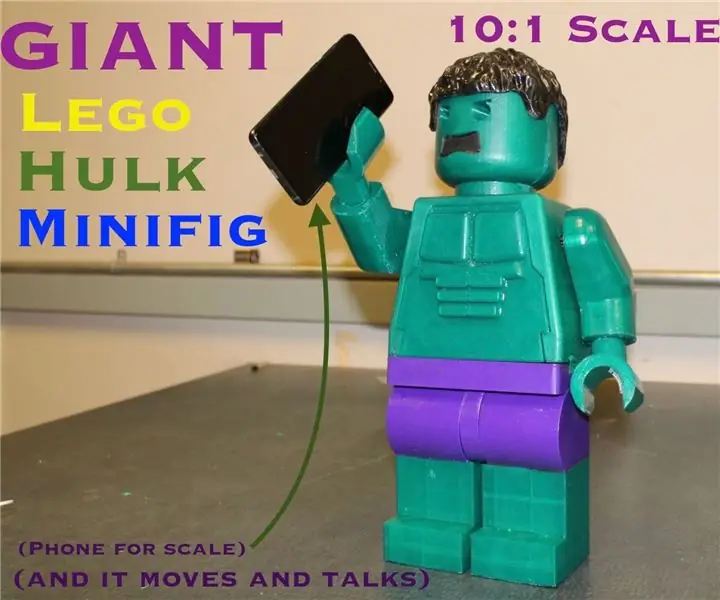
Tabla de contenido:
- Paso 1: Lista de materiales
- Paso 2: divide y vencerás
- Paso 3: diseño [opcional] e impresión 3D: diseño
- Paso 4: Diseño e impresión 3D: Impresión 3D
- Paso 5: [Opcional] Suavizado de impresiones 3D
- Paso 6: Montaje [parcial]: Montaje del cabezal
- Paso 7: Electrónica: soldar la PCB y la mayor parte de la electrónica
- Paso 8: Electrónica: Adaptador de conector de batería
- Paso 9: Código: compile y cargue el código
- Paso 10: Montaje: ajuste los componentes electrónicos
- Paso 11: Montaje: Montaje de los servomotores
- Paso 12: Montaje: encaje las piernas
- Paso 13: Montaje: Torso
- Paso 14: Vota por mí
2025 Autor: John Day | [email protected]. Última modificación: 2025-01-23 14:39
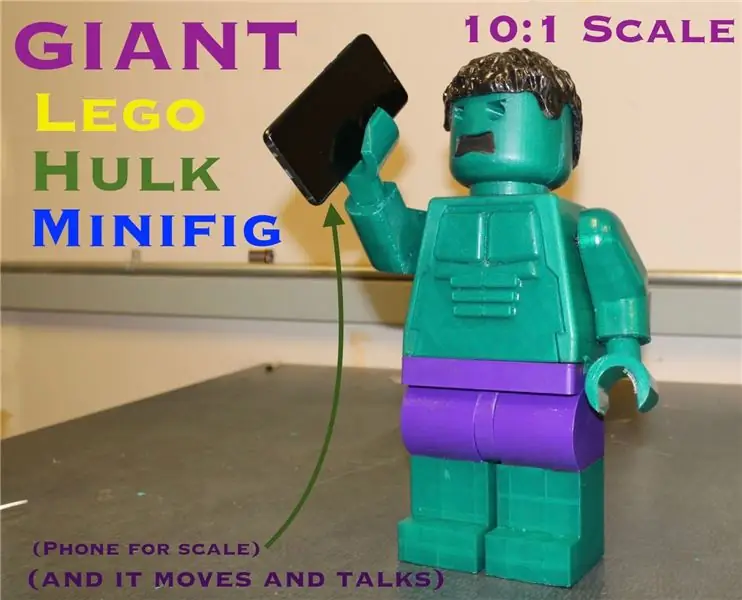


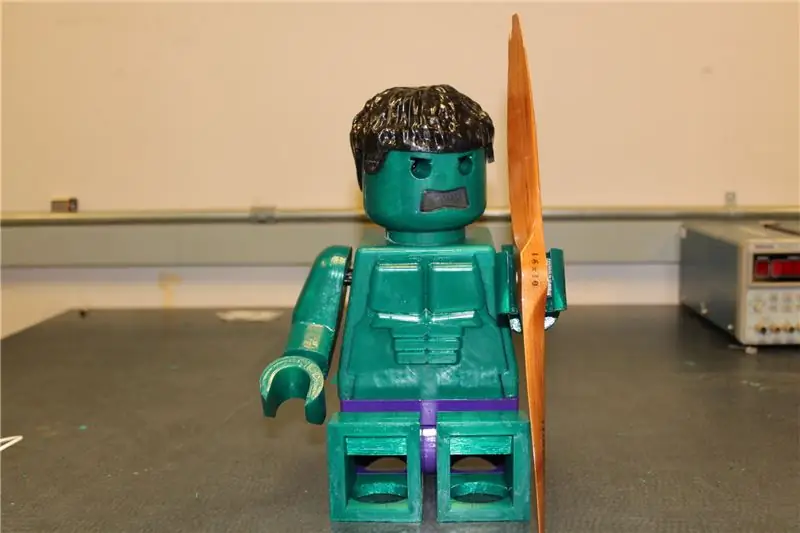
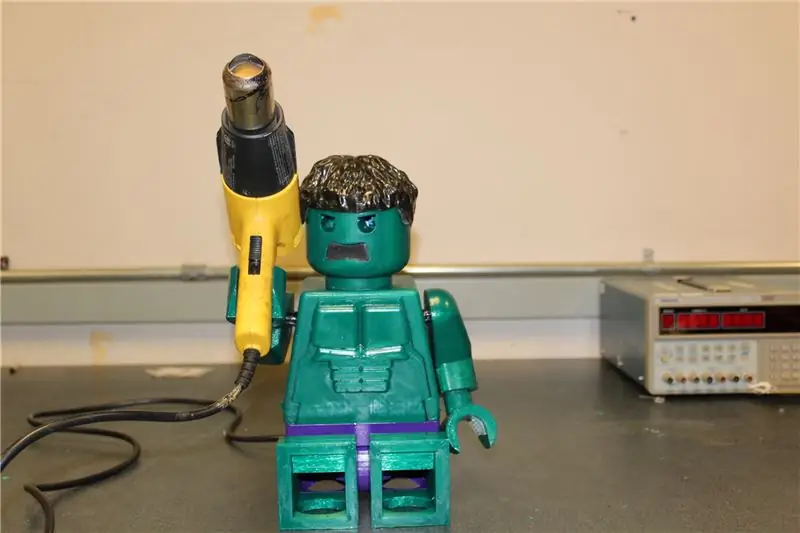
Proyectos Fusion 360 »
Siempre he jugado con legos cuando era niño, pero no tenía ninguno de los legos 'elegantes', solo ladrillos clásicos de lego. También soy un gran fanático de Marvel Cinematic Universe (MCU) y mi personaje favorito es Hulk. Entonces, ¿por qué no combinar los dos y hacer minifiguras de un Hulk gigante, porque más grande siempre es mejor, verdad? Así que decidí hacer un modelo a escala 10: 1 de las minifiguras lego originales.
Una minifig gigante de Lego Hulk (supongo que se llamaría megafig) no es suficiente. Decidí divertirme un poco más y darle vida. También le agregué algunas características novedosas adicionales que le permiten moverse y hablar agregando 3 servomotores, un módulo de reproductor MP3 y un altavoz con un amplificador incorporado.
Como tiene un módulo de reproductor de MP3 y un altavoz, ¡puedes cargar todas tus canciones favoritas en una tarjeta SD y usarla también como altavoz!
La electrónica y el hardware de este proyecto también se obtienen fácilmente y son relativamente económicos. De esa manera, este proyecto es fácilmente reproducible por las masas (y la comunidad de Instructables). Mi estimación para el costo del proyecto es de alrededor de $ 50-80; esto dependerá de dónde obtenga los artículos. Si está dispuesto a esperar por eBay o Aliexpress, será más barato, si no, DFRobot envió el mío a través de DHL y lo obtuve en 2 días. Se puede decir el mismo argumento sobre la calidad del filamento que utilizó. Teniendo en cuenta que puede comprar uno pequeño por $ 5 en Amazon, diría que el precio aumenta de manera bastante lineal, o menos, dado que tiene muchas más funciones que cualquier figura de lego comprada en la tienda.
