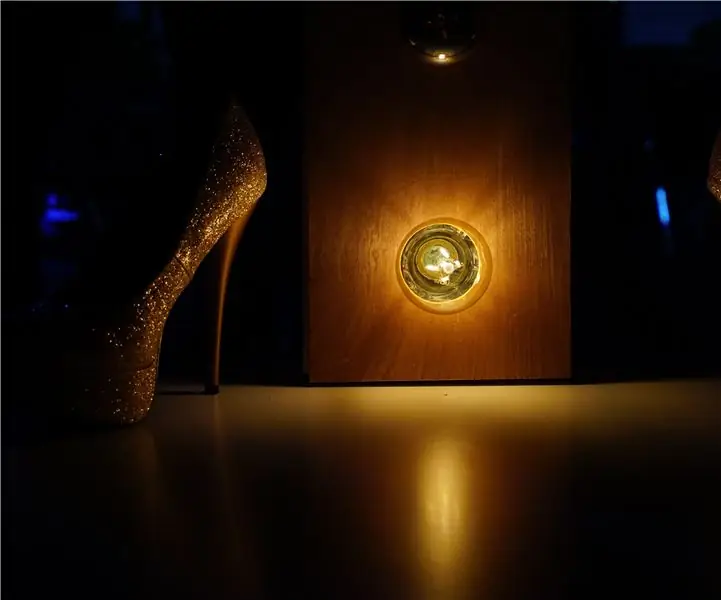
Tabla de contenido:
- Suministros
- Paso 1: Circuito de 5 V: Arduino
- Paso 2: diseñar la caja
- Paso 3: construcción de la caja
- Paso 4: instalación de los enchufes en la caja
- Paso 5: Soldar la electrónica de bajo voltaje
- Paso 6: Conexión de los componentes de 220 V
- Paso 7: pargos magnéticos (opcional)
- Paso 8: Qué haría de otra manera
2025 Autor: John Day | [email protected]. Última modificación: 2025-01-23 14:39
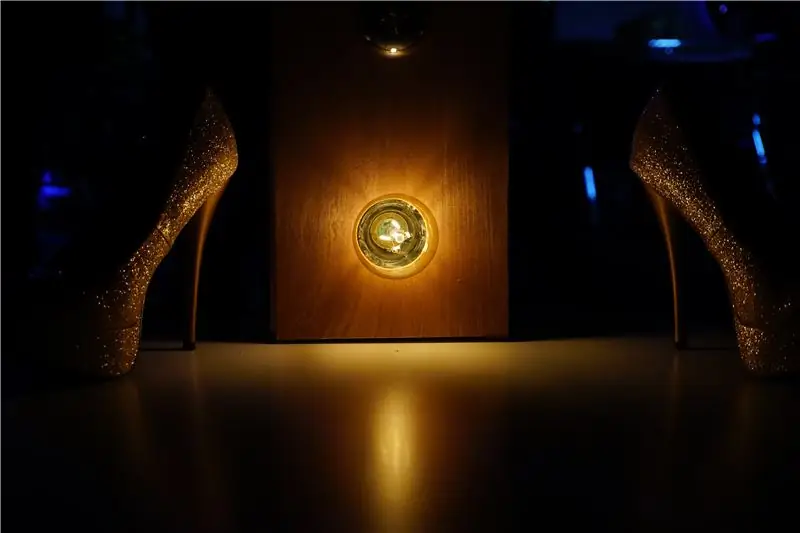
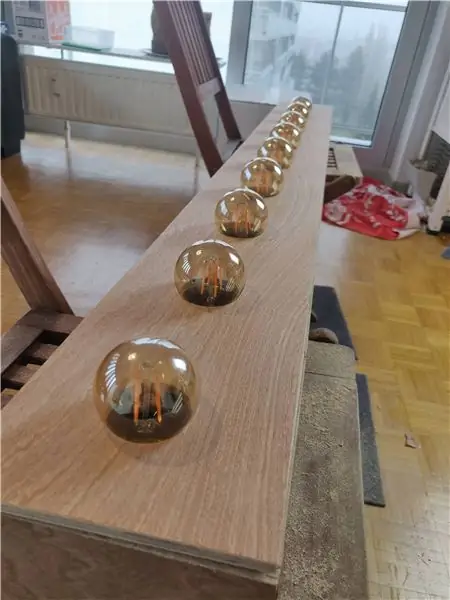
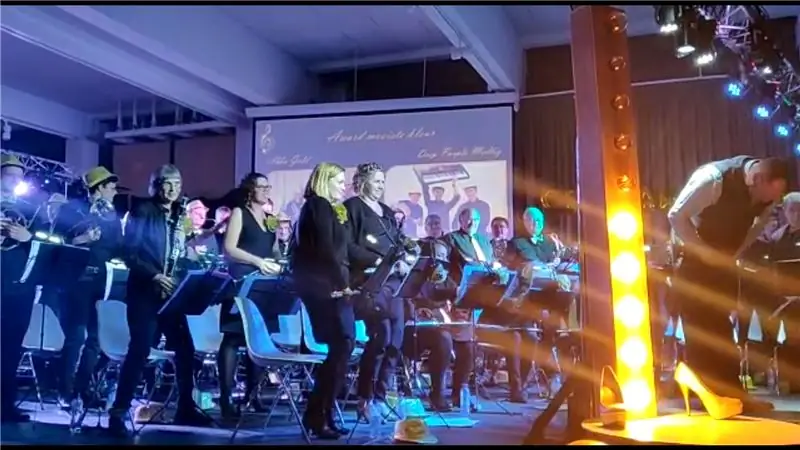
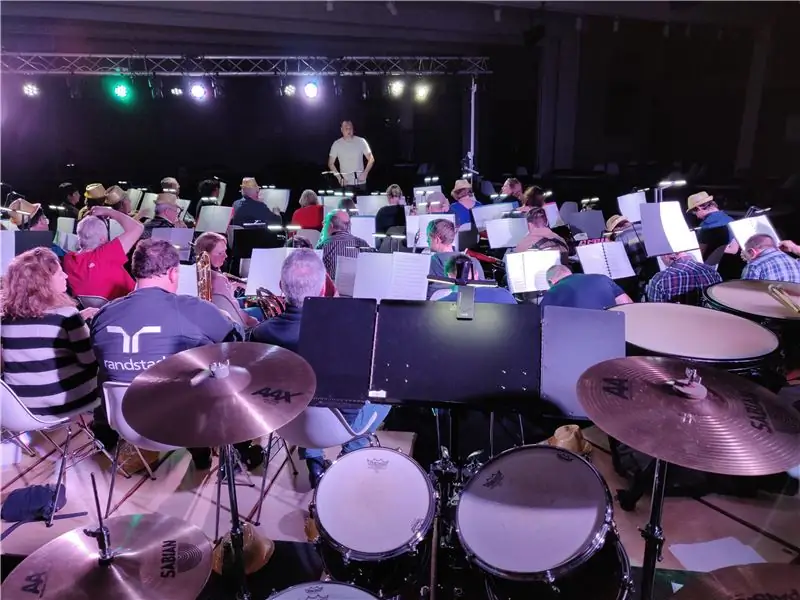
Desde alrededor del año 2001 comencé a tomar lecciones de batería. Después de diez años, en 2011, me uní a mi primera banda de conciertos y me enganché. Hacer música juntos y tocar en un concierto es estimulante. Ahora estoy en una banda de concierto diferente desde hace ya más de 5 años. Tenemos dos conciertos al año y varios encargos paralelos.
