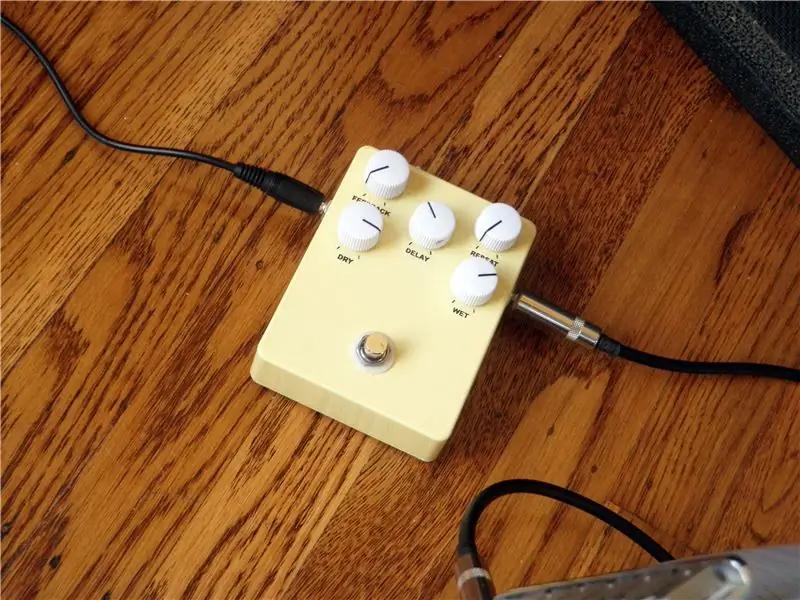
Tabla de contenido:
- Paso 1: Ve a buscar cosas
- Paso 2: el esquema
- Paso 3: Breadboard the Circuit
- Paso 4: suelde el circuito
- Paso 5: haz soportes de goma
- Paso 6: Stencil el frente
- Paso 7: pintar
- Paso 8: taladro
- Paso 9: pelar
- Paso 10: Perfora un poco más
- Paso 11: grabar de nuevo
- Paso 12: revestimiento de corcho
- Paso 13: potenciómetros e interruptores
- Paso 14: Cablee el panel frontal
- Paso 15: Conecte la energía
- Paso 16: conecte el panel frontal
- Paso 17: Cablee todo lo demás
- Paso 18: Toques finales
- Paso 19: Plug and Play
2025 Autor: John Day | [email protected]. Última modificación: 2025-01-23 14:39
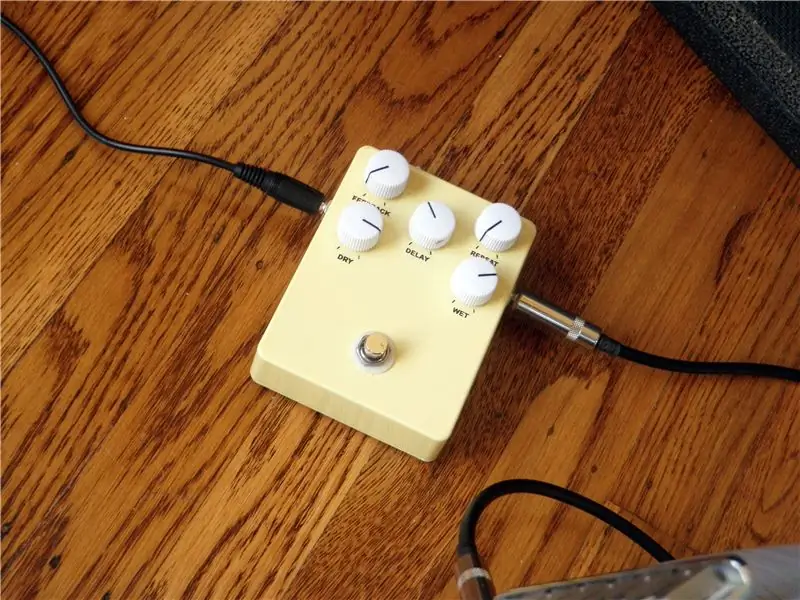
Construir pedales de guitarra es un proceso costoso, a menudo frustrante y que requiere mucho tiempo. Si cree que va a ahorrar tiempo y dinero haciendo su propio pedal de retardo digital, le recomiendo que lea R. G. Página de Keen sobre la economía de la construcción de pedales. Sin embargo, si como yo, eres obsesivo, disfrutas jugando con la electrónica y quieres hacer algo que se vea y suene exclusivamente tuyo, continúa leyendo … ¡pero no digas que no te lo advertí!
A continuación se muestran instrucciones detalladas sobre cómo hice mi propio pedal de retardo digital. Debo admitir que utilicé una cortadora láser como parte integral del proceso, pero siento que la mayoría de las tareas para las que la estoy usando se pueden realizar con muchas herramientas más modestas. Mi enfoque del Instructable no está tanto en el montaje del circuito, sino en el montaje de la carcasa, ya que aquí es donde radica el verdadero meollo del problema. Atornillar muchas cosas en un pequeño recinto no es particularmente fácil. Sin embargo, espero que estas instrucciones ayuden de alguna manera a simplificar el proceso.
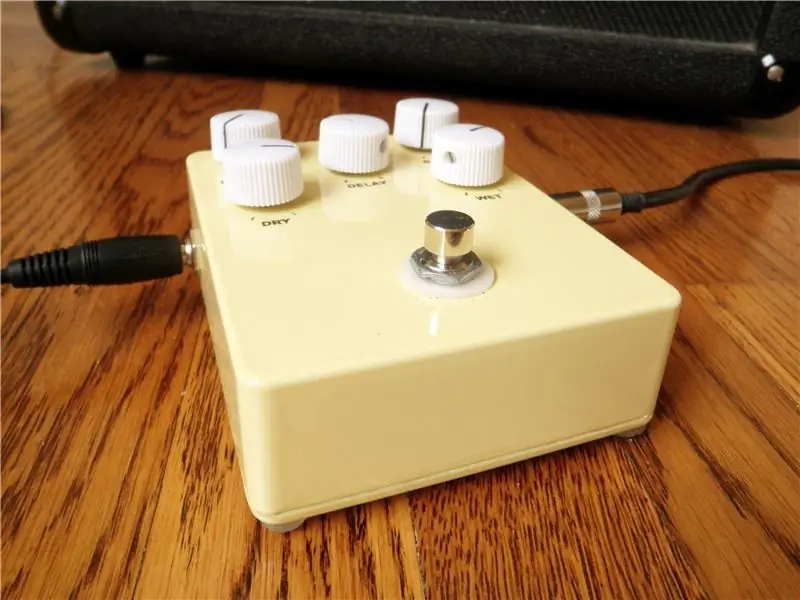
Retraso corto:
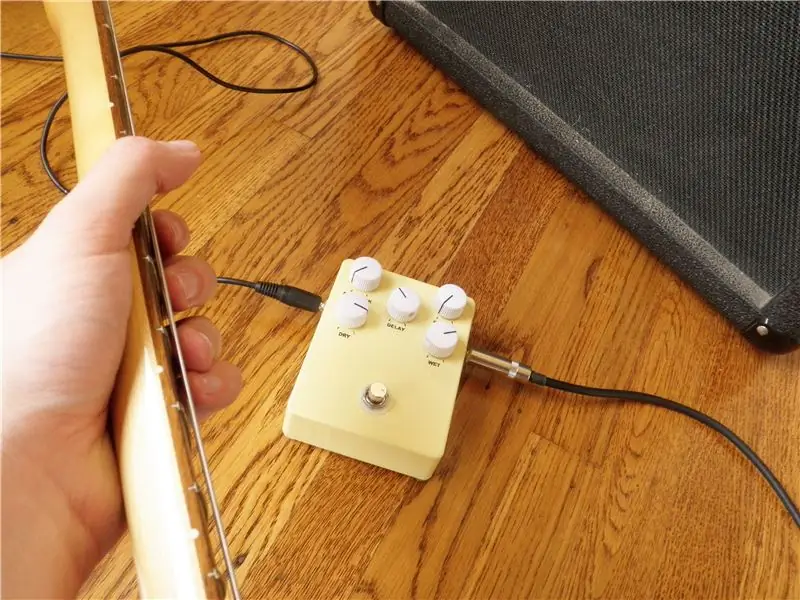
Retraso prolongado sin comentarios:
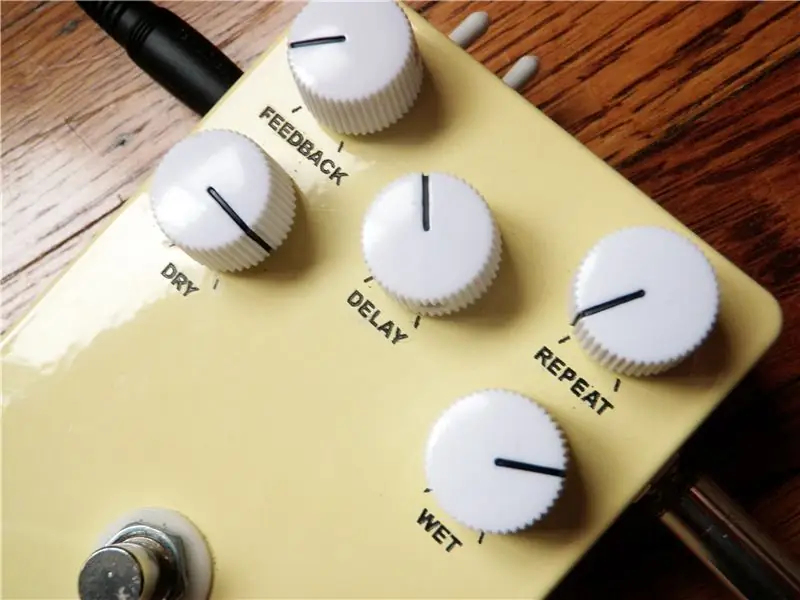
Retraso prolongado con retroalimentación:
Paso 1: Ve a buscar cosas
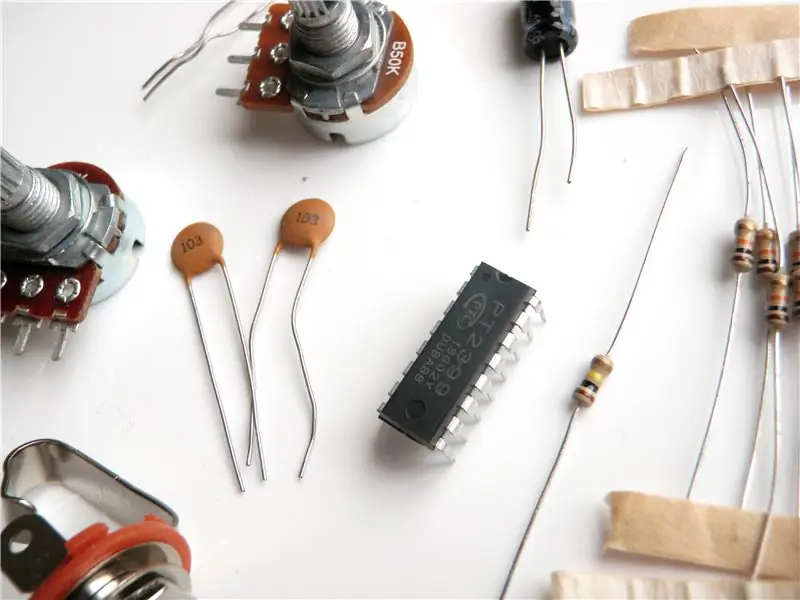
Necesitará:
(x1) Caja de acero tamaño "BB" (x1) Procesador de eco PT2399 (x1) Amplificador operacional de bajo ruido TL072 (x1) LM7805 (x3) Potenciómetros de 100K (x1) Potenciómetro de 50K (x1) Potenciómetro de 5K (x1) PCB (x1) Interruptor de pedal DPDT (x1) Interruptor de palanca SPST (SPDT correcto) (x1) Toma de corriente (con corte) (x2) Tomas mono de 1/4 "(x5) Perillas (x1) lámina de caucho santopreno de 1/16" (McMaster- Carr 86215K22) (x1) hoja de corcho de 1/8"
condensadores: (x1) 100uF (x3) 47uF (x1) 4.7 uF (x6) 1 uF (x3) 0.1 uF (x2) 0.082 uF (x3) 0.0027 uF (x2) 0.01 uF (x1) 100 pF (x1) 5 pF
resistencias: (x2) 1K (x11) 10K (x2) 15K (x1) 100K (x1) 510K (x2) 1M
(Tenga en cuenta que algunos de los enlaces en esta página son enlaces de afiliados. Esto no cambia el costo del artículo para usted. Reinvierto los ingresos que recibo en la realización de nuevos proyectos. Si desea alguna sugerencia de proveedores alternativos, permítame saber.)
