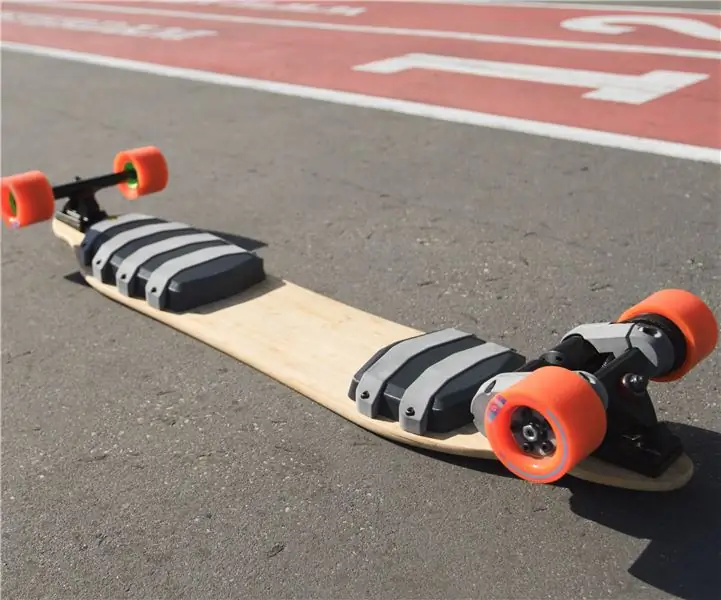
Tabla de contenido:
2025 Autor: John Day | [email protected]. Última modificación: 2025-01-23 14:40
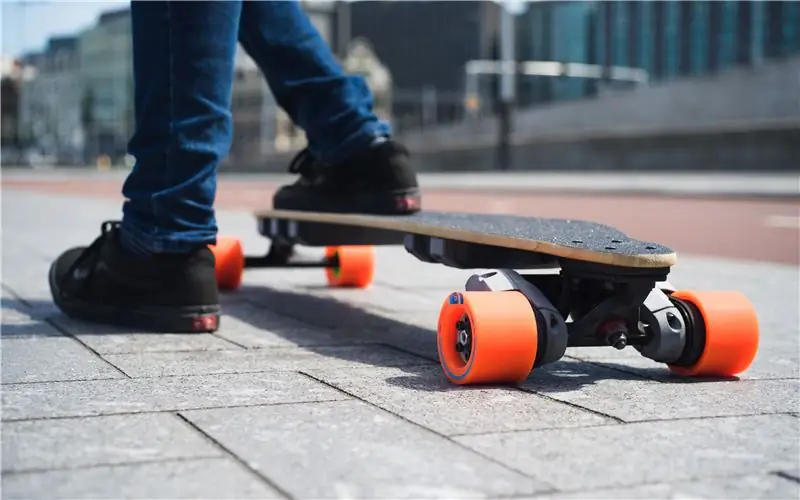
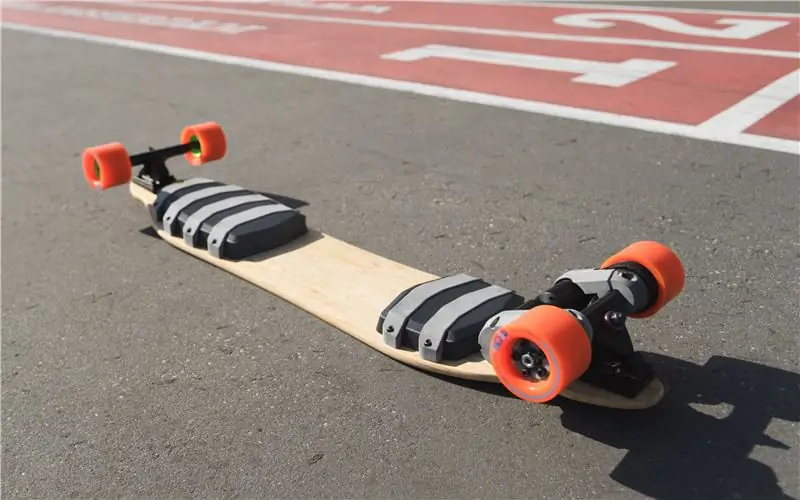
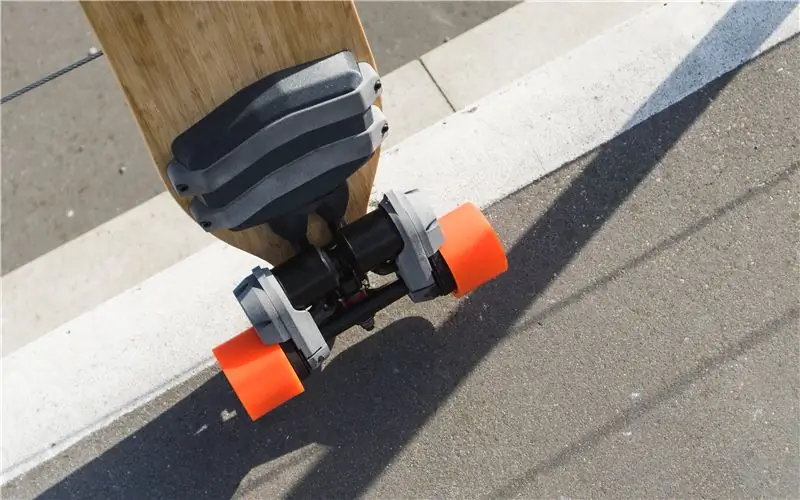
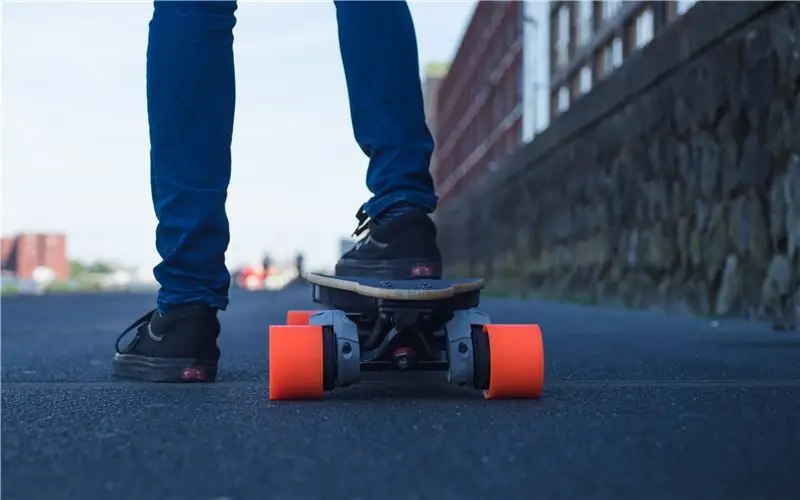
Este Instructable es una descripción general del proceso de construcción del Fusion E-Board que diseñé y construí mientras trabajaba en 3D Hubs. El proyecto fue encargado para promover la nueva tecnología HP Multi-Jet Fusion ofrecida por 3D Hubs, y para mostrar múltiples tecnologías de impresión 3D y cómo se pueden combinar de manera efectiva.