Paso 1: Lista de materiales
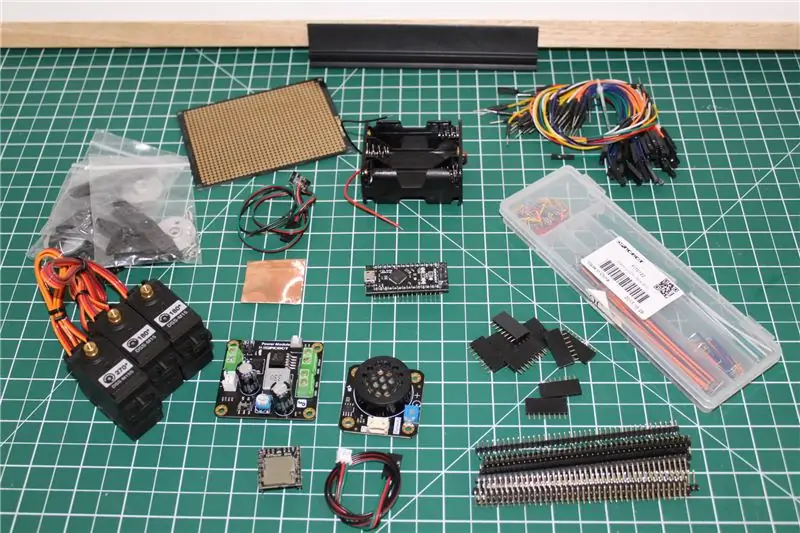
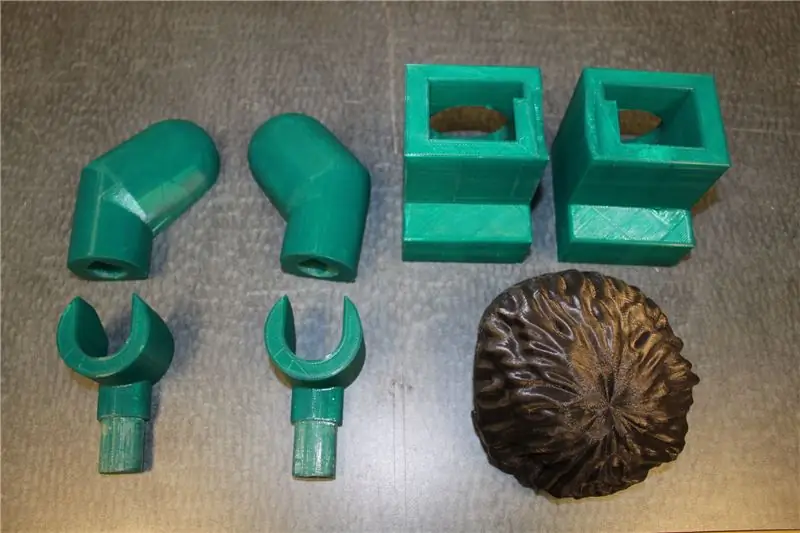
Hardware
Tuercas y pernos M3 surtidos
1 kg de PLA verde (obtuve una tonelada de filamento por un buen precio en Kijiji, pero puede obtener el suyo en Amazon o filaments.ca si está en América del Norte)
200 g de PLA púrpura (utilicé la marca CCtree de Amazon y superó mis expectativas por el precio)
200 g de PLA negro (utilicé mi marca favorita de confianza, aunque un poco cara, Innofil)
Resina epoxi y agente endurecedor (esto es para suavizar y dar brillo a la impresión, también puede usar XTC3D pero los encontré muy caros)
CA Glue and Accelerant o Superglue (el primero es preferible porque puede acelerar el tiempo de curado a unos pocos segundos)
Cepillo de espuma (el mío lo compré en una tienda de arte local, Curry's, que me dio un descuento para estudiantes).
Consejo profesional / Dato curioso: CA Glue es en realidad un súper pegamento, donde CA significa cianoacrilato (algo así como cuando compra Tylenol vs acetaminofén en una farmacia, este último es una marca genérica con el nombre químico real). El beneficio de usar CA Glue es que puede comprarlo con acelerante, lo que reduce el tiempo de curado a un par de segundos, por lo que no es necesario sujetarlo o sostenerlo hasta que se seque.
Precaución: tenga cuidado de no mancharse las manos con el pegamento CA + la mezcla de acelerante porque se quemará.
Electrónica
Arduino Pro Nano
Módulo reproductor MP3
Módulo de altavoz y amplificador
Servos de 180 y 270 grados (elegí usar 2180 grados para el brazo y 1270 grados para la cabeza)
Convertidor reductor de voltaje (también puede usar un 7805, pero no pueden proporcionar tanta corriente como este, además, ¡esto también funciona para un LiPo de 3 celdas!)
Resistencia de 1K ohmios (estoy seguro de que probablemente tenga alguna por ahí o puede comprar un paquete que durará toda la vida)
Placa de circuito impreso
Cables de puente
Alambres para protoboard
Batería de polímero de litio (LiPo) de 2 celdas o soporte de batería AA de 6 V (prefiero LiPo ya que es recargable y puede dar 7,2 V a los servomotores)
Encabezados de pines (M / F)
Conector XT60 (si elige usar una batería de polímero de litio con un xt60)
Pines de engarce JST (O simplemente puede soldar los extremos hembra del cable de puente; ya tenía un engarzador y tenía pines de engarzado JST, así que usé esto para que se vea más profesional)
Termoencogible (¡mucho más ordenado y de aspecto más profesional que la cinta aislante!)
Instrumentos
impresora 3d
Soldador, soldadura, bomba desoldadora
Multímetro (para circuitos de solución de problemas)
Crimper (si elige usar una batería de polímero de litio con un conector XT60)
Cuchillo X-acto: compré el mío en una tienda de arte local por alrededor de $ 2 con un descuento para estudiantes
Papel de lija: grano 400, grano 600, grano 1000, grano 200
"Pero no tengo una impresora 3D"
¡No hay problema! Puede enviar los STL a servicios de impresión 3D como Shapeways y 3DHubs
Sé que la lista parece desalentadora y larga. Traté de hacerlo lo más completo posible, al tiempo que proporcioné justificaciones y detalles sobre cómo hice mis elecciones de diseño. De esa manera, puede elegir y modificar el proyecto para convertirlo en el suyo. Mi objetivo es permitir que los usuarios siempre sean creativos y realicen sus propios proyectos utilizando el mío como guía en lugar de simplemente cortar la carga, ¡pero siéntase libre de duplicarlo también!
La impresión 3D también se está volviendo más común, así que tal vez tengas un amigo que tenga una impresora 3D que puedas usar. Los filamentos son cada vez más baratos y puede obtener una bobina de 1 kg por menos de $ 20 CAD o AUD (o <$ 15 USD).
Paso 2: divide y vencerás
Esta construcción puede no parecer compleja, pero abarca los bloques fundamentales de la robótica: electromecánica, circuitos y programación integrada. Como tal, un poco de planificación previa sería de gran ayuda en la construcción.
He separado esta compilación en 5 segmentos:
- Fase de diseño e impresión 3D
- Postprocesamiento
- Electrónica
- Código
- Montaje
¡Divide y conquistaras! Mientras espera que terminen sus impresiones, puede comenzar con la electrónica y la codificación.
Paso 3: diseño [opcional] e impresión 3D: diseño
![[Opcional] Diseño e impresión 3D: Diseño [Opcional] Diseño e impresión 3D: Diseño](https://i.howwhatproduce.com/images/011/image-30025-8-j.webp)
Dado que mis habilidades con Fusion360 son limitadas, pedí a un amigo que me ayudara a CAD estos archivos. No tiene que diseñar el suyo propio si sigue esta guía al pie de la letra. Simplemente vaya al siguiente paso e imprímalos en 3D. ¡Todas las dimensiones son métricas!
Sin embargo, si elige un PCB o altavoz diferente, es posible que deba cambiar el tamaño de los orificios y cortar las extrusiones donde se supone que deben estar los componentes.
Sin embargo, si quieres otras minifiguras de lego que no sean Hulk, entonces siéntete libre de CAD tú mismo. ¡Alguien, por favor haga una versión gigante de lego batman de esto!
Consejos profesionales: diseñe pensando en la impresión 3D
(1) Los círculos en forma de lágrima se pueden imprimir sin soportes, así que incorpore formas de lágrima para recortes circulares en lugar de círculos.
(2) Se pueden imprimir ángulos de 45 grados o más pronunciados sin soportes, por lo que debe hacer que sus voladizos tengan ángulos de 45 grados para soportarlos.
Paso 4: Diseño e impresión 3D: Impresión 3D
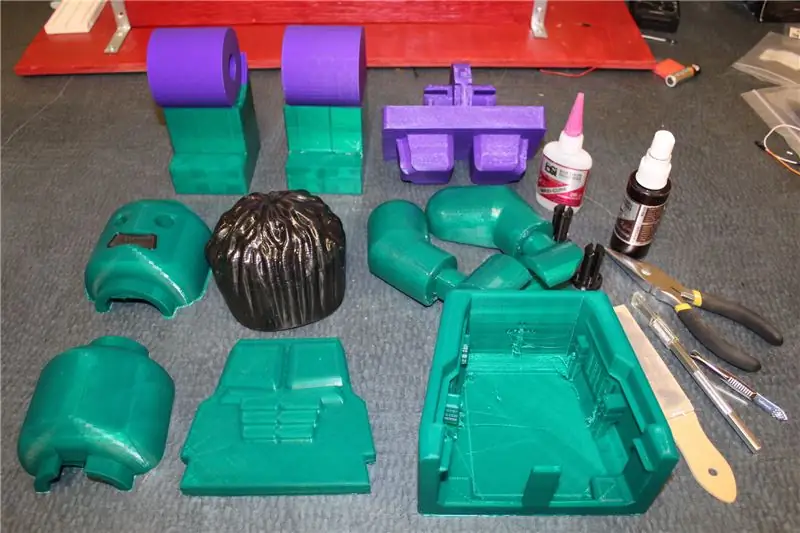
Este paso es bastante sencillo, tome su tarjeta SD, guarde el gcode de su cortadora para cualquier archivo STL que desee imprimir e imprímalo o simplemente pídalo en Shapeways o 3DHubs.