Paso 2: el esquema
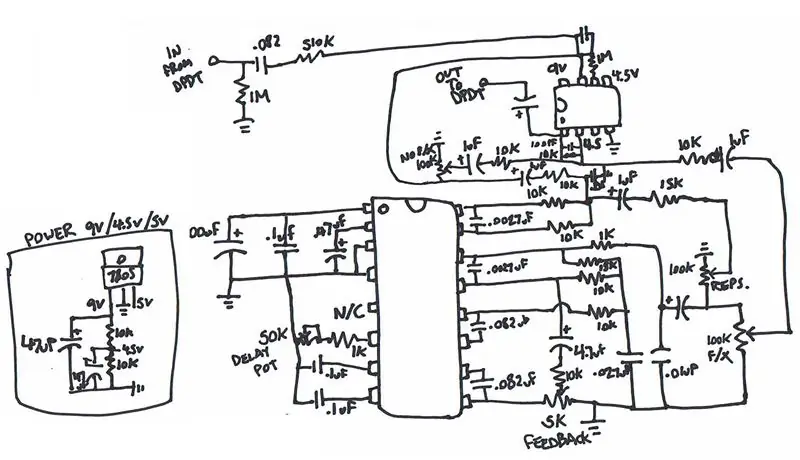
Mi esquema se basa en gran parte (léase: casi en su totalidad) en el pedal EchoBender de Casper Electronics, que a su vez se basa en gran medida en el pedal Rebote 2.5 Delay de Tonepad, que a su vez, más o menos, se basa en el esquema de ejemplo en la hoja de datos PT2399. Al tener los tres en la placa de pruebas, personalmente no puedo escuchar una diferencia significativa en el sonido entre la versión de Casper Electronic y la del Tonepad, que algunas personas dicen que tiene un sonido superior (el de la hoja de datos simplemente suena plano). Lo bueno de la versión de Casper Electronics es la inclusión de un potenciómetro de retroalimentación, que le da un sonido realmente completo al efecto de eco.
Las cosas que he cambiado son algunos valores de resistencia y condensador levemente significativos. La mayor diferencia es que he eliminado el potenciómetro de distorsión de "retardo largo". Este potenciómetro básicamente está obligando al chip a submuestrear la entrada para crear un retraso más largo y, en mi opinión, no suena muy bien. Si le gusta el audio submuestreado y con retardo largo, por supuesto, agregue un potenciómetro grande (1M) en serie con el potenciómetro de retardo. Como también puede haber inferido de esto, cuanto mayor sea el retardo, menos clara será la señal de salida; así que tenga en cuenta que incluso el "retraso corto" comienza a degradarse cuando se pone en marcha por completo.
En aras de la redundancia, he vuelto a dibujar el esquema. He puesto tres notas de imagen en mi esquema para indicar las partes del circuito que han cambiado. El esquema dibujado por Casper Electronics es mucho más claro y te recomiendo que vayas principalmente por ese.
Paso 3: Breadboard the Circuit
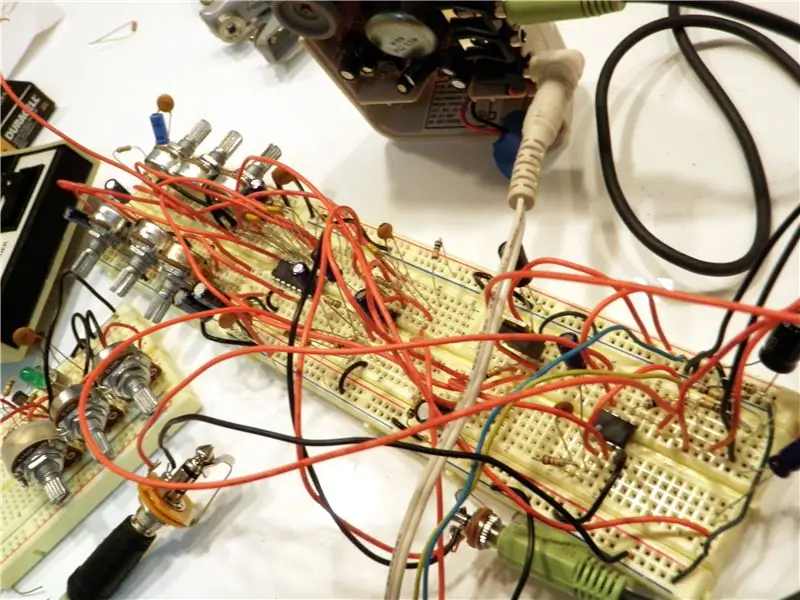
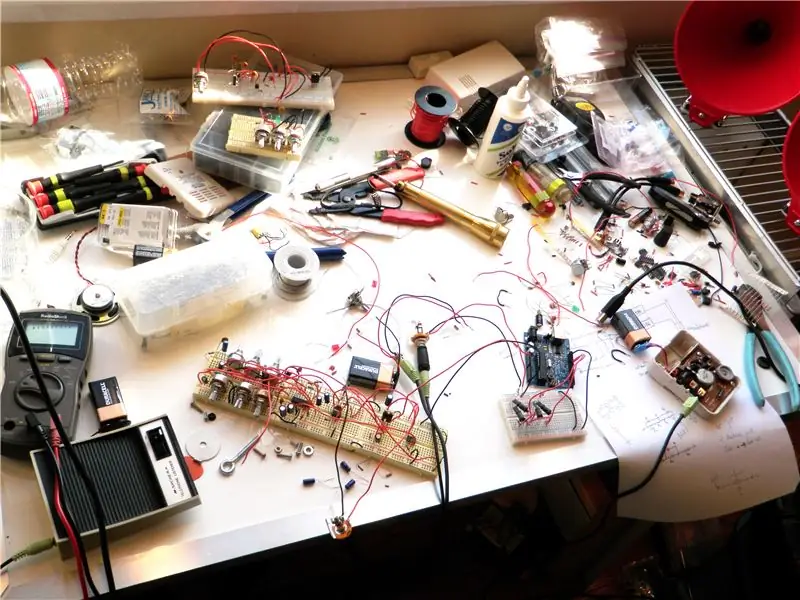
Construye el circuito en una placa de pruebas.
¿Por qué protoboard?
Hay un par de razones: 1) Para asegurarse de hacerlo bien en primer lugar. No hay nada peor que soldar un circuito de forma permanente para descubrir que no funciona. 2) Este método permite la experimentación. Por ejemplo, si no le gusta cómo suena, puede cambiar partes fácilmente hasta que lo haga. 3) Puede ampliar fácilmente el circuito. 4) También es rápido de hacer y si descubre que no le gusta el circuito en absoluto, no solo perdió mucho tiempo soldando. 5) Le da una referencia para seguir cuando finalmente decida soldarlo permanentemente.
Paso 4: suelde el circuito
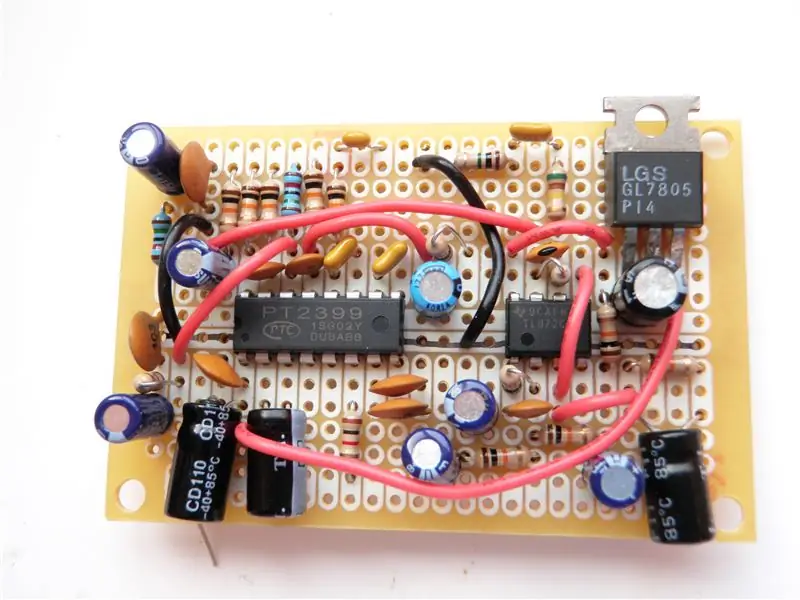
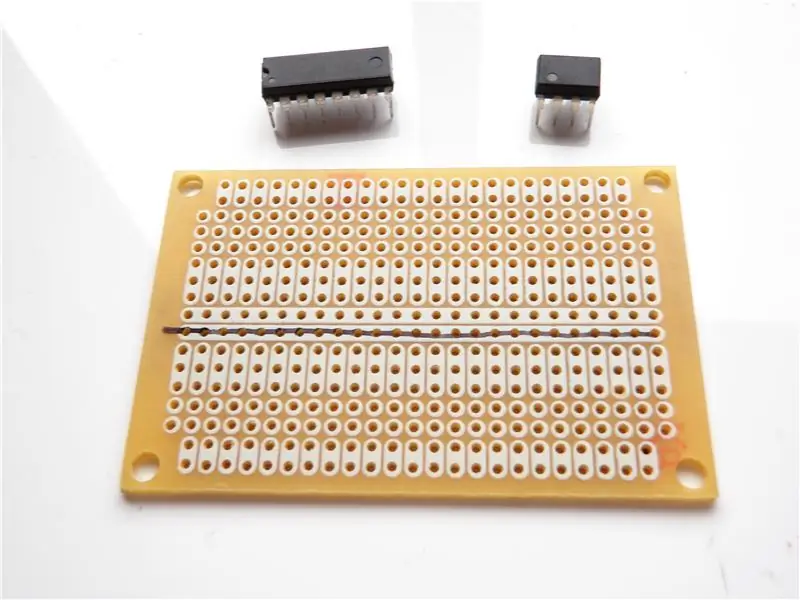
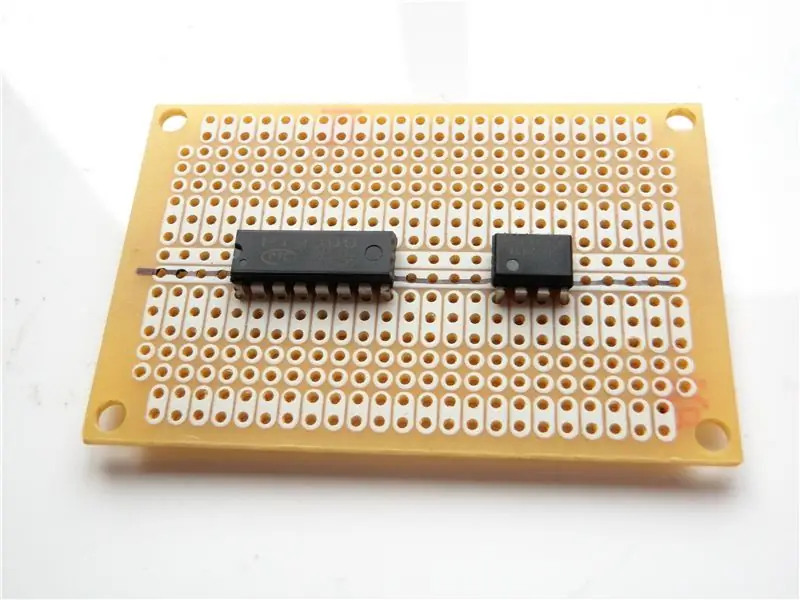
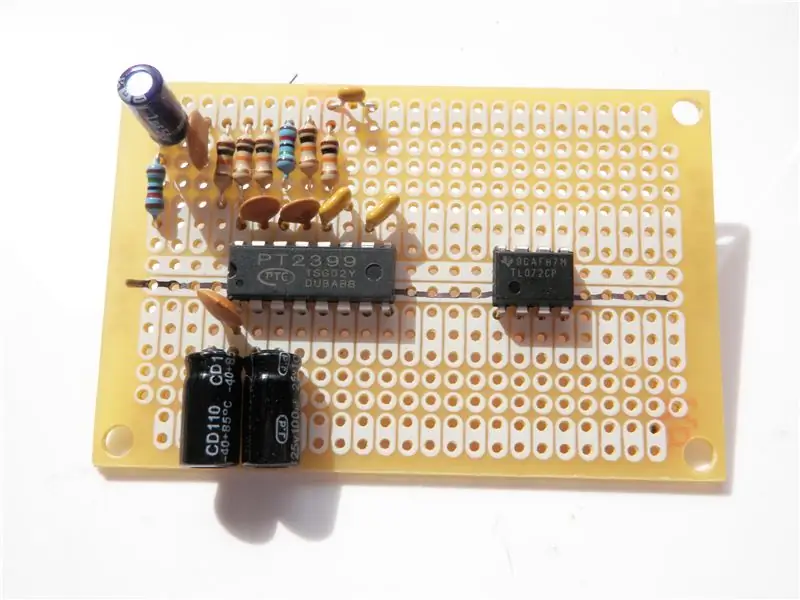
Una vez que esté seguro de que el circuito funciona en la placa de prueba, suelde todo, excepto los conectores, potenciómetros e interruptores, a una placa de circuito impreso. Preste mucha atención a sus conexiones.
Si tiene suficientes piezas para hacerlo, se recomienda que deje la placa de pruebas intacta como punto de referencia. Es aconsejable desmontar la placa de pruebas solo después de estar absolutamente seguro de que el circuito soldado funciona.