Como tema de nuestro concierto de año nuevo queríamos realizar una ceremonia de premiación a las mejores canciones que hemos tocado. La configuración fue que tocábamos dos canciones en cada categoría. Por ejemplo, "Hielo contra fuego" para el que jugamos un popurrí de "Frozen" y uno de "Cómo entrenar a tu dragón". Luego, la audiencia debe votar por la mejor canción, que luego recibirá un premio personalizado impreso en 3D.
Durante la lluvia de ideas durante los preparativos, tuvimos muchas ideas sobre cómo hacer que la audiencia votara, desde votos en papel hasta aplicaciones. Pero todas esas sugerencias requieren que el espectáculo se detenga para cada premio, mientras que distrae seriamente a la audiencia. Cuando se sugirió un medidor de aplausos, todos supimos que habíamos dado en el blanco. Pero algunas búsquedas en línea no revelaron una solución realmente lista para usar. Así que me levanté con valentía, me declaré fabricante novato y dije que podía construir uno fácilmente desde cero con un presupuesto bastante pequeño.
Oh, vaya, no estaba preparado para la madriguera del conejo en la que caería.
Suministros
Instrumentos
- Tu taladro inalámbrico favorito
- Broca circular y otras brocas
- destornilladores
- Impresora 3D (opcional)
Caso
- Madera contrachapada. (Elijo multiplex de 8 mm, pero en retrospectiva, debería haber optado por 12 mm o incluso más grueso)
- 4 x cierre magnético de puerta (opcional en retrospectiva)
- Empulgueras
Electrónica (5V)
- Arduino Nano
- Amplificador de micrófono electret - MAX4466 con ganancia ajustable (o similar, lo que se adapte a sus necesidades)
- Módulo de relé de 2 X 5V 8 canales
- Transformador de 220V a 5V
- cables, muchos cortos y un cable de cuatro hilos de varios metros para el control 'remoto'
- dos interruptores
Electrónica (220V)
- cables eléctricos estándar (los sobrantes de la construcción de la casa son ideales, pero lo mejor es que sean flexibles)
- Toma de corriente CA con fusible (opcional pero muy recomendable)
- Bombillas de tu elección
- Casquillos de bombilla
Paso 1: Circuito de 5 V: Arduino
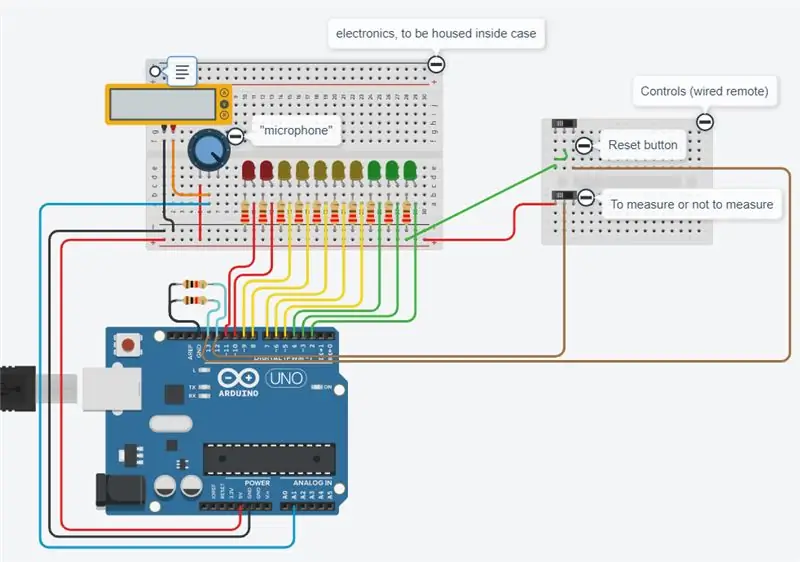
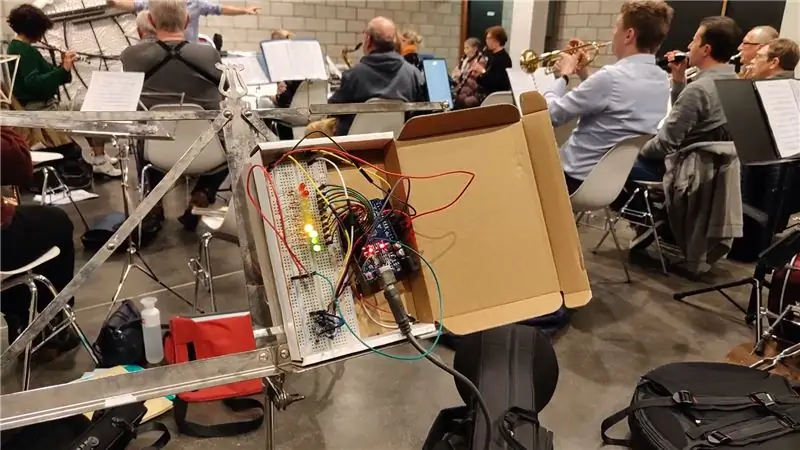
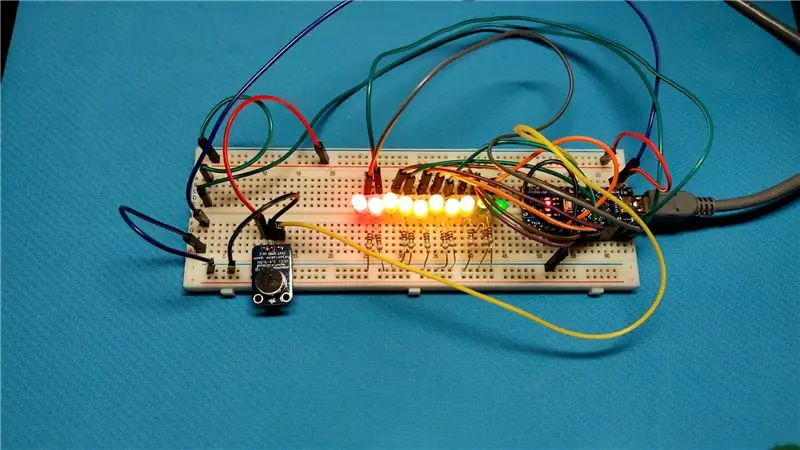
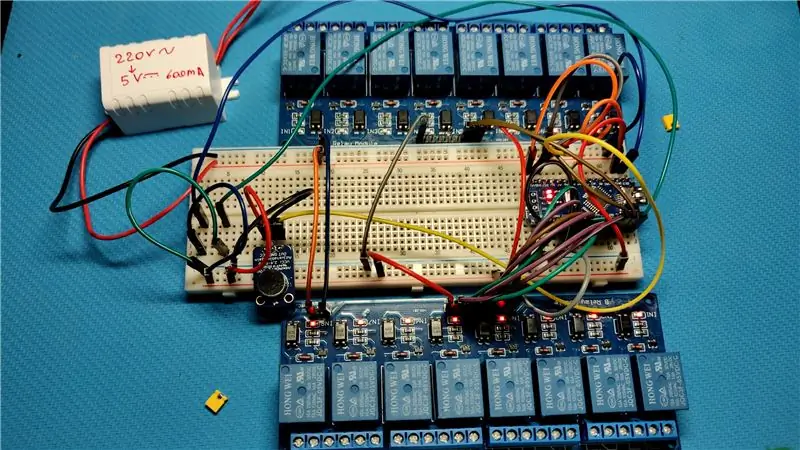
Hay tres partes principales en esta construcción: (1) la electrónica de 5V que hará el "pensamiento duro": escuchar y decidir cuándo y qué luces encender; (2) la carcasa para encajar todo perfectamente, oculta todos los 'delitos', y (3) el circuito de 220 V que está controlado por el circuito de 5 V.
Comencemos con los circuitos de 5V, ya que podemos construirlos a pequeña escala.
