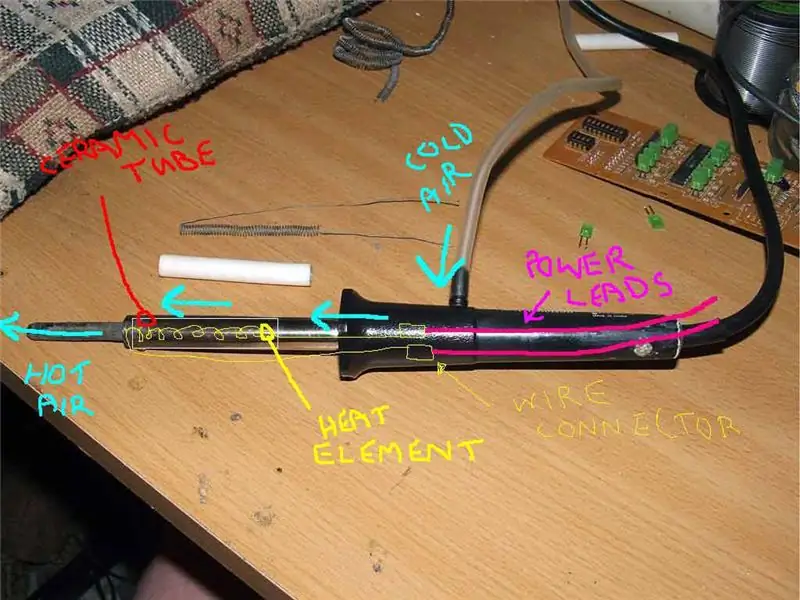
Tabla de contenido:
- Paso 1: Del basurero a mi casa
- Paso 2: el ventilador
- Paso 3: Unidad de soplado
- Paso 4: Elemento calefactor
- Paso 5: Primer plano del elemento
- Paso 6: tubo de cerámica
- Paso 7: El elemento y el tubo de cerámica
- Paso 8: El Gutz
- Paso 9: la boquilla
- Paso 10: Clavija cuadrada en un agujero redondo
- Paso 11: todas las cosas están aquí
- Paso 12: soplador de velas:)
- Paso 13: Fuente de alimentación regulada
- Paso 14: Temp # 1
- Paso 15: Temp # 2
- Paso 16: Temp # 3
- Paso 17: fusión del alambre de soldadura
- Paso 18: primer trabajo
2025 Autor: John Day | [email protected]. Última modificación: 2025-01-23 14:40
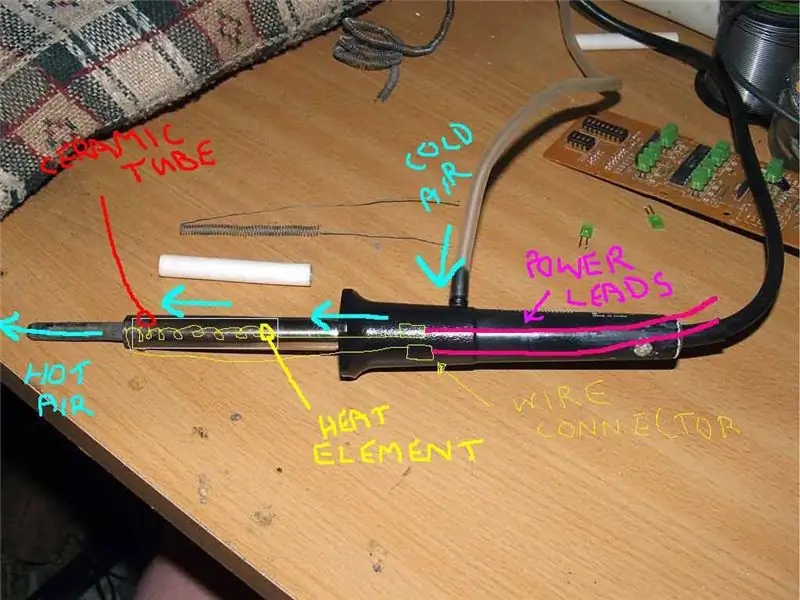
Esta es mi primera publicación de Eva de un artículo de bricolaje en la web. Así que discúlpeme por algunos errores tipográficos, protocolo, etc. Las siguientes instrucciones muestran cómo hacer que un soldador de aire caliente EN FUNCIONAMIENTO sea adecuado para TODOS los usos que requieran soldadura. Este soldador de aire caliente no se limita a dispositivos SMT (tecnología de montaje en superficie) o alambre de soldadura súper delgado. En menos de 15 segundos después de encender a este bebé, alcancé más de 300 grados centígrados de aire caliente. Todavía tenía espacio para más… jajaja. El costo para mí fue de menos de $ 10 dólares australianos. más gasolina para que mi coche llegue al vertedero local y vuelva a casa. Si no tiene una fuente de alimentación regulada, estoy seguro de que una fuente de alimentación ATX o dos conectadas en serie juntas proporcionarían suficiente energía para encender su versión. Si lo hace de esta manera, un potenciómetro es esencial para ajustar la salida de amperaje y el voltaje de CC. Esta unidad de orificio es SEGURA de descargas eléctricas debido a los peligros de alto voltaje / corriente típicos de los suministros de CA alimentados por la red, pero si tiene un ticker deficiente … use protección:)
Paso 1: Del basurero a mi casa
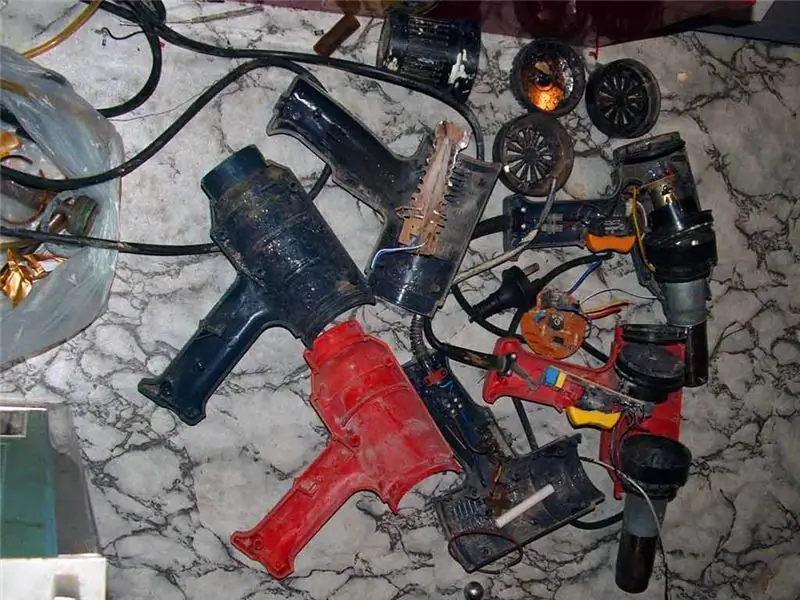
No tenía mucha fe en poder sacar algo útil de estas pistolas de aire caliente cuando las compré en el basurero local por casi nada. Después de que las separé, algunas partes funcionaron y otras no. Era solo una cuestión de tirar las partes inútiles y mantener las buenas y luego algunas más de sobra más adelante en caso de que mi plancha fallara en los años venideros. Una vez que recogí lo que pensé que podría ser útil para hacer realidad mi idea, los expuse todos ante mí y medité sobre ellos con algunos cafés y cigarrillos. INTRODUCCIÓN: Ayer por la mañana, mi soldador de 50 vatios se rompió. Trágico, lo sé … jajaja. La principal tragedia fue que no tenía $$$ para conseguir otro. Bueno, tenía una suma de dinero, pero no lo suficiente para conseguirme otra. Soy un fotógrafo independiente, pobre en eso y estoy trabajando en el uso de PWM (modulación de ancho de pulso) para regular el suministro de voltaje de pequeñas baterías de plomo-ácido extraídas de scooters viejos que funcionan con baterías. Los componentes electrónicos para fabricar mis reguladores de voltaje PWM los obtengo al desoldar viejas fuentes de alimentación ATX y televisores, etc. Los reguladores