Paso 5: haz soportes de goma
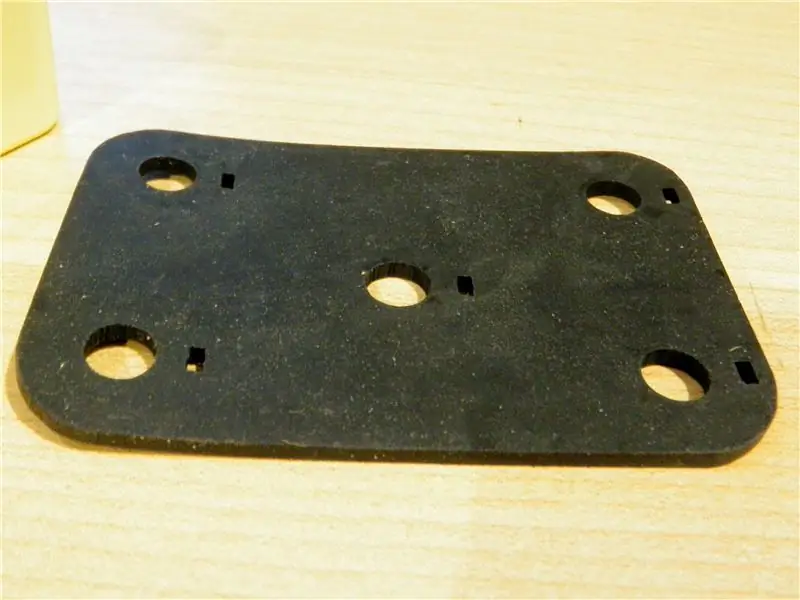

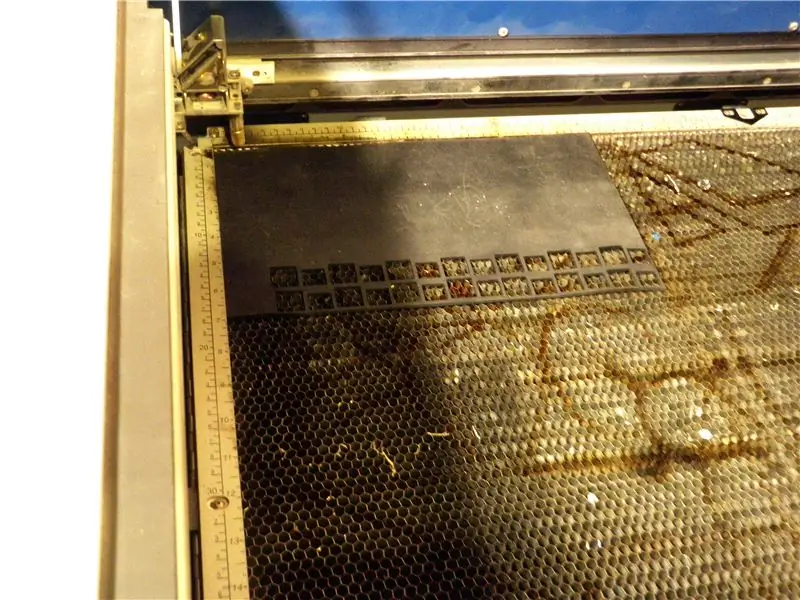
Usando los archivos adjuntos, corte los patrones de soporte en una hoja de goma de 0.2 . Usé un cortador láser, pero probablemente pueda obtener los mismos resultados con un cuchillo afilado y un trazo cuidadoso.
Estas dos piezas irán entre los potenciómetros y la caja, y los interruptores y la caja. Funcionarán para evitar que el cuerpo de los potenciómetros e interruptores giren.
Paso 6: Stencil el frente
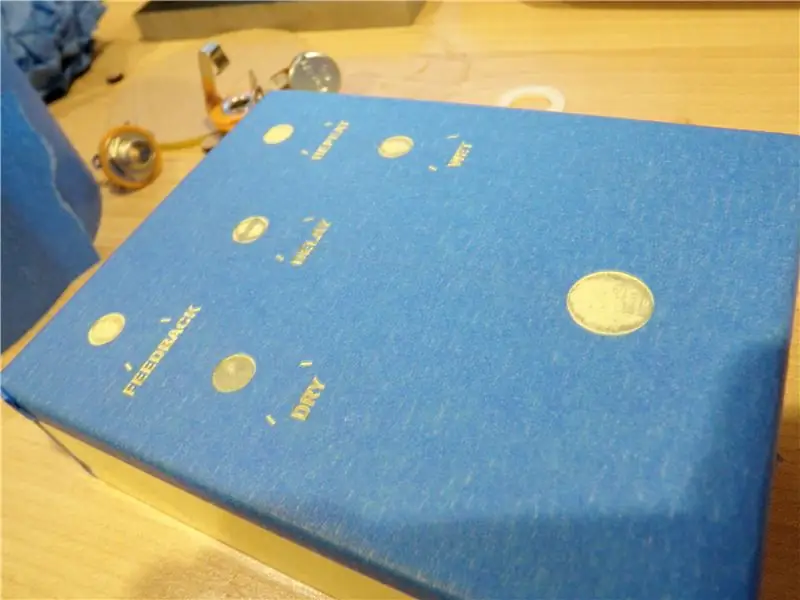
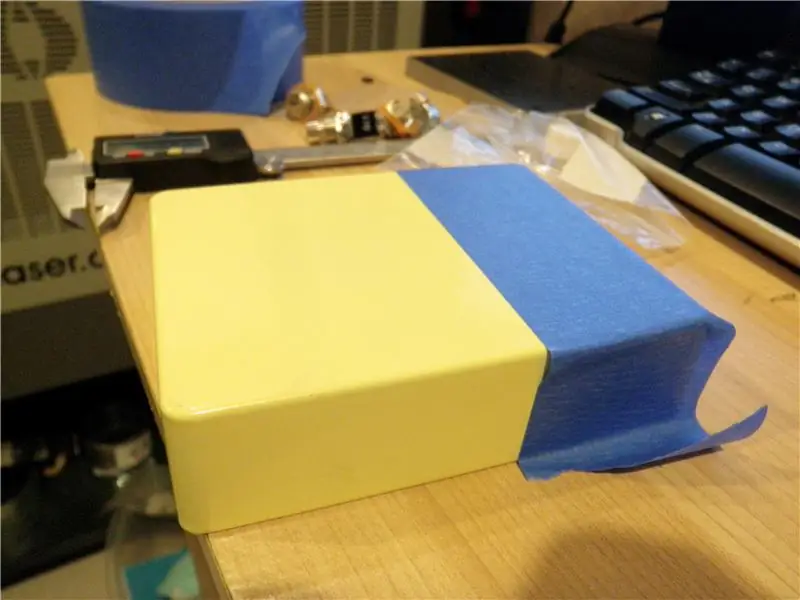
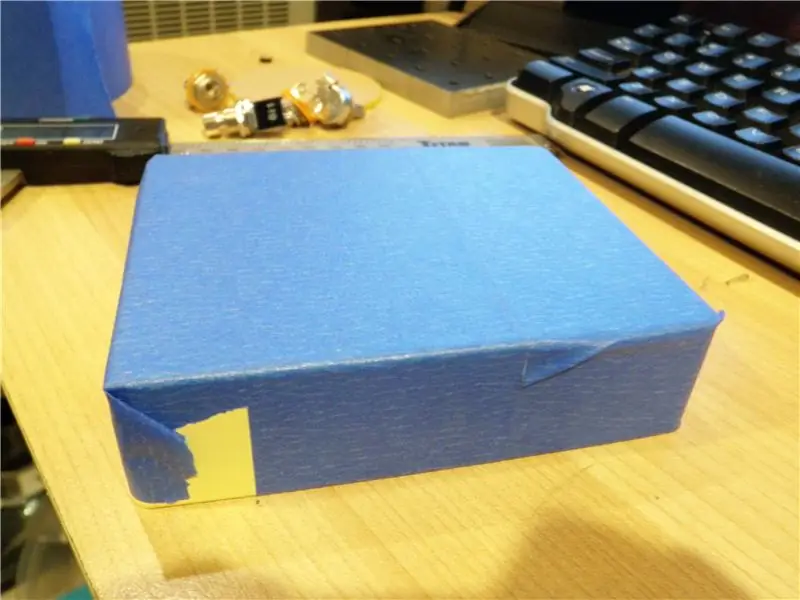
Descargue el archivo adjunto, ponga a cero su recinto en el cortador láser y aplique la plantilla a la imagen en el frente de la caja. Haz un pase fuerte o dos pases medios. Desea grabar hasta que pueda comenzar a ver el metal del recinto.
Si no tiene un cortador láser, imprima el archivo en papel adhesivo, péguelo a su caja y recórtelo con un cuchillo Exacto
Paso 7: pintar
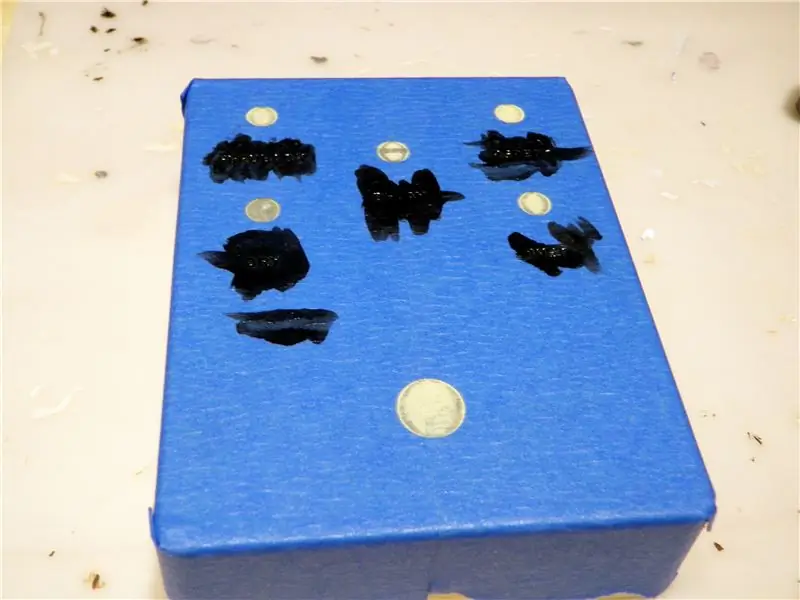
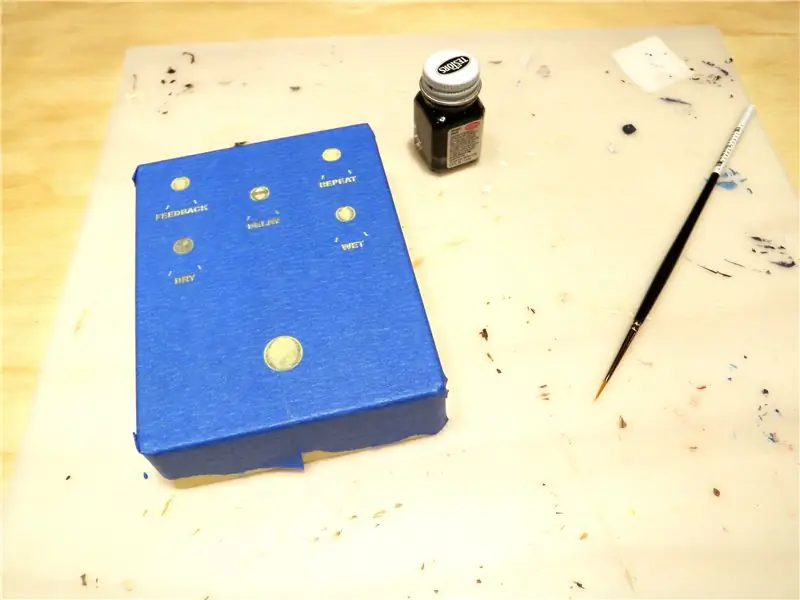
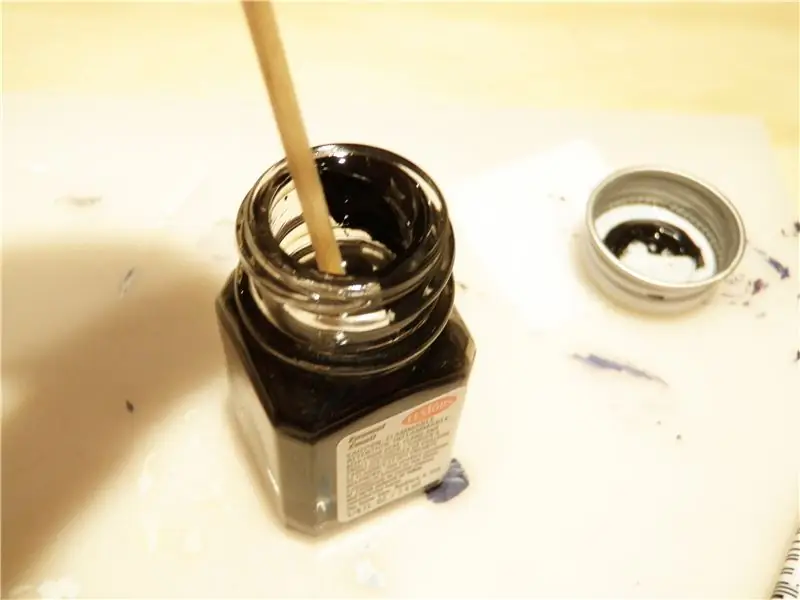
Revuelve bien tu esmalte negro (ya que tiende a separarse) y luego aplica una capa a cada una de las palabras grabadas en la parte superior de la caja. Espere a que se seque y aplique una segunda capa. Luego, espere a que se seque una vez más y continúe.
Consejo: para evitar que el cepillo se seque entre capas, puedes dejarlo completamente sumergido en el esmalte.
