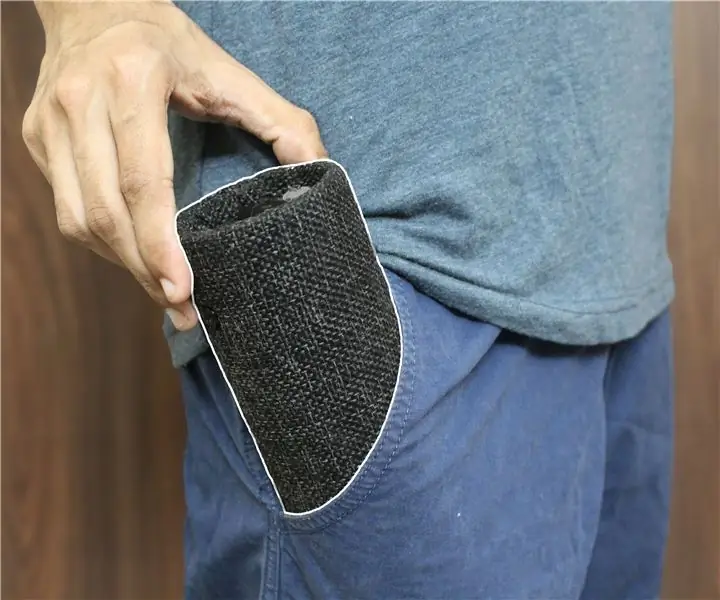
Tabla de contenido:
- Paso 1: contenedor de polvo
- Paso 2: componentes electrónicos
- Paso 3: impulsor
- Paso 4: Carcasa de componentes
- Paso 5: Sección superior de la carcasa del componente
- Paso 6: Cuerpo principal
- Paso 7: reparación de los circuitos en una hoja de fibra de vidrio
- Paso 8: Modificación de la carcasa de PVC y el cuerpo principal
- Paso 9: malla antipolvo
- Paso 10: Trabajo de tapicería
- Paso 11: Montaje final
- Paso 12: accesorios de boquilla
2025 Autor: John Day | [email protected]. Última modificación: 2025-01-23 14:39
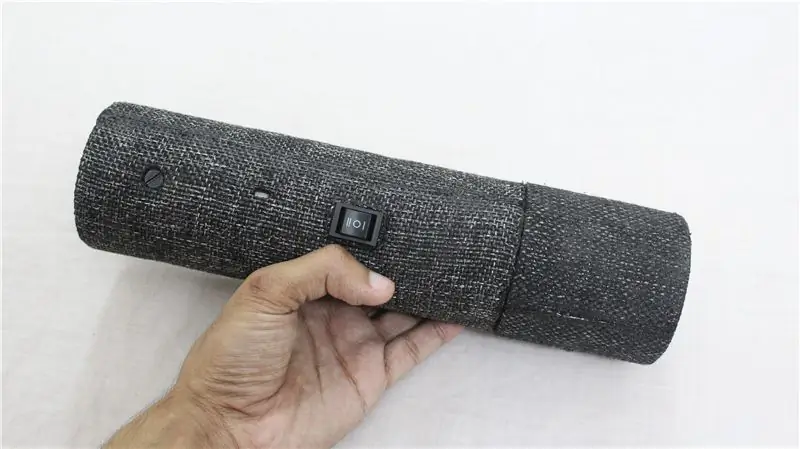
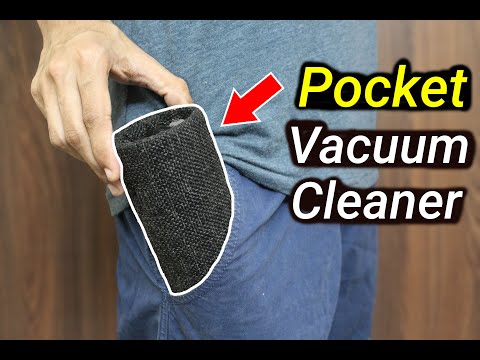
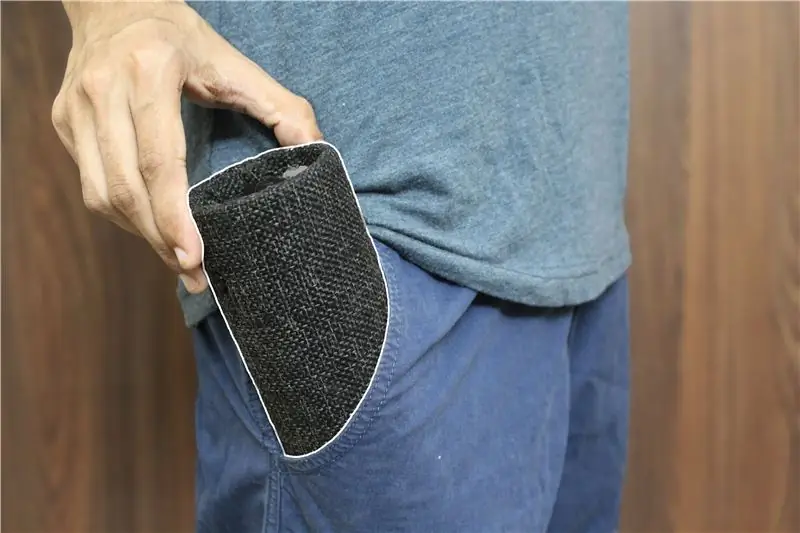
Hola a todos, espero que se estén divirtiendo con los bricolaje. Como habrás leído el título, este proyecto trata de hacer una aspiradora de bolsillo. Es portátil, conveniente y muy fácil de usar. Las características como la opción de soplador adicional, el almacenamiento de boquillas incorporado y las opciones de fuente de alimentación externa llevan las cosas a un nivel mejor que una aspiradora de bricolaje normal. El proceso de construcción total fue muy interesante y desafiante para mí, ya que involucró diferentes campos de trabajo como Electrónica, corte y moldeo por calor de PVC, ciertos aspectos de la artesanía, tapicería y algunos otros. Entonces, ¡profundicemos en la construcción! ¿Debemos?
Paso 1: contenedor de polvo
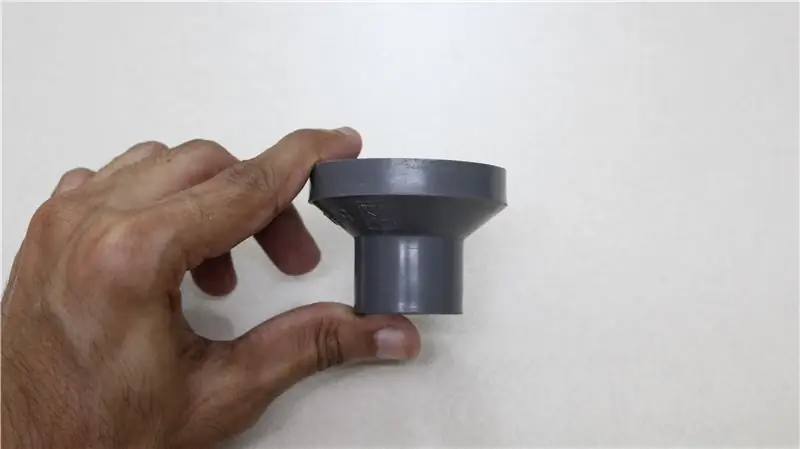
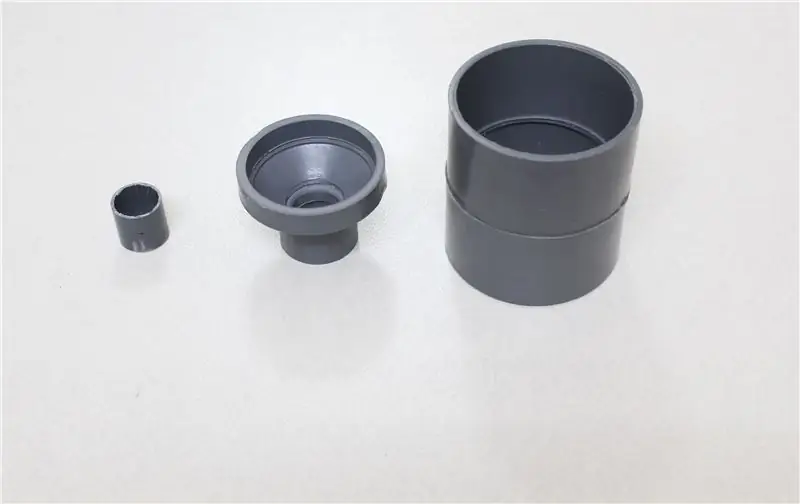
El contenedor de polvo tiene dos propósitos. Uno, para reducir el diámetro de la carcasa (boquilla). Esto ayuda a aumentar la velocidad de succión al final (efecto venturi). En segundo lugar, ayuda a recoger el polvo durante el proceso de succión.