lineales son demasiado ineficientes para satisfacer mis necesidades portátiles de energía, ya que esta energía finalmente se usará para controlar mis flashes fuera de cámara y otros cosas. De todos modos, volviendo al meollo de esta presentación:) Una búsqueda de dos horas en Google en la WWW reveló que la gente convirtió sus soldadores en soldadores de aire caliente. Pero todos estaban trabajando antes de que los modificaran y el mío estaba muerto desde el principio… jajaja. Además, las otras creaciones que vi en la web se limitaron en gran medida a eliminar los bits electrónicos SMT más pequeños. Me di cuenta de que en mi revisión rápida de las "creaciones" de otras personas, todas tenían el mismo defecto y problema básico: exponer suficiente aire frío que pasa a través de sus dispositivos para calentar el elemento antes de dejar el soldador. A la mayoría de las personas se les ocurrió la idea de insertar una malla de cobre o hierro en el barril cerca del elemento para aumentar el área de superficie del elemento calefactor expuesto al paso del aire más frío. Mi experiencia con este método utilizado por otros me recordó a mis primeros experimentos de enfriamiento Peltier que luego usé para mi acuario marino… eso fue con problemas de transferencia de calor. Vaya … se desviaron;) De todos modos, siempre quise quitar los componentes a granel de las placas de circuito impreso usando esas pistolas de aire caliente para quitar pintura que consumen carbón. ¡Pero tampoco tengo el dinero para eso! Así que pensé en hacer un soldador que pudiera actuar como una pistola de aire caliente y también como un delicado soldador. Así que después de varias tazas de café y muchos cigarrillos y muchas más búsquedas en Google, tenía en el fondo de mi mente una idea de todos los aparatos que necesitaba para conseguir un soldador que funcionara … ir al vertedero local. Me encanta el basurero … ¡¡tantas cosas útiles y baratas también !! Es muy parecido a ir a una ferretería a buscar ventanas. $ 10 ozzy dólares más tarde salí del basurero con 2 computadoras portátiles y tres pistolas de aire caliente para quitar pintura. Las armas habían visto días mejores y no tenía muchas esperanzas de sacarles algo que pudiera funcionar. Las computadoras portátiles que guardo para sus pantallas LCD que usaré para mi proyector de películas de bricolaje:) Pero ese es otro proyecto. En casa, separé las pistolas de aire. Me encanta separar las cosas … algo de lo que nunca crecí cuando era niño. LO SENTIMOS papá y mamá !!!
Paso 2: el ventilador

Parte del conjunto del ventilador de los sopladores decapantes de pintura. Aquí se muestra un ventilador de 17 V CC. Quité el puente rectificador y el condensador y usé este tipo de ventilador, ya que era todo lo que tenía para entregar aire al soldador. Esta resultó ser una situación afortunada más tarde, ya que tenía la cantidad correcta de flujo de aire que pasaba y estaba en contacto directo con el elemento calefactor.
Paso 3: Unidad de soplado
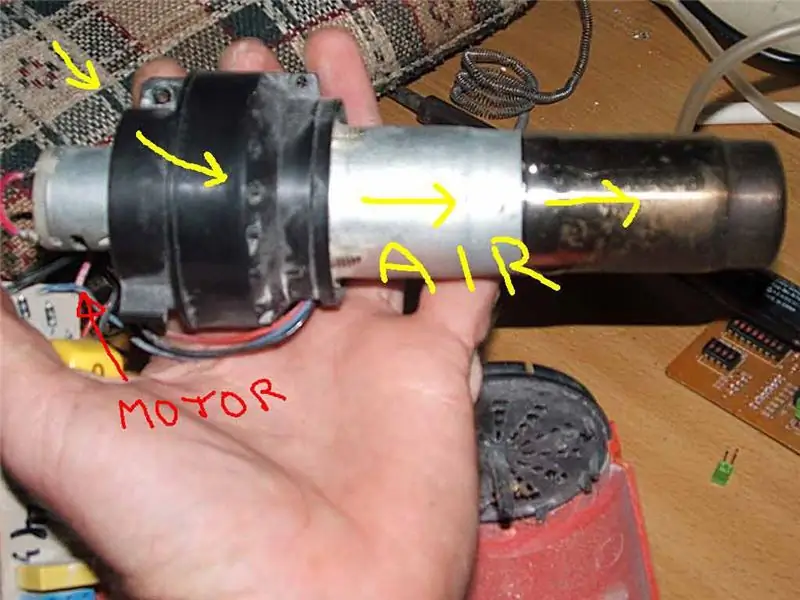
Esta es la unidad de ventilación esencial que entrega aire frío a través del elemento calefactor. Utilicé todo este conjunto como medio para bombear aire. Cómo iba a conectar esto, no tenía idea.