Paso 8: taladro
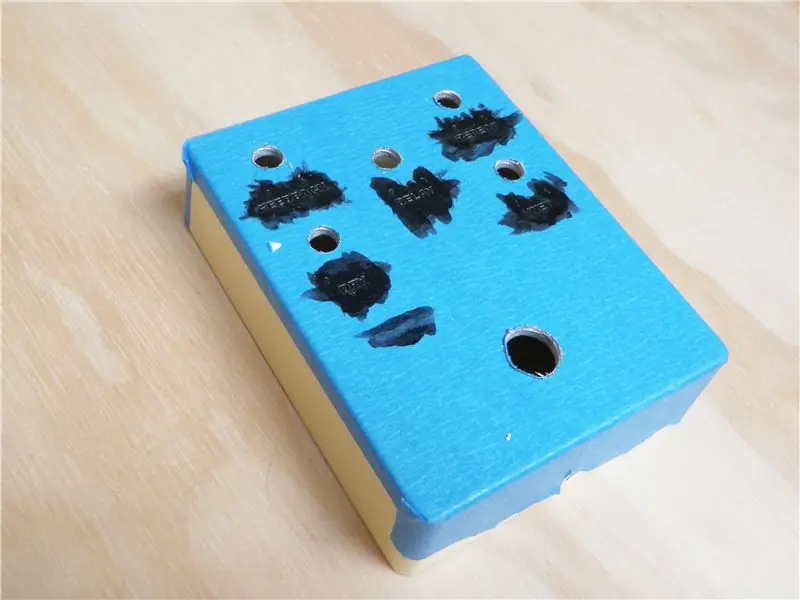
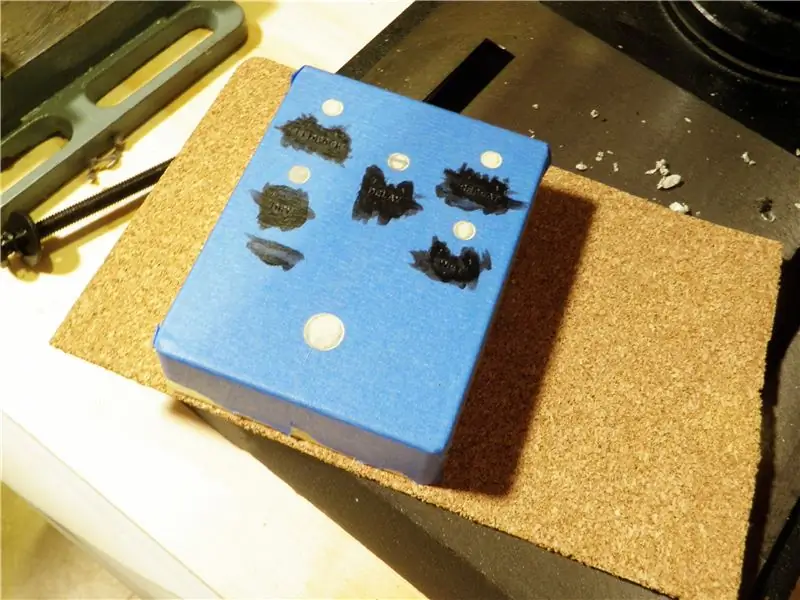
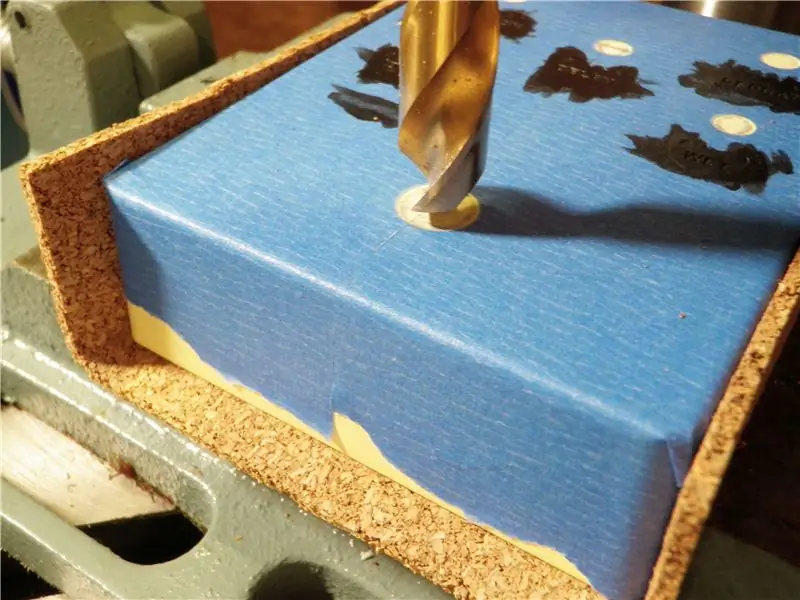
Sujete su caja en un tornillo de banco de prensa de taladro. Asegúrese de utilizar algún tipo de relleno uniforme como una sábana de tela o, en mi caso, una esterilla fina de corcho. Asegúrese de sujetar correctamente el tornillo de banco o asegurarlo de otro modo a la taladradora.
Con una broca de 1/2 , alinee la broca con el centro de la marca del botón del interruptor de pie y luego taladre.
Reemplace la broca de 1/2 "con una broca de 9/32" y repita el proceso de alineación y perforación para hacer 5 orificios para los potenciómetros.
Paso 9: pelar
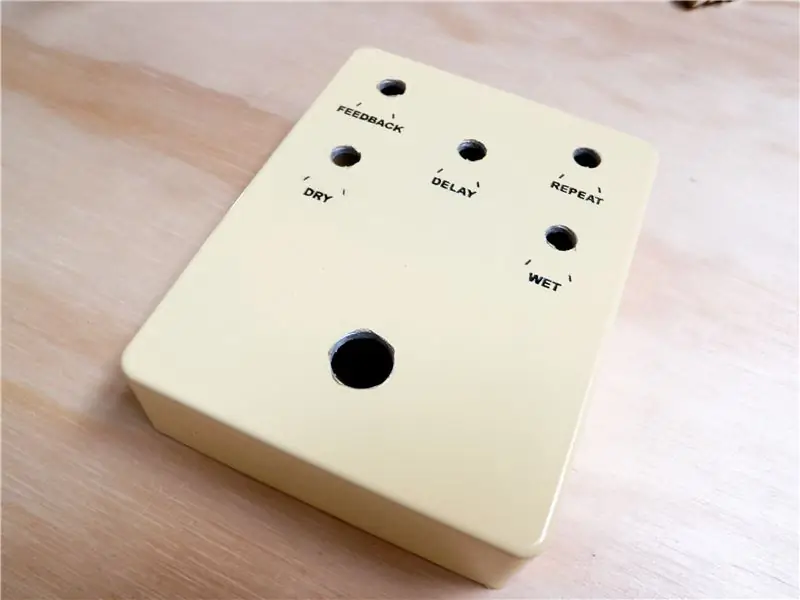
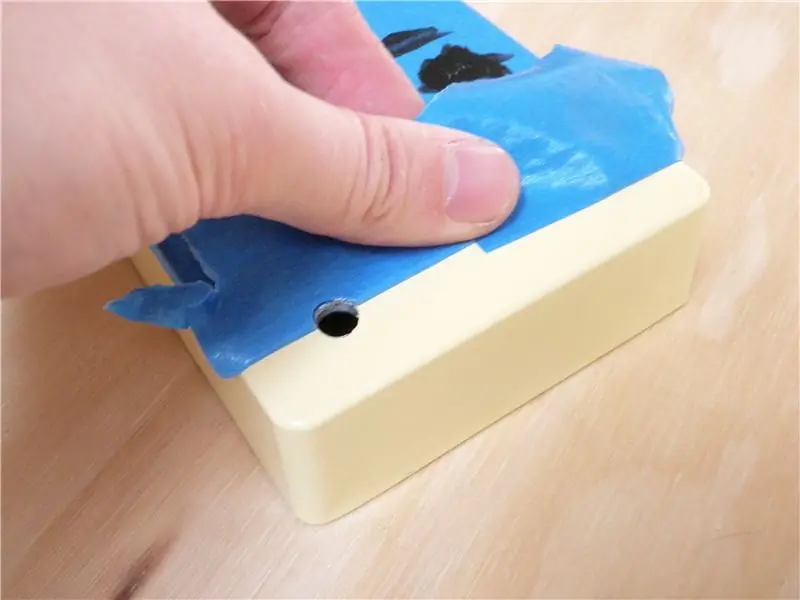
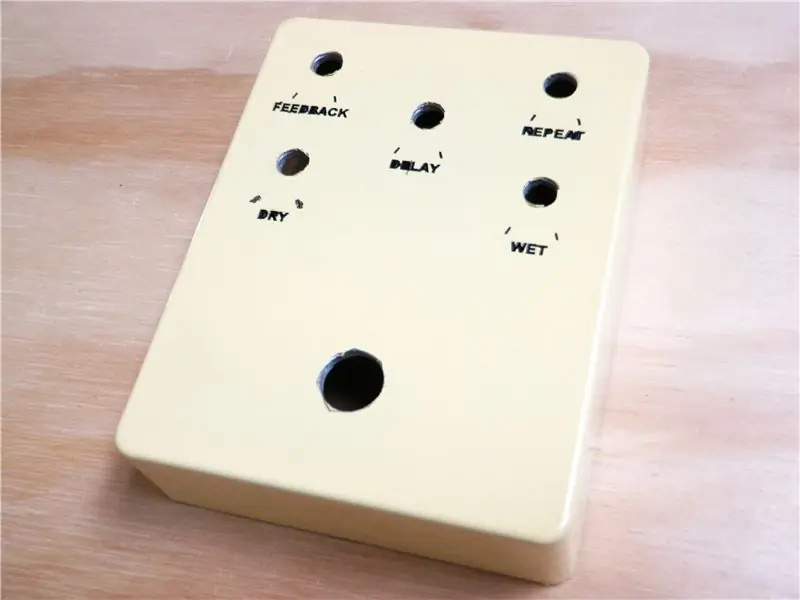
Quita la cinta de pintor y usa con cuidado un cuchillo Exacto para recoger o raspar suavemente los restos de pintura alrededor de las letras.