No fue una tarea fácil encontrar recursos en línea. Imaginé diez luces, que se encendieron según el volumen de los aplausos, pero nadie parecía haber hecho esto antes. Entonces, comencé pequeño; En tinkerCAD construí una simulación en línea de cómo quería que se vieran las partes electrónicas de 5V. Puede encontrar mi diseño muy rudimentario con código aquí: https://www.tinkercad.com/things/8mnCXXKIs9M o más abajo en esta página como archivo "Applause_1.0.ino".
Hacer una versión preliminar en línea y probar varios códigos de Arduino en esta simulación realmente me ayudó a tener una mejor visión de lo que se necesitaba para esta compilación. De esta manera experimenté agregando una forma de controlar el comportamiento del programa: terminé con dos interruptores. Un interruptor enciende y apaga la medición, el otro restablece la puntuación a 0/10.
Conseguí todos los componentes necesarios: algunos LED, resistencias, un Arduino y, lo más importante, un micrófono compatible con Arduino.
Construí el circuito y probé todo en el siguiente ensayo, solo para darme cuenta de que el micrófono que compré era demasiado sensible para mi uso. Solo un aplauso a una proximidad razonable, o solo la banda tocando, saturaría el micrófono dando una puntuación de 10/10. Esto me llevó a buscar un micrófono con ganancia variable. Finalmente me decidí por el amplificador de micrófono Electret - MAX4466. Tiene un tornillo muy pequeño en la parte posterior con el que puede ajustar la ganancia. (nota al margen: también cambié el Arduino uno por un Arduino Nano sin ningún motivo en particular).
El MAX4466 funcionó mejor, pero también alcanzó el máximo cuando aplaudió muy cerca, por lo que decidí incluir también el tiempo de aplauso como una variable en la fórmula en lugar de solo el volumen de los aplausos. También escribí un código un poco más elegante para esta versión 2.0 del software (incluso si lo digo yo mismo). Si se sobrepasaba un umbral de sonoridad, solo se encendía la primera luz seguida de una breve pausa durante la cual no se podía encender ninguna luz. Después de esperar, Arduino escucharía si el sonido aún era lo suficientemente fuerte como para que se encienda la segunda luz, si es así, la luz se enciende y se activa el siguiente período de espera. El tiempo de espera aumentaría cada vez que se encendiera una nueva luz. Un aplauso debería durar 22,5 segundos a todo volumen para que las luces muestren 10/10. Puede encontrar el código en tinkerCAD https://www.tinkercad.com/things/lKgWlueZDE3 o debajo como archivo "Applause_2.0.ino"
Una prueba rápida con los módulos de relés conectados en lugar de los LED me enseñó que los relés estaban ENCENDIDOS cuando la señal era BAJA y APAGADOS cuando la señal era ALTA. No hay problema, simplemente cambiando algunos ENCENDIDOS y APAGADOS en el código y estábamos listos para comenzar.
Con todo esto resuelto. Podría empezar a soldar todo junto. Pero necesitaba saber cuánto tiempo deberían durar todas las conexiones dentro de la caja. Primero construyamos la caja exterior y organicemos todos los componentes en ella.