Paso 4: Elemento calefactor
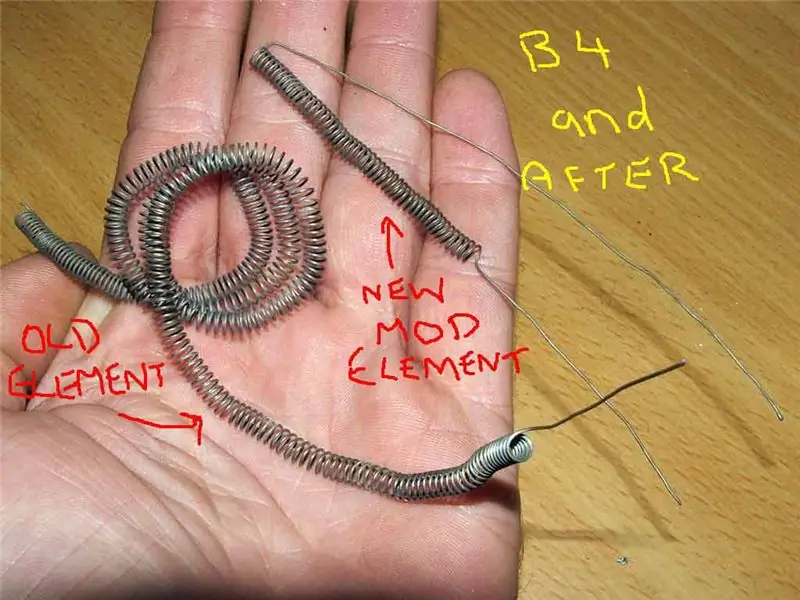
No olvide el elemento calefactor. Al hacer los tramos largos de alambre recto, engarce las curvas y asegúrese de no tener curvas cerradas. A la corriente no le gusta tomar curvas cerradas. RESUMEN: Encontré que dos ventiladores tenían cojinetes gastados y uno estaba bien. Tenía dos elementos calefactores rotos y algunos discos y tubos aislantes de cerámica. Realmente no hay mucho en estos bebés … me pregunto por qué son tan caros. Todo lo que son es un elemento calefactor y un motor. Un puente rectificador se encontraba entre el voltaje de la red de CA y el motor del soplador de aire. Esto fue alentador ya que quería hacer funcionar mi fuente de alimentación para la idea en mi cabeza desde un bajo voltaje de CC. No me gusta jugar con la red eléctrica de 240 voltios CA. Los motores tenían una potencia nominal de 17 voltios CC. Eso está lo suficientemente cerca de mis 12 voltios CC deseados. Encendí mi ventilador elegido que no tenía cojinete de traqueteo y funcionó. Kewl. También vi que una de las pistolas tenía cilindros huecos de cerámica que se usaban para sostener los elementos calefactores. Inserté uno de los cilindros en el tubo de metal de mi soldador. Encaja perfectamente. Eso también fue muy alentador. Todavía no tenía idea de cómo sería la idea final. Ser adaptativo y usar lo que está disponible es mi lema. Antes también había desmontado mi soldador muerto para ver cómo funcionaba y si podía arreglarlo. Su elemento estaba relleno. También noté que se basaba en un calentamiento conductivo para calentar la punta. Mi concepto desde el principio fue pasar aire frío a través del barril hueco, exponerlo a un elemento calefactor y hacer que salga aire caliente por la punta. Muy parecido a un mini decapante de pintura de aire caliente. Este concepto nunca cambió, pero las ideas sobre cómo llegué a este fin cambiaban constantemente, ya que diseñé numerosas ideas nuevas con lo que tenía disponible frente a mí en mi mesa de trabajo.
Paso 5: Primer plano del elemento
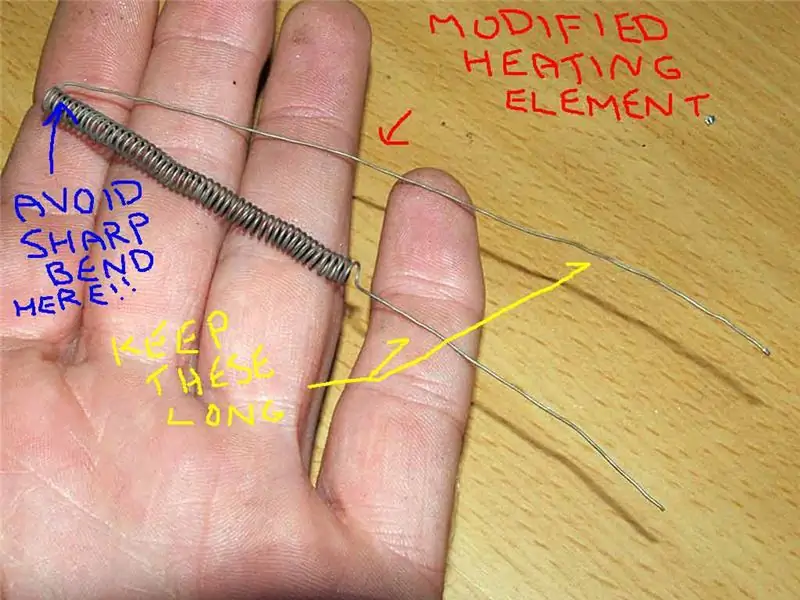
La idea de mantener largas las longitudes rectas es tener algo de espacio para jugar al armarlo todo. La longitud final que se decidió fue un poco más grande que esta. Hice un cortocircuito en la batería de 12 voltios y, aunque la batería estaba medio muerta, pude obtener algo de calor. Supuse que algunas longitudes adicionales de bobina pueden ayudar a desensibilizar los flujos de temperatura durante cambios leves de voltaje.
Paso 6: tubo de cerámica
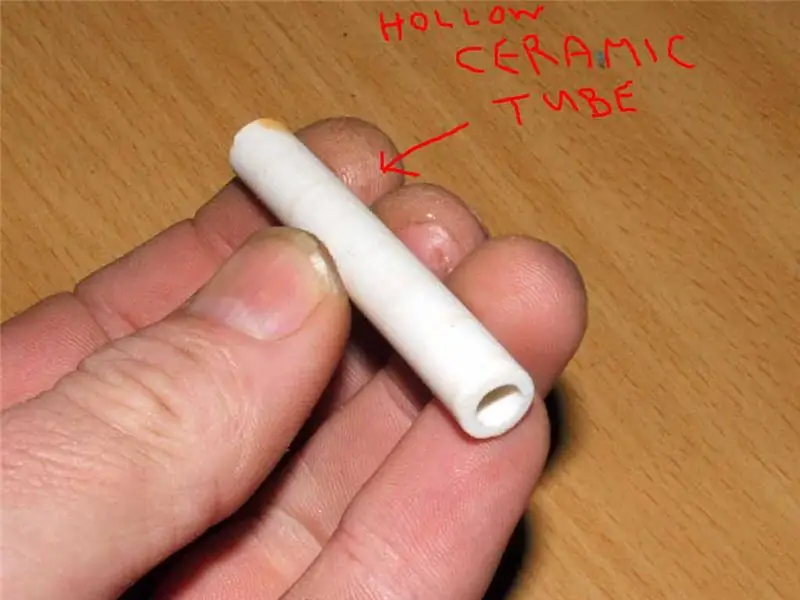
Pensé que este tubo sería lo mejor desde el tocino y los huevos, no me decepcionó:) Esta es una de las varillas aislantes que se usan para separar los elementos calefactores entre sí dentro de las pistolas de aire caliente. El elemento pasó por el exterior de esta varilla. Apunté a colocar el elemento dentro de la varilla y que entrara aire frío y saliera aire súper caliente. Todavía no tenía ni idea de cómo se uniría todo esto… excepto algunas imágenes locas de cómo podría hacer y lucir el producto final.