Diseñé y construí un longboard motorizado eléctrico, que se puede usar para viajes cortos a moderados o combinar con el transporte público para ofrecer un rango de viaje mucho más amplio. Tiene una alta velocidad máxima, es muy maniobrable y se transporta fácilmente cuando no está en uso.
Paso 1: proceso de diseño
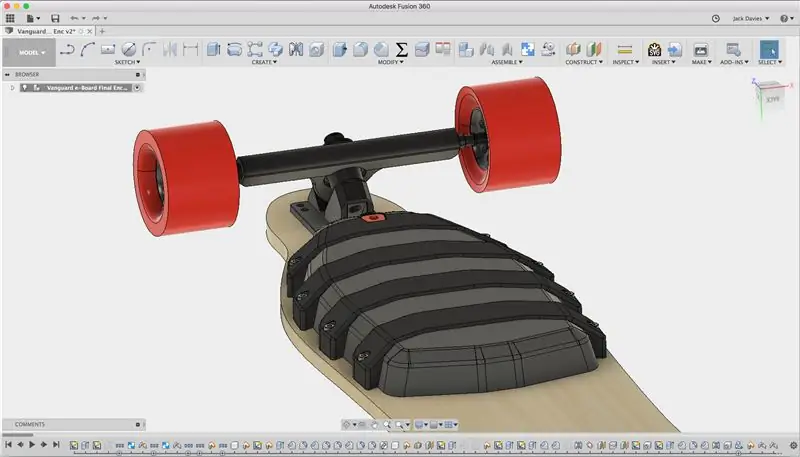
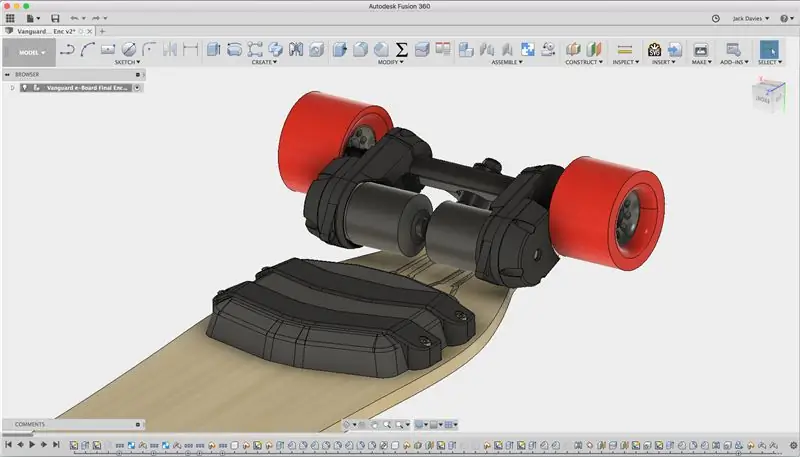
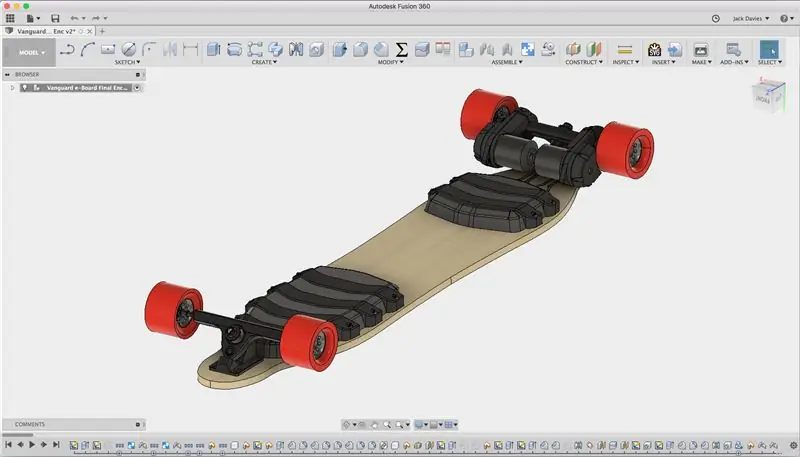
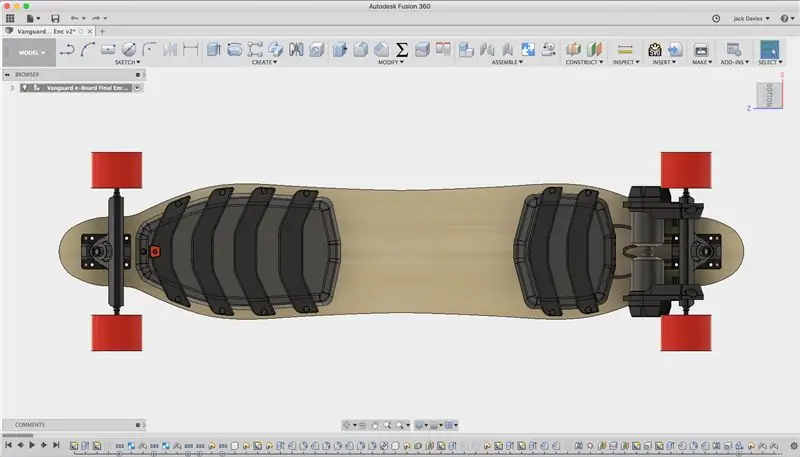
Comencé el proyecto identificando los principales componentes estándar del longboard; camiones, cubierta y ruedas. Estas eran partes listas para usar, así que las usé como punto de partida del diseño. La primera etapa fue diseñar el tren motriz, esto incluye los soportes del motor, la configuración de los engranajes e incluyó algunas modificaciones a los camiones. El tamaño y la posición de los soportes del motor determinarían el tamaño y la ubicación de los gabinetes, por lo que era importante que esto se completara primero. Calculé los requisitos de par y velocidad máxima deseados, lo que me permitió seleccionar los motores y la batería para la placa. También se calculó la relación de transmisión y se seleccionaron los tamaños de las poleas, junto con la longitud de la correa de transmisión. Esto me permitió calcular el tamaño correcto de los soportes del motor, lo que aseguró una correa bien tensada.