Paso 2: diseñar la caja
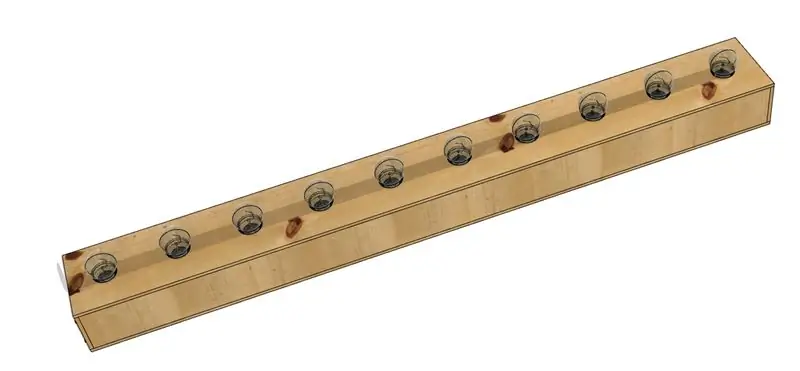
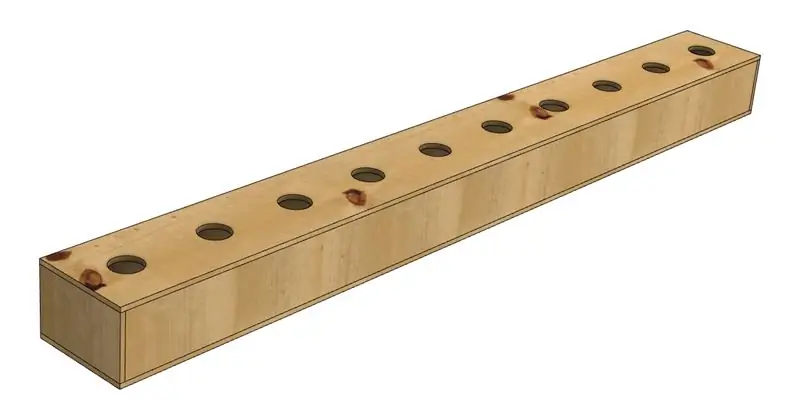
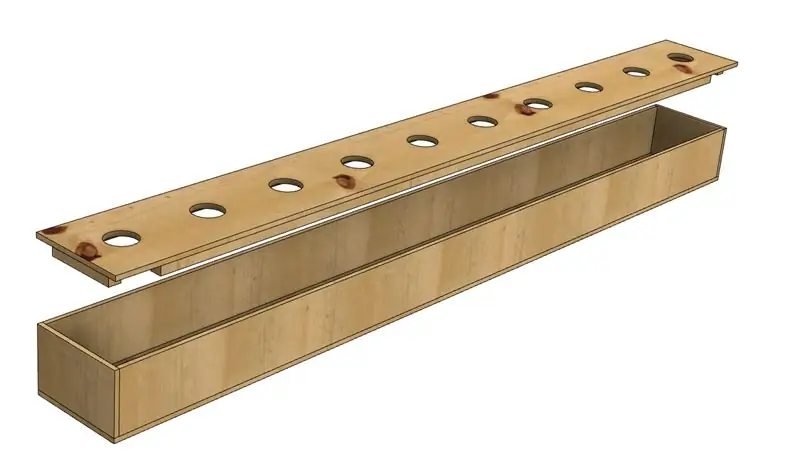
Un segundo aspecto de esta construcción fue su estética. El medidor de aplausos estaría en el medio de la atención, por lo que al menos tenía que verse bien. Elegí construir una caja de madera ya que tengo las herramientas básicas para ello y es relativamente fácil.
Habiendo aprendido en tinkerCAD que experimentar en el mundo digital es altamente educativo, también diseñé la caja del medidor de aplausos en el popular programa 3D-CAD Fusion360 antes de comprar cualquiera de los materiales necesarios.
En el transcurso de varias iteraciones, finalmente me decidí por este diseño (ver imágenes). Es una caja rectangular simple con las luces que sobresalen de los orificios circulares en el panel frontal.
Se evitaron tornillos feos en el panel frontal agregando algunas barras de soporte en el interior del panel frontal, donde más tarde se atornillarían los broches magnéticos de la puerta. En retrospectiva, el sistema de cierre magnético es más una característica de seguridad que una realmente necesaria, ya que las barras sujetaban la placa frontal solo por fricción, muy bien.
También agregué la electrónica a mi diseño digital. Esto cambió algunas cosas, por lo que ya estaba dando sus frutos que lo diseñé por primera vez en Fusion360. Por ejemplo, la caja tenía que ser un poco más ancha que los 15 cm iniciales para que los relés encajaran de lado. También terminé modelando e imprimiendo en 3D soportes de plástico para los enchufes de luz que a su vez mantendrían las luces en su lugar. Me pareció que esta era la opción que me daría suficiente "margen de maniobra" para cometer errores en el futuro. (Sé que estos soportes también se pueden comprar como tales, pero esto me costó tres veces más y tenía un presupuesto limitado)
He agregado el archivo F360 de mi diseño final aquí para que lo utilices como referencia y juegues con él.