Paso 7: El elemento y el tubo de cerámica
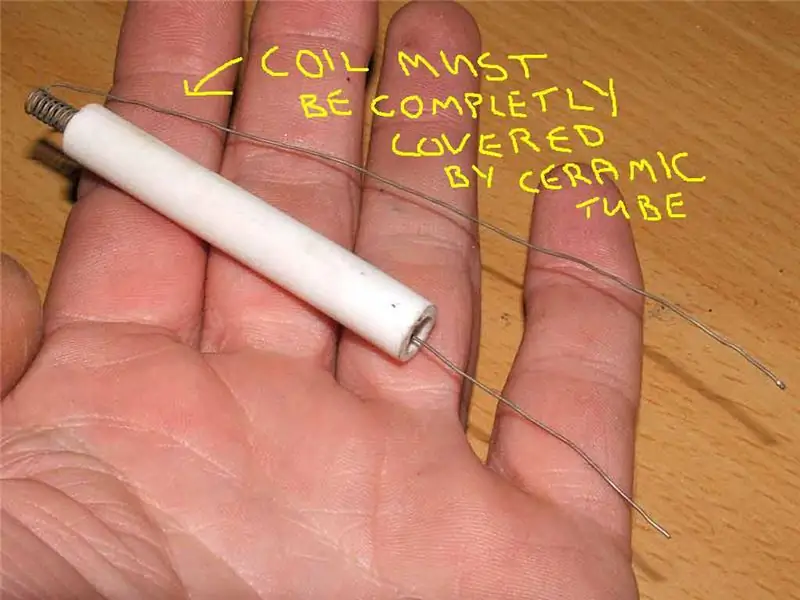
Este es esencialmente el extremo operativo de todo. DESCRIPCIÓN GENERAL: Primero que nada, necesitaba un elemento calefactor. Pensé que podría reducir el tamaño de los elementos calefactores rotos clasificados para 240 voltios de CA para que quepan dentro de la tubería de cerámica y que funcionen silenciosamente bien con doce voltios. El amperaje era un problema por el que preocuparse y se podía solucionar variando la longitud de la bobina para obtener la salida de calor deseada. Demasiada bobina y tendré que usar más voltios y / o amperios … muy poco y sobrecaliento la bobina y rompo el enlace. Experimenté con algunas longitudes de bobina usando la energía de mis pequeñas baterías de plomo-ácido de 12 voltios y encontré una longitud que emitía suficiente calor (145 grados centígrados) como cifra inicial. Inserté la bobina en el tubo de cerámica, asegurándome de que no tuviera curvas cerradas y de que saliera de la bobina longitudes suficientemente largas de alambre recto. Los largos fueron para darme suficiente espacio para jugar cuando vaya a colocar a este bebé dentro del eje de mi soldador. Además, las longitudes largas me permitieron colocar el elemento calefactor más lejos del mango de la plancha. Parecería que todo el hierro de soldadura fue hecho para ser diseñado en reversa para su uso con flujo de aire caliente. Noto que otras personas en la web han tenido pensamientos similares.
Paso 8: El Gutz
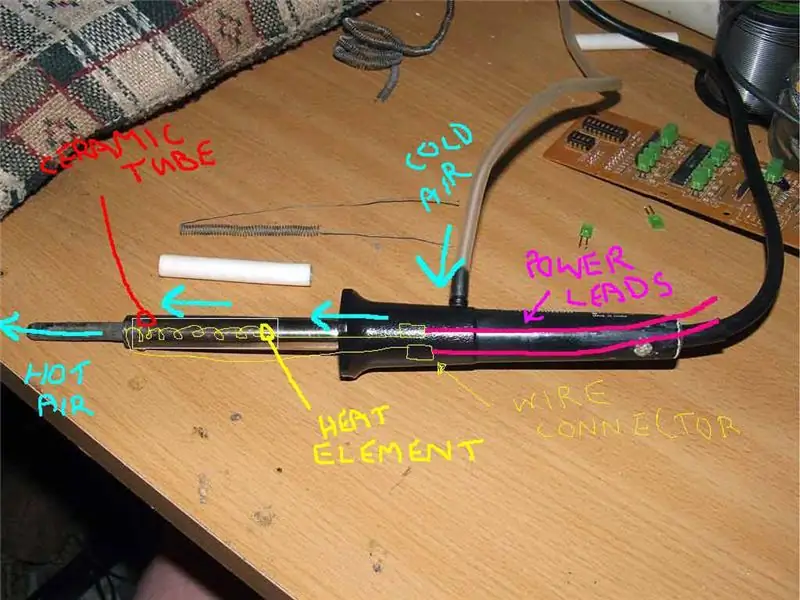
Los fundamentos de todo. No mucho realmente. Pero malditamente efectivo más allá de lo que esperaba. DESCRIPCIÓN GENERAL: Con el elemento dentro del eje de soldadura, noté que tenía que aislar el cable que corría por el exterior del eje de la carcasa de metal. Tenía varios tamaños diferentes de tubos de aislamiento térmico que solucionarían este problema. A continuación, tuve que remodelar ligeramente el eje en una forma ovalada para que se ajustara al elemento calefactor de cerámica con el tubo de aislamiento térmico de alambre agregado. El siguiente paso fue ver si aún podía pasar aire a través del elemento con el aislamiento agregado. Pude ver la luz a través del otro lado del pozo que me dijo que todo estaba bien. Ahora lo fácil era usar los conectores de terminales de cables que utilizaba la plancha para unir los extremos del elemento calefactor a los extremos del cable de alimentación de la batería. Usé el cable de CA de 240 voltios que se usaba anteriormente para la plancha, ya que quería un cable grueso capaz de manejar algunos amperios.
Paso 9: la boquilla
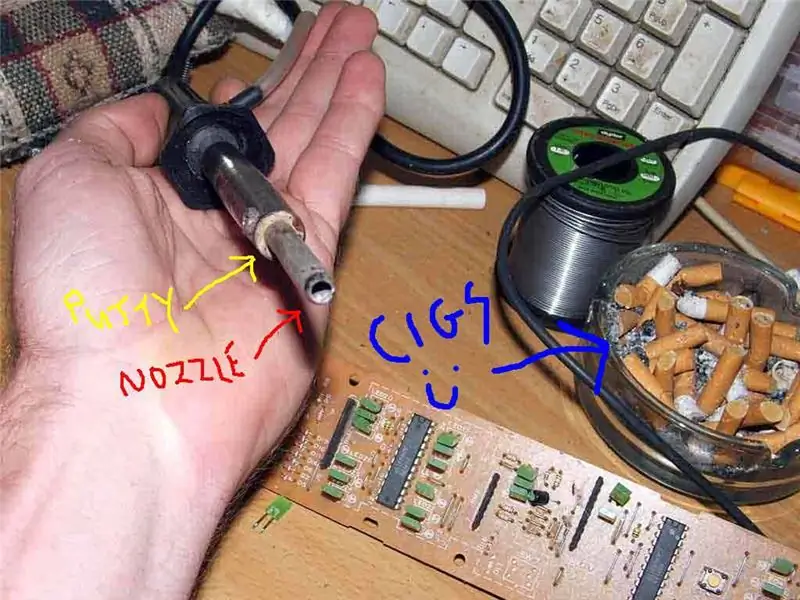
La boquilla es lo que solía estar dentro de la plancha. El elemento calefactor para el suministro de CA de 240v se envolvió alrededor de esto y la varilla calefactora de cobre utilizada para soldar cosas se sentó dentro del tubo hueco. agujero e inserte un poco de tubería una vez que la unidad esté junta. Posteriormente se bombearía aire a través de este tubo. Era importante hacerlo bien, así que utilicé calibradores y algunas marcas para obtener la longitud correcta. El siguiente problema que encontré fue conseguir una boquilla para la punta. Invertí el eje interior que se usaba anteriormente para sostener el elemento calefactor y dremelled la brida y encajó perfectamente. ¡Ahora tengo una boquilla! El siguiente paso fue usar una boquilla de mi acuario que encajaría en el mango y también en el tubo de plástico por el que fluirá aire. Perforé un agujero donde una "X" marcaba el lugar, teniendo cuidado de no tener demasiada presión sobre el taladro. Habría hecho esto sin la tripa, pero sentí que podría salirse con la suya sin perforar las entrañas si hubiera tenido cuidado. Este arreglo funcionó, pero es solo temporal, ya que quiero ver si el concepto funcionó. Luego agregaré algo de retención mecánica aquí usando una boquilla de rosca o algo así. Con el soldador casi completamente unido, necesitaba abordar el problema de la entrada de aire en la cosa. No tenía una bomba de aire utilizada para un acuario. Tengo un acuario, pero no los uso, son tan ineficientes. Lo que sí tengo son los sopladores de aire de las pistolas de aire caliente que obtuve del basurero. Estos bebés son enormes en comparación con el pequeño tubo que tengo que encontrar con el soldador.
