo). Consulte las imágenes incluidas.
Después de que todas las celdas estén dispuestas y presione en la placa inferior. Coloque la otra placa encima de las baterías. Si parece un ajuste apretado, comience por un extremo y golpee ligeramente las baterías una o dos celdas a la vez y muévase gradualmente hacia el otro extremo del banco de baterías. Las dos placas deben sostenerlas todas en su lugar sin flexión.
ADVERTENCIA:
Tenga mucho cuidado y tómese su tiempo con este siguiente paso, puede causarle una descarga eléctrica y posiblemente provocar un cortocircuito en las baterías. Limpia cualquier material conductor cercano para que no coloques accidentalmente la batería encima haciendo una conexión eléctrica.
Si está satisfecho con su bloque de baterías, entonces es hora de soldar por puntos. Si usa la misma soldadora por puntos que yo, tendrá que obtener un grosor de.1-.15, esta soldadora no puede soldar más gruesa que esa. La ubicación de las tiras de níquel es importante. La forma más fácil de explicarlo es consultar las imágenes que he incluido para ver el diseño exacto. Corta y coloca las tiras de níquel sobre la batería. Sujete la batería contra el soldador con una buena cantidad de presión y vuélvala a tapar una vez, revísela, vuélvala a tapar una vez más y pase a la siguiente celda.
Finalmente, habrá terminado de soldar por puntos. Ahora es el momento de conectar el sistema de gestión de la batería (BMS). Un BMS monitorea y distribuye la corriente de manera uniforme entre todas las celdas conectadas. El cable más grueso (calibre 14-18) que es rojo y negro era para poder convertir 10P en un banco de baterías de 20P. Normalmente, esto se haría soldando por puntos más tiras en el mismo patrón, pero para encajar en este caso específico, necesitaba que los dos ladrillos estuvieran uno al lado del otro en lugar de un rectángulo largo.
Monte (pegamento caliente) el BMS en un material de tipo aislante como plástico duro, espuma o cartón. No lo monte directamente al costado de las baterías.
Los otros cables más delgados (calibre 28-30) están todos conectados a varios puntos del BMS. Usé los mismos códigos de color para el mismo punto en el BMS. El negro es 0 V, el amarillo es 4,2 V, el verde es 8,4 V, el rojo es 12,6 V y el rosado es 16,8 V. Cada número tiene dos cables porque necesita estar conectado a las primeras celdas y las últimas celdas en paralelo. Si hiciera un banco de baterías rectangular largo, sus cables comenzarían en el extremo del banco y los segundos cables se extenderían hasta el otro extremo del bloque. Usé un soldador en las tiras de níquel para no dañar la celda.
Terminar la batería es fácil. Suelde un cable rojo y uno negro de grosor (calibre 14) de aproximadamente 6 pulgadas de largo como mínimo, con un conector XT60 en el extremo. Esto va a los símbolos + y - en el BMS. Apliqué un poco de cinta kapton para evitar que el bloque se moviera. Deslice el banco de baterías en una envoltura retráctil de 300 mm, corte el exceso y aplique una pistola de calor o un soplete con cierta distancia. El banco de baterías ahora está completo.