El tiempo total de impresión de todas las impresiones fue de aproximadamente 80 horas. Usó alrededor de un poco más de 1 kg de material en total usando filamentos negros, púrpuras y verdes, en su mayoría verdes porque Hulk es verde, duh. Siempre puede imprimirlo en un solo color y luego pintar con aerosol las piezas individuales, que es otro método para alisarlo (consulte el siguiente paso).
Consejo profesional 1: lucha contra el filamento translúcido
Si tiene un filamento de aspecto transparente como el que obtuve para mi verde, puede salirse con la suya y seguir luciendo opaco (1) aumentando el grosor de la carcasa o (2) usando un conjunto de relleno dinámico para llenar hasta el 50% en incrementos del 5%. Desafortunadamente, dado que la resina es transparente, no cubre la transparencia del filamento.
Consejo profesional 2: lidiar con la deformación no plástica
Para las piezas que necesitan flexionarse levemente, imprímalo con un relleno más alto que el ajuste predeterminado, alrededor del 50%, para que no sea demasiado quebradizo cuando tenga que apretar los pasadores juntos. Puede dejar el grosor de pared predeterminado. Me tomó alrededor de 5 intentos antes de obtener la combinación correcta de relleno y grosor de pared. También use filamento de alta calidad. El filamento CCTree de Amazon es excelente ya que permite una deformación no plástica en los pines.
Consejo profesional 3: Reducir el tiempo de impresión
No hay almuerzo gratis si desea ahorrar tiempo en la impresión 3D. Casi siempre hay que hacer una compensación. Aquí hay algunos que utilicé que no afectaron mucho la calidad de impresión:
(1) Utilice una capa de mayor altura: alrededor de 0,2 mm es aceptable para la cabeza y la parte delantera del cuerpo y 0,3 mm para todo lo demás.
(2) Reduzca la densidad de relleno a alrededor del 5-10% o use relleno dinámico como se indica en ProTip 1.
(3) Active el modo de peinado para reducir los tiempos de viaje.
(4) Use bordes o balsas: puede ser contrario a la intuición usar bordes y balsas, pero le ahorrará tiempo de impresiones fallidas que salieron de la plataforma de impresión desde la boquilla que golpean algunas impresiones ligeramente fuera del eje z repetidamente.
(5) Utilice menos soportes. Para impresiones que requieren una gran cantidad de soportes como el cabello, el uso de soportes de menor densidad alrededor del 5-10% aún producirá una impresión exitosa.
Paso 5: [Opcional] Suavizado de impresiones 3D
![[Opcional] Suavizado de impresiones 3D [Opcional] Suavizado de impresiones 3D](https://i.howwhatproduce.com/images/011/image-30025-10-j.webp)
![[Opcional] Suavizado de impresiones 3D [Opcional] Suavizado de impresiones 3D](https://i.howwhatproduce.com/images/011/image-30025-11-j.webp)
![[Opcional] Suavizado de impresiones 3D [Opcional] Suavizado de impresiones 3D](https://i.howwhatproduce.com/images/011/image-30025-12-j.webp)
Este es un proceso largo y oneroso, pero muy gratificante. No tiene que hacerlo, pero hace que el resultado final se vea mucho mejor. Siguiendo la guía de BrittLiv, elegí suavizar mi impresión con una capa de epoxi, excepto que decidí lijarla primero a un grano 1000 (preferiblemente 2000, pero no tenía ninguno).
Mezcle el epoxi con un tiempo de trabajo de 30 minutos a 1 hora para que pueda terminar todas las piezas antes de que se endurezca. Luego, tardará otras 24 a 48 horas en curar, dependiendo del grosor de la capa que haya utilizado.
Precaución: Use guantes al aplicar epoxi. Puede volverse alérgico al epoxi, lo que provocará dermatitis de contacto, por lo que no querrá nada en sus manos. Además, no tiene que lijar minuciosamente sus huellas dactilares en su trabajo de impresión que solo tardó 12 horas en imprimirse.
Este paso es bastante largo y detallado, aunque las acciones que se toman para suavizar la impresión son bastante simples. Hubo muchas técnicas que se utilizaron y probaron durante todo el proceso, y quería compartir todas las lecciones que he aprendido.
Consejo profesional 1: nivelar la capa Utilice un plato de papel o cualquier superficie plana como una 'paleta' antes de pintar, en lugar de sumergir el cepillo de espuma en una taza llena de epoxi. Esto le permitirá controlar y aplicar una capa uniforme en el trabajo de impresión.
Consejo profesional 2: use un pincel de espuma No tengo conocimientos previos en las artes ni nada relacionado con él, por lo que cuando se trataba de elegir un pincel de una tienda de arte local, no tenía ni idea de qué elegir, así que pedí ayuda. Me trajeron un punto muy bueno, si usa un cepillo típico, los trazos de las cerdas serán visibles, así que use un cepillo de espuma ya que no hay cerdas.
Consejo profesional 3: Evite la pegajosidad mezclando la proporción adecuada y midiendo con precisión
Use una escala para medir la proporción adecuada de resina y endurecedor. Contrariamente al consejo en línea de mezclar más endurecedor para que se seque más rápido, siempre use la proporción adecuada. Es ciencia simple, o más bien química. La mezcla de resina y endurecedor es una reacción química; de hecho, se puede decir que es una reacción exotérmica porque el epoxi se calienta a medida que los mezcla. Las proporciones sugeridas son las proporciones estequiométricas que permiten que toda la resina y el endurecedor reaccionen juntos para formar el epoxi, por lo que cualquier exceso no reaccionará y quedará con una capa de pegajosidad.
Lecciones aprendidas
1) No sumergir en agua una vez hecho
No tenía una buena superficie para colocar las piezas impresas en 3D, así que simplemente la coloqué encima de un papel de desecho. Como era de esperar, el epoxi goteó y se adhirió al papel. En realidad, no es difícil de quitar porque simplemente puedes remojar el papel en agua y frotarlo, es decir, si no pusiste epoxi en el área que hace contacto con el papel (no deberías). Desafortunadamente, remojar la impresión con epoxi en agua hizo que se viera manchada, como un automóvil que intentaste lavar pero no se secó correctamente.
No había nada que pudiera hacer para deshacerme de las manchas, incluso si lo secaba correctamente. La única solución fue lijar todo de nuevo, y lijar el epoxi no es nada divertido, hasta que esté suave (lijar hasta un grano 2000), luego recubrirlo nuevamente con epoxi, lo que significa más espera.
Sin embargo, hay un lado positivo, después de que repetí el tedioso proceso de alisado y epoxi, ¡el resultado final se veía significativamente mejor! Puedo imaginar que hay un punto de rendimiento decreciente para esto y en algún momento no tiene sentido repetir esto, donde la primera capa tiene el mayor impacto.
2) No caliente la pistola
NO use una pistola de calor para acelerar el curado del epoxi. El plástico se ablandará y deformará incluso si lo calienta a distancia. Tenía una muestra de PLA y aprendí que es mejor tener paciencia y esperar.
3) Sigue lijando
Al principio era reacio a lijarlo porque lo hacía lucir blanco y rayado y estaba preocupado de que cuando lo cubra con una capa de epoxi mantendrá su color rayado opaco. Me equivoqué. De hecho, lijarlo hasta que esté suave y muy rayado dio los mejores resultados.
¿Como funciona?
Cuando lo lija, se deshace de las imperfecciones y los baches, por lo que obtiene una impresión suave, pero no llena ninguno de los huecos y grietas. Cuando aplica epoxi a una impresión, está llenando efectivamente todos los espacios que dejan las capas y cualquier irregularidad en la impresión. Tenga en cuenta que si sumerge la parte impresa en 3D en agua, su apariencia es mucho más suave mientras está húmeda, eso se debe a que el agua llenó los espacios, pero se evapora. La resina lo rellena de forma permanente y no deja ninguna decoloración ya que es incolora.
Paso 6: Montaje [parcial]: Montaje del cabezal
![Montaje [parcial]: montaje del cabezal Montaje [parcial]: montaje del cabezal](https://i.howwhatproduce.com/images/011/image-30025-13-j.webp)
![Montaje [parcial]: montaje del cabezal Montaje [parcial]: montaje del cabezal](https://i.howwhatproduce.com/images/011/image-30025-14-j.webp)
![Montaje [parcial]: montaje del cabezal Montaje [parcial]: montaje del cabezal](https://i.howwhatproduce.com/images/011/image-30025-15-j.webp)
Hay algunos componentes electrónicos que no necesita soldar gracias al diseño de PCB modular que proporcioné. Estos son los servomotores y el módulo de altavoz. Dado que el servomotor y el módulo de altavoz son independientes del cuerpo, podemos colocarlos en el cabezal y terminar el ensamblaje del cabezal.