Paso 10: Clavija cuadrada en un agujero redondo
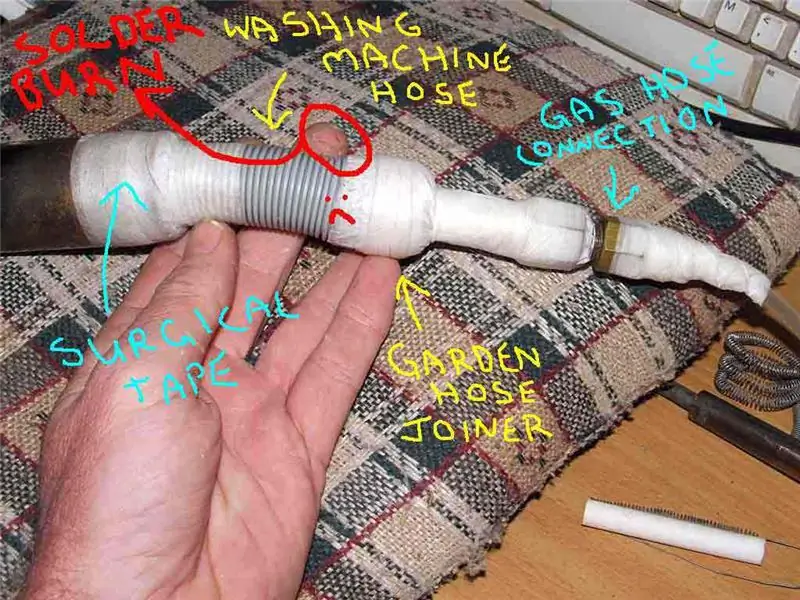
Mi mayor desafío fue decidir cómo encajar mi manguera pequeña en una salida de soplador enorme con lo que tenía en la casa. RESUMEN: Viajé al cobertizo trasero y reuní todos los tubos y bitz que pensé que serían útiles y comencé a colocar una clavija cuadrada en un agujero redondo. Terminé usando un trozo de tubo de una lavadora vieja, un conector de manguera de jardín, un pequeño trozo de tubo de 1/4 de pulgada y una boquilla de gas de latón y montones de cinta quirúrgica. Encendí el soplador de aire y recibí una agradable brisa de aire fuerte al final del tubo. El diseño se arreglará más adelante con respecto a las obstrucciones del flujo de aire, etc. que existen con este artilugio. Mi objetivo es trabajar en el efecto venturi para aumentar aún más la salida de aire en la boquilla sin aumentar la velocidad del ventilador. Luego, simplemente conecté el tubo pequeño en el pezón que sobresale del mango del soldador.
Paso 11: todas las cosas están aquí
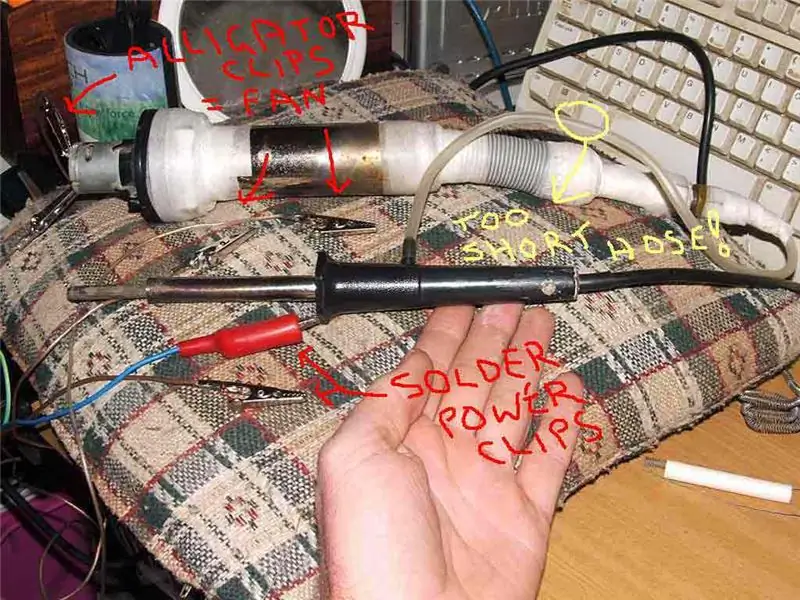
El soplador y el soldador es todo lo que hay para esto.