Paso 10: Perfora un poco más
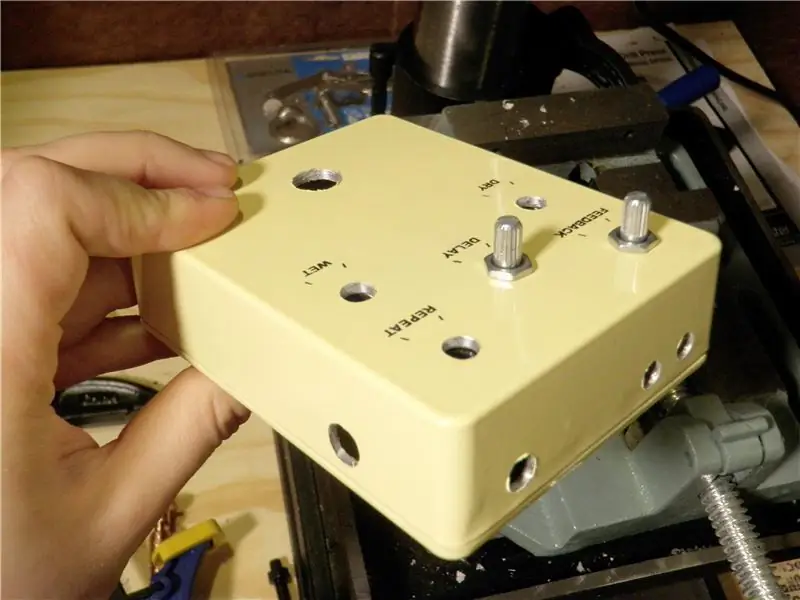
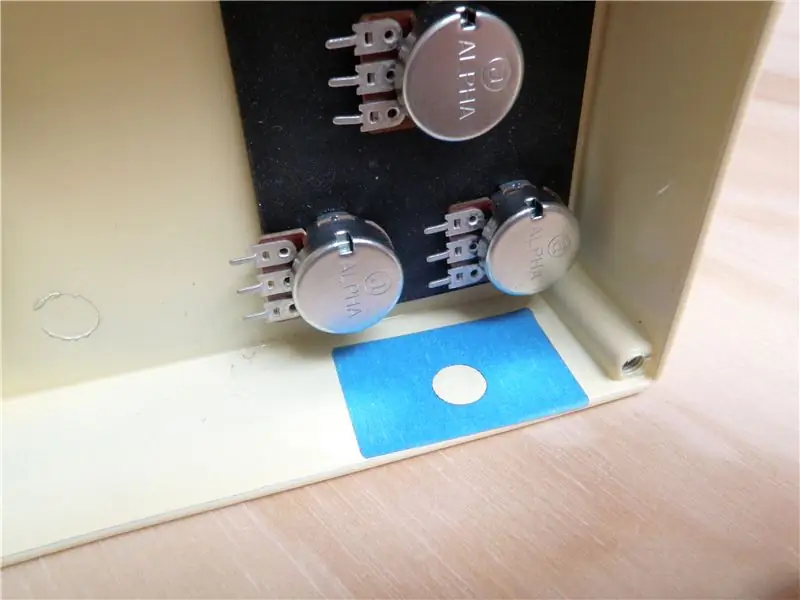
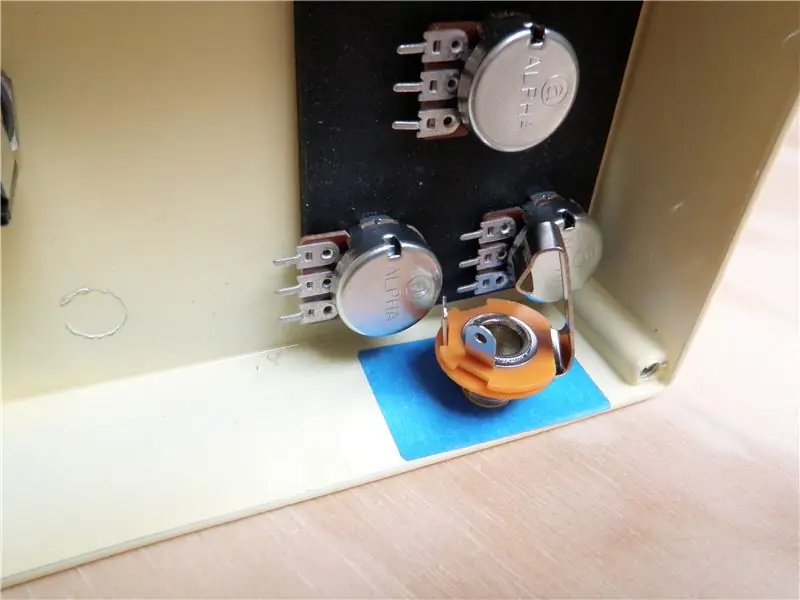
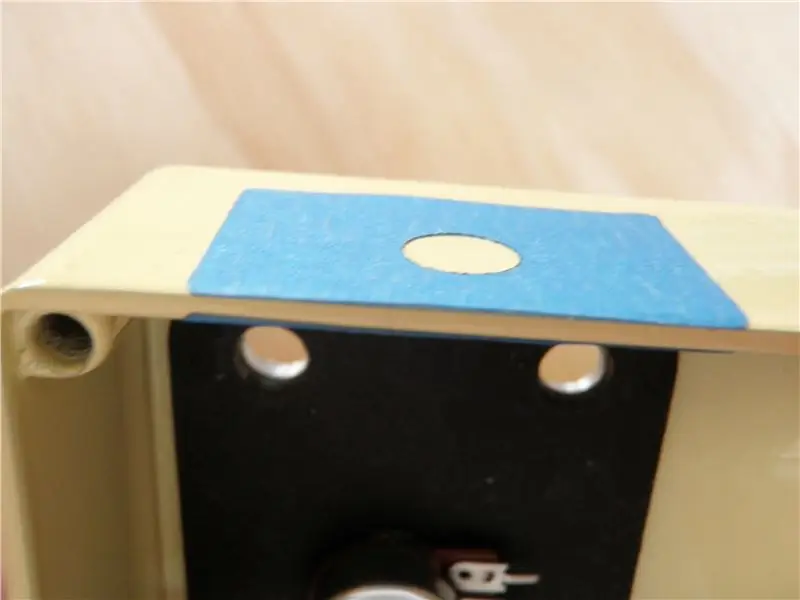
Ahora, necesitamos perforar agujeros en el costado de la caja. Dos de los orificios tendrán un diámetro de 3/8 y serán para las tomas de audio (en los lados izquierdo y derecho). Los otros dos orificios serán para la toma del adaptador de corriente CC y un interruptor de encendido / apagado (en la parte posterior). Para estos dos orificios, obviamente debe usar brocas apropiadas para el tamaño de la pieza que tiene (recomiendo perforar orificios de prueba en el material de desecho primero). Como puede ver, también hice un orificio adicional para un interruptor que no hice terminan usando (puede ignorar eso a menos que tenga un uso para él).
Para averiguar dónde perforar estos orificios, instalé temporalmente algunos potenciómetros, luego, usando plantillas de cinta y las piezas que se instalarán, descubrí la posición exacta del orificio en el interior de la caja. Una vez que tuve esto en su lugar, alineé una plantilla idéntica en el exterior de la caja. La teoría aquí es que el agujero en el interior coincide con el agujero en el exterior, de modo que cuando perfora, su pieza debe encajar exactamente donde debe estar.
Descubrí que lo que funciona mejor en este caso es si las tomas de audio de 1/4 "están situadas entre y" arriba "(al mirar hacia abajo dentro de la caja) las dos filas de potenciómetros (y también lo suficientemente lejos del borde para dar cuenta del borde La posición del interruptor y el conector de alimentación son menos críticas, pero también deben estar situadas "encima" del potenciómetro.
Una vez que toda la cinta esté en su lugar, perfore los agujeros.
Paso 11: grabar de nuevo
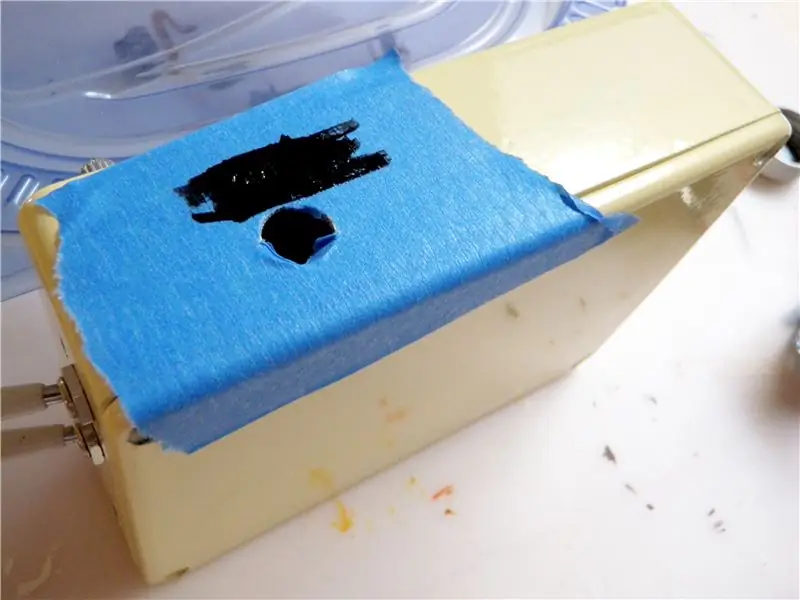
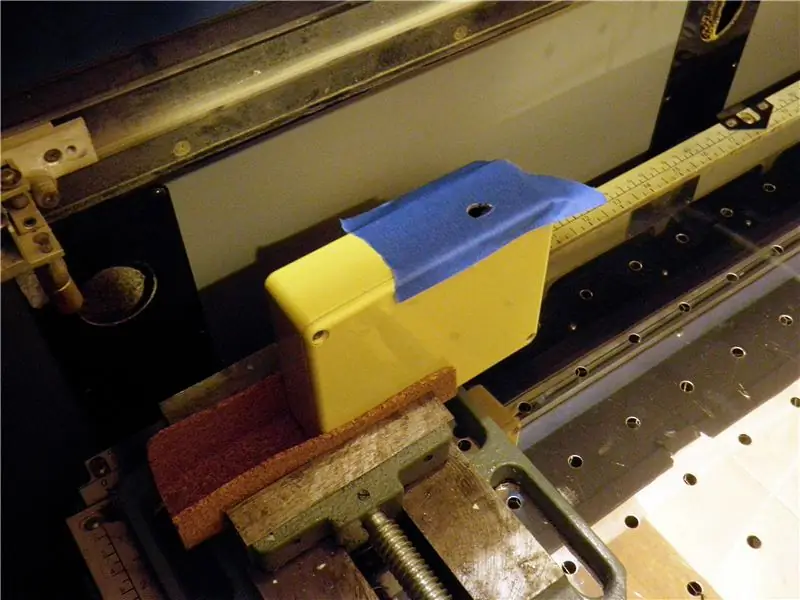
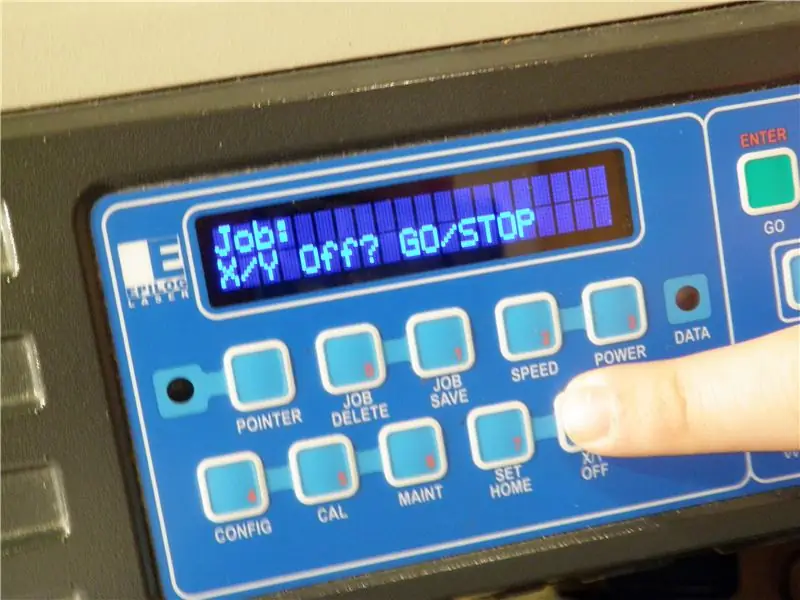
Esta vez, estamos haciendo las cosas un poco al revés, como pueden notar, primero perforamos los agujeros y ahora estamos grabando. Decidí hacerlo de esta manera para asegurarme de perforar agujeros que se alinearan correctamente con los potenciómetros en el interior de la caja.
De todos modos, simplemente coloque un trozo de pintura sobre el agujero y use un lápiz o una cuchilla para atravesar la cinta y exponer el agujero. A continuación, coloque la caja en un tornillo de banco de taladro. Baje la base de su cortadora láser alrededor de un pie y luego coloque todo el shebang adentro. La forma más fácil de hacer esto es apagar el bloqueo del eje x / y, encender el puntero de punto rojo, mover el cabezal del láser hacia donde crea que debería estar el punto cero y luego restablecer el inicio del láser. Luego, con un poco de prueba y error y algunos trozos de cinta, debería poder obtener la alineación correcta.
Grabe usando los siguientes ajustes:
Potencia: 50 Velocidad: 100 Pases: 5
Si no tiene un cortador láser, haga algunas plantillas como antes y péguelas apropiadamente a la caja.
Cuando haya terminado, repita el proceso de pintura, pelando y quitando el exceso de pintura.
Paso 12: revestimiento de corcho
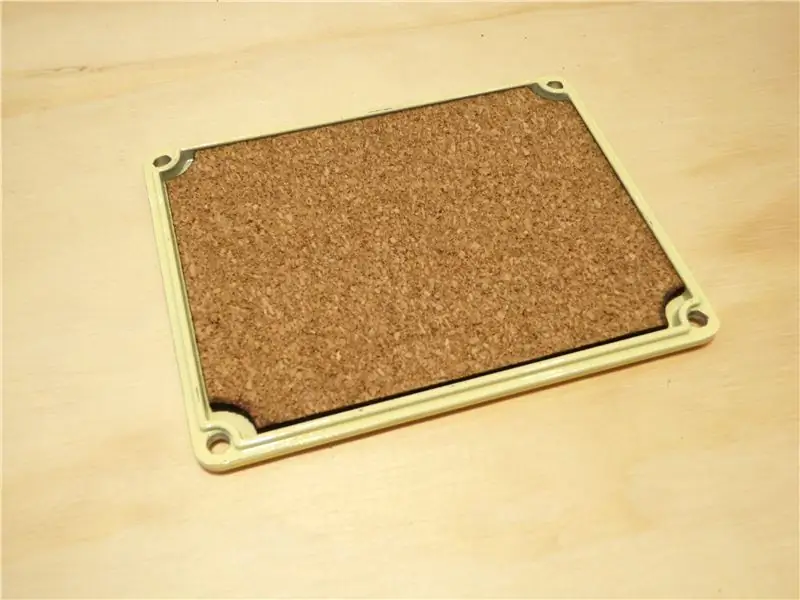
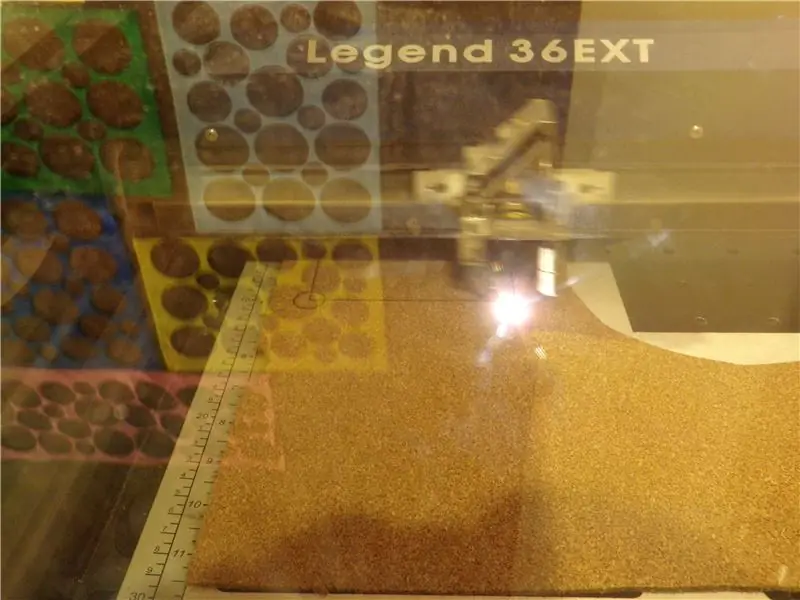
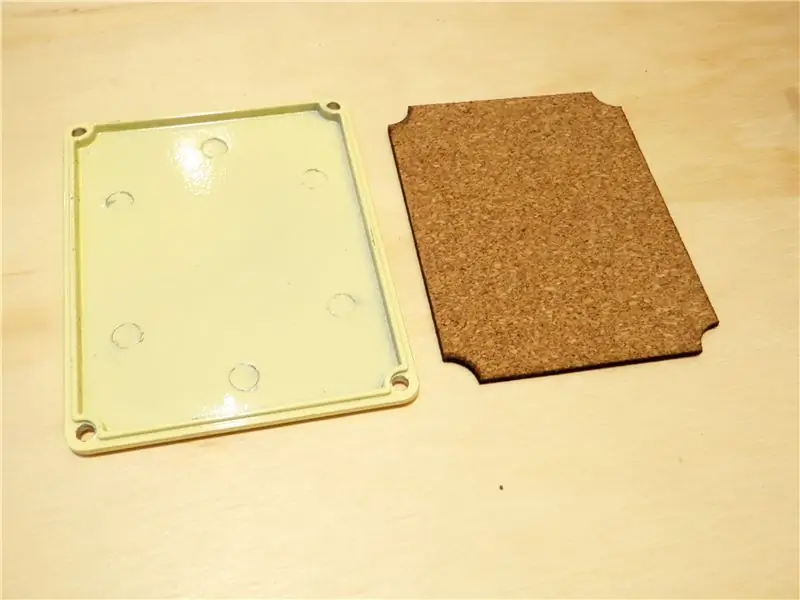
Cubra la tapa con una hoja de corcho u otro aislante delgado. Esto le dará a la placa de circuito una superficie sobre la que descansar que no sea conductora y evitará que se produzca un cortocircuito.