La siguiente etapa fue diseñar los gabinetes de la batería y el controlador de velocidad (ESC). La plataforma seleccionada está compuesta predominantemente de bambú, por lo que es bastante flexible y se dobla sustancialmente en el medio. Esto tiene las ventajas de ser cómodo de conducir, ya que absorbe los baches de la carretera y no los transfiere al ciclista. Sin embargo, esto también significa que se necesita un gabinete dividido para albergar la batería y los componentes electrónicos, ya que un gabinete de longitud completa no podría flexionarse con la placa y haría contacto con el suelo durante el funcionamiento. Los controladores de velocidad electrónicos (ESC) se colocaron más cerca de los motores debido a limitaciones eléctricas. Debido a que los motores están conectados a través de los camiones, la posición cambia durante los giros, por lo que el gabinete tuvo que diseñarse para permitir el espacio libre de los motores.
El sistema de batería se colocó en el otro extremo de la plataforma y albergaba la electrónica relacionada con la energía. Esto incluía el paquete de baterías, compuesto por 20 celdas de iones de litio 18650, el sistema de gestión de la batería, el interruptor de encendido / apagado y el enchufe de carga.
Utilicé Autodesk Fusion360 para todo el proceso de diseño, este software me permitió modelar rápidamente componentes dentro del ensamblaje principal, lo que aceleró considerablemente el tiempo de desarrollo. También utilicé las funciones de simulación en Fusion360 para asegurarme de que las piezas fueran lo suficientemente fuertes, especialmente los soportes del motor. Esto me permitió reducir realmente el tamaño de los soportes, ya que pude verificar los requisitos de resistencia y deflexión y eliminar el material sin dejar de mantener un factor de seguridad adecuado. Una vez finalizado el proceso de diseño, fue muy fácil exportar las piezas individuales para la impresión 3D.
Paso 2: tren motriz
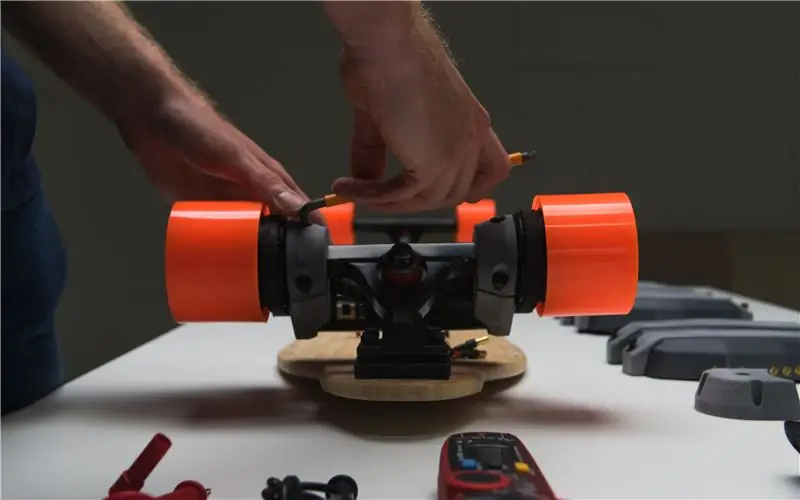
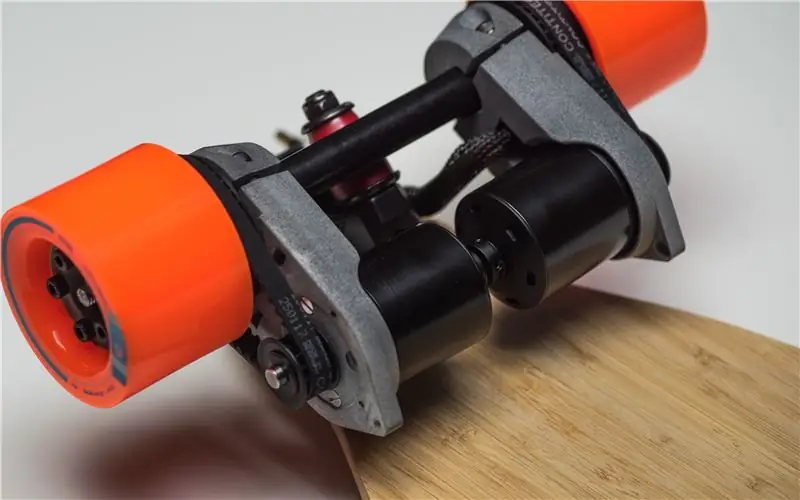
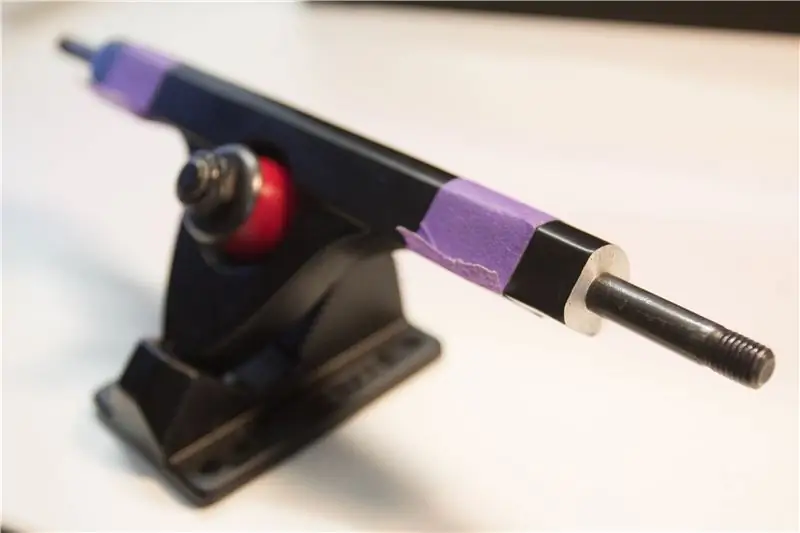
Primero completé la construcción del tren motriz, para asegurar el espacio adecuado para la caja de la electrónica. Seleccioné camiones Caliber para usar, ya que tienen un perfil cuadrado que era perfecto para sujetar los soportes del motor. Sin embargo, el eje era un poco demasiado corto para permitir que los dos motores se usaran en el mismo camión, por lo que necesitaba extenderlo para permitir que las ruedas encajaran.