Coloque el altavoz en la parte delantera de la cabeza. Hay clavijas para que el altavoz se atornille, pero dado que estas dos piezas van a quedar intercaladas por el servo y el cabello, no hay necesidad de atornillarlo, y no se separará a menos que lo fuerces.
Paso 7: Electrónica: soldar la PCB y la mayor parte de la electrónica
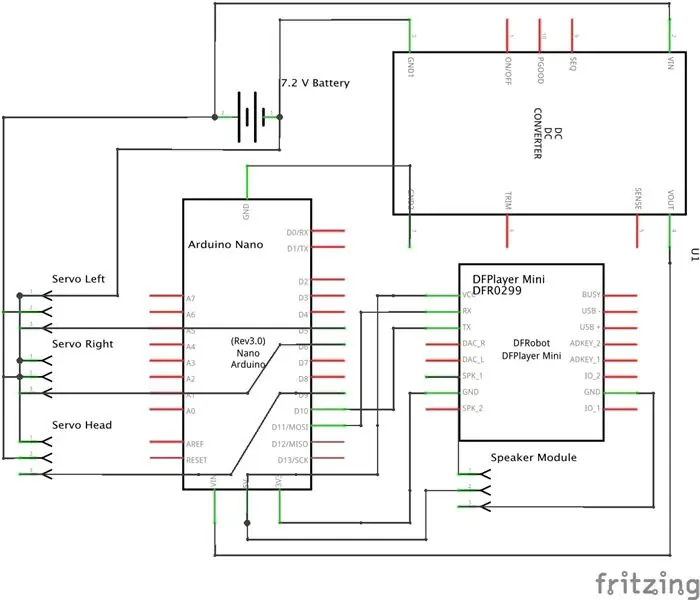
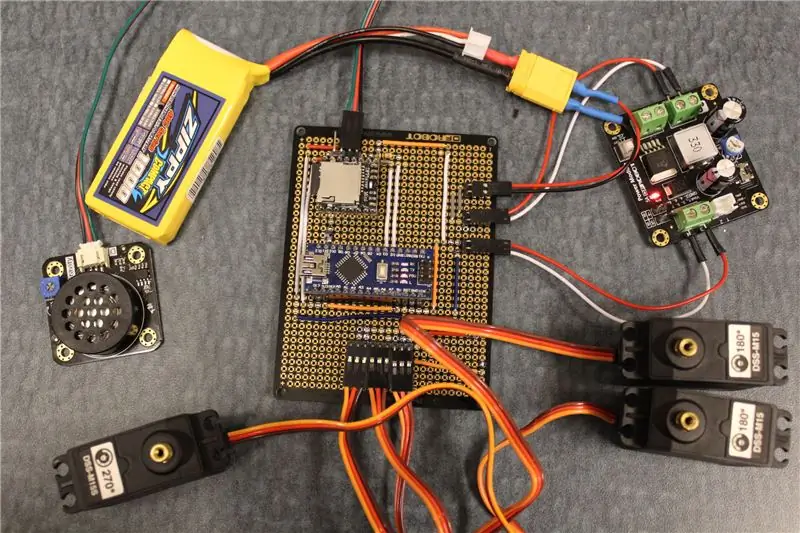
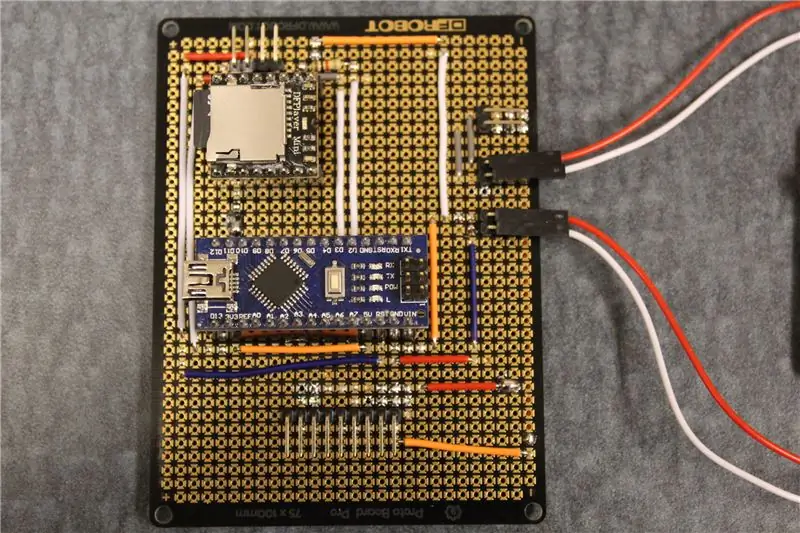
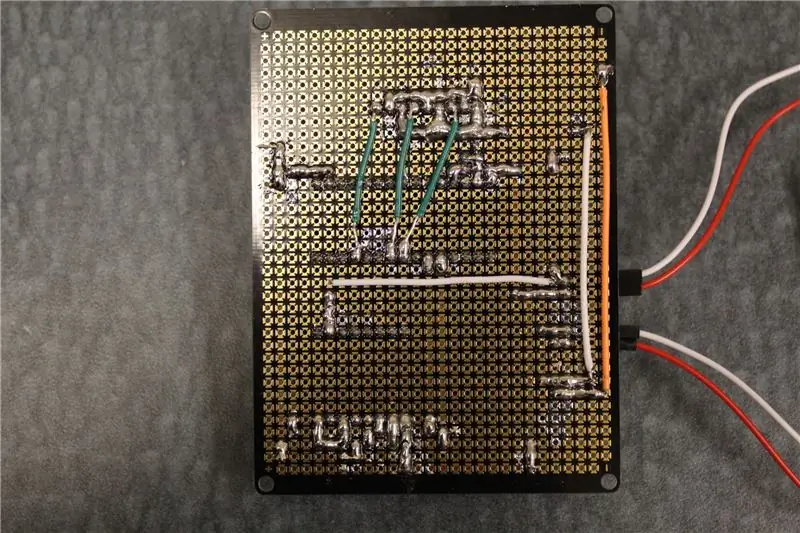
Suelde la PCB según el esquema proporcionado. También agregué el documento Fritzing para que pueda abrirlo en Fritzing y ejecutar el enrutamiento automático para la PCB e imprimirlo si no desea soldar las rutas del bus usted mismo.
Para hacer que el circuito sea más ordenado y modular, empleé algunas técnicas que se indican a continuación:
- Utilice encabezados de clavija hembra como enchufes IC personalizados para Arduino Nano y DFPlayer Mini.
- Utilice cabezales de clavija macho para conectar los servomotores y los altavoces. De esta forma no se sueldan directamente en la PCB y se pueden quitar en cualquier momento.
- Agregue encabezados de clavija macho para la entrada de la batería y la entrada y salida del convertidor reductor de voltaje. De esta manera, puede enrutar y agregar fácilmente más rutas de bus al voltaje apropiado. Esto no es necesario, pero simplifica el cableado y permite que haya menos cables colgando del convertidor reductor de voltaje. Como puede ver, solo usé 2 pares.
Esto requiere una cantidad moderada de experiencia y habilidades de soldadura debido a la cantidad de conexiones en puente que debe realizar y a lo cerca que están los pines entre sí.
Entonces, ¿cómo se obtiene un buen resultado al soldar la PCB?
Consiga un buen soldador con control de temperatura y un PCB con almohadillas cuadradas. Utilice una plancha con punta de cincel (plana) para aumentar el contacto entre el componente y la almohadilla. También me gusta usar 2/3 de estaño y 1/3 de plomo, ya que el plomo tiene una temperatura de fusión más baja, lo que facilita un poco la soldadura.