Paso 12: soplador de velas:)
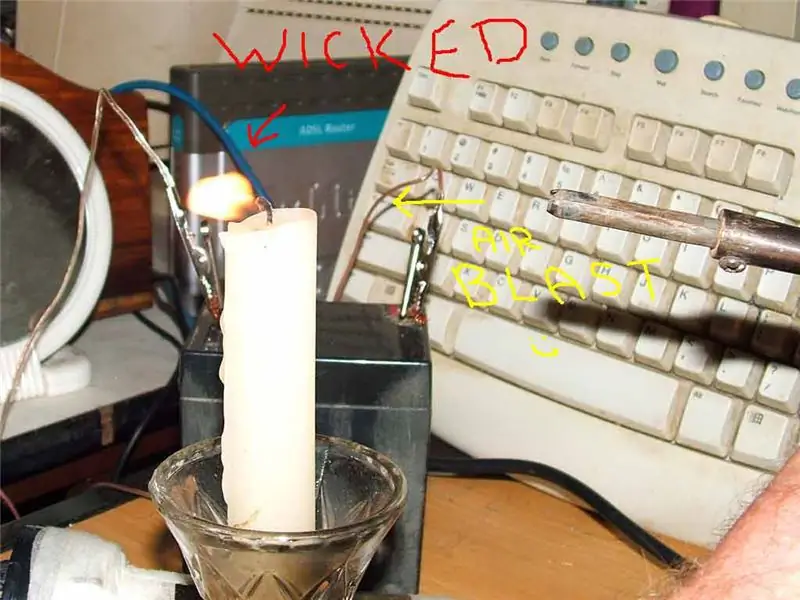
La fuerza del aire caliente es la clave para eliminar todo ese buen calor del elemento calefactor dentro del soldador. La prueba y el error deberían proporcionarle la cantidad correcta de flujo de aire a través del elemento calefactor que calentará efectivamente el aire frío que ingresa a la cámara de calentamiento y sale de la boquilla a la temperatura deseada. Un flujo de aire demasiado rápido y el aire no tendrá tiempo suficiente para calentarse a los niveles deseados. Creo que tuve suerte ya que no tuve que preocuparme por esto. El beneficio adicional de tener una bobina utilizada para calentar con aire que fluye hacia la cámara que contiene el elemento calefactor, es que la turbulencia resultante distribuye el aire de manera más uniforme reduciendo las pérdidas de energía durante el calentamiento del aire frío.
Paso 13: Fuente de alimentación regulada
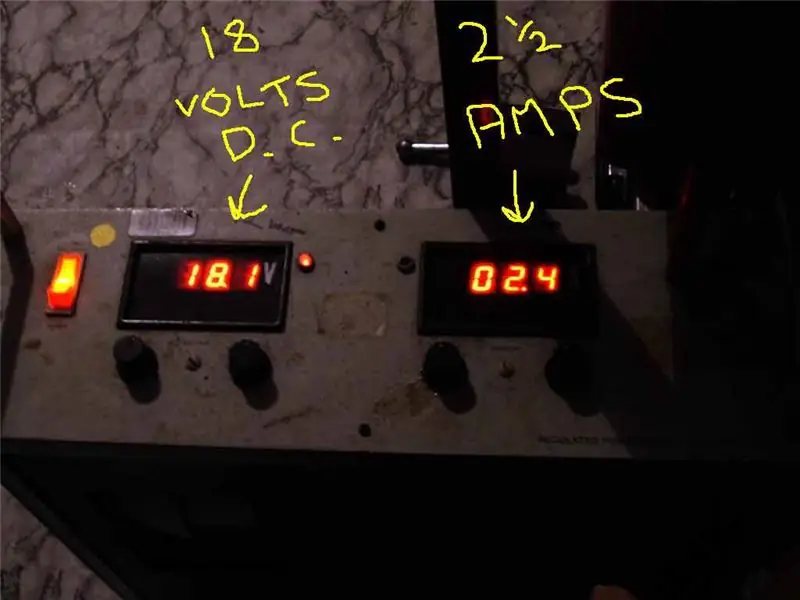
Este viejo fiel ex R. A. A. F. La unidad vivirá más allá de mis años. Tantas funciones y fabricado en Australia. Estas son las estadísticas operativas máximas deseadas que alcanzaron los 310 grados centígrados. Me tomó menos de 15 segundos alcanzar esta temperatura desde un comienzo en frío. Mucho mejor que esperar varios minutos a que se caliente un soldador estándar. Observo que a 16 voltios, la temperatura máxima era de 270 grados centígrados impares. A 18 voltios, la temperatura máxima fue de 310 grados centígrados. Entonces puedo calcular las matemáticas en cuanto a predecir los rangos de temperatura que salen de la boquilla a una variedad de voltajes y amperaje. La distancia lineal entre estos rangos está determinada, por supuesto, por el calibre del cable del elemento, su longitud y también el CFM del flujo de aire a través de la boquilla.
Paso 14: Temp # 1
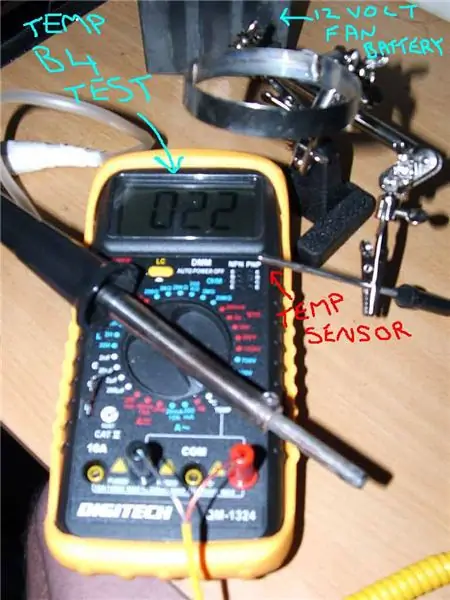
Temperatura de la habitación. Listo para el gran espectáculo … jajaja
Paso 15: Temp # 2
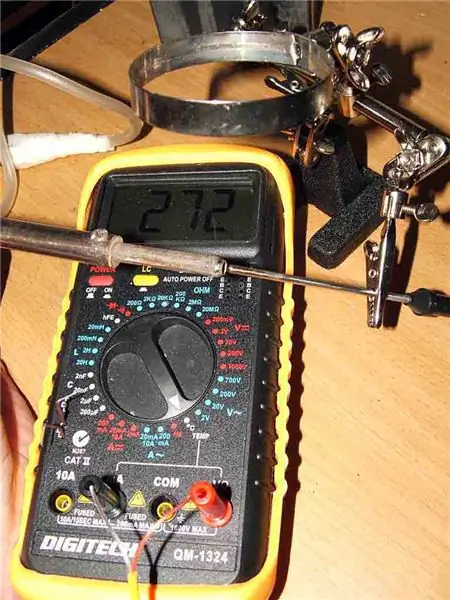
Encendido y subiendo. Ver cómo aumentaban esos números fue una verdadera prisa. Noté que el elemento dentro del eje aún no brillaba en absoluto cuando miré hacia arriba, lo que me mostró que podía alcanzar temperaturas sustancialmente más altas antes de que fallara el elemento, usando el cable del elemento calefactor de las pistolas de aire caliente de pintura desintegradas. Una vez que haya hecho una pieza de trabajo más permanente, experimentaré con varios diámetros de boquilla, ya que creo que una boquilla más pequeña sería excelente para eliminar componentes individuales y una boquilla más ancha para chips IC y demás.