Logré esto cortando parte del cuerpo de suspensión del camión de aluminio, exponiendo más del eje de acero. Luego corté la mayor parte del eje, dejando alrededor de 10 mm que luego pude enhebrar con un dado M8.
Luego, se podría atornillar un acoplador y agregar otro eje roscado, extendiendo efectivamente el eje. Usé compuesto de retención Loctite 648 para asegurar permanentemente el acoplador y el eje nuevo para asegurar que no se desenrosque durante el uso. Esto permitió que los dos motores encajaran en el camión y proporcionó suficiente espacio libre para las ruedas.
El tren motriz se imprimió principalmente con la tecnología HP Multi-Jet Fusion, para garantizar la rigidez y la resistencia durante las altas aceleraciones y frenadas, donde se transferirían las mayores fuerzas.
Se diseñó una polea especial para bloquear en las ruedas traseras, que luego se conectó a la polea del motor con una correa HTD 5M. Se agregó una cubierta impresa en 3D para brindar protección al ensamblaje de la polea.
Paso 3: Recintos de nervios
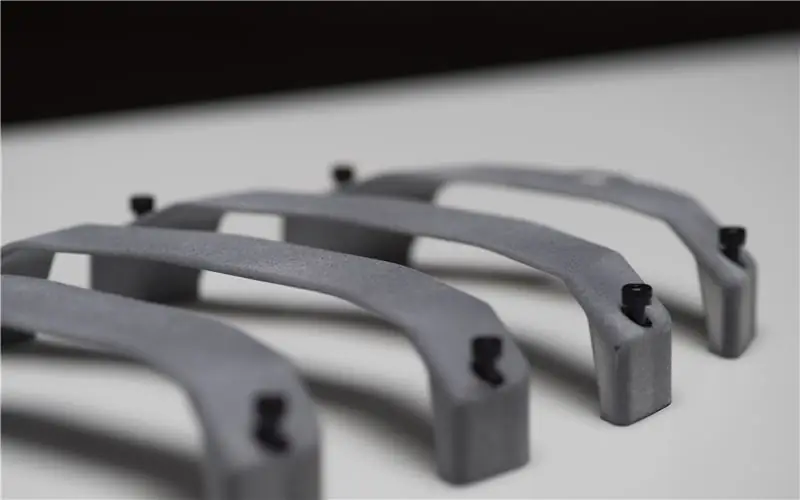
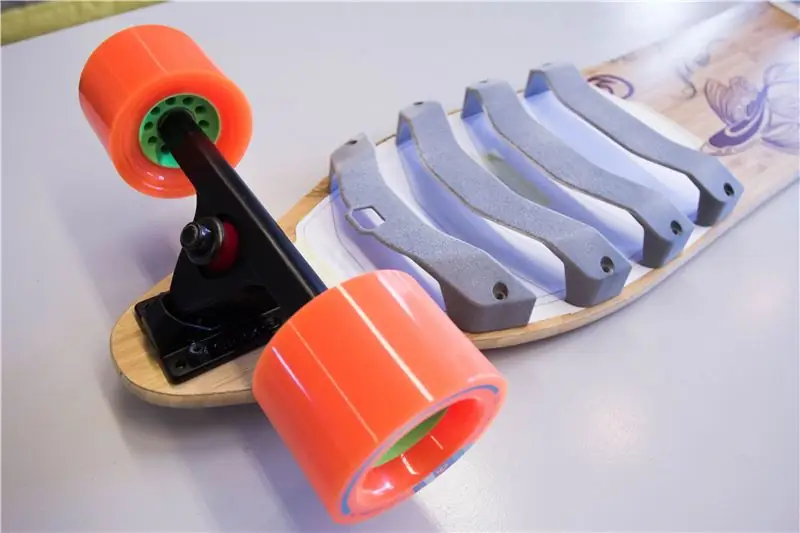
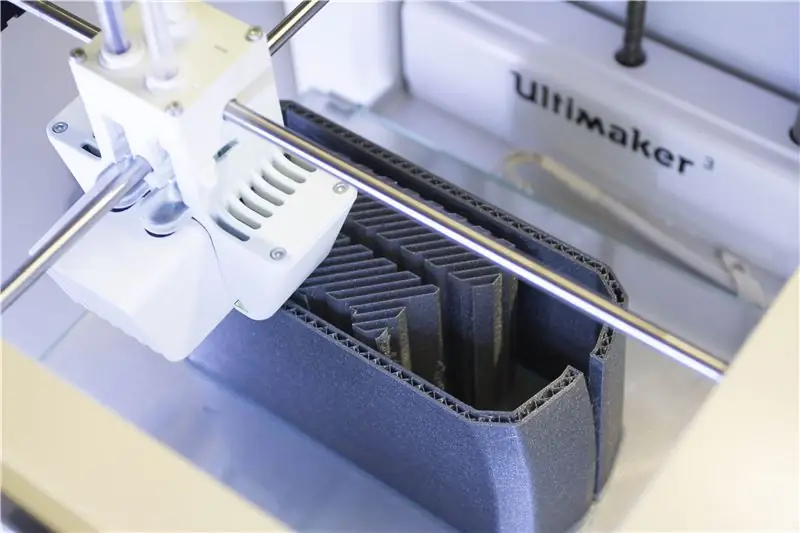
Una de las principales decisiones de diseño que tomé fue separar los gabinetes, lo que resultó en una apariencia limpia y permitió que la plataforma flexible funcionara sin ninguna rigidez adicional de los gabinetes. Quería transmitir los aspectos funcionales de la tecnología HP Multi Jet Fusion, por lo que decidí imprimir en FDM el cuerpo principal de los gabinetes, lo que redujo los costos, y luego usé las piezas de HP para sujetarlas y sujetarlas a la plataforma. Esto proporcionó una estética interesante a la vez que muy funcional.