Paso 2: Impresión y montaje
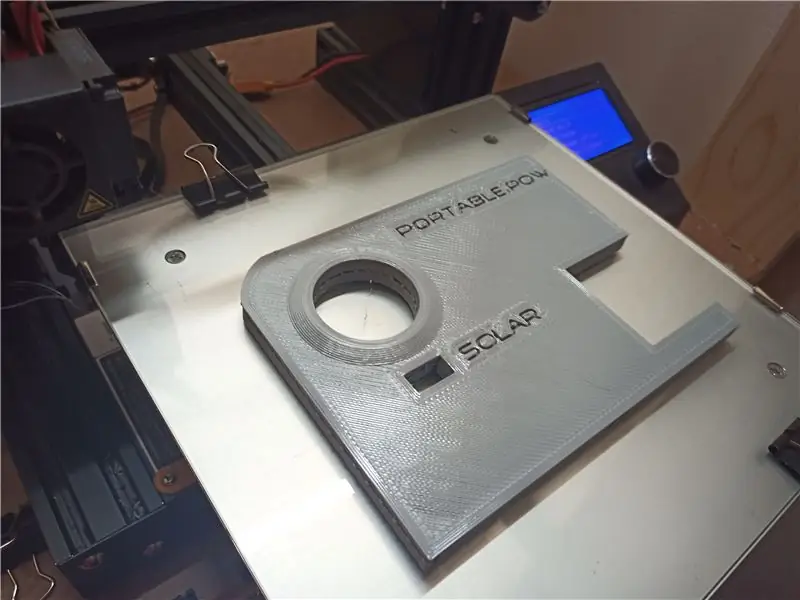
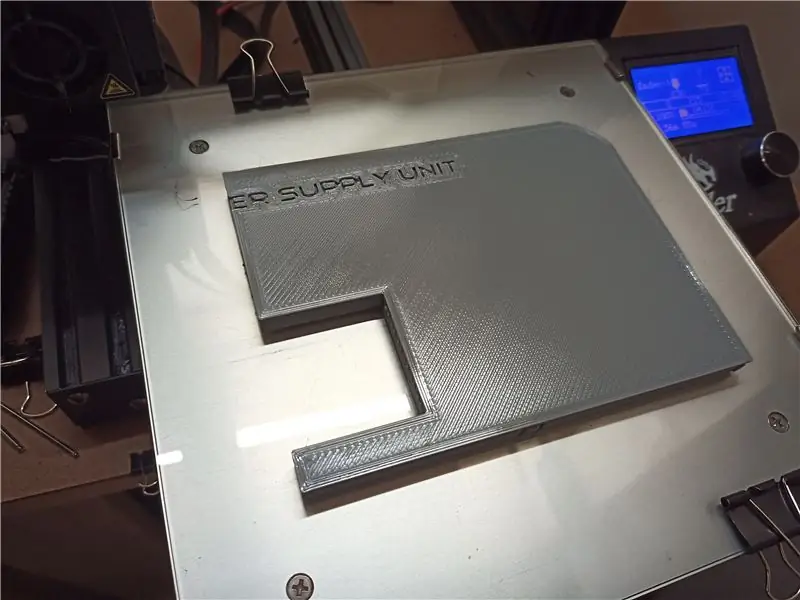
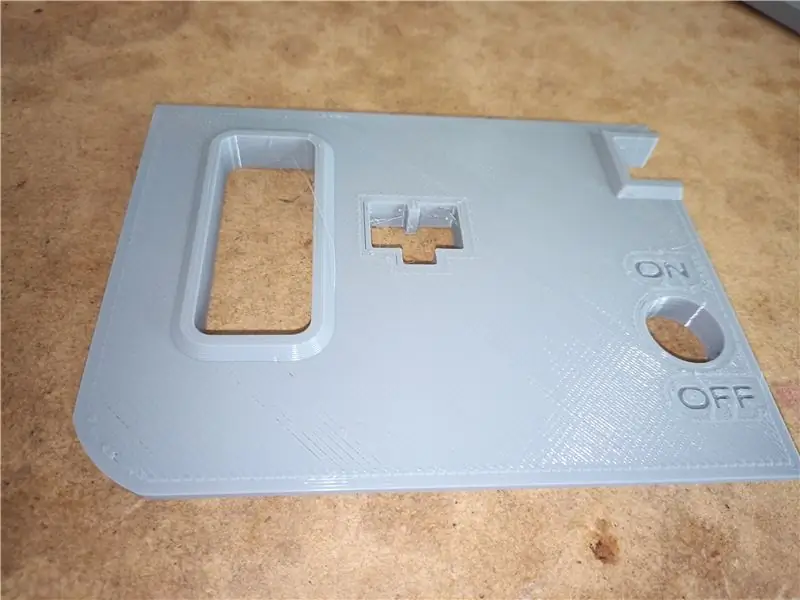
Si es completamente nuevo en la impresión 3D, le sugiero que lea a continuación, de lo contrario, puede pasar a la sección de configuración de impresión.