La lima adjunta se puede utilizar en un cortador láser y produce una forma que representa el labio interior de la tapa y los orificios para tornillos.
He pegado el corcho a la tapa con un poco de pegamento en aerosol. En retrospectiva, debería haber alineado los bordes con cinta azul antes de rociar, ya que necesitaba lavar el pegamento en aerosol después (lo cual era un dolor en el cuello).
Paso 13: potenciómetros e interruptores
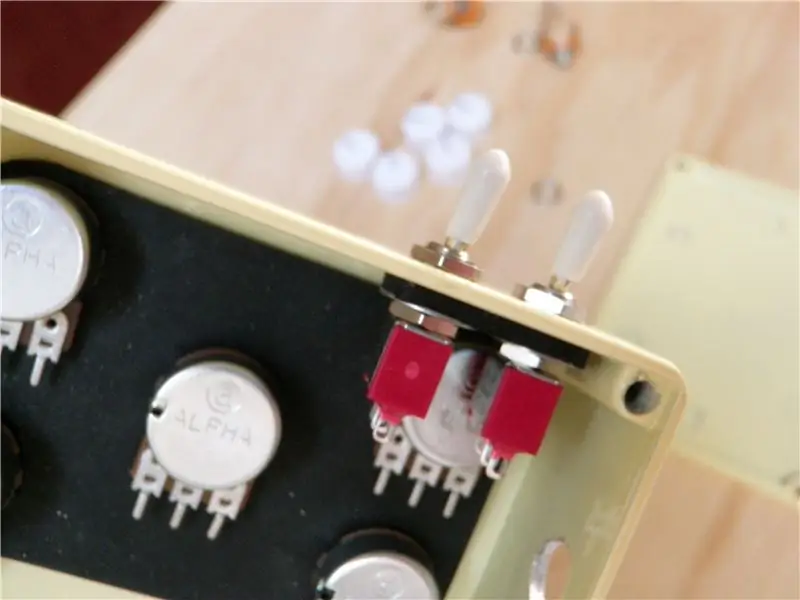
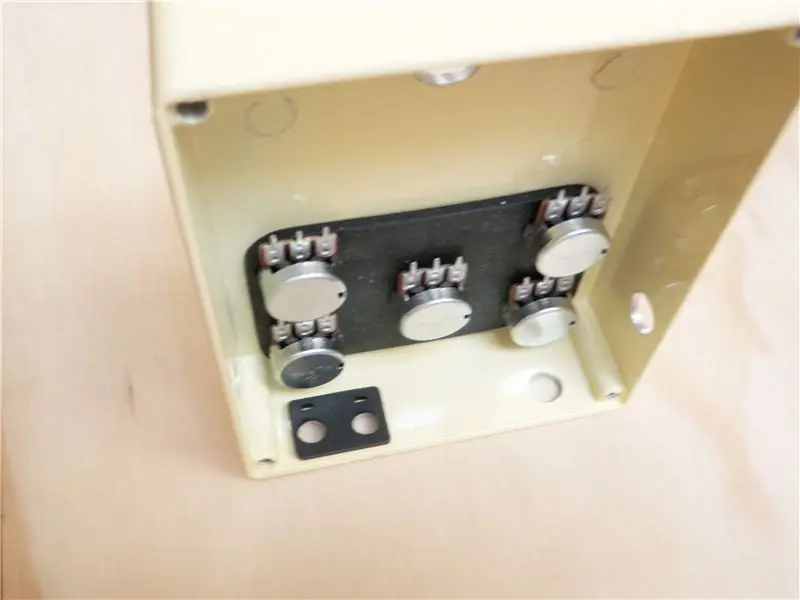
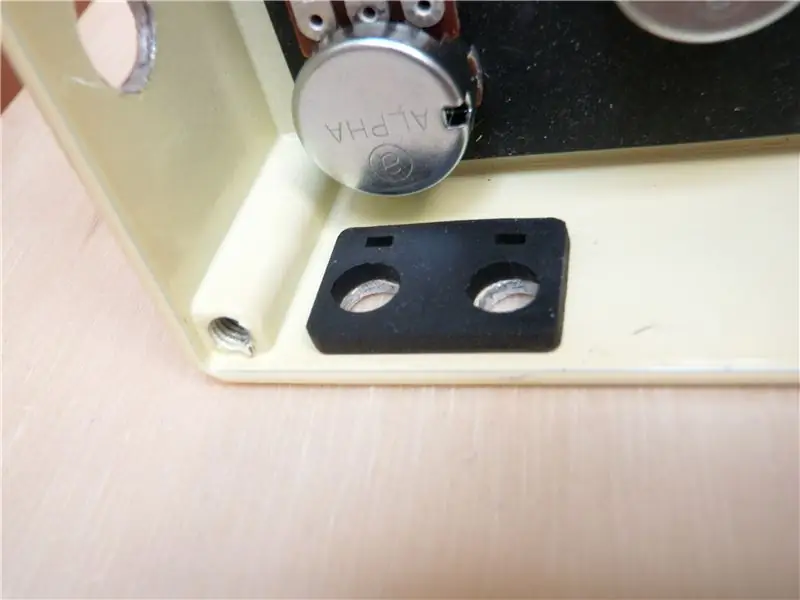
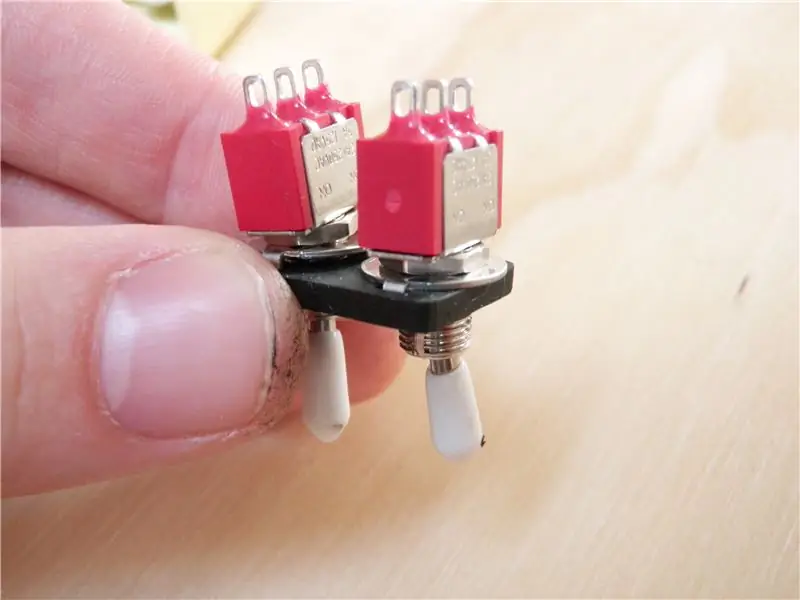
Instale sus potenciómetros e interruptores dentro de la caja usando los soportes de goma para mantenerlos en su lugar.
No olvide alinear los potenciómetros con sus etiquetas apropiadas.
100K - Volumen seco 100K - Volumen húmedo 100K - Repetir 50K - Retraso 5K - Comentarios
Paso 14: Cablee el panel frontal
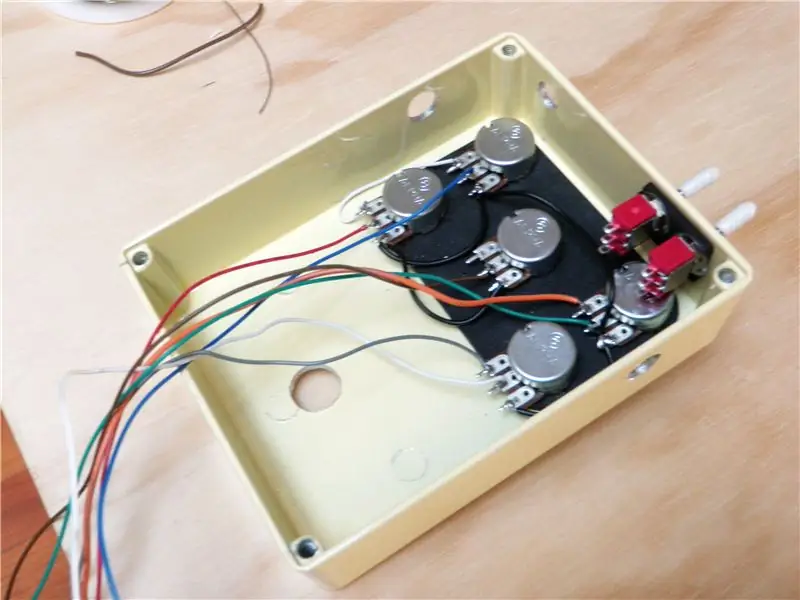

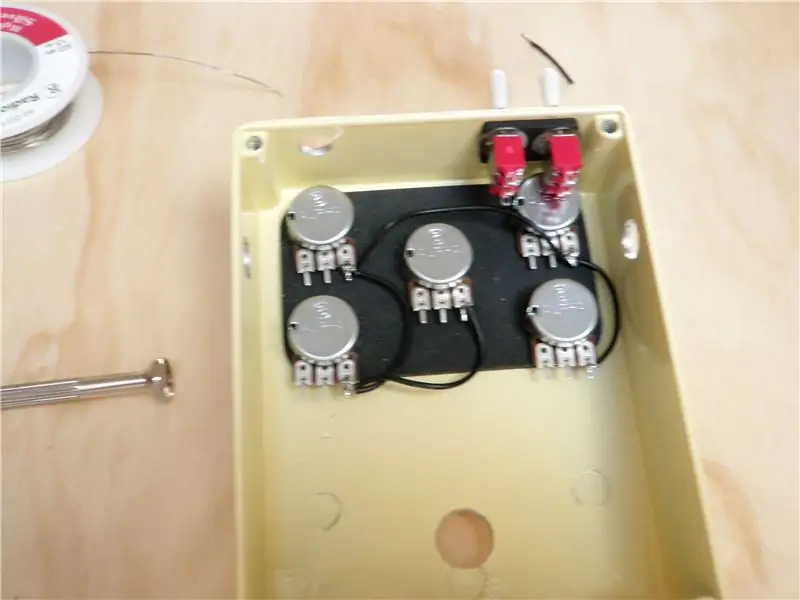
Es hora de conectar los potenciómetros con un cable trenzado. El pin derecho de cada uno debe estar conectado a tierra. Los otros pines deben conectarse según el diagrama de cableado a continuación.
Recomiendo usar cables de diferentes colores para cada pin no conectado a tierra. Para esta variedad de cables, utilicé el mazo de cables de una fuente de alimentación de computadora rota. Esto me dio muchos cables de diferentes colores para elegir.