Paso 3: construcción de la caja
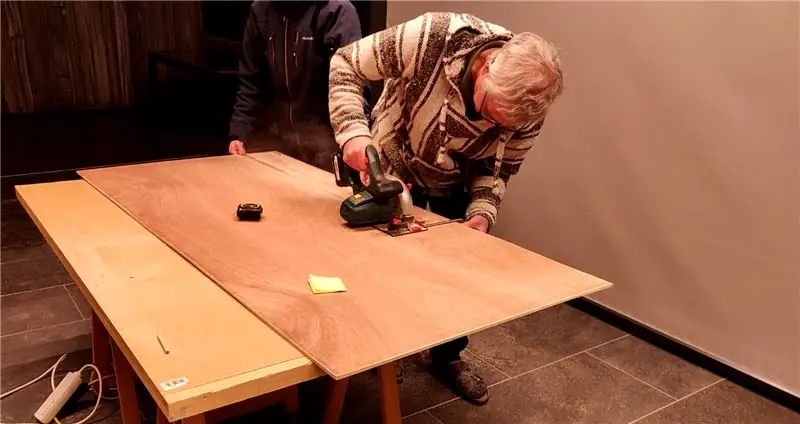
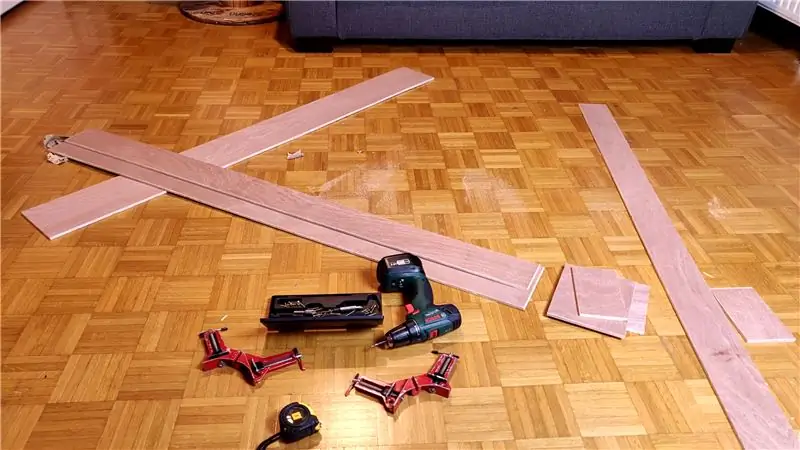
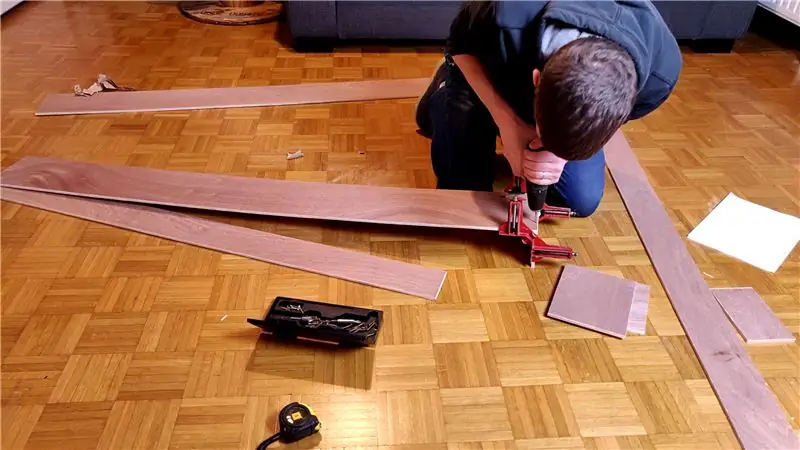
Con el diseño digital finalizado llegó el momento de ir a la ferretería, comprar una gran hoja de madera contrachapada y empezar a cortar. Como no tenía realmente herramientas tan "elegantes", fui a la casa de mis padres un fin de semana y corté la madera a medida allí.
Sin embargo, mi diseño terminó produciendo una hoja de corte bastante exótica:
- 2 veces 16.6x150cm para la parte delantera y trasera
- 2 veces 16.6x10.2cm para la parte superior e inferior
- 2 veces 10,2x148,4 cm para los lados
Las barras de soporte en el interior del panel frontal eran sobras y se usaron como tales, de lo contrario, la longitud preferida habría sido 134 cm y 12 cm.
Una vez en casa, coloqué todas las partes en el piso y con la ayuda de algunas abrazaderas de esquina (prestadas), comencé a perforar previamente los orificios y atornillar las tablas. Recuerde que los tornillos solo se colocan en la parte superior, inferior y posterior del medidor para reacciones puramente estéticas.
La perforación piloto de los agujeros y atornillar todas las tablas fue una tarea precaria debido a que la madera contrachapada tenía solo 8 mm de grosor, a menudo me maldije por pensar que 8 mm sería lo suficientemente grueso.
El panel frontal necesitaba algunos orificios cuidadosamente espaciados de alrededor de 5 cm de diámetro. Marqué la línea central del tablero frontal y comencé desde un lado. El centro del primer orificio estaba a 8 mm (el grosor del material) + 75 mm (la mitad de 150 mm) desde el borde del tablero. Todos los demás orificios están separados por 150 mm. Al final solo tenía 2 mm de diferencia cuando marqué el décimo hoyo… ¡fue un buen día!
La única broca circular que pude tomar prestada era de 51 mm, lo suficientemente cerca como para comenzar felizmente a perforar.
Las guías de la placa frontal se pegaron en su lugar en el interior de la placa frontal con pegamento para madera simple.
Paso 4: instalación de los enchufes en la caja
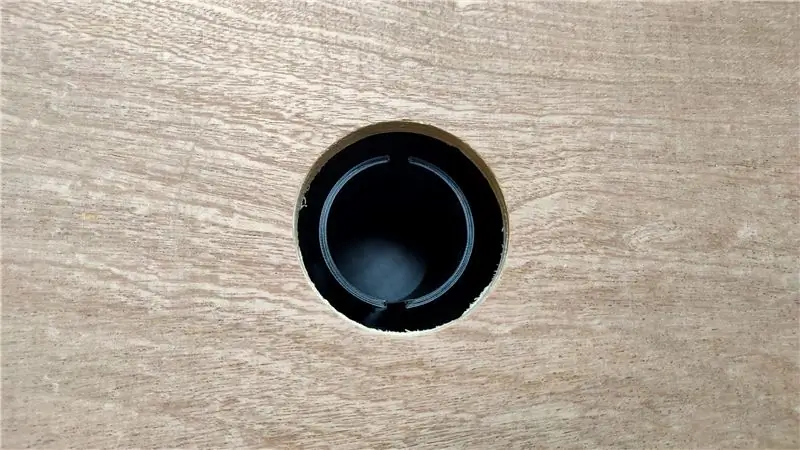
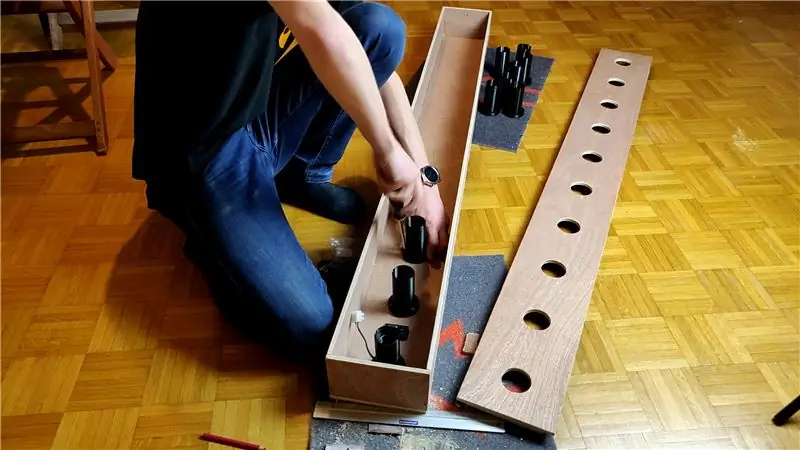
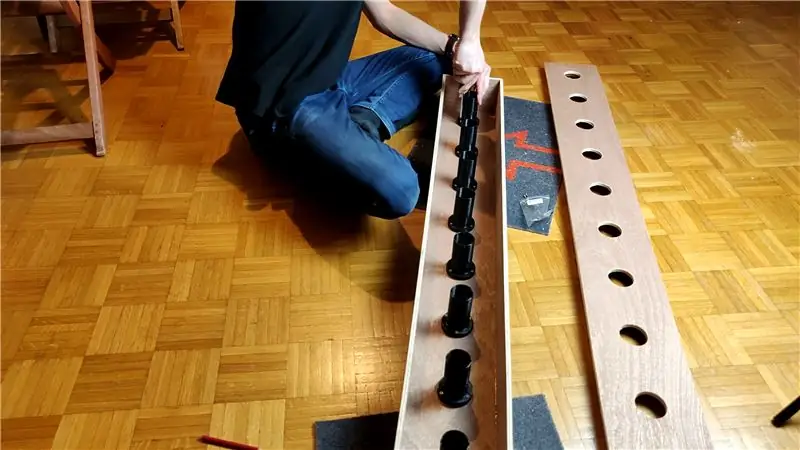
Los primeros componentes que se montan en nuestra caja recién construida son los soportes para enchufes de luz. La razón de esto es que los soportes deben colocarse centrados debajo de cada orificio de la placa frontal. Porque el soporte sostiene los casquillos de luz en su posición, que a su vez tendrán las bombillas atornilladas, y las bombillas son literalmente lo único que sobresale del panel frontal y, por lo tanto, son lo único que no se puede mover. otra posición dentro de nuestra caja. Dado que su posición es fija, deberían entrar primero, para asegurarse de que no cometa un error estúpido más adelante.