Tengo dos Ender 3. Ambos son de muy buena calidad por su precio y pueden manejar PLA, ABS y PETG. La adhesión a la cama suele ser el mayor problema a pesar de dominar la nivelación de la cama. Lo que eliminó ese problema para mí fue tirar las camas originales y reemplazarlas con vidrio templado. Por supuesto, tuve que nivelarlo de nuevo pero solo una vez. Antes de cada impresión, la limpio con un 70% de alcohol isopropílico. Deje que su impresora se precaliente completamente. Mantenga la impresora y el filamento en un lugar seco. Más humedad significa más problemas. Es probable que las perlas no se laminen correctamente, lo que provocará una fácil separación entre dos capas en el medio de una pieza terminada.
Si aún no tiene una impresora 3D y está considerando obtener una Ender 3, siga de cerca este tutorial de construcción. Seguí todos los pasos en ambas impresoras que ensamblé y salí perfecto en el primer intento. Yo uso Cura para la cortadora. Se incluyen muchas opciones de configuración y además es de uso gratuito.
Configuración de impresión
Este enlace es para los archivos STL
Se recomienda ABS o PETG. Cuanto mayor sea el porcentaje de relleno, mejor. Elegí el 25% para las cuatro placas frontales. Usé boquilla 0.8 en calidad de borrador y obtuve un producto de aspecto decente en un promedio de cinco horas por pieza. Estos necesitan soportes y estar orientados con letras mirando al cielo.
Los componentes interiores se imprimieron con una boquilla de 0,6 con calidad estándar.
(1) Soporte plano 100% relleno
(4) Pajaritas 100% relleno
(2) Barras magnéticas 75% - 100%
(1) Soporte del controlador de carga 75% - 100%
(1) Soporte de montaje del convertidor Buck 50% de relleno. Hay dos versiones. Solo necesita dos pernos para montarlo en la carcasa, así que diseñé un orificio de 2 y otro de 4. Pero solo hace falta imprimir uno u otro.
18650 Batería 4S 10P Placas 100% de relleno con boquilla 0.4 en calidad estándar. Hice esto con PLA ya que será envuelto y luego encerrado nuevamente en un estuche. Dependiendo de cuántas baterías pretenda usar (40 celdas = 2 placas 4S 10P en total necesarias) (80 celdas = 4 placas 4S 10P en total necesarias)
Ensamblar estos juntos es básicamente como bloques de lego. Las pajaritas son para ayudar a mantener los platos juntos, pero no son necesarios. Lo que mejor asegura todo junto son las barras magnéticas, así como la presión del ajuste apretado de la caja. Al insertar imanes en las piezas, tenía una pila en la mano, apliqué un poco de superpegamento en la pieza y presioné un imán con la pila encima de ella. Esto fue para que la polaridad sea inversa y los imanes se peguen accidentalmente de manera incorrecta.
Una vez que una barra magnética tenía cuatro imanes pegados y presionados hasta el fondo, la dejé secar durante algunas horas. Le di a cada uno de los cuatro imanes un segundo imán para permanecer conectado a él. De esta manera, la polaridad ya es correcta para cuando las placas frontales están pegadas y presionadas sobre esos imanes.