Paso 16: Temp # 3
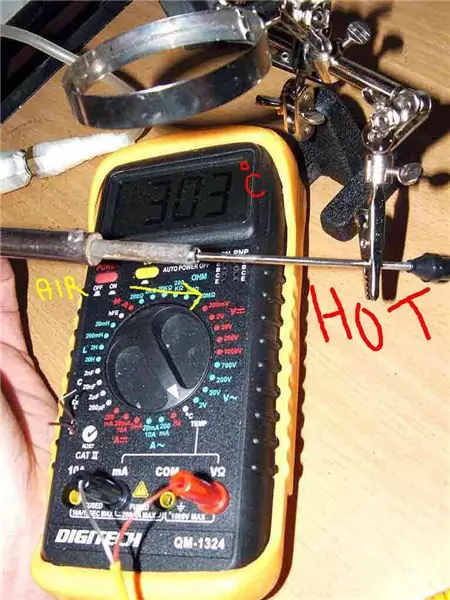
Tengo más de 310 grados centígrados. Podría haber obtenido más, pero no era necesario para lo que pretendía usar a este bebé. También me estaba volviendo demasiado paranoico al ver cómo aumentaban esos números … rofl DESCRIPCIÓN GENERAL: Encendí el ventilador y encontré varias fugas de aire. Los sellé con masilla de fraguado sólido. Se acerca el momento de la verdad. Ahora necesitaba una fuente de energía. Pensé en pequeños transformadores, pero quería un suministro variable de voltaje y amperaje, para poder calcular las condiciones máximas de funcionamiento. Recuperé mi viejo regulador de voltaje AUSTRALIAN MADE (ex stock de R. A. A. F.) y lo conecté a mi plancha. Todas las cosas que se fabrican hoy que obtenemos están fabricadas en China y no son fiables como el infierno. Este bebé fue hecho para durar y trabajar. Tenía el ventilador conectado a mi paquete de baterías separado del elemento calefactor de soldadura. Las razones eran obvias:) Encendí un cigarrillo y me preparé para lo peor … Comencé con un voltaje de CC bajo … los amperios son calibrados automáticamente por el regulador. Hice apartar mi multímetro para medir la temperatura del aire caliente. Para abreviar la historia (risas), a 16 voltios CC y poco más de 2 amperios… la temperatura alcanzada fue de 275 grados centígrados… ¡¡¡KEWLIES !!! Alcancé mi temperatura objetivo. Corté alambre de soldadura de 1 mm como queso suizo. Pude quitar los LED de una placa PCB sin ni siquiera freírlos o mis dedos que sostenían los LED del otro lado de la placa. El eje de metal del soldador era mucho MÁS FRÍO que cuando funcionaba por debajo de 240 voltios. Podría tocar el eje de metal sin quemarme los dedos. Sin embargo, hacía bastante calor donde está el elemento, pero aún más frío sustancialmente. ¿Qué hace que la mía sea diferente de las otras creaciones que vi en la WWW? Tengo un elemento calefactor en espiral con una gran superficie de buen calor (risas) que tiene aire frío que pasa directamente a través de ellos. Las otras unidades que vi usan el elemento calefactor del soldador original, una varilla conductora de cobre que absorbe el calor del elemento y envía el calor a la punta, un poco de malla de alambre en la cavidad de aire para aumentar la exposición de la superficie al aire frío expuesto al calor.. Eliminé todas esas barreras conductoras y aumenté la eficiencia a montones.
Paso 17: fusión del alambre de soldadura
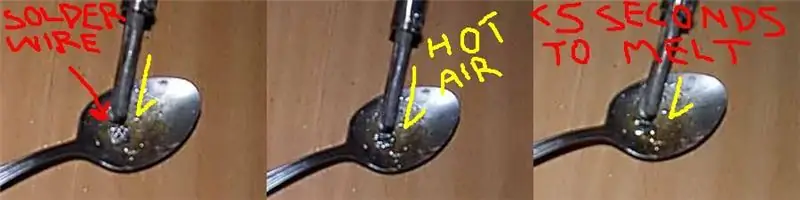
Derretí esta bola de alambre de soldadura como un helado bajo el sol de verano
Paso 18: primer trabajo
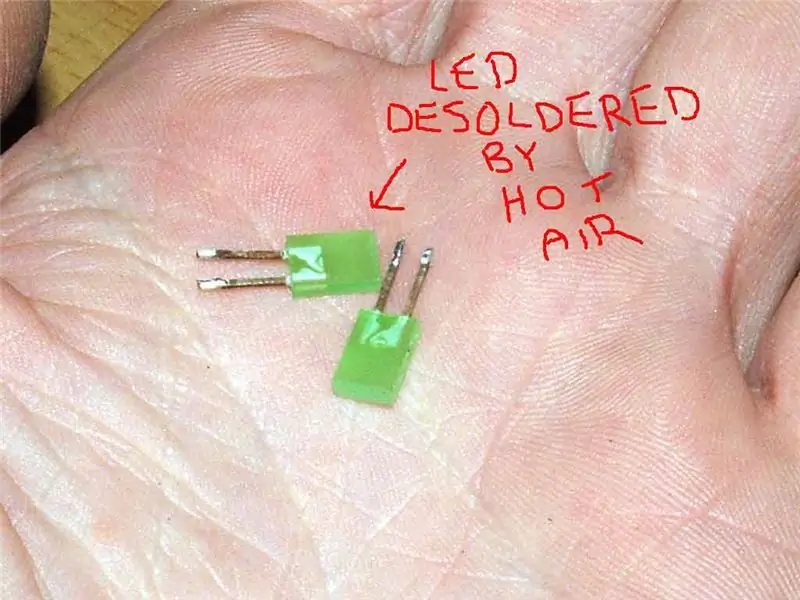