Paso 8: Electrónica: Adaptador de conector de batería
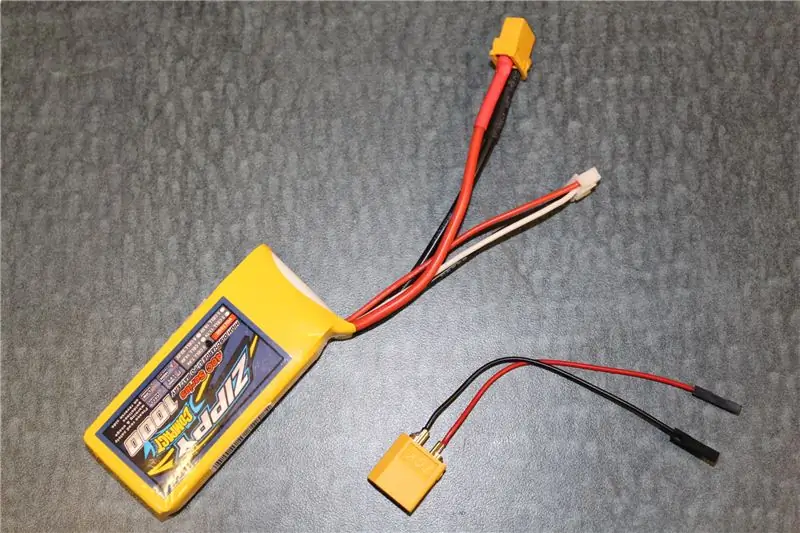
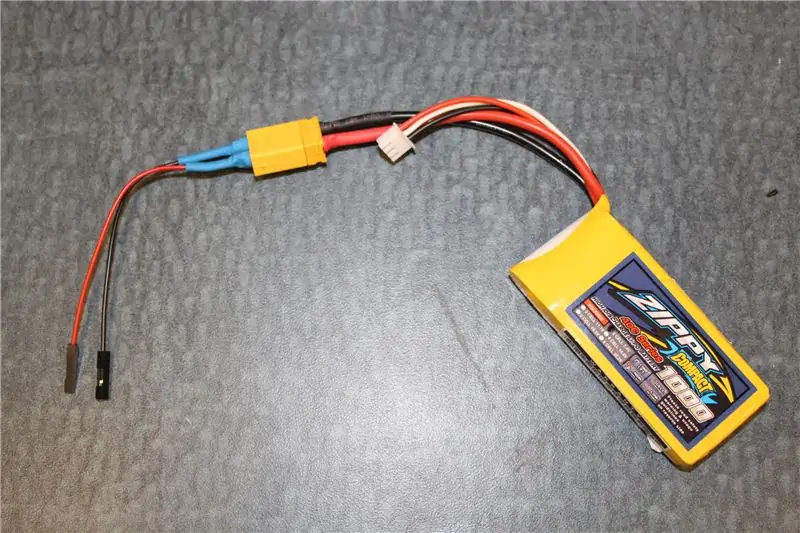
La salida de la batería LiPo de 2 celdas es a través del conector XT60, que es un estándar en los aviones RC. No quería cortarlo porque XT60 es el estándar para muchos enchufes para motores sin escobillas que uso y también puede manejar hasta 60 A de corriente, que necesito para otras aplicaciones.
1. Soldar XT60
En cambio, opté por una solución más modular. Suelde un adaptador XT60 con un XT60 macho a JST hembra (etiquetado arriba): negativo a negativo (cable negro) y positivo a positivo (cable rojo).
2. Engarzado / soldadura de pines hembra JST a XT60
Coloque las clavijas sin rizar en la engarzadora y apriételo de modo que sujete las clavijas firmemente mientras permite que los cables se deslicen, formará un cubo abierto. Inserta el cable pelado en el cubo abierto y luego rómpelo. Repita esto para los cables rojo y negro y luego deslice ambos pasadores engarzados en la carcasa del JST.
Alternativamente, puede cortar el extremo macho del cable de puente M / F y soldar el cable al XT60 como hice yo.
3. Encoja los conectores con calor
Asegúrese de encoger con calor los conectores para que no se cortocircuiten accidentalmente. Estas baterías de litio harán algunos fuegos artificiales hermosos, aunque no tan agradables, si se acortan
Consejo profesional 1: soldar XT60s
Cuando suelde los cables delgados al XT60, primero estañe los cables y luego llene las cavidades del XT60 con soldadura hasta la mitad. Manteniendo la plancha en los conectores, sumerja los cables estañados y retire la plancha, mientras sujeta el cable. Manténgalo quieto durante unos segundos y encoja el calor una vez que se enfríe.
Consejo profesional 2: Prevención de la deformación del conector
Para evitar que el conector XT60 se deforme por el calor alto, coloque el conector hembra y macho (¡los conectores sin soldar, NO las baterías!) Entre sí antes de soldar. De esa manera, mantendrán la forma del conector y evitarán que los conductores se muevan, ya que es un ajuste perfecto.
Paso 9: Código: compile y cargue el código
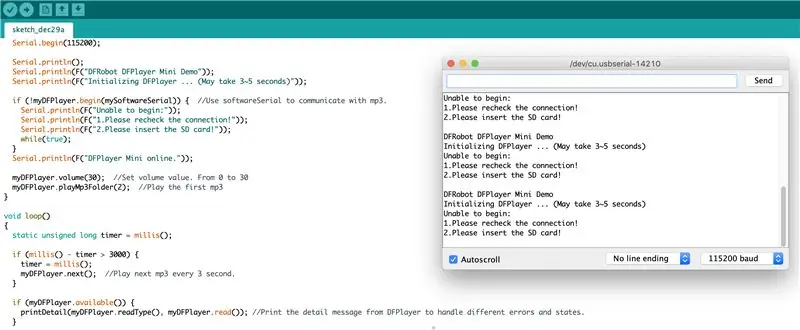
Descargue el código adjunto y cárguelo en el Arduino Nano. Este es responsable de ejecutar 4 modos de movimiento diferentes desde el servo, así como de reproducir efectos de sonido a través del módulo MP3. El módulo MP3 reproduce los sonidos según el orden en que se cargan los archivos MP3 en la tarjeta SD.
Si desea usarlo como altavoz, simplemente use la siguiente función para reproducir archivos de música aleatorios en un bucle.
myDFPlayer.randomAll ();
Para obtener más información sobre todos los comandos que se pueden dar al reproductor MP3, puede encontrarlo en las especificaciones del fabricante.
En mi caso, todo lo que se necesita es reproducir un archivo MP3 específico. La forma en que me aseguré de que el módulo MP3 reprodujera el archivo apropiado en lugar de depender del orden es usando el método incorporado, que supone que está en la carpeta llamada MP3 (no distingue entre mayúsculas y minúsculas):
myDFPlayer.playMP3Folder (1);
donde el argumento 1 es el nombre del archivo, 0001.mp3.
Usando el método que se basa en el orden de carga del archivo:
myDFPlayer.play (1);
asume que está en la carpeta raíz y no requiere un nombre de archivo específico.
Paso 10: Montaje: ajuste los componentes electrónicos
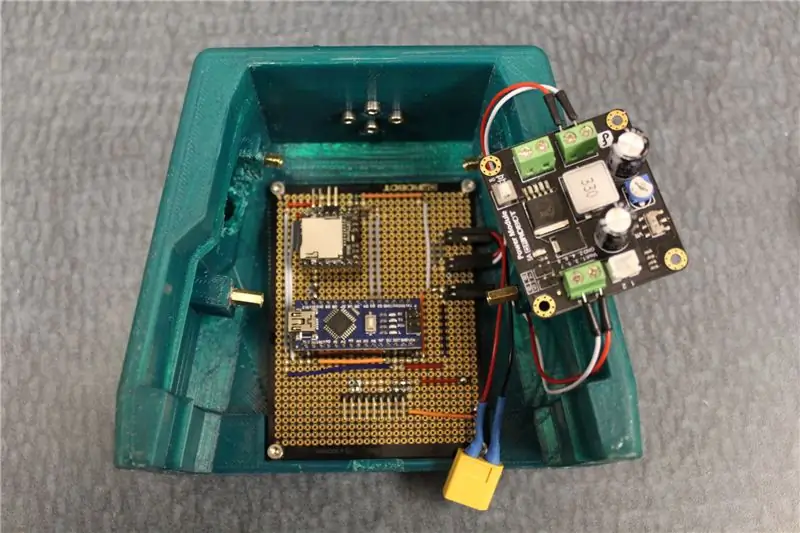
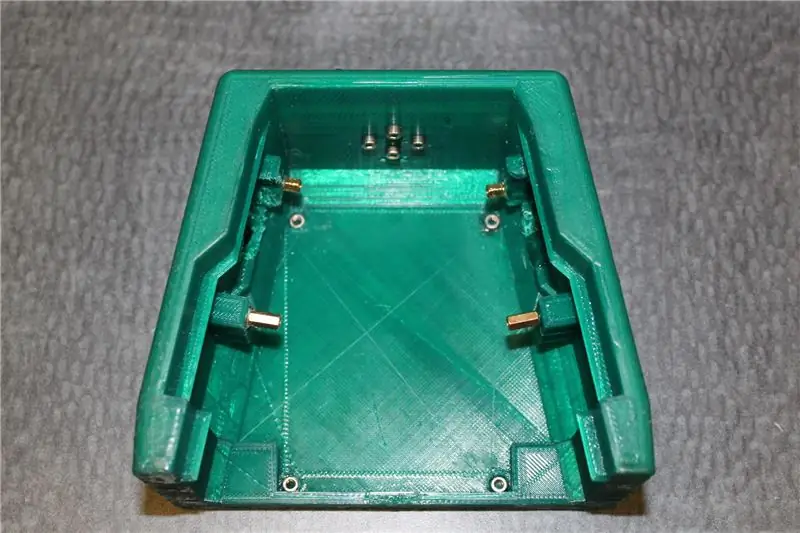
Comenzaremos con la PCB y los componentes electrónicos, luego pasaremos a conectar los servomotores.
Primero, para facilitar el montaje, G y desenchufe los componentes.