Paso 3: Montaje y cableado
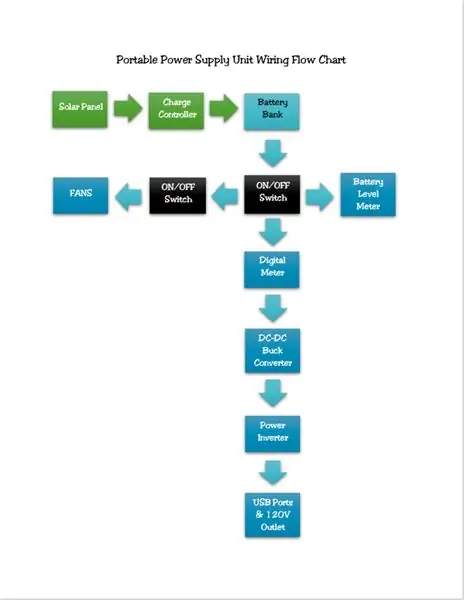
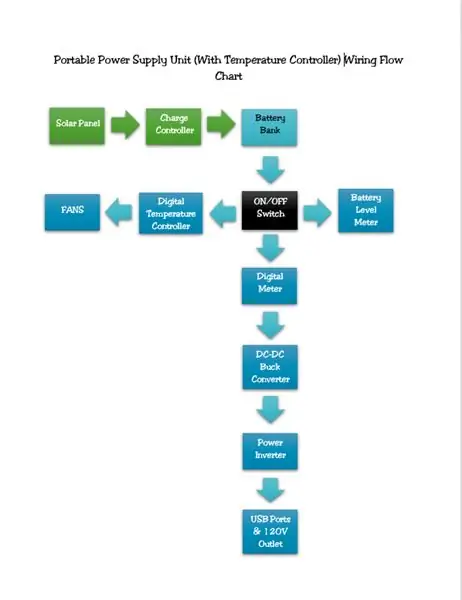
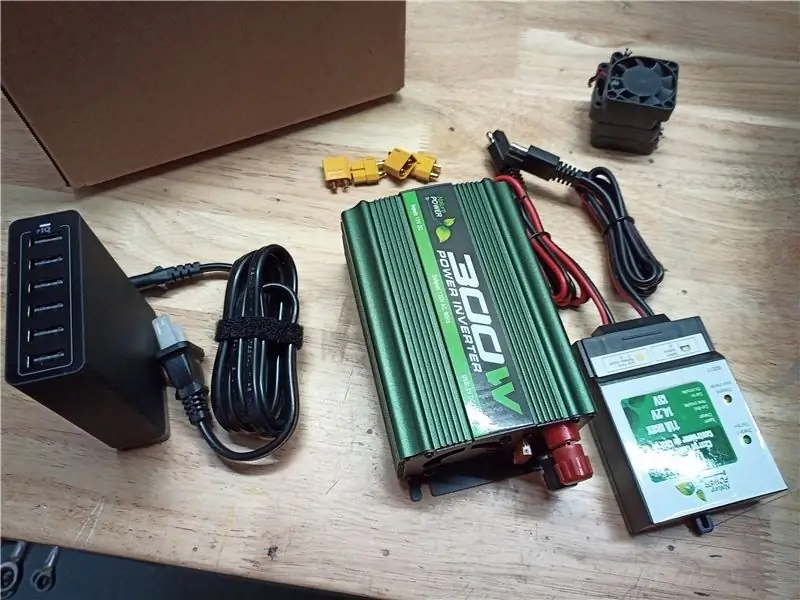
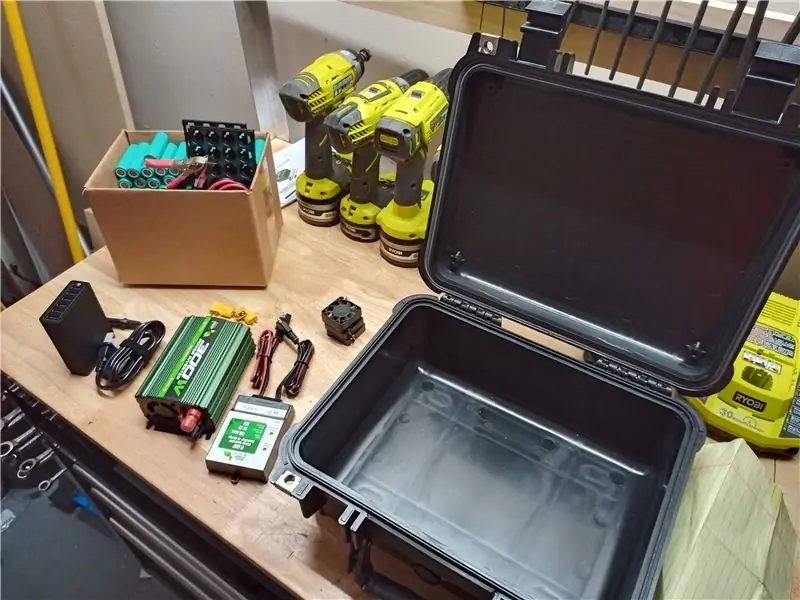
Consulte los diagramas de flujo incluidos para saber cómo conecté las cosas.