Está hecho de dos accesorios de tubería de PVC. Un acoplador de PVC de 2 pulgadas y un reductor de PVC de 1,5 a 0,5 pulgadas. La longitud del lado de 1,5 pulgadas del reductor se toma como 1 cm y el resto se corta con una sierra para metales. Un tubo de 0,5 pulgadas se inserta temporalmente en el otro extremo de modo que se extienda a una longitud de 1 cm. Este lado se mantiene como parte inferior y se coloca dentro del acoplador de PVC de 2 pulgadas. La extensión anterior de PVC de 1 cm ayuda a elevar el reductor para proporcionar espacio para la opción de almacenamiento de la boquilla, que discutiremos en una etapa posterior. Ahora, con un taladro del tamaño adecuado, se perfora el contenedor de polvo y el reductor interior. Tenga en cuenta que estamos perforando en el lado de 1,5 pulgadas del reductor. Del mismo modo, se perforan 4 orificios para la inserción y fijación de los pernos. El espacio de aire restante dentro de la sección se sella luego con masilla epoxi. Esto terminó el contenedor de polvo. Pasemos al siguiente.
Paso 2: componentes electrónicos
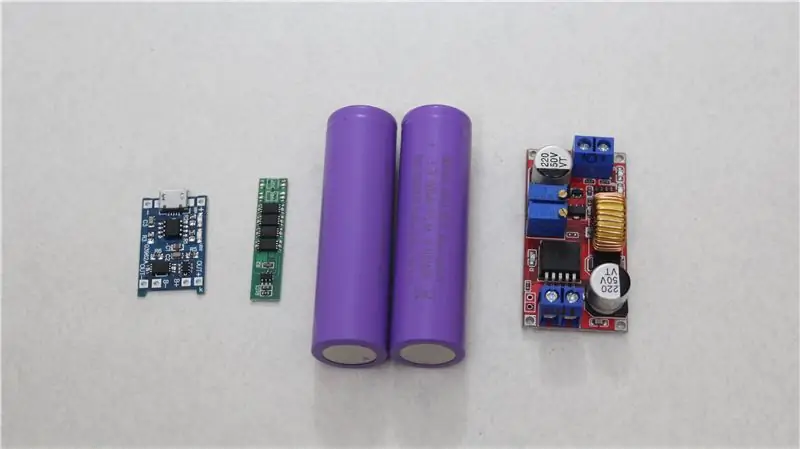
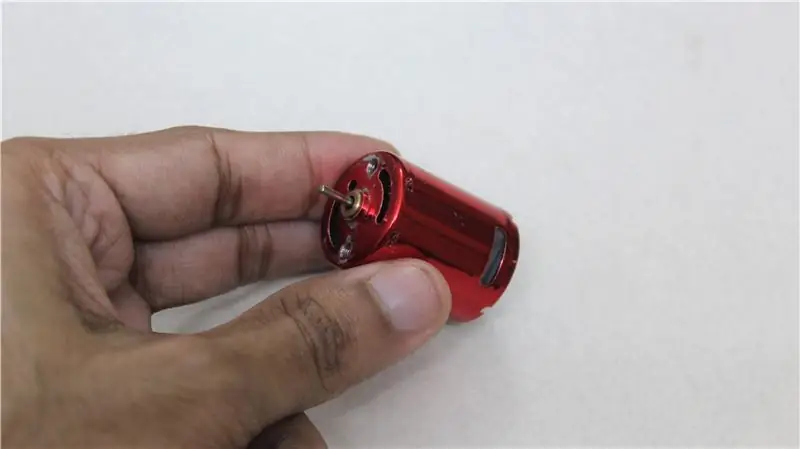
Se utilizaron un total de 5 componentes electrónicos para las funciones requeridas. Se mencionan a continuación.
1) Módulo convertidor reductor de corriente constante / voltaje constante
www.banggood.in/DC-DC-5-32V-to-0_8-30V-Pow…
2) placa del sistema de gestión de la batería 1S (placa BMS)
www.gettronic.com/product/1s-10a-3-7v-li-i…
3) 18650 celdas de iones de litio (se requieren 2 de ellas)
www.banggood.in/2PCS-INR18650-30Q-3000mah-…
4) Módulo de carga
www.banggood.in/5-Pcs-TP4056-Micro-USB-5V-…
5) Motor DC de 40, 000 rpm
www.banggood.in/RS-370SD-DC-7_4V-50000RPM-…
NOTA: Todos los enlaces anteriores son enlaces no afiliados y no lo estoy obligando a comprar el producto específico. Considérelo solo como referencia y también consulte varios sitios web y vendedores para obtener el precio más bajo disponible en su ubicación.
Ahora analizaremos cada uno de los componentes en detalle a continuación.
Módulo convertidor reductor de corriente constante / voltaje constante
Aunque podríamos conducir el motor de CC sin este módulo, agregar este módulo hace que nuestra aspiradora sea más flexible. El motor que estamos usando consume alrededor de 4.2 A a 7.4 V. En nuestro caso estamos usando las dos celdas de iones de litio en paralelo, el máximo que podríamos obtener es de alrededor de 4.2 V y bajaría a 3.7V y luego a 2.5V donde los circuitos se activan. y corta la descarga adicional. Mientras probaba la succión, descubrí que una corriente de 3 A para la celda de iones de litio hace un buen trabajo. Entonces, ir a 4.2 A más alto no es tan eficiente y más sobre agota la batería mucho más rápido. Por lo tanto, el consumo de corriente requerido de 3A se controla mediante este módulo. Por otro lado, establecer el nivel de voltaje en 7,4 V con el módulo nos ayuda a utilizar cualquier adaptador de CC por debajo de los 30 V. Se reduciría automáticamente a nuestros 7,4 V requeridos todo el tiempo y, por lo tanto, proporcionaría más flexibilidad de uso.
Placa del sistema de gestión de batería 1S (placa BMS)
La placa BMS proporciona la protección de sobrecarga y subcarga para las celdas de Li-ion. La placa de carga en sí es capaz de proporcionar esta función, pero está clasificada hasta un límite máximo de 3A. Llevar el circuito a su límite máximo no es una buena práctica de diseño, utilicé un BMS separado clasificado en 10A para esta función.
18650 celdas de iones de litio
Dos de estas celdas se utilizan en paralelo para una mayor capacidad. Asegúrese de que cada celda esté completamente cargada individualmente antes de conectarla en paralelo. La batería con un nivel de voltaje diferente cuando se conecta en paralelo, conduce a una carga rápida incontrolada de la celda inferior por la celda superior y, por lo tanto, no se recomienda.
Módulo de carga
Usar el módulo de carga es bastante sencillo. Dado que estamos usando un BMS en el lado de salida, los terminales de salida en el módulo de carga se dejan solos.
Motor de corriente continua de 40, 000 rpm
Una aspiradora típica en realidad funciona muy por debajo de las 40 000 rpm. Entonces, ¿por qué opté por un valor más alto? Bueno, esos son mucho más grandes que el que construyo. Esto favorece el uso de un impulsor más grande y más ancho para la succión requerida. Pero en nuestro caso, el tamaño era la mayor prioridad y debería ser lo suficientemente pequeño como para caber en un bolsillo. Entonces, usar un impulsor más grande no era nuestra opción. Para compensar esta limitación, opté por un motor de rpm más altas. El que utilicé es un motor de CC RS-370SD que tiene una potencia de 50, 000 rpm a 7,4 V sin carga.