Paso 15: Conecte la energía
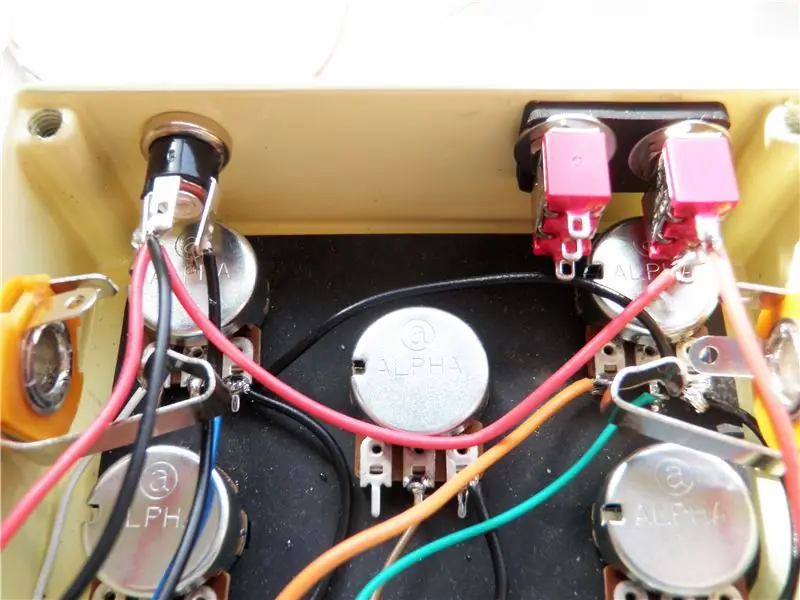

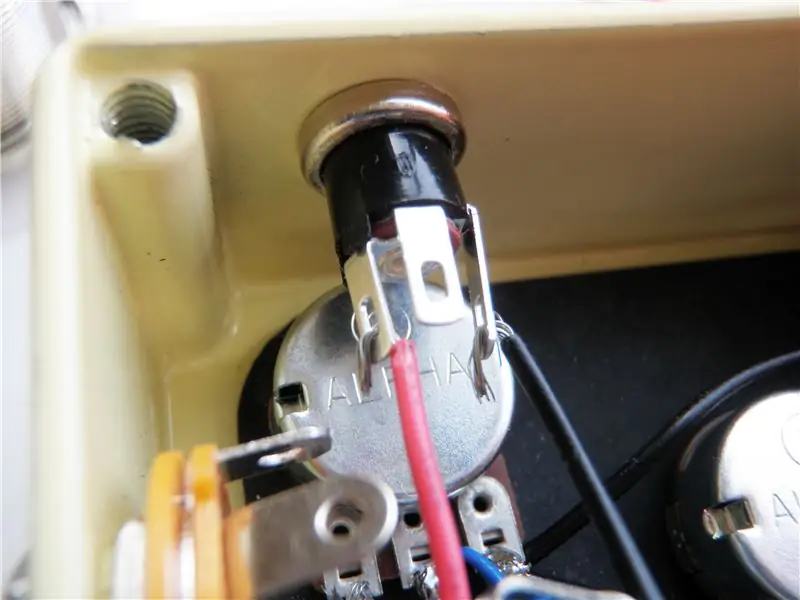
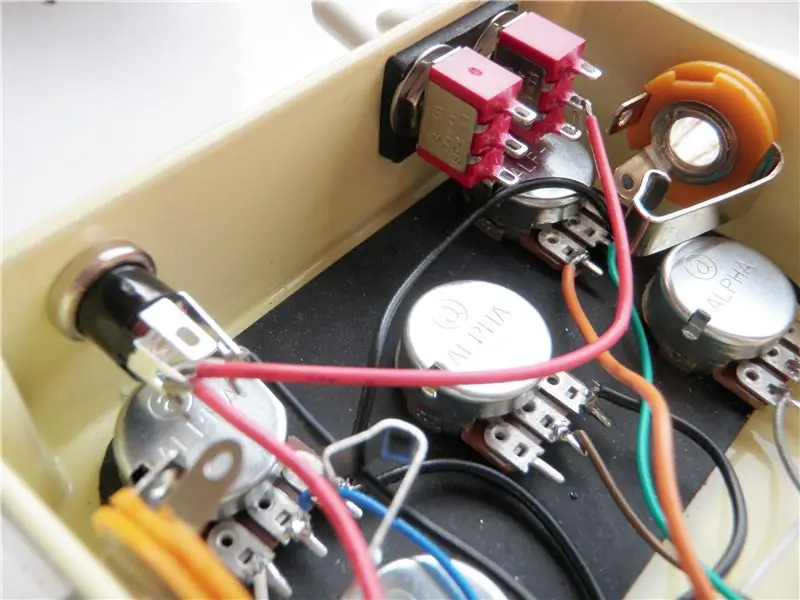
Conecte el enchufe de alimentación de modo que tenga una punta positiva. En otras palabras, el cable rojo de la batería de 9 V debe conectarse al pin central y el cable negro de la batería debe conectarse a uno de los pines que se desconecta cuando se inserta el enchufe.
Conecte otro cable negro entre el pin no utilizado y tierra en la placa de circuito.
Además, conecte un cable rojo desde la clavija de alimentación roja a la clavija central de su interruptor de alimentación SPST. Conecte un último cable rojo al terminal que hace la conexión al pin central cuando el interruptor está en la posición "On".
Paso 16: conecte el panel frontal
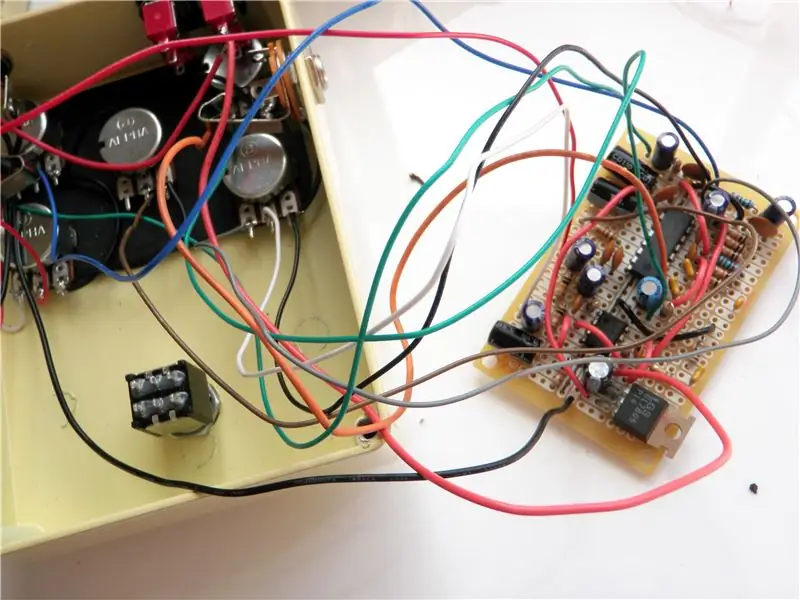
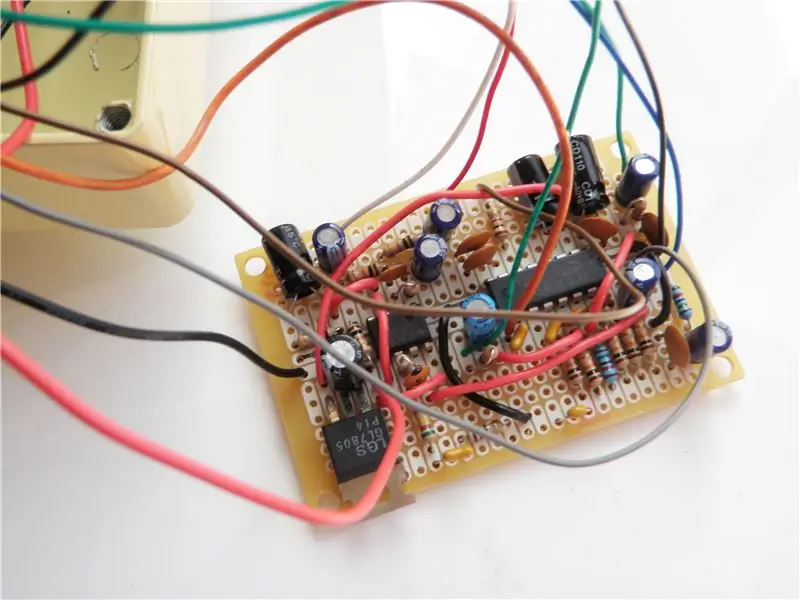
Conecte los cables de los potenciómetros y el interruptor de encendido a la placa de circuito según corresponda.
Paso 17: Cablee todo lo demás
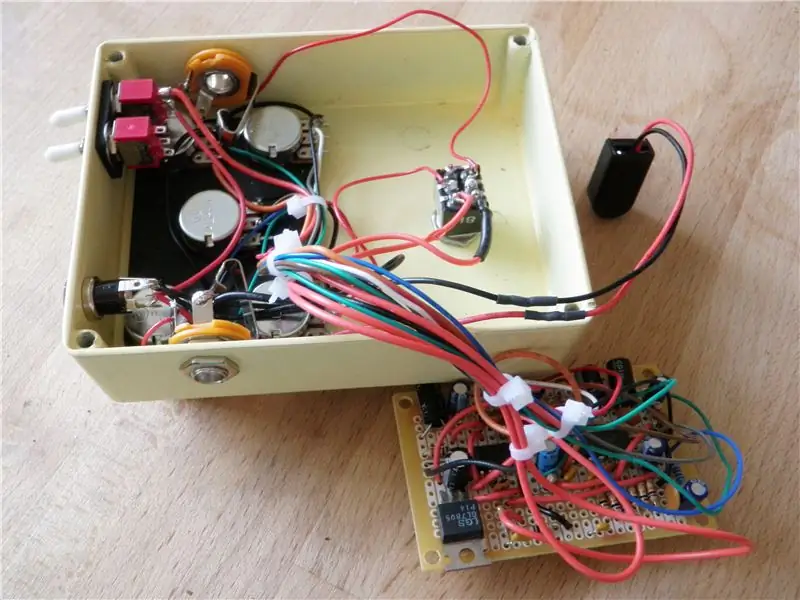
Por último, debe conectar el interruptor de pedal DPDT y las tomas de entrada y salida.
Si su carcasa es conductora, solo necesita conectar un pin de las tomas a tierra. El otro pin hará una conexión a través del estuche.
Dicho esto, asegúrese de conectar las tomas de entrada y salida correctamente. En caso de que no sepa cuál es correctamente, los pines de entrada y salida deben conectarse respectivamente a los pines centrales del interruptor DPDT. Se debe conectar un par de pines externos a la placa de circuito (prestando especial atención a "In" y "Out"). El otro conjunto de clavijas simplemente se debe unir para lograr una derivación real.
Paso 18: Toques finales
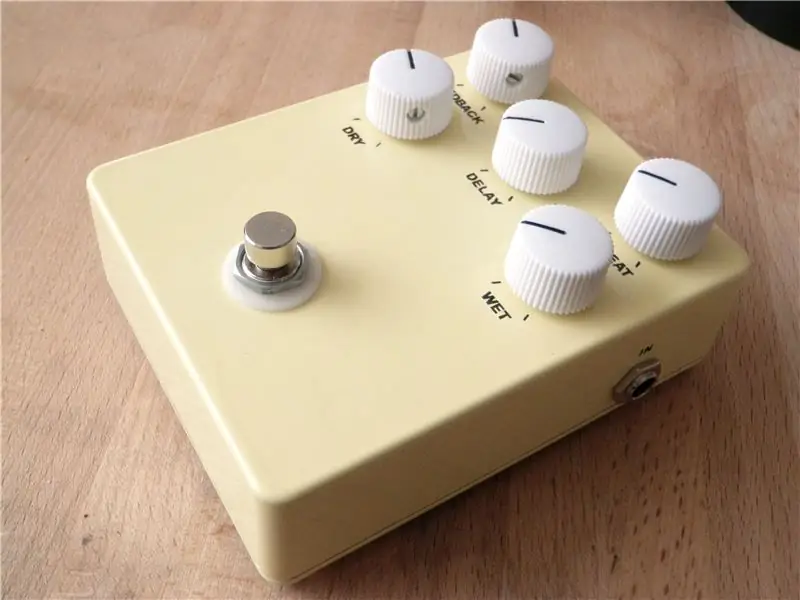
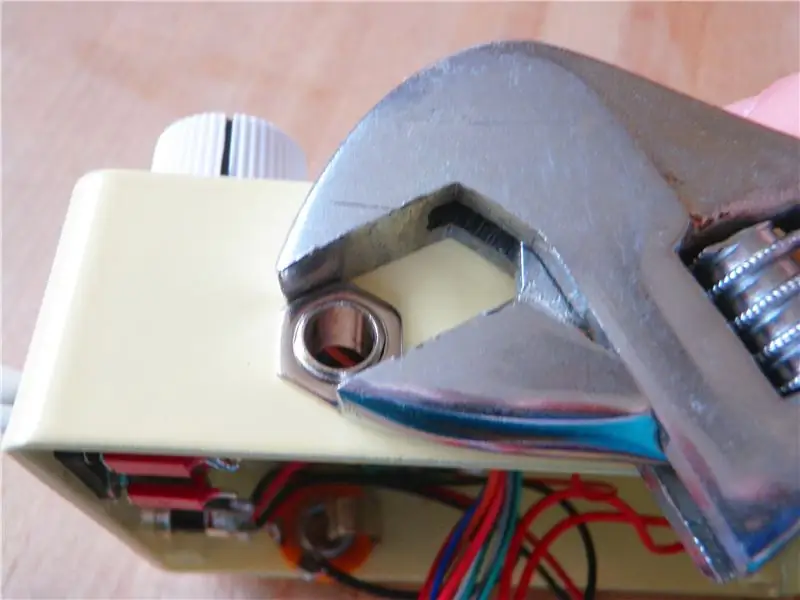
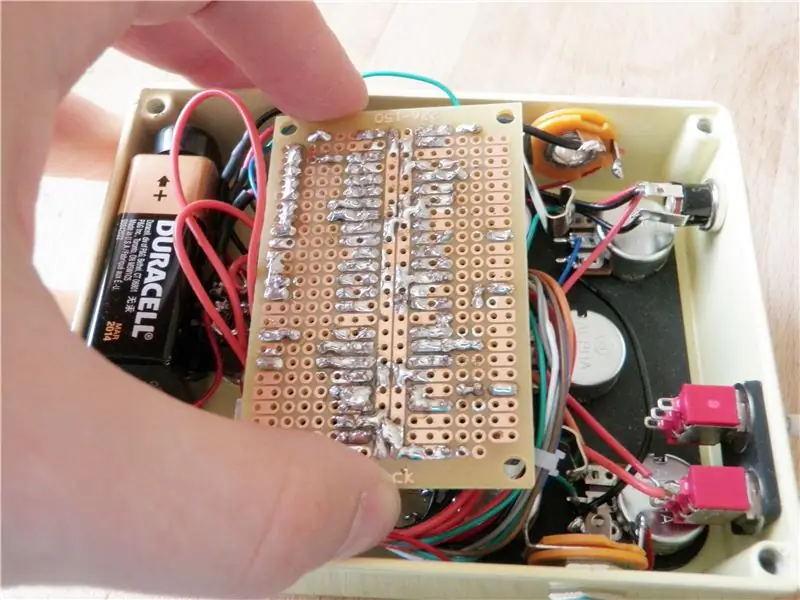
Ahora es el momento de dar los toques finales.