Conectar todo junto no es muy complicado, así es como parece. Para la mayoría de los componentes, solo involucran cables positivos y negativos. Los interruptores es donde se vuelve un poco complicado. Si tiene la intención de tener un control automático del ventilador mediante un controlador / sensor de temperatura digital, todo lo que necesita es un interruptor basculante para encender y apagar el dispositivo. Si desea otras utilidades, como una barra de luz LED o algo así, en ese caso es probable que desee utilizar un segundo interruptor.
Antes de soldar algo, recuerde colocar primero los medidores e interruptores en las placas frontales impresas. De lo contrario, tendrás que hacerlo dos veces. Aprendí esto de la manera difícil. Al montar los ventiladores, lo ideal es que desee que el aire circule hacia adentro y el otro hacia afuera. El inversor también tiene un ventilador que expulsa el aire por la parte posterior.
Para el inversor, lo desarmé temporalmente en la placa de circuito. No necesita hacer mucho, pero para extender el alcance de la toma de 120V tendrá que realizar un desmontaje. No haga esto mientras esté enchufado a algo. Cuatro tornillos en la placa inferior exponen todo. Es necesario aflojar cuatro tornillos más en la placa frontal (con las salidas). Saque los tapones de salida de la placa frontal. La placa no se podía quitar a menos que se cortaran los cables o se cortara la placa frontal. Probablemente pueda simplemente cortar los cables porque el siguiente paso consiste en cortarlos de todos modos para extender el alcance.
Elegí una ruta diferente y corté pequeñas muescas en la placa con cuidado usando una herramienta giratoria. Luego tomé unos alicates y los doblé para poder deslizar los enchufes de salida. Luego me di cuenta de que necesitaba unir y soldar unos quince centímetros de cable. Solo tiene un total de tres cables para extender. Sugiero que se corten, empalmen, suelden y encojan un cable a la vez. Esto permite que la extensión del enchufe de salida alcance la placa frontal de la carcasa. Una vez realizada la modificación, deberá volver a colocar el panel inferior en el inversor y preparar los soportes de montaje.
Usé una barra de ángulo de extrusión de aluminio. Posición marcada para agujeros, perforados y cortó la pieza de la barra. He diseñado los soportes para que puedan imprimirse en 3D y hacer tu vida un poco más fácil. Consulte las imágenes para ver cómo las monté en la carcasa. Antes de perforar cualquier agujero, asegúrese de estar satisfecho con su diseño y de que la batería no se deslice demasiado. Empujé mi banco de baterías hasta la esquina derecha de la caja, el inversor justo al lado, y luego taladré los agujeros. Cuando perfora los orificios, el soporte de montaje del convertidor reductor debe montarse primero porque no hay suficiente espacio para perforar los orificios con el inversor montado en el camino.
Solo taladro agujeros a través de la carcasa para estos dos soportes y dos agujeros para el soporte de montaje designado para el convertidor reductor CC-CC. Antes de colocar un tornillo / perno a través de dicho orificio, aplicaría sellador de silicona en el interior y el exterior para mantenerlo a prueba de agua. También usé arandelas en ambos extremos de los pernos. Diseñé las barras magnéticas para que también pudieran fijarse a la carcasa mediante pernos.
En mi PPSU, utilicé cinta VHB para pegar el controlador de carga en el costado de la carcasa. Mientras creaba este instructivo, me tomé el tiempo para crear un soporte que puede imprimir en 3D y perforar agujeros para atornillar si lo desea. La única otra área en la que usé una pequeña cantidad de cinta VHB fue entre el soporte plano y el enchufe solar para evitar que se deslice al enchufarlo al conector del panel solar.