Como mencioné antes, existen enchufes de luz disponibles comercialmente con un soporte integrado para montarlos perpendiculares a una pared, pero estos cuestan 4 veces más que los simples que están hechos para colgarlos del techo sin siquiera hacer un débil intento de Parece bonito. Entonces, opté por un soporte barato e impreso en 3D para los enchufes. (Archivo STL a continuación). Al hacer el diseño en 3D, me aseguré de que hubiera suficiente espacio de 'maniobra' para colocar los enchufes en una variedad de profundidades.
Imprimí solo un soporte para verificar el diseño. Después de eso, imprimí 9 soportes a la vez, llenando completamente toda mi placa de construcción y terminando durando más de 50 horas.
Marqué arbitrariamente la parte superior e inferior de la placa frontal y la caja (recuerde que obtuve una enorme desviación de 2 mm entre el diseño digital y la realidad). Luego comencé el tedioso proceso de centrar un soporte con la tapa en su lugar, levantar con cuidado el frente, marcar su posición con un lápiz y pasar al siguiente soporte. Cuando todo estuvo dicho y hecho, volví a revisar todas las posiciones antes de atornillarlas finalmente en la placa trasera.
Una nota sobre los tornillos: el diseño de mi soporte tiene una base bastante gruesa, esto se hace a propósito para asegurarme de que mis tornillos de 16 mm de largo no sobresalgan de la parte posterior de mi placa posterior de 8 mm. Otra razón más para optar por una madera contrachapada más gruesa. (Olvídese de "vivir, amar, reír", es "vivir, amar y aprender").
De todos modos, los enchufes de luz fueron los siguientes. Elegí la altura preferida a la que quería que las bombillas sobresalieran por encima del panel frontal, y luego medí la profundidad a la que deberían estar los enchufes, nuevamente colocando cuidadosamente todo mientras el frente está cerrado y levantándolo y midiendo. Un pequeño detalle: primero tuve que desenroscar y romper un trozo del extremo del cable de todos los enchufes que sirvieron como alivio de tensión para los cables cuando colgaban horriblemente del techo, pero como los estaba montando en soportes impresos personalizados, no me sirvieron para nada. Peor aún, el alivio de tensión hizo que los cables resistieran la curva cerrada en la que los estaba forzando, haciendo así su trabajo a la perfección, … por lo que se tuvo que eliminar el alivio de tensión para que los enchufes encajaran en los soportes de la manera que quería.
Pegué todos los enchufes en los soportes y lo dejé reposar durante la noche con bandas de goma que mantenían la presión. Por supuesto, me olvidé fabulosamente de que compré 9 bombillas normales y una gruesa para la décima luz, esta luz más grande es más esférica en lugar de tener forma de pera, lo que requiere un enchufe que se coloca más cerca del frente de la caja que todas las demás luces..(Vive y aprende)
Por lo tanto, me vi obligado a romper el pegamento (solo rompiendo ligeramente mi impresión en 3D) para liberar el zócalo y reposicionarlo. Después de grandes cantidades de más pegamento tanto para fijar el soporte como para unirlo al enchufe a la altura correcta, se realizó el montaje de los enchufes.
También atornillé los conectores de las tomas de luz a uno de los lados de la placa trasera.