Los quité de un PCB viejo en un abrir y cerrar de ojos. DESCRIPCIÓN GENERAL: Una vez que obtenga un tubo de plástico más largo y vuelva a trabajar este prototipo en una disposición más permanente, tendré suficientes piezas de repuesto para cuidar a este bebé durante los próximos años. Las mejoras que haré son configurar los ajustes de temperatura a través de ollas de ajuste y usar mis otros bitz y piezas para configurar un panel LCD con configuraciones que se muestran como temperatura, voltaje y amperaje y, por supuesto, algunos fusibles y tal vez un condensador en el motor. Ya conozco la condición operativa media y puedo ajustar en consecuencia desde allí. Un punto para recordar es que cuando apague la unidad, apague el elemento primero, deje que el aire pase por un minuto para enfriar la unidad. Implementaré un temporizador para este poco más tarde. Por supuesto que no puedo hacer esto sin un soldador que funcione, pero ahora tengo uno …
Recomendado:
Batería de litio LiFePo4 de 12 v y 18 amperios para bricolaje: 10 pasos (con imágenes)
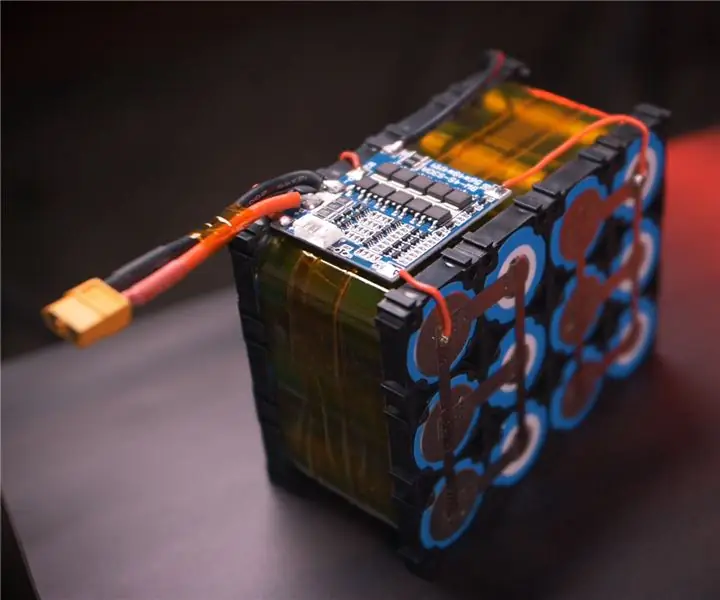
Batería de litio LiFePo4 de 12 V y 18 amperios para bricolaje: ¡Oye! todos Mi nombre es Steve Hoy voy a mostrar cómo construyo este paquete de baterías 12V 4S3P LiFePo4 con BMS y carga de equilibrio Haga clic aquí para ver el video
SOLDADURA SMD 101 - USANDO PLACA CALIENTE, SOPLADOR DE AIRE CALIENTE, PLANTILLA SMD Y SOLDADURA MANUAL: 5 Pasos
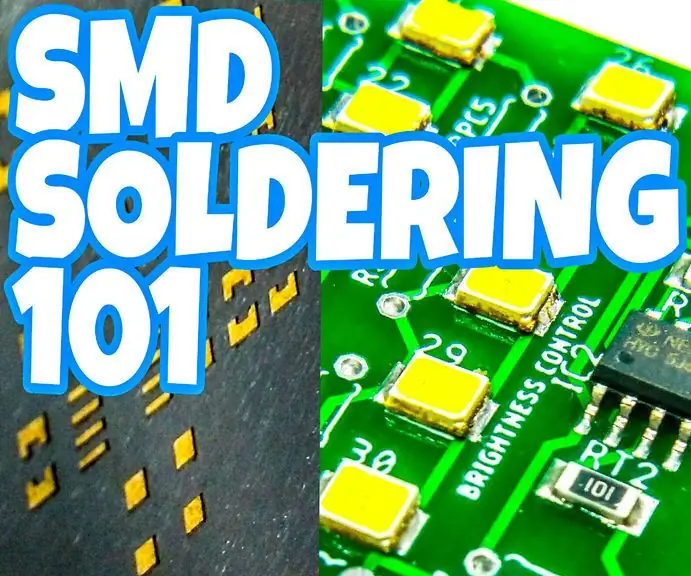
SOLDADURA SMD 101 | USANDO PLACA CALIENTE, SOPLADOR DE AIRE CALIENTE, PLANTILLA SMD Y SOLDADURA MANUAL: ¡Hola! Es bastante fácil soldar … Aplique un poco de fundente, caliente la superficie y aplique soldadura. Pero cuando se trata de soldar componentes SMD, se requiere un poco de habilidad y algunas herramientas y accesorios. En este Instructables, te mostraré mi
Hack de la estación de reflujo de aire caliente 858D SMD: 10 pasos (con imágenes)
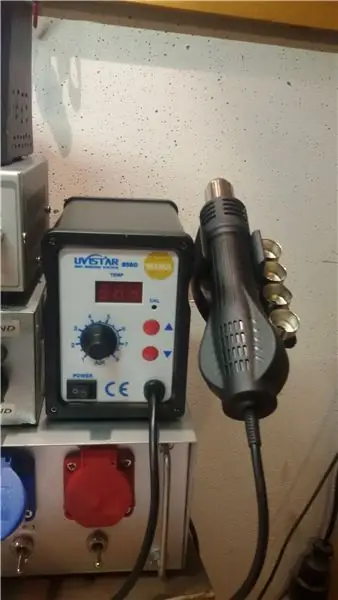
858D SMD Hot Air Reflow Station Hack: Tengo un pequeño laboratorio electrónico, donde reparo aparatos electrónicos rotos y hago algunos pequeños proyectos de hobby. Debido a que hay cada vez más material SMD por ahí, era hora de conseguir una estación de reflujo SMD adecuada. Miré un poco a mi alrededor y descubrí que el 858D era
Medidor de potencia, amperios y voltios versátil: 6 pasos (con imágenes)
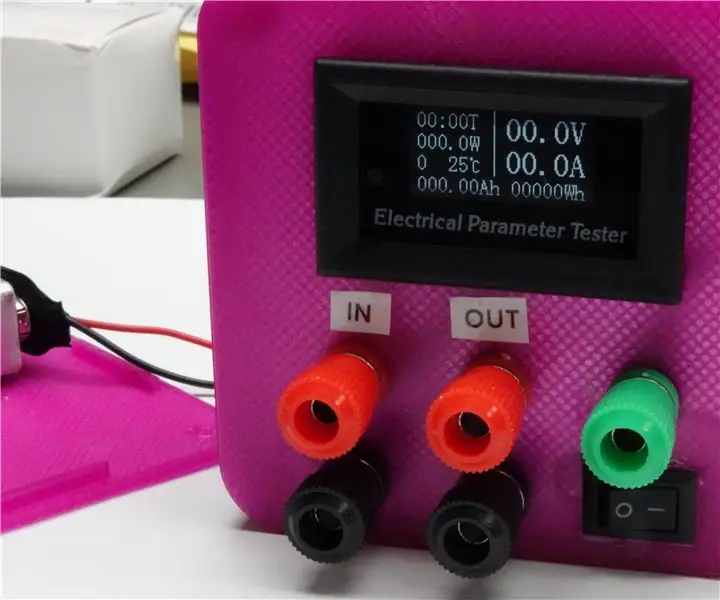
Medidor de potencia, amperios y voltios versátil: los multímetros son adecuados para muchos propósitos. Pero, por lo general, solo miden un valor a la vez. Si nos ocupamos de medidas de potencia, necesitamos dos multímetros, uno para voltaje y el segundo para Ampere. Y si queremos medir la eficiencia, necesitamos cuatro
Hacer un cuchillo caliente con un soldador: 4 pasos (con imágenes)
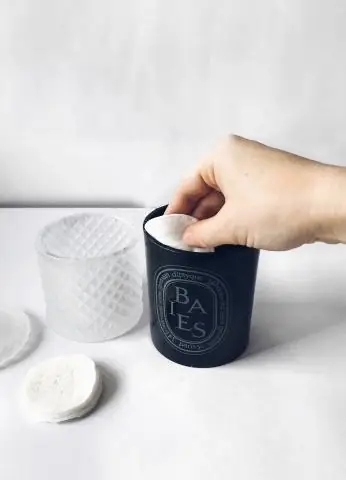
Haga un cuchillo caliente con un soldador: ¿Tiene problemas para cortar plásticos con un cuchillo x-acto común? ¡Entonces aquí hay un mod de herramienta simple que puedes hacer, convertir un soldador viejo y una hoja x-acto en un cuchillo caliente! Esta idea de cuchillo caliente no es realmente mía, encontré esta idea hecha por alguien