Los gabinetes impresos FDM se dividieron por la mitad para ayudar en la impresión, ya que el material de soporte podría eliminarse de la superficie exterior. La línea de división se colocó cuidadosamente para asegurar que quedara oculta por la parte HP cuando se sujetaba a la placa. Se agregaron orificios para las conexiones del motor y se pegaron conectores de bala chapados en oro en su lugar para
Se incrustaron inserciones roscadas en la plataforma de bambú para asegurar los recintos a la tabla, y se lijaron al ras de la superficie de la tabla para garantizar que no hubiera espacio entre la plataforma y la carcasa.
Paso 4: Electrónica
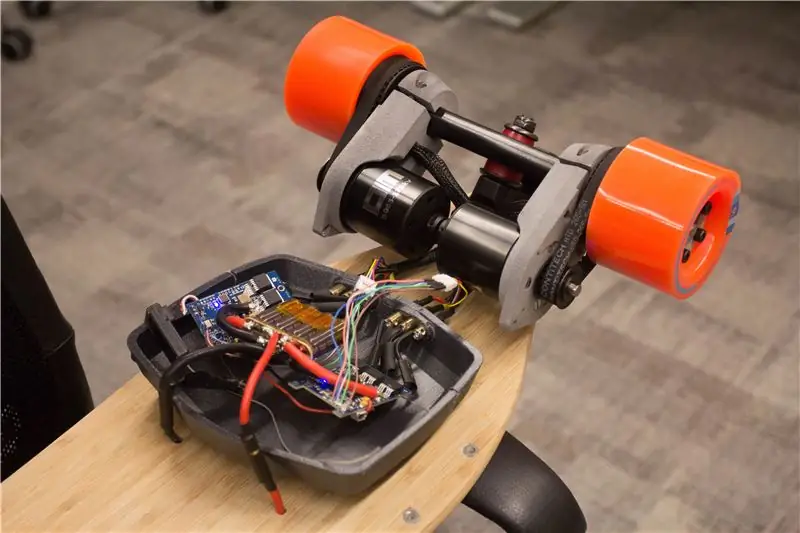
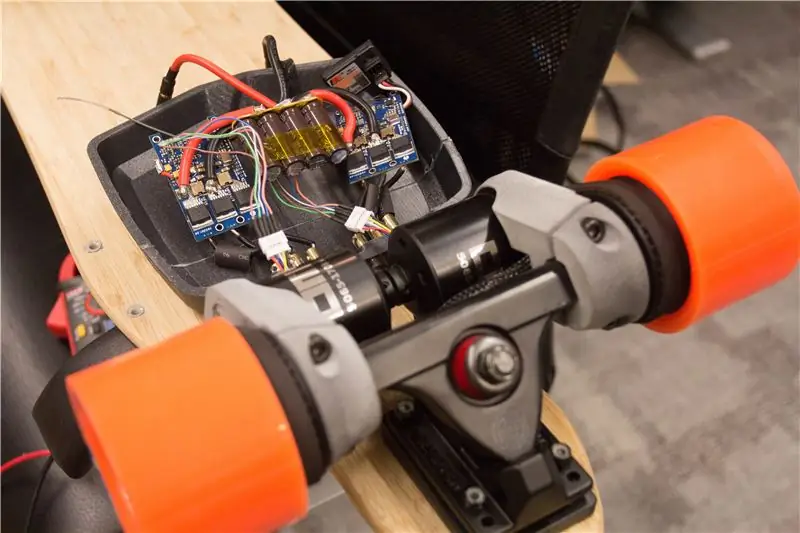
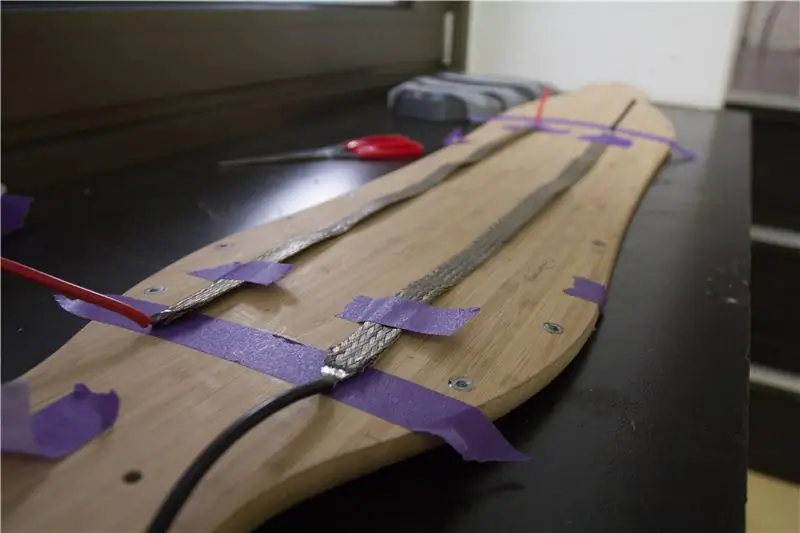
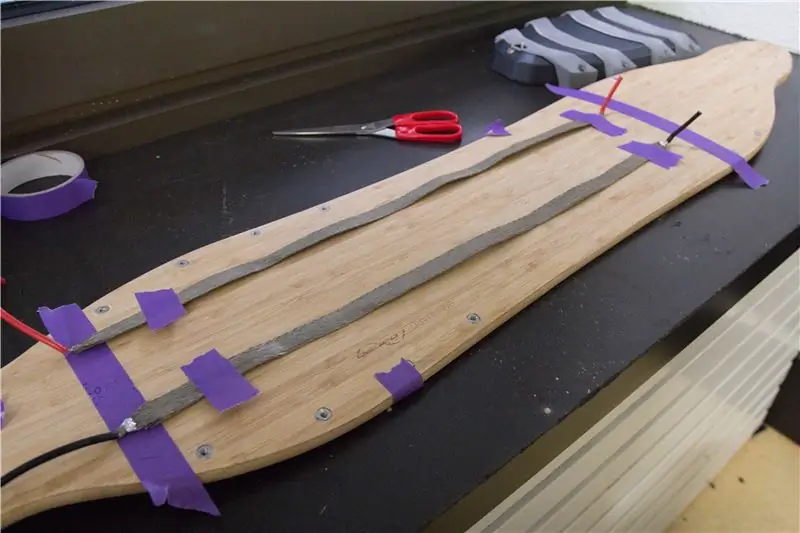
La electrónica se eligió cuidadosamente para garantizar que la placa fuera potente pero también intuitiva de usar. Esta placa podría ser potencialmente peligrosa si ocurriera algún mal funcionamiento, por lo que la confiabilidad es un factor muy importante.
El paquete de baterías se compone de 20 celdas individuales de iones de litio 18650 que se sueldan por puntos para formar un paquete de 42v. 2 celdas están soldadas en paralelo y 10 en serie; las celdas que utilicé fueron Sony VTC6. Usé un soldador por puntos para soldar las lengüetas de níquel para formar el paquete, ya que la soldadura crea demasiado calor que puede dañar la celda.