Utilice una llave sin dientes para apretar las tuercas y fije firmemente los potenciómetros, interruptores y tomas en el interruptor.
Conecte una batería de 9V.
Coloque todo dentro de la caja, coloque la tapa, asegúrese de que puede insertar los tapones en ambos conectores sin obstáculos y luego atornille la caja para cerrarla.
Si aún no lo ha hecho, coloque las perillas del potenciómetro y apriete su tornillo de fijación.
Por último, es posible que desee considerar colocar algunos pies de goma autoadhesivos en la parte inferior.
Paso 19: Plug and Play
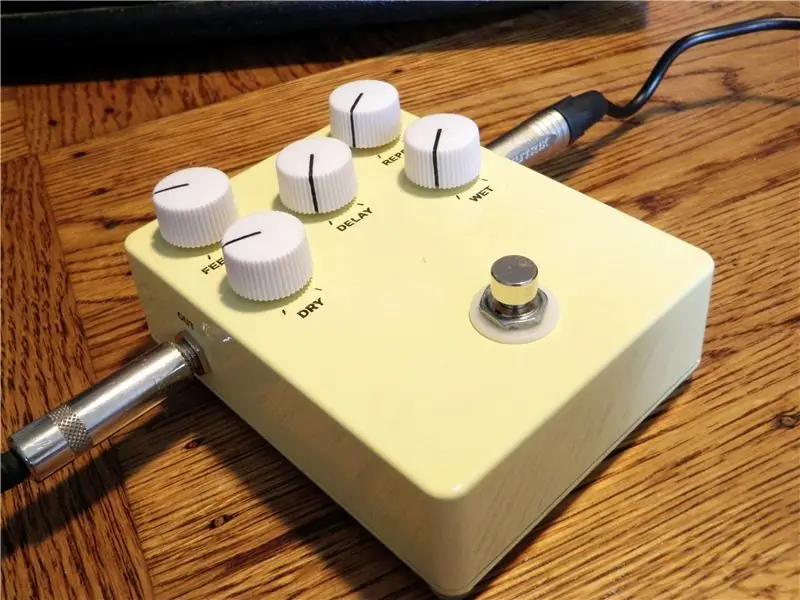
Conéctalo y rockea.
Si rockear no está funcionando, ¡NO ENTRE EN PÁNICO!
Abra la carcasa de nuevo y depure el problema.
A continuación, se ofrecen algunos consejos para la depuración:
1) ¿Está encendido? Bueno … enciéndelo. 2) ¿Tiene carga la batería? 3) ¿Hay conexiones puenteadas en la PCB? 4) ¿Todas las conexiones coinciden con el esquema? 5) ¿Ha cableado los interruptores correctamente? 6) ¿Ha enrutado el cable correctamente de IN a OUT? 7) ¿Está subido el volumen de su guitarra y amplificador? 8) ¿Está tu amplificador encendido? 9) ¿Qué tal el volumen del pedal? 10) Si está encendido pero no demorado, ¿ha intentado pisar el interruptor de pie?
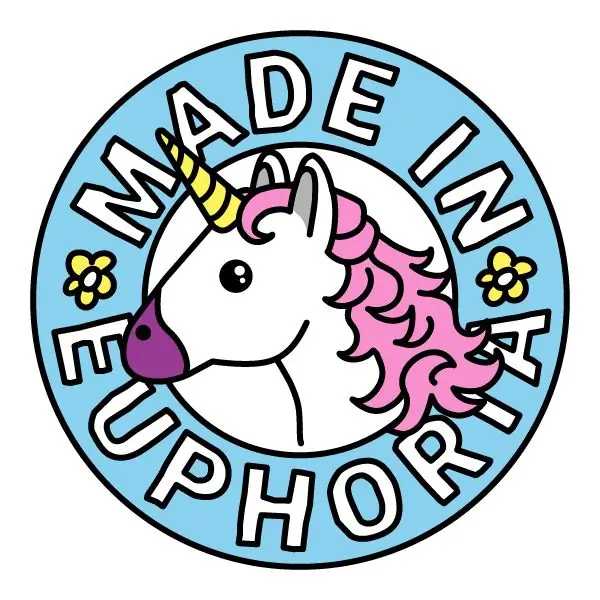
¿Te pareció útil, divertido o entretenido? Siga a @madeineuphoria para ver mis últimos proyectos.
Recomendado:
Retardo de cinta de microcassette: 4 pasos
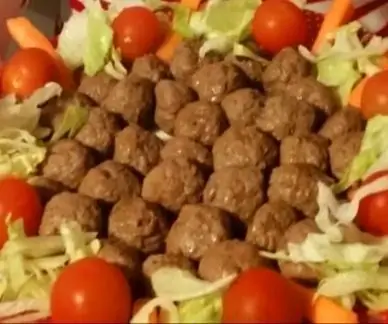
Retardo de cinta de microcassette: esta es una guía para aquellos que desean construir un retardo de cinta barato, divertido y diferente de los dictáfonos de cinta de microcassette. Originalmente publiqué una guía para la compilación en mi sitio / blog (dogenigt.blogspot.com) pero el proyecto ha ganado mucha popularidad
JOYSTICK USB DE RETARDO CERO - MODIFICACIÓN ANALÓGICA AUTOMÁTICA: 5 pasos
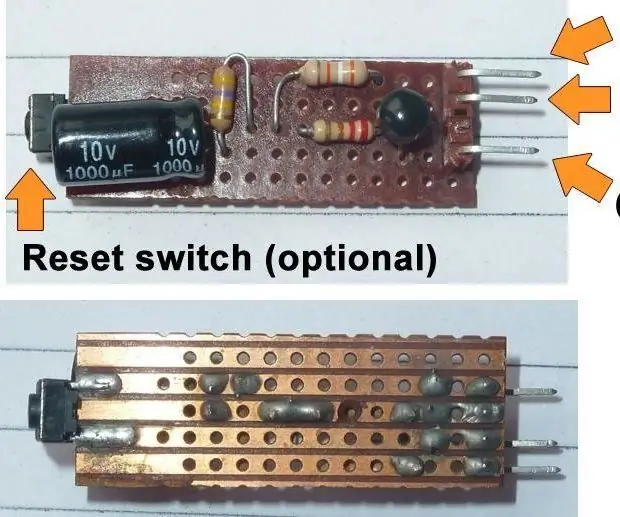
JOYSTICK USB ZERO DELAY - MODIFICACIÓN ANALÓGICA AUTOMÁTICA: Este es un proyecto adicional a la modificación del joystick analógico verdadero del codificador USB Zero Delay. Debe haber modificado, probado y calibrado con éxito el codificador en el proyecto anterior antes de agregar este dispositivo. Cuando esté terminado y funcionando
Sistema de retardo automático: 5 pasos
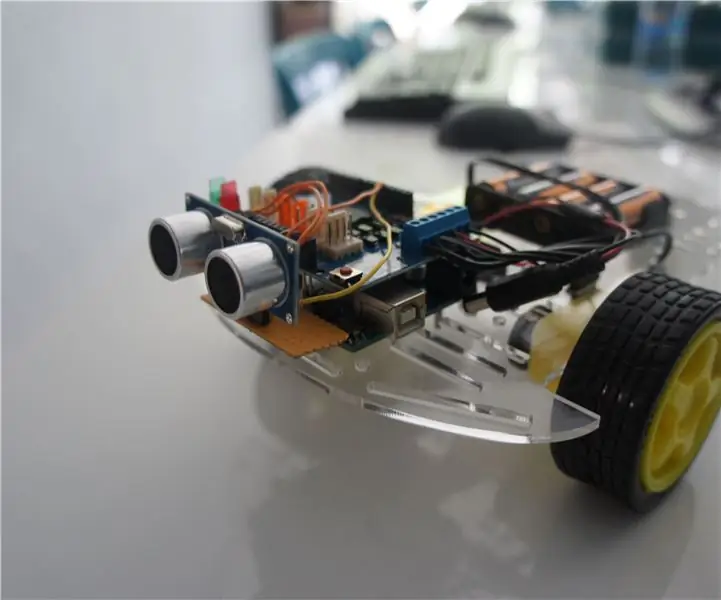
Sistema de retardo automático: este proyecto se desarrolla modificando el algoritmo del robot que evita objetos. Además, el robot en este instructable puede ser controlado por un teléfono inteligente a través de Bluetooth
Efecto de doble retardo: 10 pasos (con imágenes)
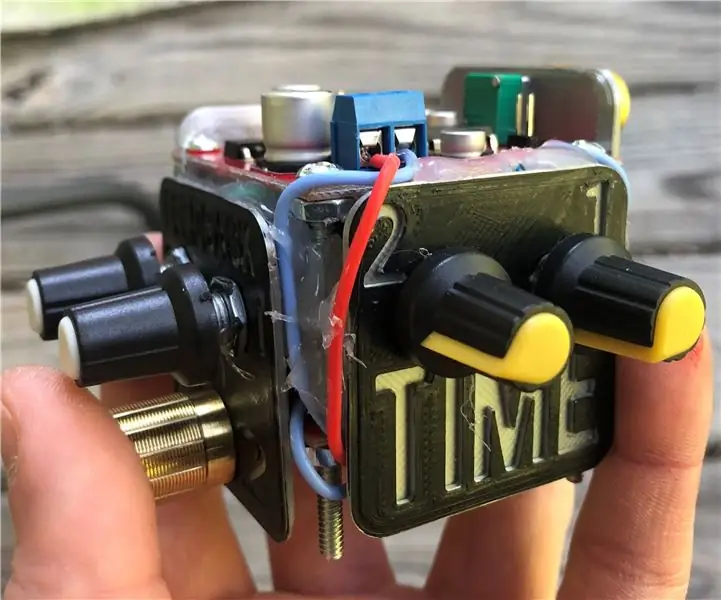
Efecto de retardo doble: ¡Efecto de retardo doble SUPER simple! Mi objetivo era construir el retraso más compacto y loco posible utilizando solo un puñado de componentes. El resultado es una máquina de ruido sin caja, fácilmente modificable con un sonido sorprendentemente masivo. ACTUALIZACIÓN: Detalles
Un circuito de retardo de tiempo simple: 3 pasos (con imágenes)
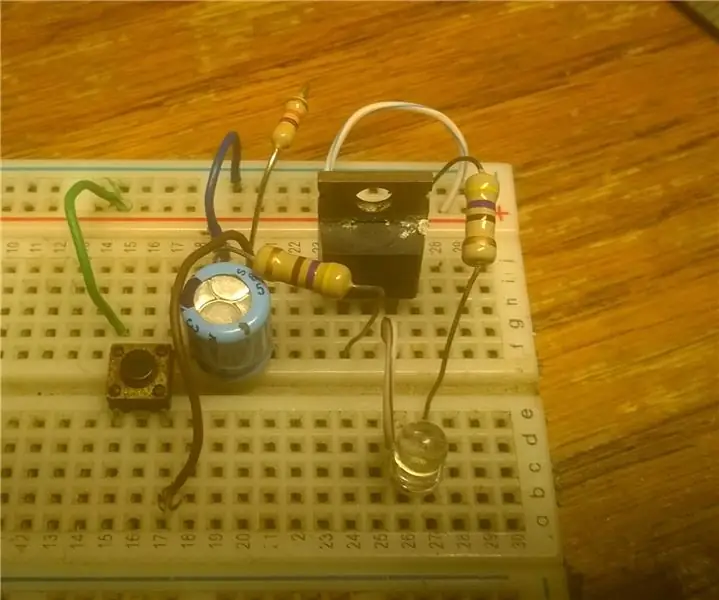
Un circuito de retardo de tiempo simple: finalmente decidí agregar otra línea a mi controlador de carga y quería una salida de potencia constante en lugar del PWM que sale del controlador de descarga, así que hice este pequeño circuito práctico para tomar una señal PWM y cambiarla a una señal de CC constante