Paso 3: impulsor
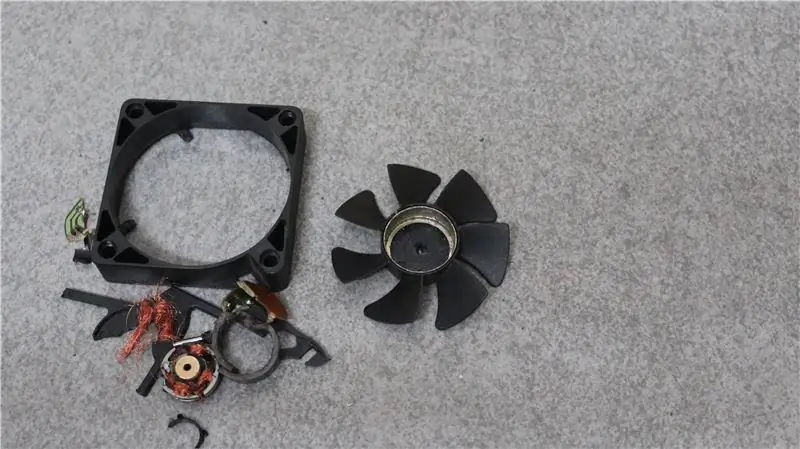
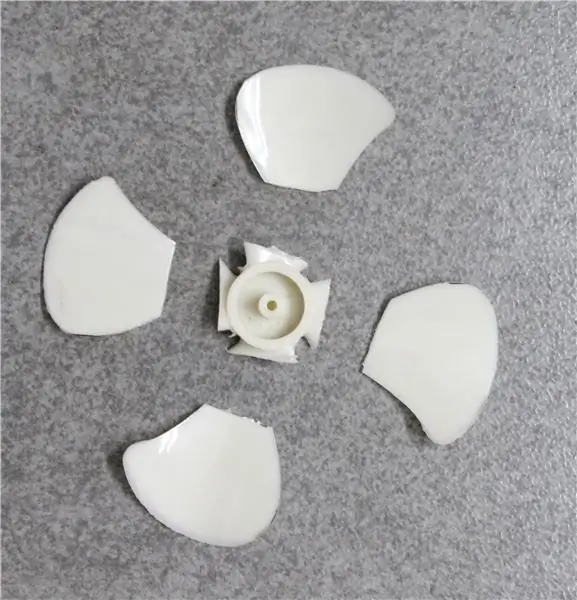
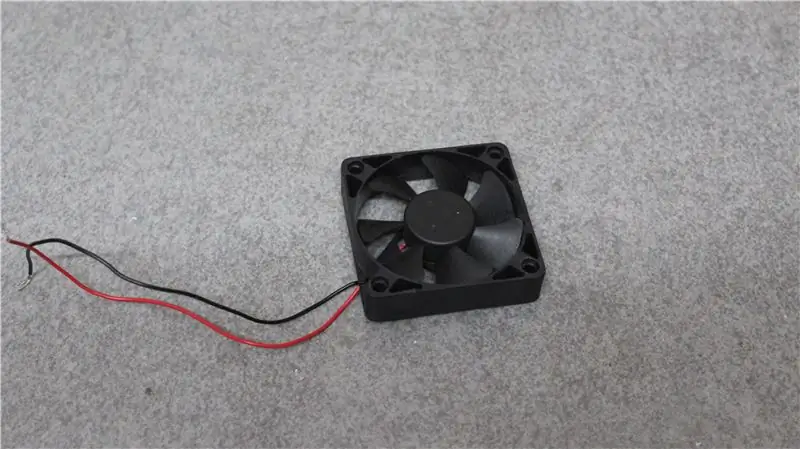
El impulsor es la parte principal de nuestro proyecto. Es lo que crea la opción de succión y soplador posible. Dado que el impulsor gira a una velocidad muy alta, el peso desequilibrado del impulsor en cualquier punto se sumaría a la vibración de toda la estructura durante su funcionamiento. Además, debe diseñarse fuerte para soportar la rotación a tan altas revoluciones por minuto. Si ha visto otros proyectos de aspiradoras de bricolaje, estará familiarizado con el proceso de corte de láminas de metal para hacer el impulsor. Es una buena técnica, pero a menudo el impulsor estaría desequilibrado en la distribución del peso. Teniendo en cuenta nuestro problema anterior con la vibración, abandoné este método y en su lugar utilicé un ventilador de refrigeración de CC como impulsor. Sin embargo, estos ventiladores están diseñados para ser motores de corredera y podemos encontrar un centro adecuado para sujetarlos al eje del motor. Por lo tanto, se utiliza un ventilador de juguete de plástico separado como punto de conexión. Las hojas se cortaron y se retuvo la parte central principal. Esto se fija aún más al impulsor con masilla epoxi.
Paso 4: Carcasa de componentes
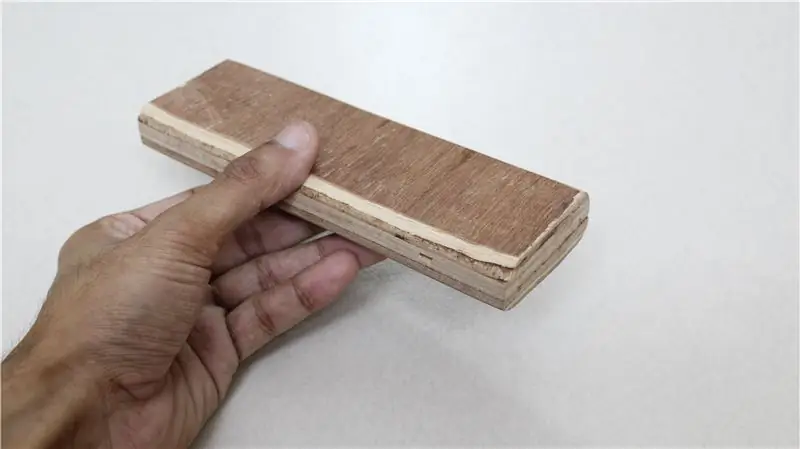
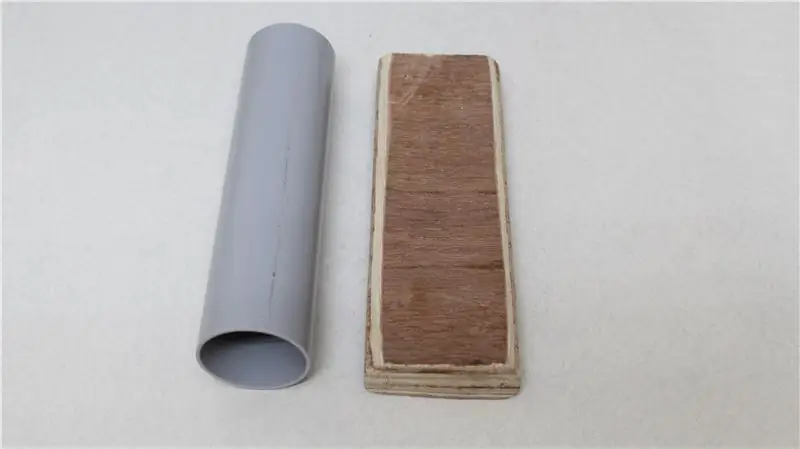
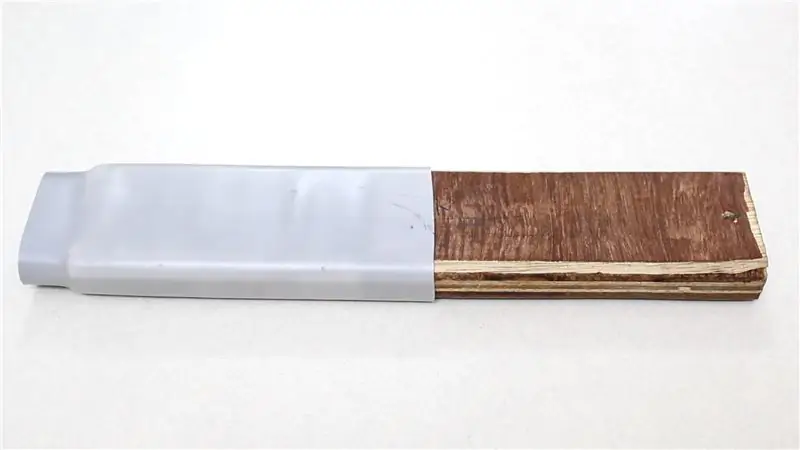
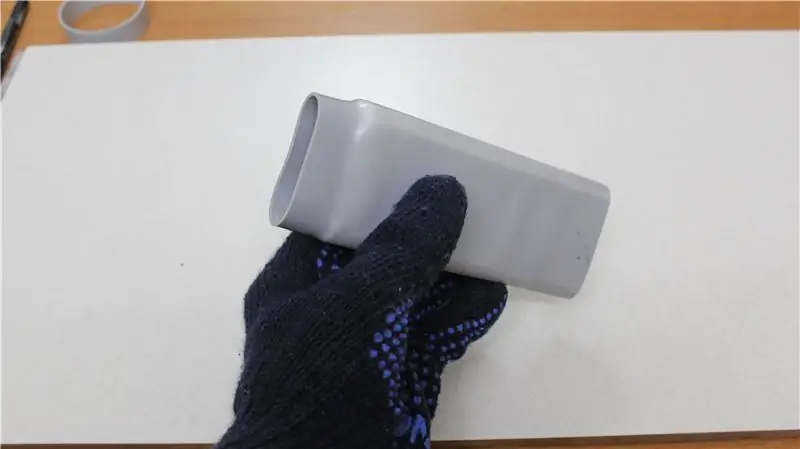
La carcasa del componente oculta todos los componentes electrónicos mencionados anteriormente. Esta pieza rectangular de carcasa se fabrica calentando un tubo de PVC de 1,25 pulgadas con una pistola de calor. Para adquirir la forma requerida, primero hice un troquel a partir de una sección de madera contrachapada. Tiene una anchura de 5,5 cm, una longitud de 16 cm y un grosor de 2 cm. Este troquel de madera se inserta en el tubo de PVC después de calentarlo completamente. Después de enfriar, se retira la matriz. Lo que tenemos ahora es una carcasa hueca rectangular abierta en ambos extremos. Uno de los extremos se vuelve a calentar, se corta y se dobla para cerrar ese lado. Esto completa la carcasa del componente.