Observe cómo hay algunas extrusiones de corte hexagonal para fijar una tuerca en el cuerpo y la cabeza de la pieza de Lego. Aquí es donde se debe pegar la tuerca con pegamento CA; tenga cuidado al pegarla de no agregar accidentalmente pegamento en las roscas.
Luego coloque la PCB y alinee los orificios con las tuercas y atorníllela con pernos M3. Esta debería ser una tarea bastante rápida y trivial.
Paso 11: Montaje: Montaje de los servomotores
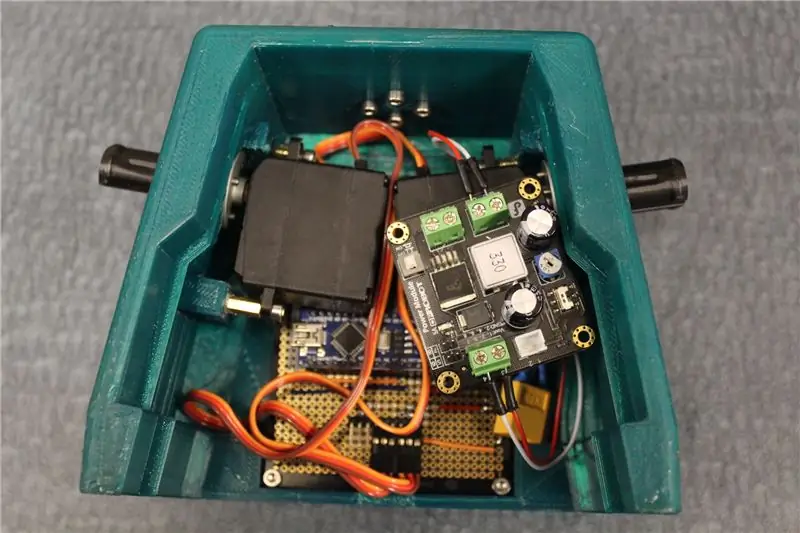
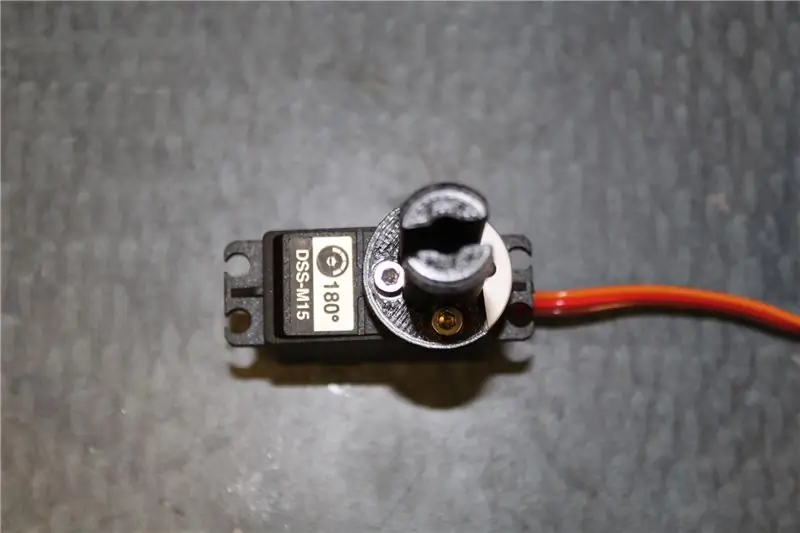
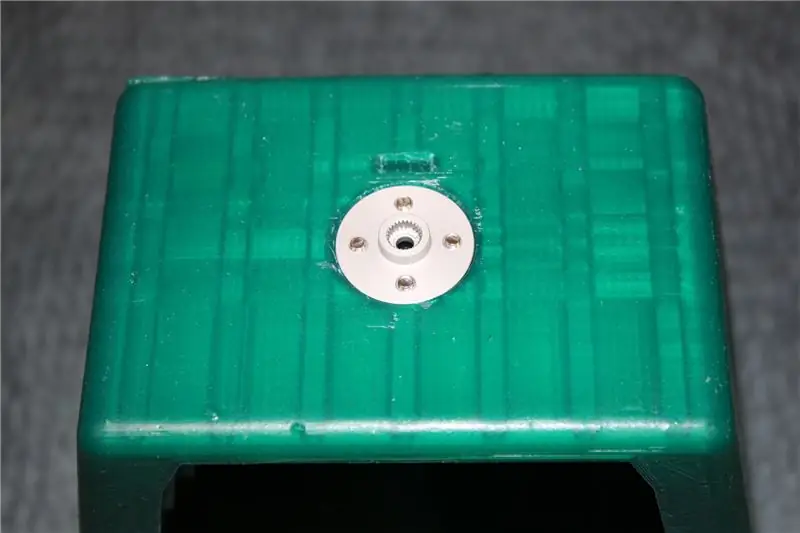
Hay dos cosas que se deben unir físicamente a los servomotores (1) La bocina circular de metal del servo (etiquetada arriba) y (2) El cuerpo del servo al cuerpo de la pieza de Lego. Los tornillos utilizados para todo este proyecto están estandarizados; todos son tornillos y tuercas M3.
Hay 3 servos cuernos que deben colocarse en el cuerpo. Uno para la cabeza y dos para los pasadores del brazo que serán accionados por el servomotor. Hay un orden particular en el que deben colocarse de manera que no tenga que colocar las manos de manera incómoda.
- Atornille la bocina del servo para la cabeza en la parte superior del cuerpo con tornillos de 4 m3 hacia la bocina.
- Atornille los pasadores del brazo en la bocina del servo y luego en el servomotor de 180 grados usando los tornillos provistos con el servo. Atorníllelo hacia la bocina ya que los orificios de la bocina están roscados.
- Coloque separadores a los lados del cuerpo donde se va a montar el servo. Los separadores son para solucionar el espacio entre el servo y la plataforma de montaje debido a un error de diseño. Esto se solucionará y no es necesario que realice este paso.
- Luego, simplemente atornille el chasis del servomotor y la bocina del servo al cuerpo como se muestra en las imágenes. Si no está utilizando separadores, necesitará tornillos autorroscantes que se proporcionarán con el servomotor. Los servos en el cuerpo son bastante ajustados, por lo que debes jugar con ellos hasta que puedas meterlos a ambos.
Paso 12: Montaje: encaje las piernas
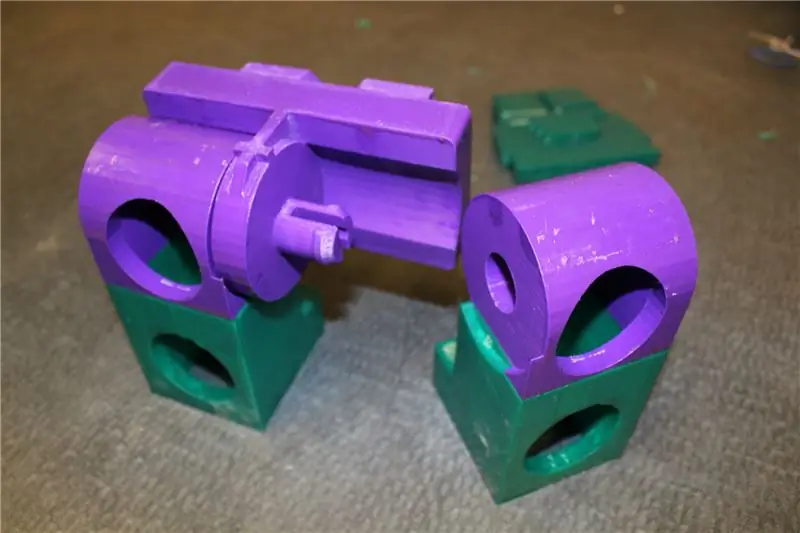
Lo último que tenemos que hacer es ensamblar todas las piezas como un Lego clásico.
- Pegue las dos mitades de las piernas, debajo (PLA verde) y arriba de la rodilla (PLA púrpura) juntas con pegamento CA
- Junte las piernas hasta las caderas. Si está siendo un poco terco, apriete ligeramente los dos pines y empuje las piernas hacia la cadera.
Es por eso que usé filamento de calidad (usé CCTree de Amazon para las piezas moradas y sorprendentemente no es quebradizo y de colores brillantes para el precio).