Paso 5: Soldar la electrónica de bajo voltaje
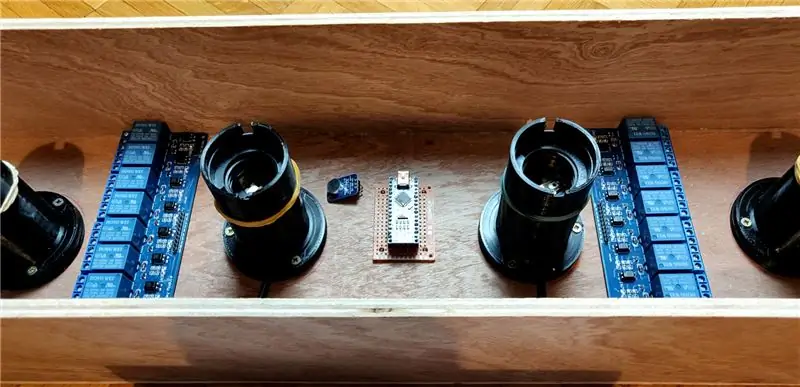
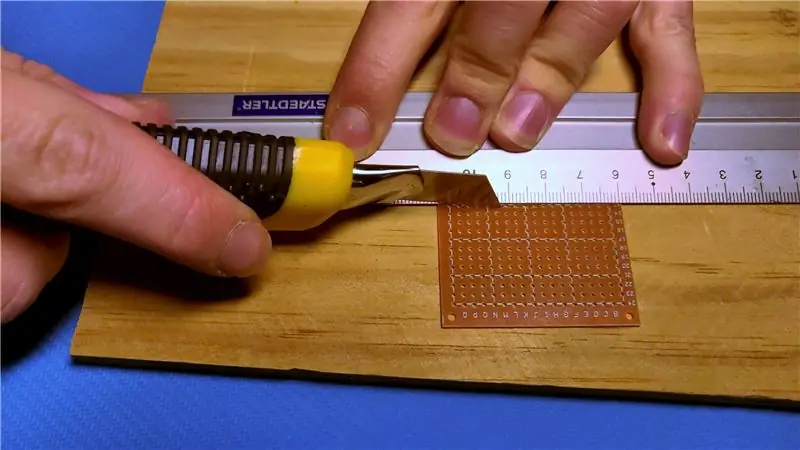
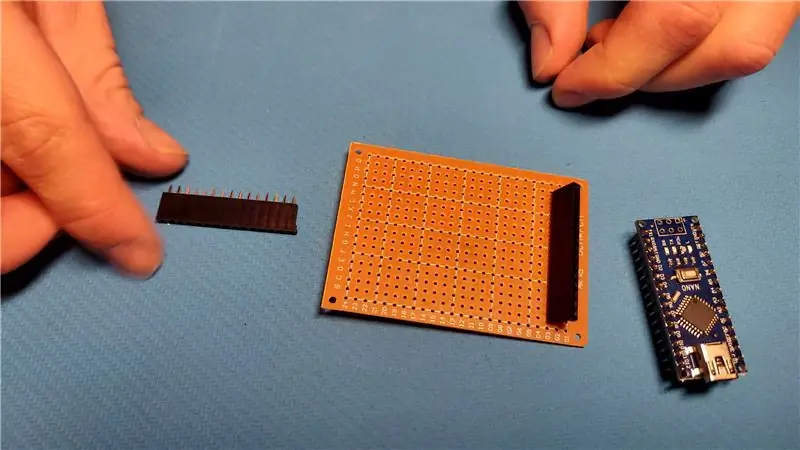
El siguiente orden del día es "ajustar en seco" todos los componentes electrónicos de bajo voltaje en la caja para tener una idea de cuánto tiempo deben ser las conexiones soldadas entre las partes.
Comencé colocando el Arduino en el medio entre las luces 5 y 6 y colocando los relés en los lugares adyacentes arriba y abajo.
Me di cuenta de que no cabían tornillos para madera a través de los orificios del Arduino nano. Esto se resuelve rápidamente soldando algunos encabezados femeninos en una placa de pan soldable. Los encabezados sostendrán el Arduino y algunos orificios perforados en la placa de circuito aceptarán los tornillos para madera sin quejas. Esta placa soldable también albergará las cabeceras para el micrófono a conectar, los conectores (con cables) para ir a los relés y el cable largo para la caja de control remoto.
Sobre la caja remota; Necesitaba dos interruptores al final de un cable muy largo. Estoy al final del escenario como percusionista, mientras que el compás estaría al frente del escenario. Compré 20 m de 4 hilos trenzados que se utilizan normalmente para soldar tiras de LED. Para albergar los dos interruptores, diseñé e imprimí en 3D una caja simple (archivos STL y F360 a continuación), pero cualquier caja rectangular con algunos recortes para los componentes y cables hará el trabajo.
Después de medir la distancia entre los componentes y tomar un exceso generoso en esa distancia, calenté el soldador y comencé a soldar.
Soldar todas las conexiones requiere algo de paciencia y, sobre todo, algo de concentración para hacerlo bien. He incluido el esquema de cableado que usé para hacer todas las conexiones, pero tenga en cuenta que su cableado puede ser un poco diferente si usa componentes diferentes. (O si cometí un error en mi diagrama)
Al final, mi cableado parecía como si un pájaro estuviera tratando de anidar allí. Sin embargo, milagrosamente no se cometieron errores y nada comenzó a fumar al encender la corriente.
Con todo conectado, podría atornillar cada placa de circuito al panel posterior en separadores impresos en 3D. Estos separadores cumplían dos funciones: (1) siempre es una buena idea dejar algo de espacio entre las placas de circuito y la placa en la que las monta. Y (2) ¿ya me he quejado de que tengo tornillos de 16 mm y madera contrachapada de 8 mm y que, por lo tanto, corro un peligro constante de atornillar los tornillos directamente a través de la madera? Sí, los separadores también se aseguraron de que mis tornillos no llegaran al otro extremo de la caja de madera contrachapada.