Paso 5: Sección superior de la carcasa del componente
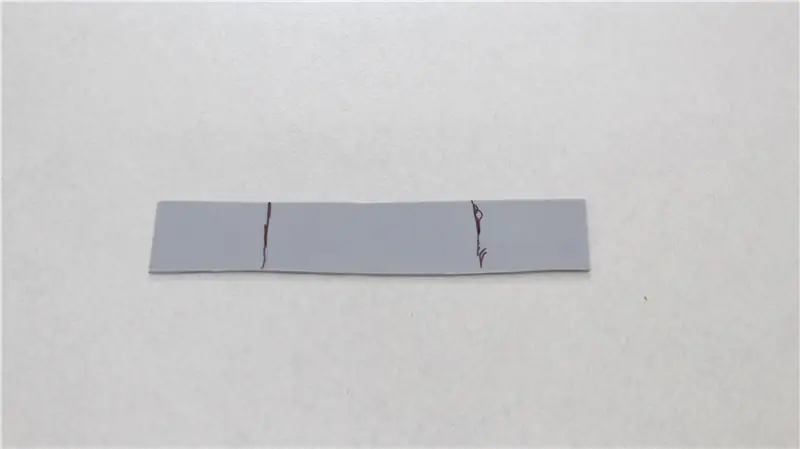
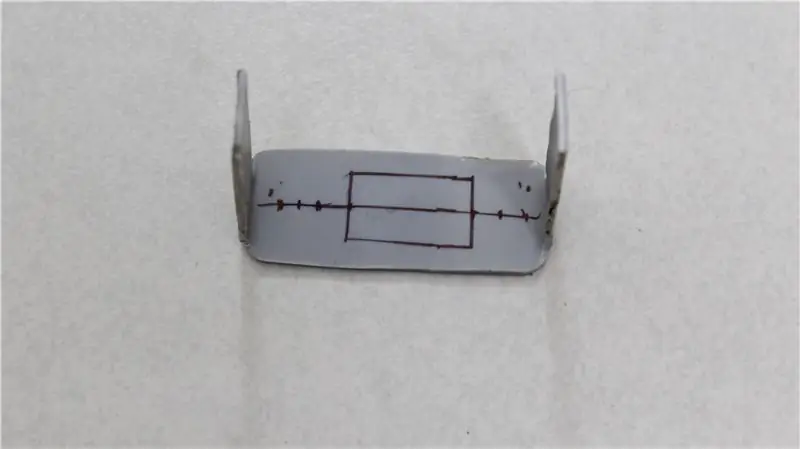
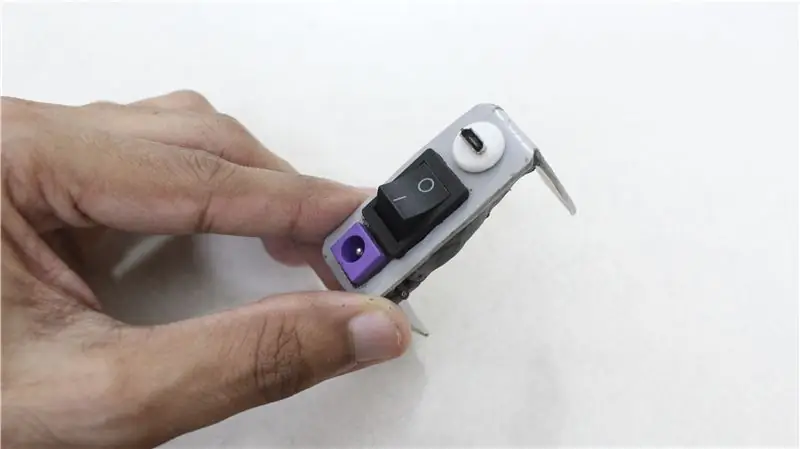
Esta parte contiene el puerto micro USB para cargar, el interruptor DPDT para alternar entre la función de succión y soplador y una toma de CC para alimentar directamente desde adaptadores de CC. Esta sección está hecha de una pequeña tira de tubería de PVC. Al calentarlo con una pistola de calor y luego aplicar presión sobre él, se convierte en una pieza plana. El extremo abierto de la carcasa del componente explicada anteriormente se coloca encima y el contorno se traza con un marcador. Además, los lados de la sección se calientan nuevamente con la pistola de calor y se pliegan hacia adentro de modo que esta sección actúe como una cubierta superior para la carcasa. Ahora hemos terminado con la forma básica y el siguiente paso es cortar las aberturas necesarias en la parte superior de esta sección para que pueda acomodar el enchufe y los interruptores. Usé un taladro y un extremo puntiagudo de una soldadura en caliente para hacer esta tarea. Ahora los enchufes y la bruja están insertados y para fijarlo en su lugar usé un poco de masilla epoxi. Asegúrese de que las clavijas estén bien expuestas y no cubiertas por el epoxi. Esto termina la sección superior y volveremos a su instalación en una etapa posterior de construcción.
Paso 6: Cuerpo principal
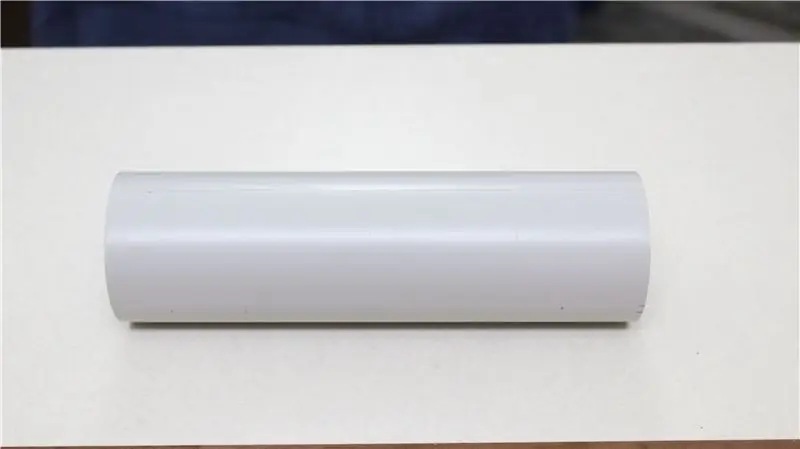
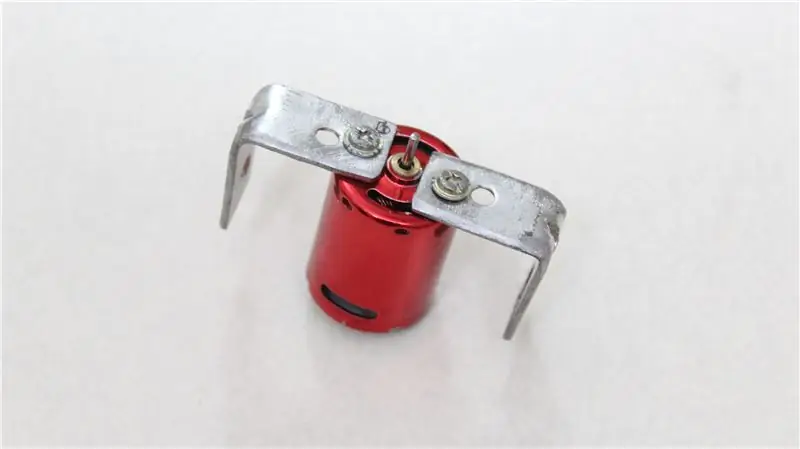
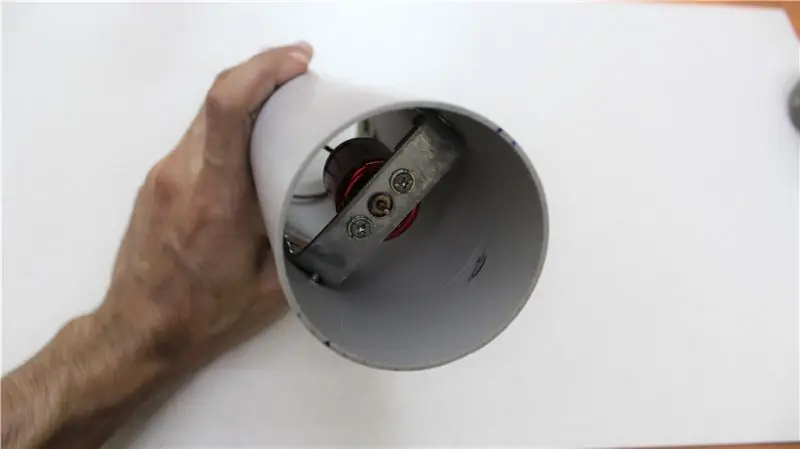
El cuerpo principal incluye la electrónica, el motor, el impulsor, los interruptores y los enchufes. Está hecho de un tubo de PVC de 2 pulgadas de 23 cm de longitud. La longitud depende de las especificaciones de tamaño de otros componentes utilizados en el proyecto. Por lo tanto, estos 23 cm son solo una estimación aproximada para mi proyecto. Por lo tanto, es mucho mejor construir este cuerpo principal hacia el último de la construcción.