Paso 13: Montaje: Torso
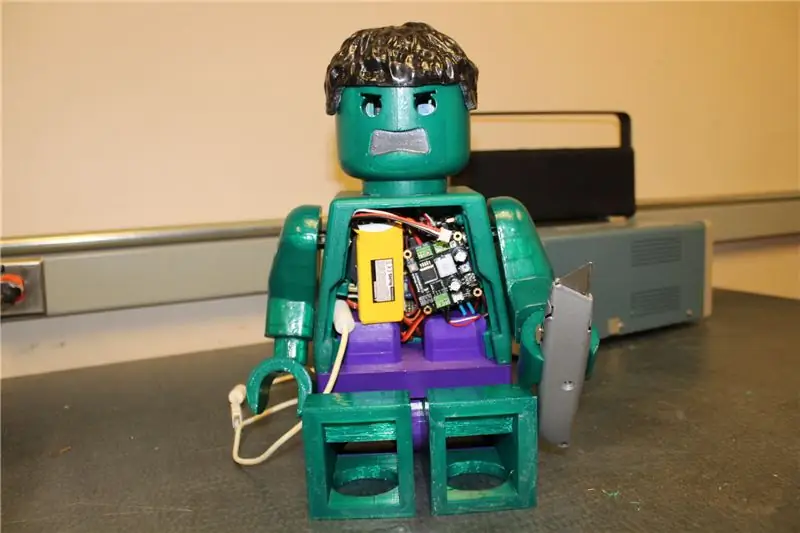
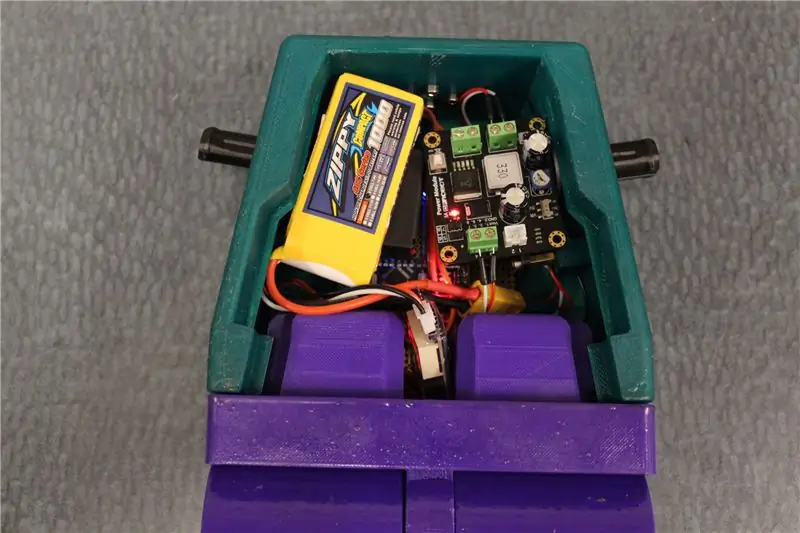
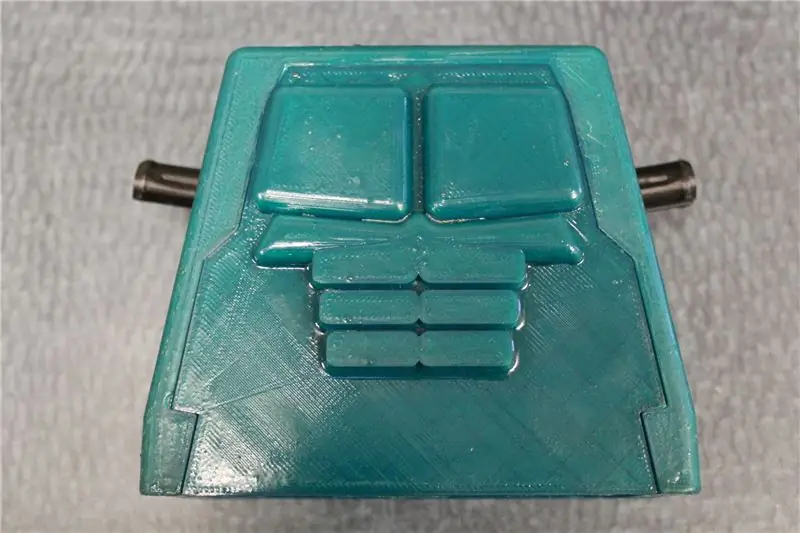
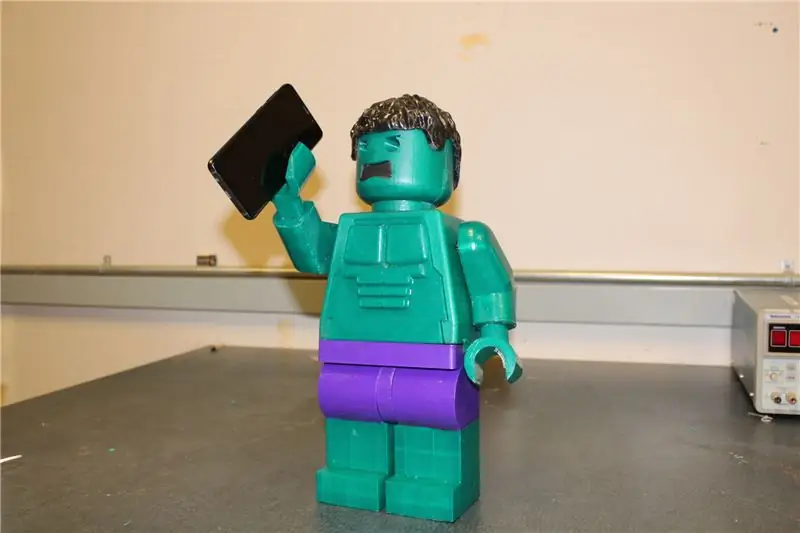
- Empuje las manos contra los brazos; es posible que los brazos necesiten un poco de lijado según las tolerancias de la impresión 3D.
- Encaje a presión los brazos en los pasadores del brazo al igual que las piernas en el
- Empuje hacia abajo los cables del altavoz y del servo a través del orificio del cuerpo y conéctelo a los cabezales de clavija correspondientes que haya soldado.
- Atornille el servo de la cabeza en el cuerno del servo del cuerpo para completar el ensamblaje. Luego, coloque la placa del pecho en la parte superior del cuerpo.
¡Listo! ¡Enciéndelo y disfruta de tu Mega Figura Lego Hulk!
Paso 14: Vota por mí
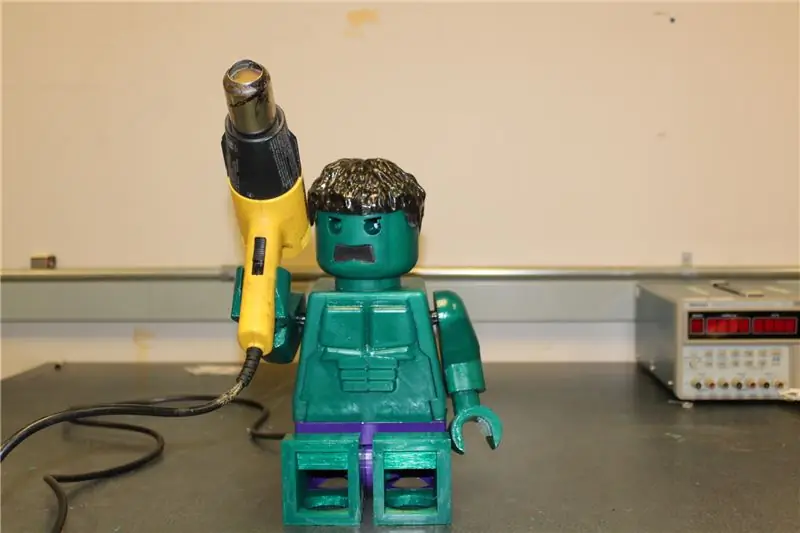
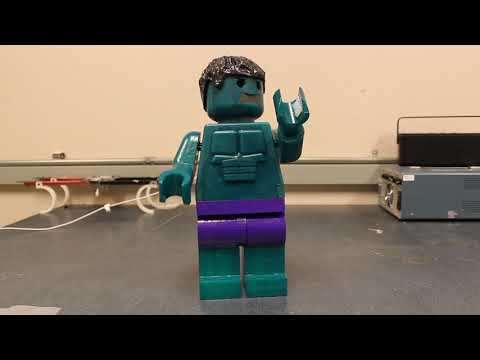
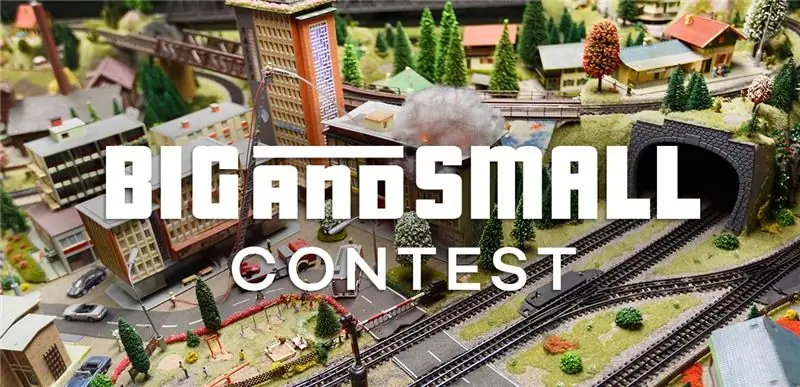
Entré en este concurso para grandes y pequeños, por lo que sus votos serán muy apreciados si lo disfrutan.