La energía de la caja de la batería se transfirió a la caja del controlador de velocidad utilizando un cable trenzado plano que se colocó justo debajo de la cinta de agarre en la parte superior de la plataforma. Esto permitió que los cables estuvieran "ocultos" y eliminó la necesidad de tender cables en la parte inferior, lo que se habría visto feo.
Como se trata de una placa de motor dual, se requieren dos controladores de velocidad para controlar independientemente cada motor. Usé el controlador de velocidad VESC para esta construcción, que es un controlador diseñado específicamente para patinetas eléctricas que lo hace muy confiable para este uso.
Los motores utilizados son 170kv 5065 out-runners que pueden producir 2200W cada uno, que es mucha potencia para esta placa. Con la configuración de engranajes actual, la velocidad máxima de la placa es de alrededor de 35 MPH y se acelera muy rápidamente.
La última etapa fue crear un control remoto para controlar el tablero. Se prefirió un sistema inalámbrico debido a la facilidad de operación. Sin embargo, era importante garantizar una alta confiabilidad de la transmisión, ya que una caída en la comunicación podría tener serios problemas de seguridad, especialmente a altas velocidades. Después de probar algunos protocolos de transmisión de radio, decidí que la frecuencia de radio de 2.4GHz sería la más confiable para este proyecto. Utilicé un transmisor de coche RC disponible en el mercado, pero reduje significativamente el tamaño al transferir la electrónica a una pequeña caja de mano que estaba impresa en 3D.