En la parte delantera, el motor y el impulsor deben fijarse con dos abrazaderas en L. Primero, las abrazaderas en L se fijan al cuerpo del motor y los cables se sueldan desde los terminales. He utilizado una abrazadera en L estándar de 1 pulgada para este propósito, pero sería necesario cortar y ajustar la abrazadera en L para que encaje correctamente dentro del cuerpo principal. Una vez hecho esto, podríamos perforar los orificios correspondientes en el extremo frontal del PVC del cuerpo principal e insertar todo el motor y la configuración de la abrazadera en L dentro del cuerpo principal. Está unido al cuerpo principal mediante pernos. He utilizado una abrazadera en L estándar de 1 pulgada para este propósito, pero se necesitarían pequeños cortes y ajustes de la abrazadera en L para que encaje correctamente dentro del cuerpo principal. Mientras coloca la abrazadera en L, tenga en cuenta que debe dejar un pequeño espacio en la parte delantera (alrededor de 2 cm en mi caso) para que el contenedor de polvo pueda insertarse en una etapa posterior. Dado que el impulsor está diseñado para ajustarse a presión en el eje del motor, podríamos hacerlo en una etapa posterior de construcción. Así que pasemos al resto.
Paso 7: reparación de los circuitos en una hoja de fibra de vidrio
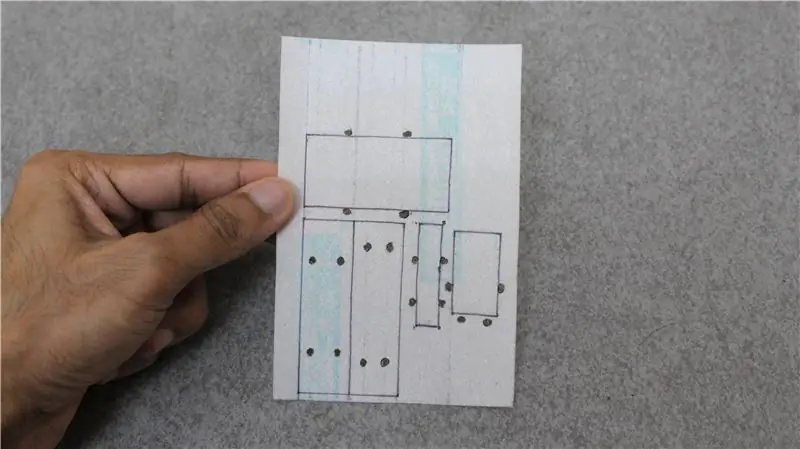
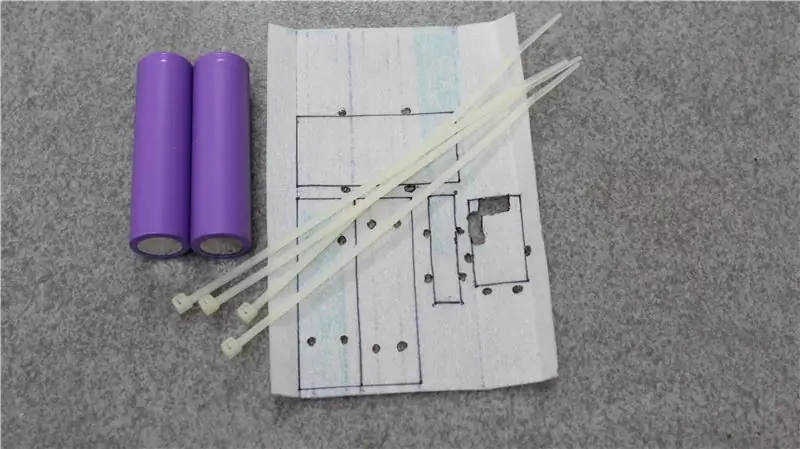
He seguido esta técnica en la mayoría de mis proyectos. La razón principal es la flexibilidad y conveniencia que brinda a la hora de colocar los componentes del circuito. La mayoría de nosotros que usamos placas de circuitos electrónicos sería consciente del hecho de que muchas de ellas no vienen con una forma adecuada de atornillar firmemente en una superficie. He estado lidiando con este problema durante mucho tiempo mientras hacía proyectos de bricolaje. Finalmente pensé en usar un trozo de lámina de fibra de vidrio y fijar los circuitos sobre él con bridas. En primer lugar, se corta un trozo de la hoja según nuestro requisito. Luego, las placas de circuito se colocan sobre él de manera que utilice el espacio de manera efectiva. El contorno se traza con un marcador y se hacen un par de agujeros alrededor de estos contornos. Estos orificios se utilizan para insertar las bridas para fijar los circuitos y se pueden hacer perforando con una punta de soldador caliente. Antes de fijar las placas, se sueldan los cables de todos los terminales de las placas de circuito.
Paso 8: Modificación de la carcasa de PVC y el cuerpo principal
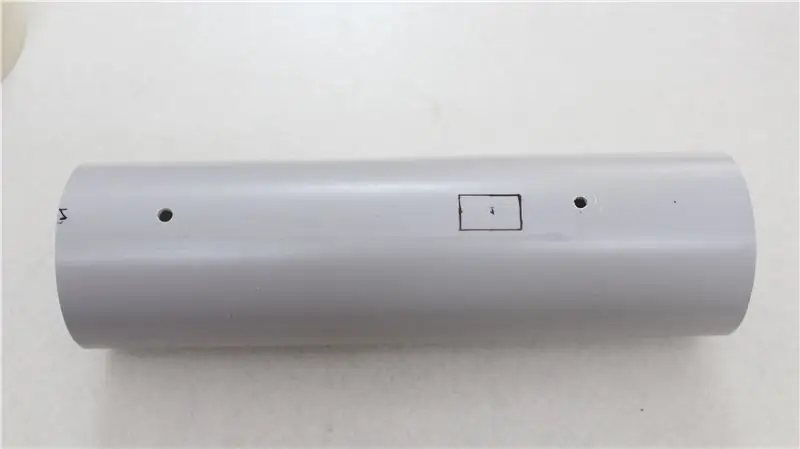
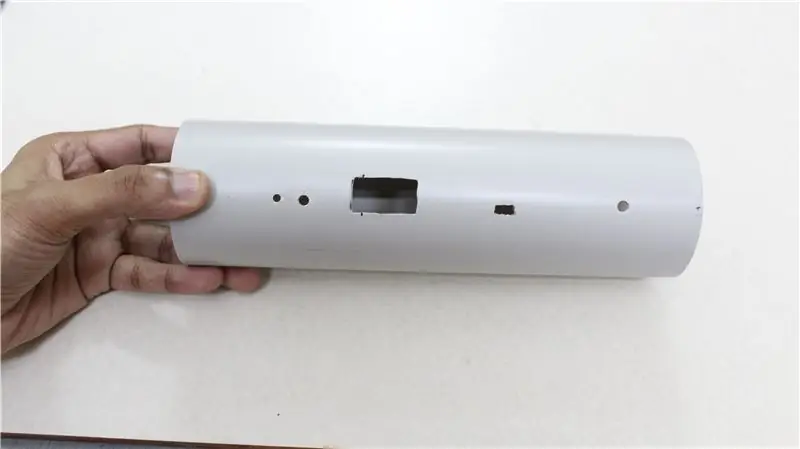
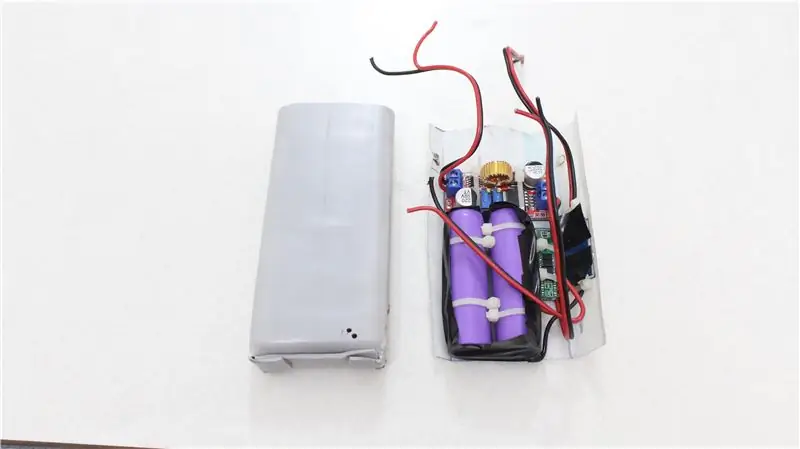
Este paso incluye una hendidura de corte para el interruptor de encendido y apagado, un orificio de perforación para el accesorio de la carcasa y una hendidura de corte para la luz indicadora de carga. Primero, inserte la carcasa del componente de PVC en el cuerpo principal hasta que toque el motor en el otro extremo. También asegúrese de que la carcasa esté un poco ajustada dentro del cuerpo principal. El uso de cinta adhesiva de doble cara fuera de la carcasa podría ayudar a conseguir un ajuste perfecto al insertar la carcasa. Luego, con un soldador caliente, haga una hendidura para el interruptor principal de encendido / apagado. La hendidura debe atravesar el cuerpo principal y la carcasa en su interior. Luego taladre un orificio pasante para fijar la carcasa en una etapa posterior con un perno. Una vez hecho esto, podríamos quitar la carcasa del cuerpo principal. La sección superior del interruptor ahora está insertada en la carcasa y los mismos orificios perforados en sus 2 patas. Una vez hecho esto, podríamos insertar los componentes del circuito (capa sobre la hoja de fibra de vidrio) en él. Luego, la sección superior del interruptor se conecta y se suelda de acuerdo con el diagrama de cableado que proporcioné en este paso.