Espero que esto haya sido inspirador, informativo o algo divertido para ti. Gracias por ver mi proyecto.
Recomendado:
Una fuente de alimentación de banco de Sleak desde la fuente de alimentación de la PC: 8 pasos (con imágenes)
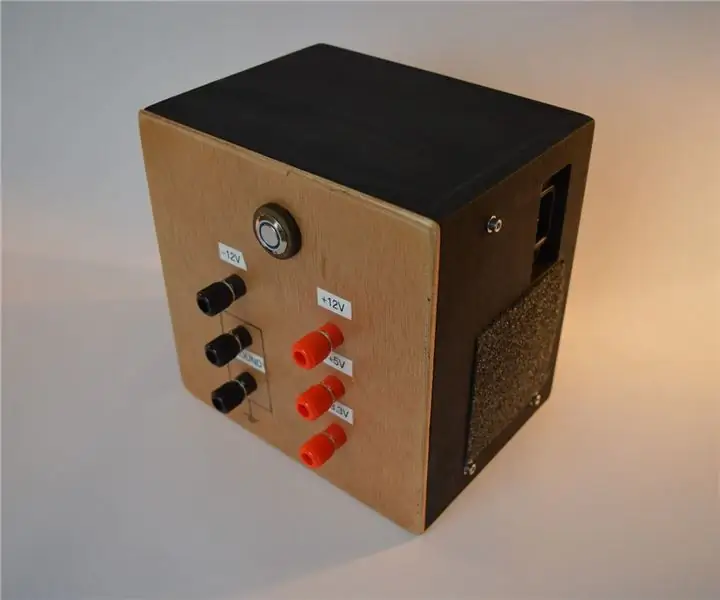
Una fuente de alimentación de banco de Sleak desde la fuente de alimentación de la PC: Actualización: la razón por la que no he tenido que usar una resistencia para detener el apagado automático de la fuente de alimentación es que (creo que …) el led en el interruptor que usé consume suficiente corriente para evitar el PSU apagándose, así que necesitaba una fuente de alimentación de sobremesa y decidí hacer una
Fuente de alimentación ATX encubierta a fuente de alimentación de banco: 7 pasos (con imágenes)
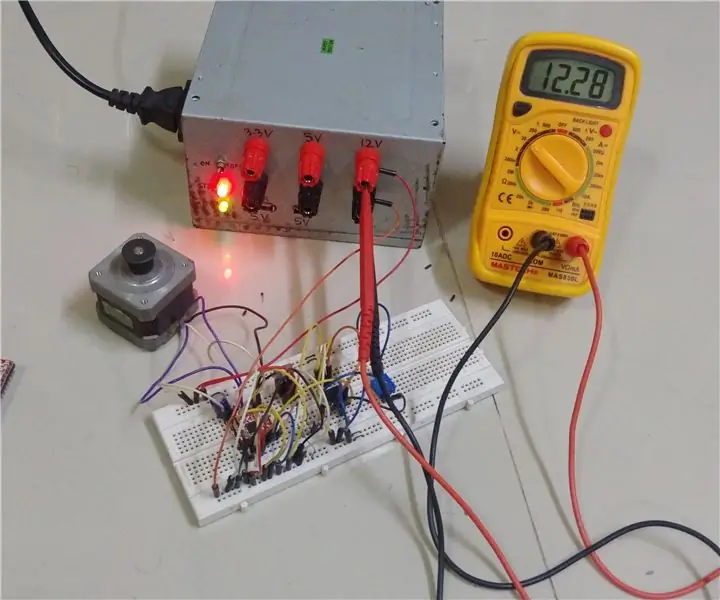
Fuente de alimentación ATX encubierta para fuente de alimentación de banco: una fuente de alimentación de banco es necesaria cuando se trabaja con electrónica, pero una fuente de alimentación de laboratorio disponible comercialmente puede ser muy costosa para cualquier principiante que quiera explorar y aprender electrónica. Pero existe una alternativa barata y confiable. Por conve
Fuente de alimentación de 220V a 24V 15A - Fuente de alimentación conmutada - IR2153: 8 pasos
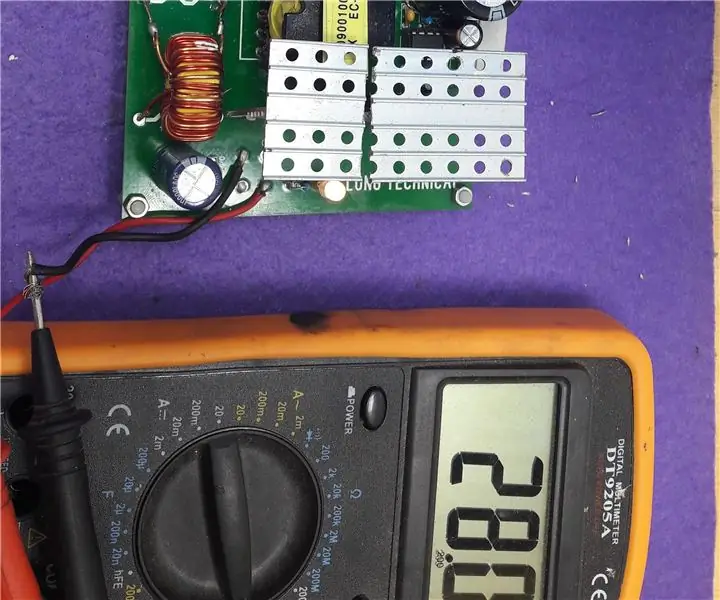