Paso 5: Tablero terminado y video promocional
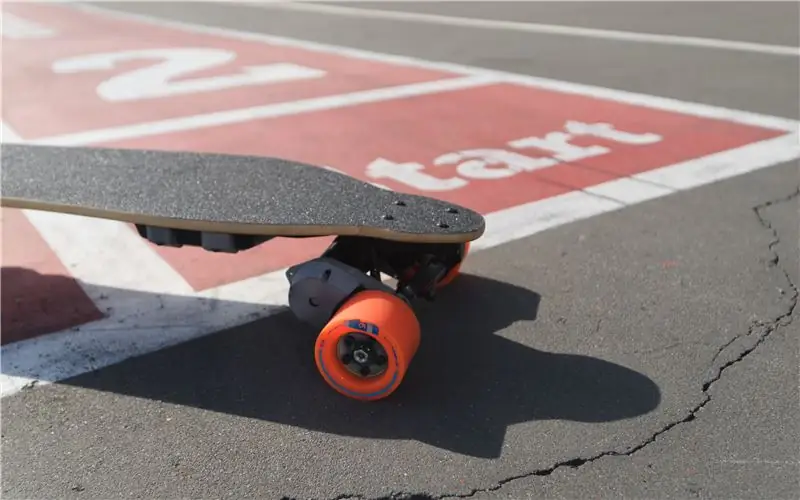
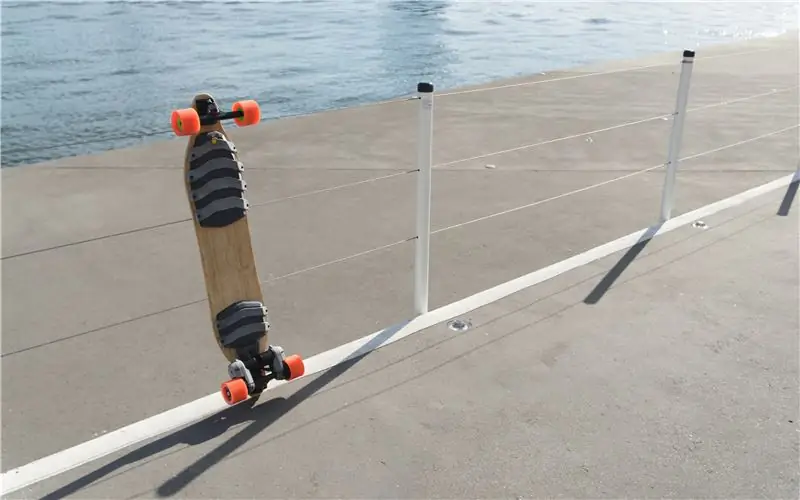
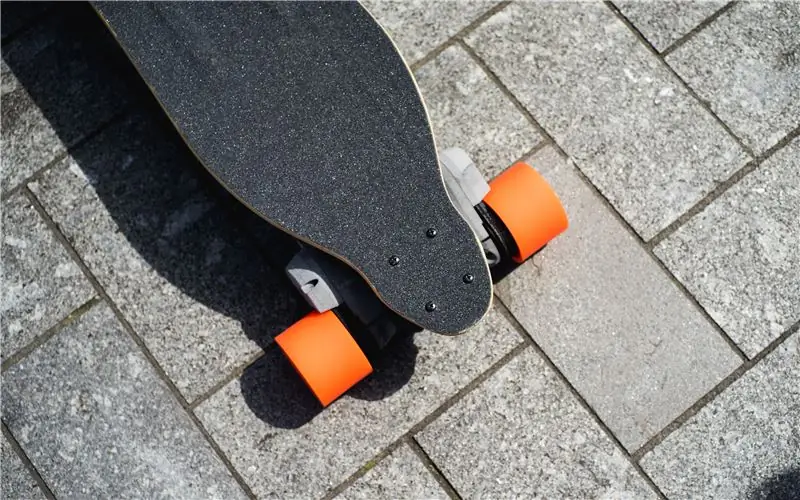
¡El proyecto ya está terminado! Creamos un video bastante impresionante del tablero en acción, puedes verlo a continuación. Muchas gracias a 3D Hubs por permitirme realizar este proyecto. ¡Échales un vistazo aquí para conocer todas tus necesidades de impresión 3D! 3dhubs.com
Recomendado:
Interruptor deslizante eléctrico impreso en 3D (usando solo un clip): 7 pasos (con imágenes)
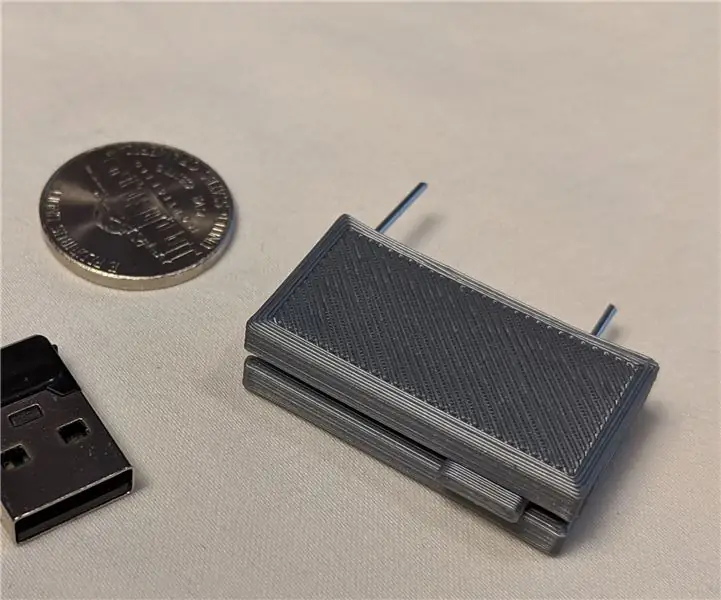
Interruptor deslizante eléctrico impreso en 3D (usando solo un clip): he incursionado en el cableado de mis propios pequeños proyectos eléctricos a lo largo de los años, principalmente en forma de clips, papel de aluminio y cartón empedrado con pegamento caliente. Recientemente compré una impresora 3D (la Creality Ender 3) y busqué f
Árbol de Navidad impreso en 3D con LED integrado: 10 pasos (con imágenes)
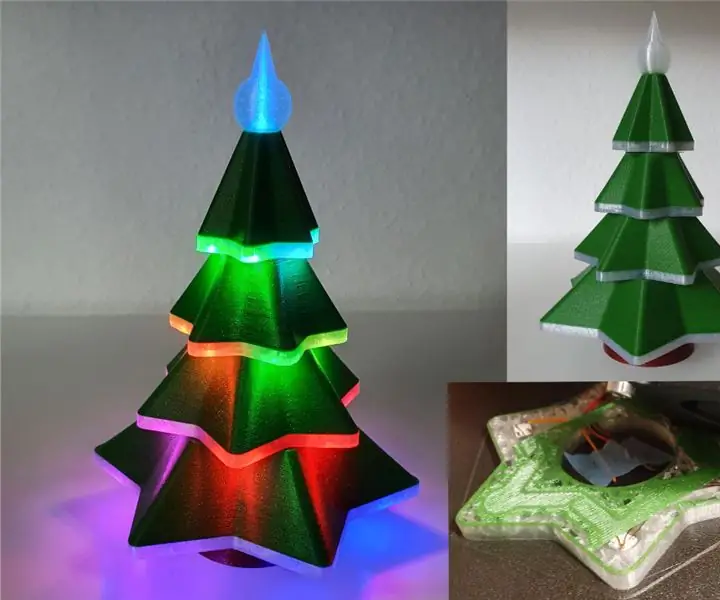
Árbol de Navidad impreso en 3D con LED integrado: este es un árbol de Navidad impreso en 3D con LED direccionables integrados en el interior. Por lo tanto, es posible programar los LED para obtener buenos efectos de luz y utilizar la estructura impresa en 3D como difusor. El árbol se divide en 4 etapas y un elemento base (el árbol