Paso 9: malla antipolvo
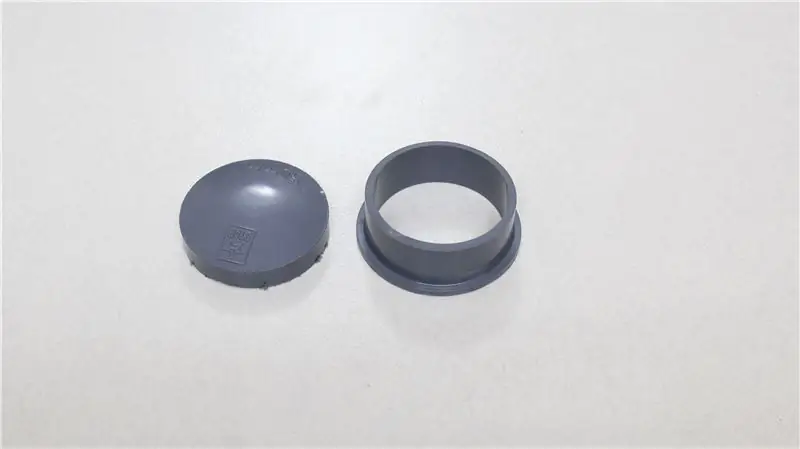
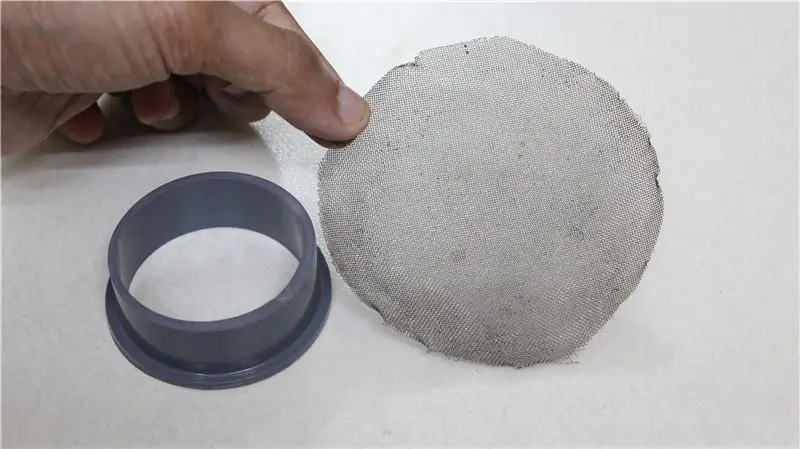
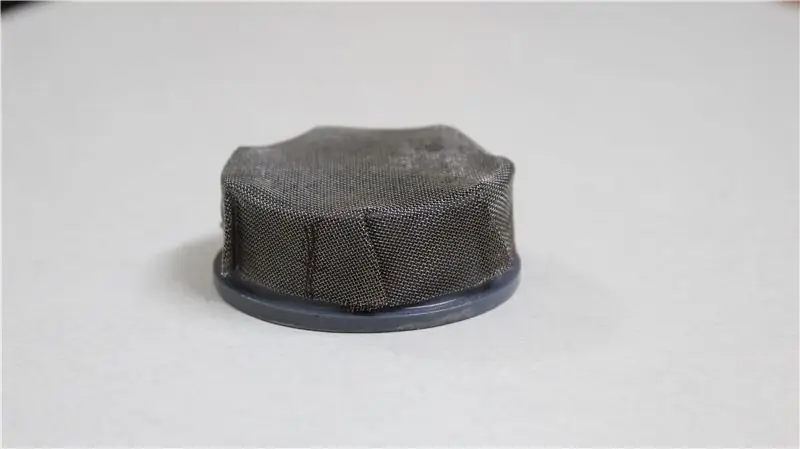
La malla de polvo actúa como un colador entre el impulsor y el contenedor de polvo, recogiendo así todas las partículas de polvo dentro del contenedor de polvo. La carcasa exterior está hecha de una tapa de PVC de 1,5 pulgadas. El lado cerrado se corta para obtener una estructura similar a un anillo. Luego, se dobla una malla metálica del tamaño apropiado sobre este lado recién cortado. Además, se fija correctamente perforando 4 orificios en los lados y luego se fija con algunos pernos. Esta sección podría insertarse posteriormente en la parte frontal del cuerpo principal.
Paso 10: Trabajo de tapicería
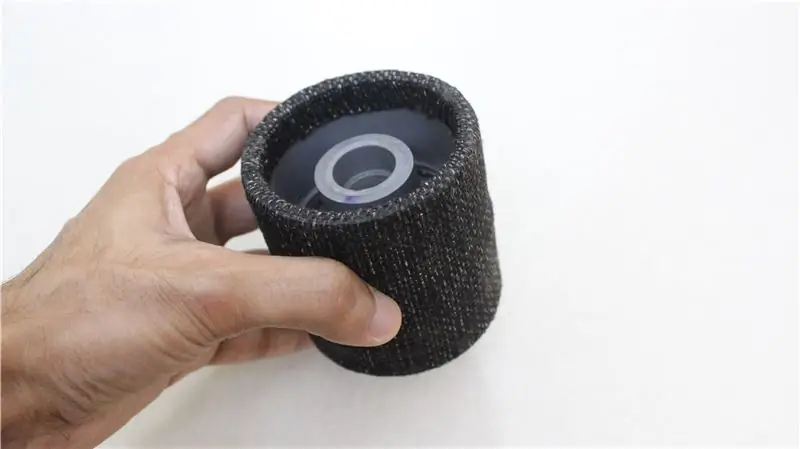
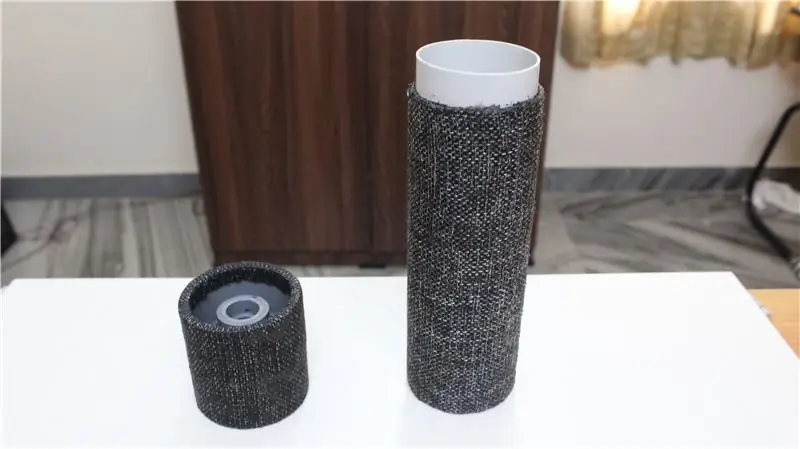
La mayoría de los procesos quedarían claros al ver el video. Así que no estoy explicando las cosas en detalle aquí. Usé un paño de yute negro y adhesivo de caucho sintético (cemento de caucho) para el trabajo de tapizado. Tanto el cuerpo principal como el contenedor de polvo están cubiertos adecuadamente con el paño. Pasemos al siguiente.