Fuente de alimentación de 220V a 24V 15A | Fuente de alimentación conmutada | IR2153: Hola, hoy hacemos una fuente de alimentación de 220 V a 24 V y 15 A | Fuente de alimentación conmutada | IR2153 de la fuente de alimentación ATX
Cómo hacer una fuente de alimentación de banco ajustable con una fuente de alimentación de PC antigua: 6 pasos (con imágenes)
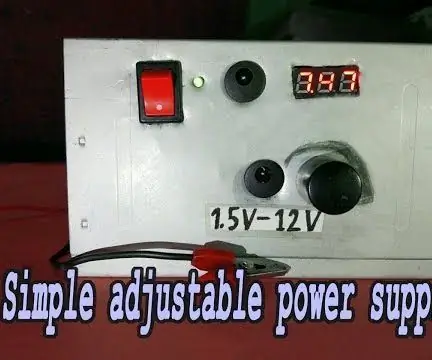
Cómo hacer una fuente de alimentación de banco ajustable con una fuente de alimentación de PC vieja: Tengo una fuente de alimentación de PC vieja por ahí, así que he decidido hacer una fuente de alimentación de banco ajustable con ella. Necesitamos un rango diferente de voltajes para alimentar o Verifique diferentes circuitos eléctricos o proyectos. Por lo tanto, siempre es bueno tener un
¡Convierta una fuente de alimentación ATX en una fuente de alimentación de CC normal !: 9 pasos (con imágenes)
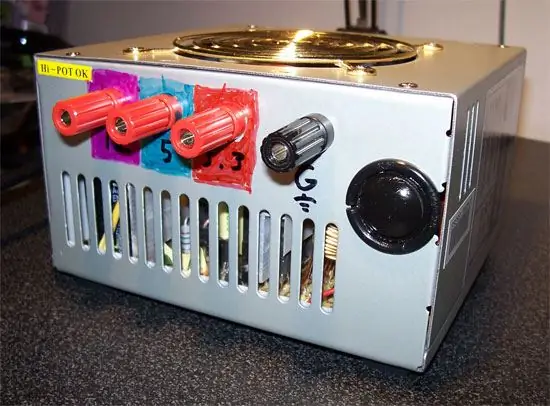
¡Convierta una fuente de alimentación ATX en una fuente de alimentación de CC normal !: Una fuente de alimentación de CC puede ser difícil de encontrar y costosa. Con características que son más o menos impredecibles para lo que necesita. En este Instructable, le mostraré cómo convertir una fuente de alimentación de computadora en una fuente de alimentación de CC normal con 12, 5 y 3.3 v