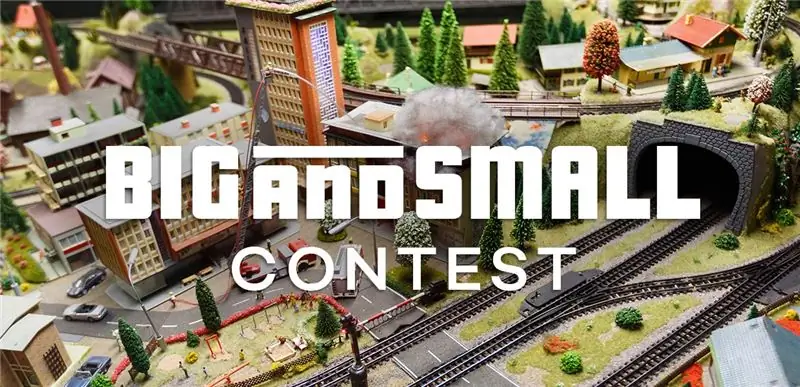
Segundo premio en el Concurso Grandes y Pequeños
Recomendado:
Molde de soplado de Papá Noel que habla: 5 pasos
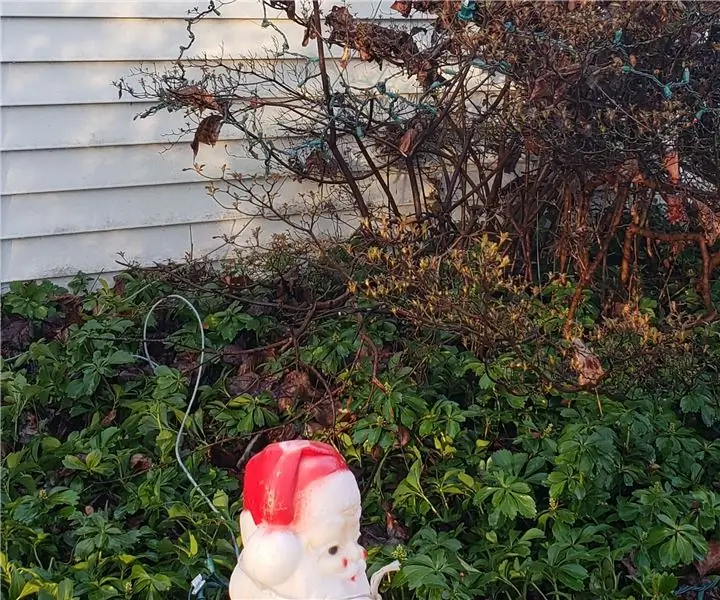
Talking Santa Blowmold: Este proyecto explica cómo hacer una decoración que reproduce un archivo de sonido cuando alguien pasa. Esto se puede lograr fácilmente con una computadora que pueda ejecutar el programa Motion y una cámara de algún tipo. En este caso utilicé un 20 " alto Santa Clau
Barbara: la cámara con IA que habla: 4 pasos (con imágenes)
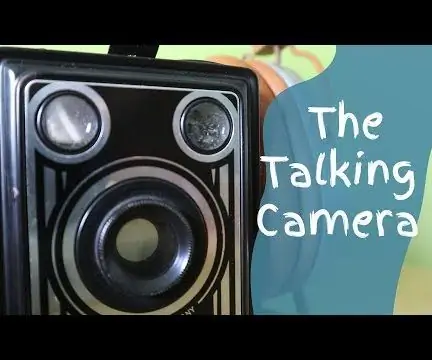
Barbara: la cámara de IA que habla: IA es la última palabra de moda, este proyecto tiene que ver con lo ligeramente inútil. Después de encontrar una API ordenada que subtitula imágenes y una cámara vieja, se establecen los objetivos: ¡Una cámara que subtitula lo que ve
Radio que habla Pi Zero: 7 pasos (con imágenes)
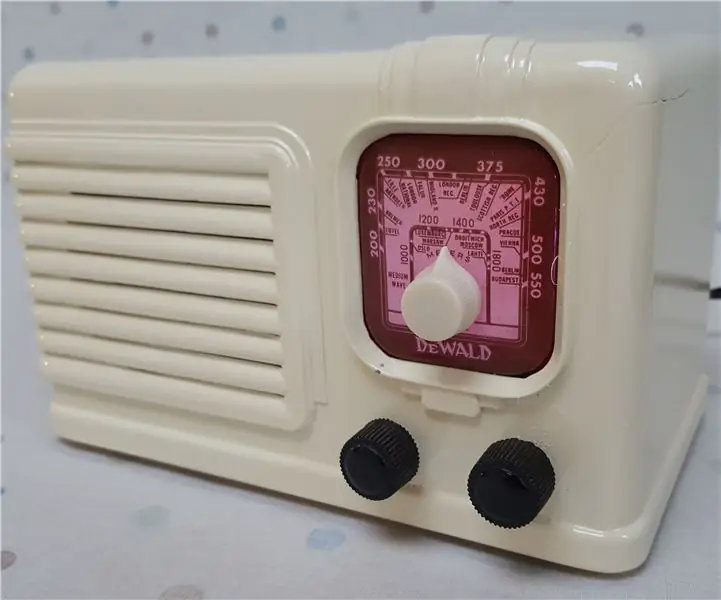
Pi Zero Talking Radio: esta es una radio de mesa DeWald de finales de la década de 1940 a la que le he dado una nueva vida usando una Raspberry Pi Zero, ¡una Blinkt! Tira de LED y un par de altavoces para PC. Lee las notificaciones de una variedad de servicios conectados a Internet utilizando el texto a voz de Pyvona (TTS)
Genial robot Instructables que se mueve: 11 pasos (con imágenes)
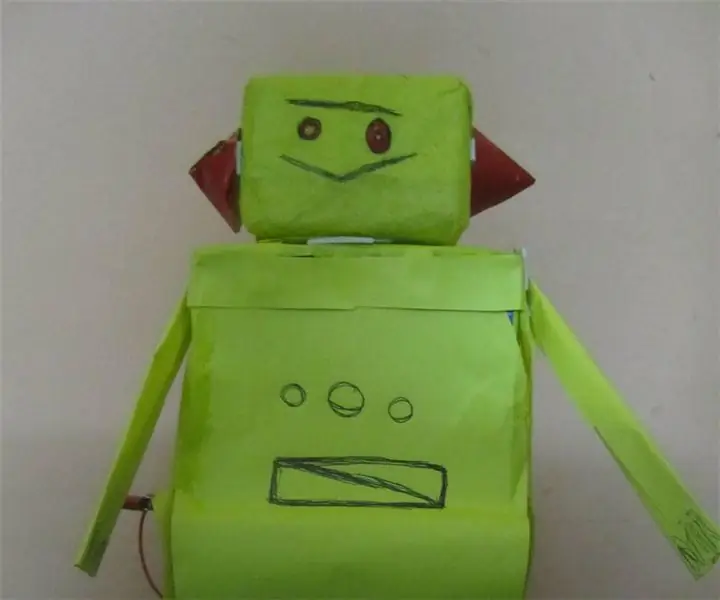
Cool Instructables Robot That Moves: si te gusta mi robot, vota por mí en el concurso de robots instructables.Es simple y fácil de hacer
RabbitPi: el asistente de IoT habilitado para Alexa, IFTTT conectado y que mueve los oídos: 12 pasos
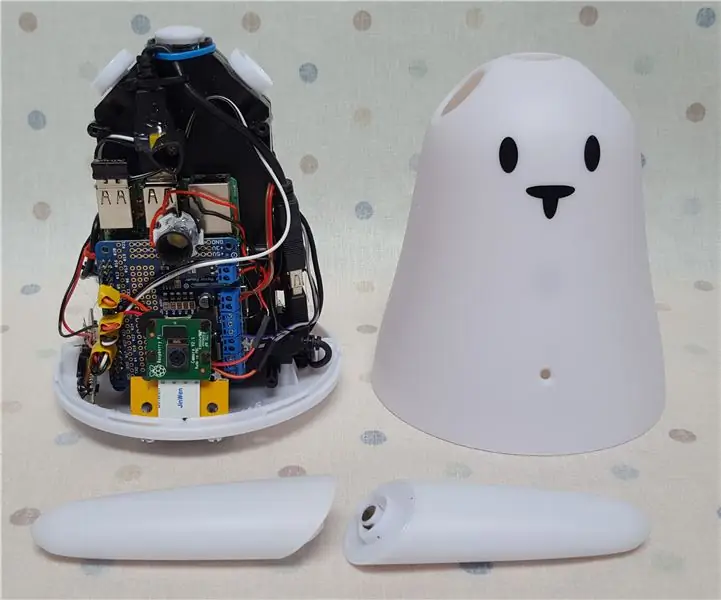
RabbitPi: el asistente de IoT habilitado para Alexa, IFTTT conectado y que mueve los oídos: este es un `` conejo inteligente '' de Nabaztag de 2005 obsoleto que he reconstruido en un moderno Asistente de IoT usando una Raspberry Pi 3 y un Adafruit Motor HAT, con un micrófono de cámara web y un altavoz Philips Soundshooter contenido en el lindo estuche original