Paso 11: Montaje final
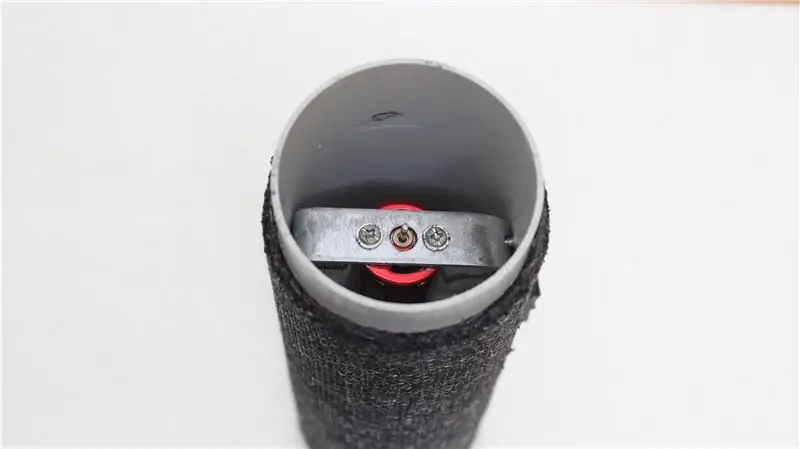
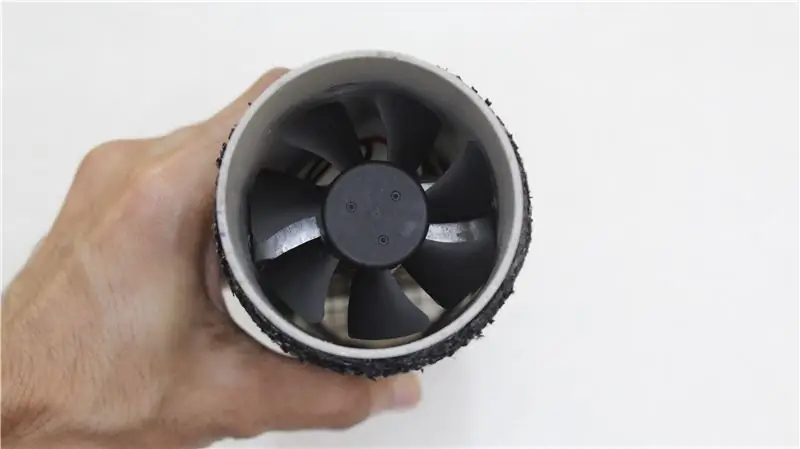
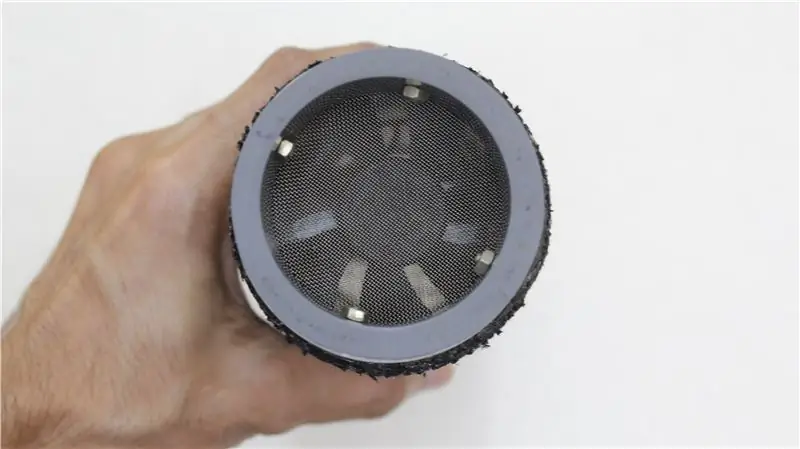
La carcasa del componente anterior ahora se inserta en el cuerpo principal. Los dos cables del motor ahora están soldados a los terminales respectivos. Todos los demás cables se sacan a través de la ranura del interruptor de encendido / apagado. La sección superior del interruptor ahora se presiona sobre la carcasa para que todos los orificios queden alineados correctamente. Ahora se inserta un perno a través de estos orificios y, por lo tanto, se fija la carcasa y la sección superior al cuerpo principal. Ahora podríamos pasar al conjunto final de conectar el interruptor de encendido / apagado en el lateral. Consulte el diagrama de cableado para conocer las conexiones. Ahora podríamos insertar el impulsor, la malla de polvo y el contenedor de polvo en la parte delantera.
Paso 12: accesorios de boquilla
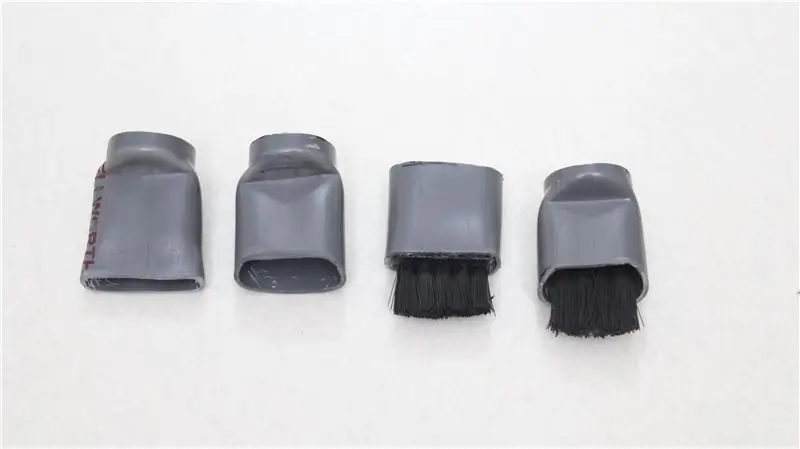
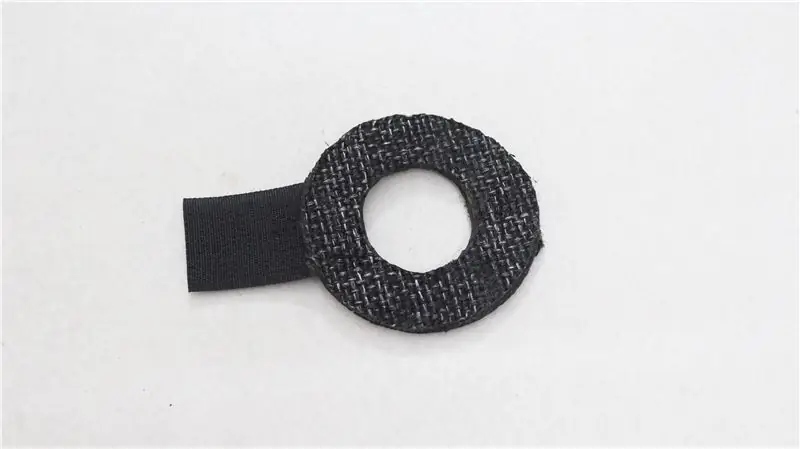
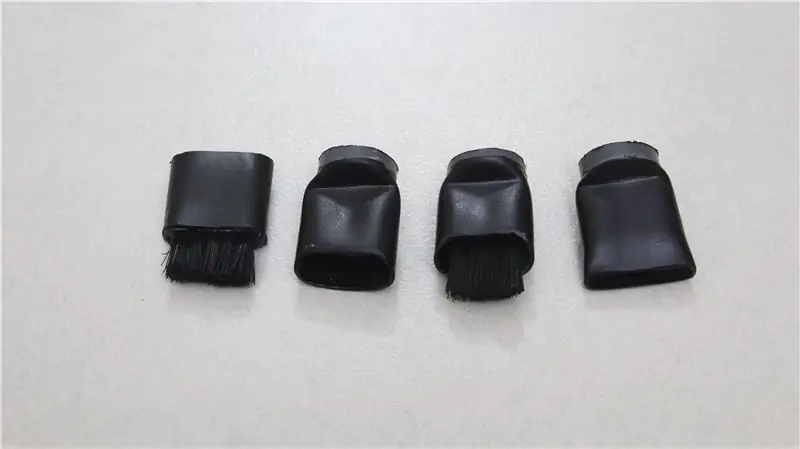
Como se mencionó al principio de este artículo, el almacenamiento de boquillas incorporado es una buena característica de esta aspiradora. Ya hemos dejado espacio para el almacenamiento al diseñar el contenedor de polvo. La mayoría de las cosas están claras en el video tutorial en sí. Todas las boquillas están hechas de tubos de PVC de 0,5 pulgadas. Se calienta para lograr diferentes tamaños y formas. También agregué un cepillo pequeño en la parte delantera de una de las boquillas para eliminar el polvo fácilmente. El cepillo se toma rompiendo un cepillo de tinte para el cabello y luego pegándolo dentro de la boquilla con adhesivo epoxi.