Control deslizante de la cámara de seguimiento de objetos con eje de rotación. Impreso en 3D y construido en el controlador de motor de CC RoboClaw y Arduino: 5 pasos (con imágenes
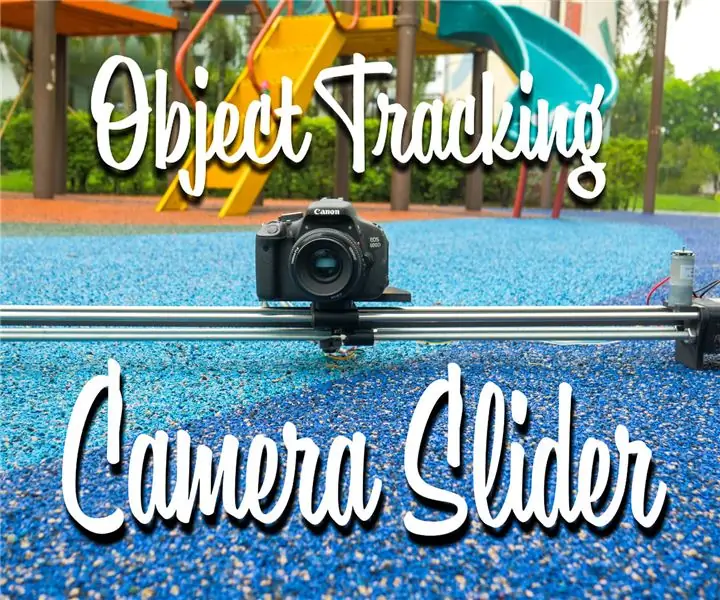
Control deslizante de la cámara de seguimiento de objetos con eje de rotación. Impreso en 3D y construido en el controlador de motor de CC RoboClaw y Arduino: este proyecto ha sido uno de mis proyectos favoritos desde que combiné mi interés por la creación de videos con el bricolaje. Siempre he mirado y he querido emular esas tomas cinematográficas en películas en las que una cámara se mueve a través de una pantalla mientras se desplaza para seguir el
OAREE - Impreso en 3D - Robot para evitar obstáculos para la educación en ingeniería (OAREE) con Arduino: 5 pasos (con imágenes)
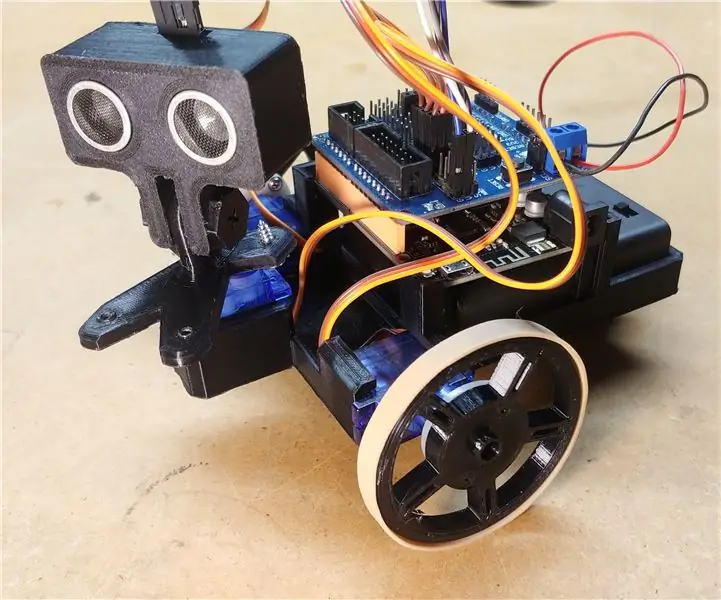
OAREE - Impreso en 3D - Robot para evitar obstáculos para la educación en ingeniería (OAREE) Con Arduino: Diseño OAREE (Robot para evitar obstáculos para la educación en ingeniería): El objetivo de este instructivo era diseñar un robot OAR (Robot para evitar obstáculos) que fuera simple / compacto, Imprimible en 3D, fácil de montar, utiliza servos de rotación continua para movem
Penny Board eléctrico V1: 8 pasos (con imágenes)
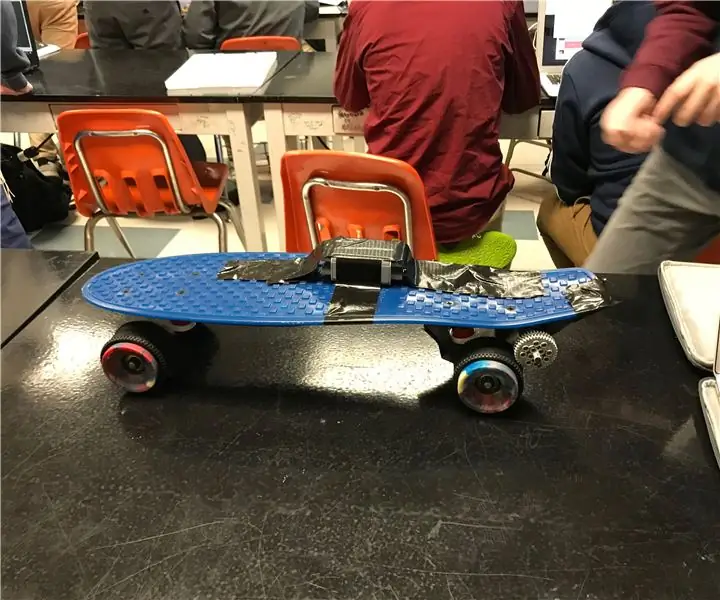
Electric Penny Board V1: esta patineta eléctrica es un prototipo de patineta bugger