Para tapar la abertura frontal del contenedor de polvo, tengo un trozo de la misma tela de yute que se ha utilizado en el anterior trabajo de tapizado. Con un accesorio de velcro como se muestra en el video, se coloca en la parte delantera.
Así que esto completa la compilación. Déjame saber tus pensamientos en la sección de comentarios a continuación. Los veo en mi próximo proyecto.
Recomendado:
Visualizador de señales de bolsillo (osciloscopio de bolsillo): 10 pasos (con imágenes)
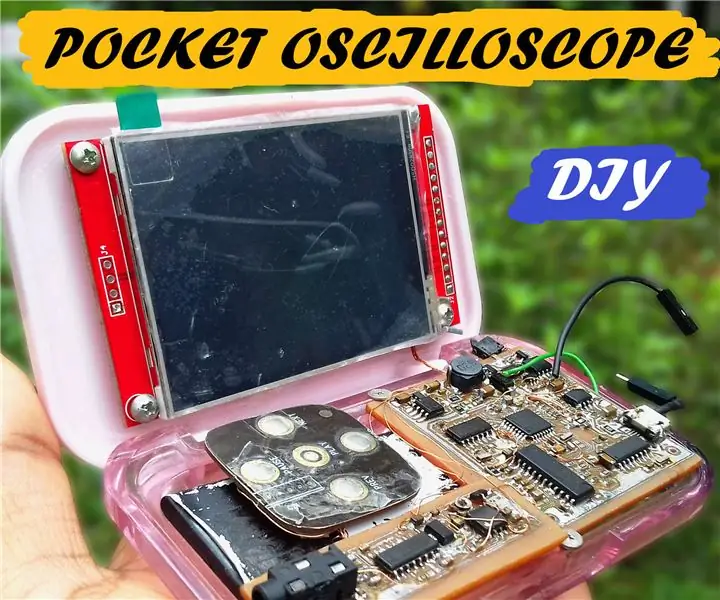
Visualizador de señal de bolsillo (osciloscopio de bolsillo): Hola a todos, todos estamos haciendo tantas cosas todos los días. Para cada trabajo allí donde se necesitan algunas herramientas. Eso es para hacer, medir, terminar, etc. Entonces, los trabajadores electrónicos necesitan herramientas como soldador, multímetro, osciloscopio, etc
Conversión de aspiradora Ni-MH a Li-ion: 9 pasos (con imágenes)
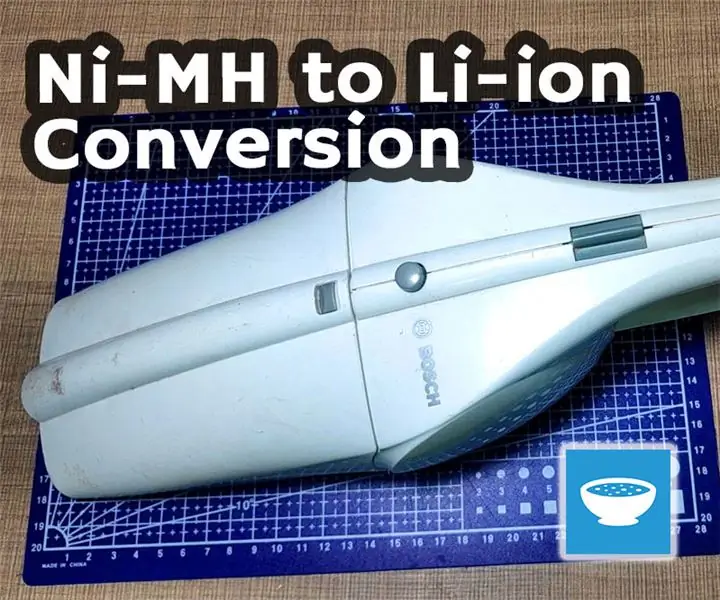
Conversión de aspiradora Ni-MH a Li-ion: Hola a todos, En este Instructable, convertiremos mi aspiradora de mano de Ni-MH a baterías de Li-ion. Esta aspiradora tiene cerca de 10 años pero en los últimos 2 años , casi nunca se usó ya que desarrolló un problema con sus baterías
Aspiradora XiaoMi + Botón Amazon = Limpieza del tablero: 5 pasos (con imágenes)
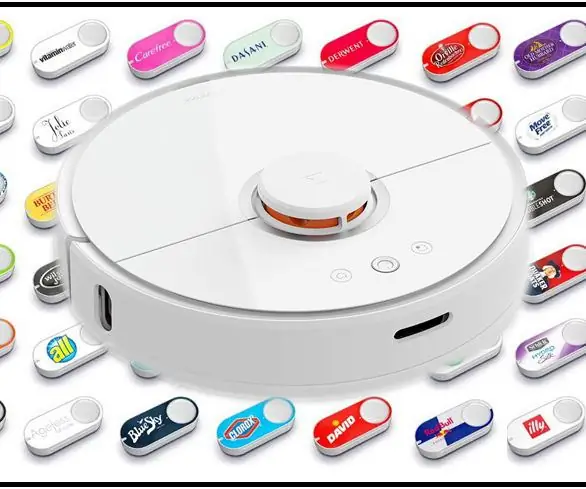
Aspiradora XiaoMi + Botón de Amazon = Limpieza del tablero: esta instrucción explicará cómo usar sus botones de tablero de Amazon de repuesto para controlar la aspiradora XiaoMi. Tengo un montón de Amazon Buttons por ahí de los tiempos en que costaban $ 1 y no los usaba. Pero al recibir un nuevo robot aspirador, decido
La primera aspiradora del mundo en una lata de Altoids: 18 pasos (con imágenes)
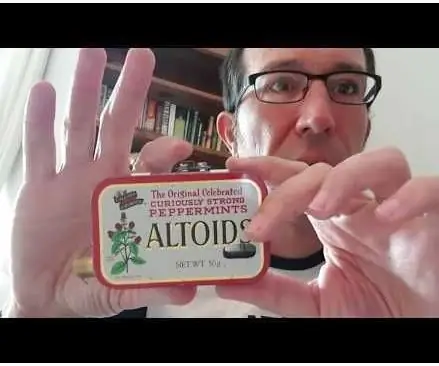
La primera aspiradora del mundo en una lata de Altoids: me encanta hacer pequeñas aspiradoras y he fabricado muchas de ellas desde que empecé hace más de 30 años. Los primeros fueron en botes de película de plástico negro con tapas grises con clip o estuches para fiestas. Todo comenzó cuando vi a mi madre luchando con
Aspiradora de un secador de pelo: 7 pasos (con imágenes)
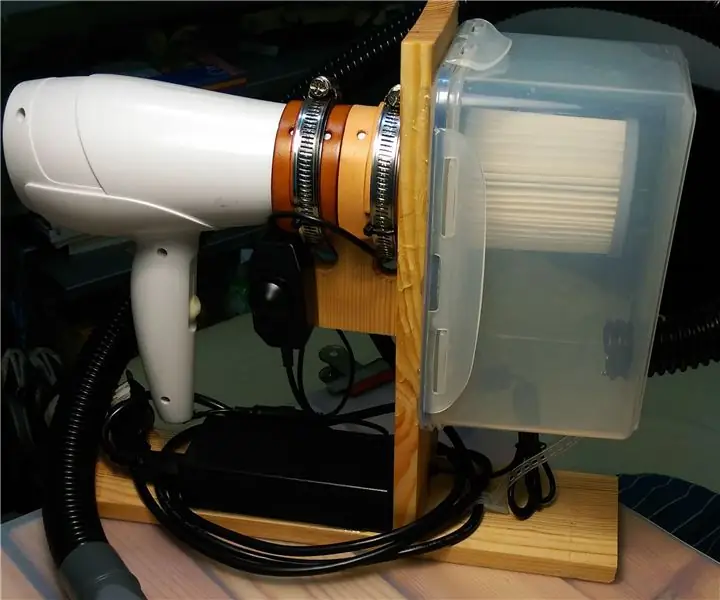
Aspiradora de un secador de pelo: En los últimos días, comencé a buscar una aspiradora para mantener limpio mi escritorio y encontré algo de basura en mi espacio de almacenamiento, hagamos una aspiradora de bricolaje