[NOTA] En retrospectiva, recomendaría usar 5 relés por módulo de relé. Mi idea de usar dos módulos de relé de 8 canales era permitir un relé roto, en ese caso simplemente tendría que cambiar las conexiones y el medidor de aplausos volvería a funcionar. Esto también dividiría un poco mejor las conexiones de 220 V entre los dos módulos, lo que haría que la gestión de cables fuera un poco más … manejable. (Vive y aprende)
Paso 6: Conexión de los componentes de 220 V
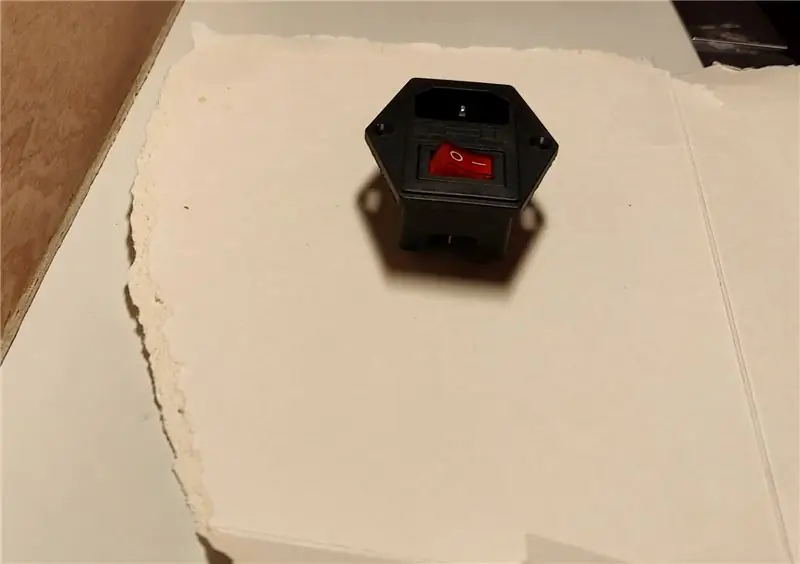
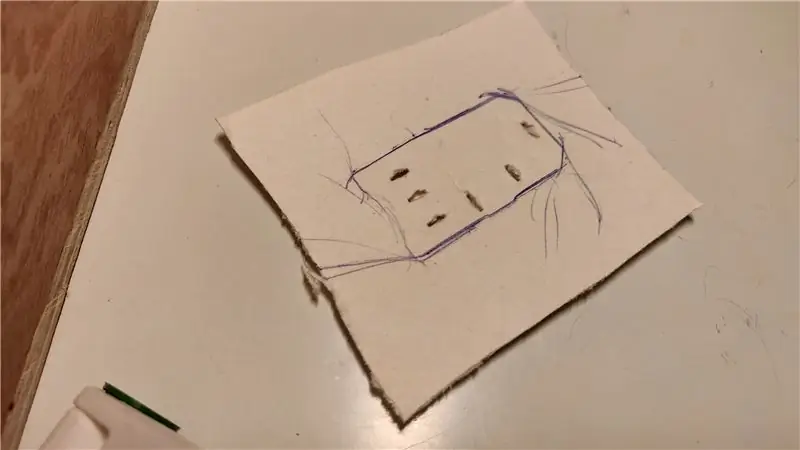
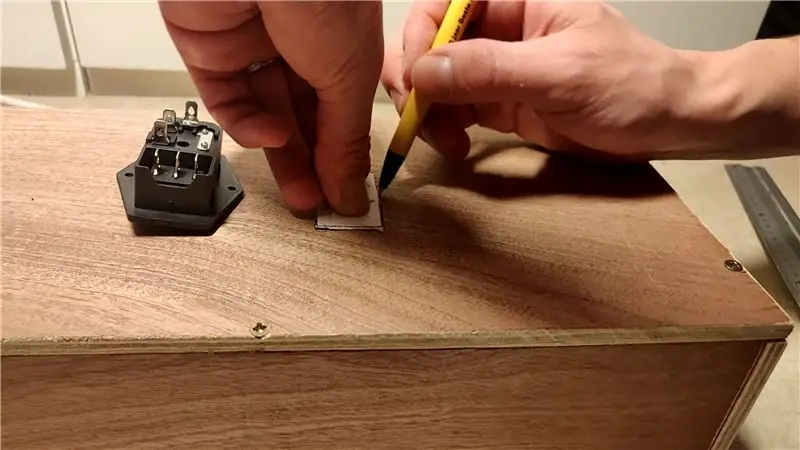
Con todos los componentes de bajo voltaje en su lugar, es hora de realizar un trabajo serio e instalar el circuito de voltaje principal.
No hace falta decir que mientras trabaja con los cables, ¡¡¡¡¡NO los conecte a la red bajo ninguna circunstancia !!!!!
Junto con el técnico que instalaría y controlaría las luces del espectáculo para nuestro próximo concierto, decidimos usar una toma de corriente con fusibles como entrada de energía para el medidor de aplausos. Esto aseguró que cualquier cable de cualquier longitud pudiera adaptarse y suministrar energía a nuestro medidor.
Además, esto agregaría una capa de seguridad a nuestra configuración: estos conectores están equipados con un fusible que se quema por encima de un cierto amperaje, asegurándose de que nada se encienda si no se supone que debe hacerlo.
Para instalar este enchufe necesitábamos sus medidas exactas. Sin embargo, tiene una forma bastante compleja. Entonces, lo más simple que se me ocurrió es presionar el enchufe de alimentación en un pedazo de cartón y trazar los contornos del enchufe. Las líneas de contorno se pueden cortar para producir una plantilla que se puede transferir a la madera.
Al marcar y cortar la ubicación del enchufe, tenga en cuenta que ya hay componentes instalados en el interior del medidor que ya no se pueden mover, lo que limita las posibles ubicaciones donde el enchufe puede salir de la caja. Lo mismo ocurre con el orificio de salida del cable de 20 m de largo para el control 'remoto'.
Normalmente, cortaría el agujero con una sierra de vaivén, pero no tengo un dispositivo de este tipo y estaba impaciente, así que simplemente taladré agujeros a lo largo de los contornos y simplemente corté el agujero con una cuchilla afilada. Esto funciona, pero no puedo recomendarlo ya que casi me corto los dedos.
Ahora es solo cuestión de conectar todo. He hecho un esquema de cableado del circuito de 220v para facilitar la referencia. El cable caliente está conectado a todas las luces en paralelo mientras que el cable neutro es interrumpido por los relés antes de conectarse a las luces. Es tan simple como eso. Solo asegúrese de conectar la luz correcta al relé correcto, o tendrá que volver a conectar el extremo de control de 5V o los cables de 220v para corregir su error.
Hay un Instructable sobre cómo conectar sus cables a la toma de corriente con fusible que explica todo mejor que nunca, así que salte allí, pero recuerde volver aquí (https://www.instructables.com/id/Wire- Up-a-Fused-AC-Male-Power-Socket /)
[NOTA] Para conectar los cables neutrales a los relés ubicados en el centro, conecté un cable al enchufe con fusible y lo dividí en diez antes de conectarlo a los relés. Estaba planeando pasar a través de los cables neutrales en los relés, conectando cada entrada de relé en paralelo entre sí. Sin embargo, los terminales del relé no aceptaron más de un cable, lo que me obligó a encontrar otra solución. Para realizar esta división, se recomienda utilizar algún tipo de conector. No tenía eso, (y estaba impaciente) y simplemente até todos los cables en un gran nudo antes de aislarlo. No recomiendo este 'nudo' por razones de seguridad eléctrica. ESPECIALMENTE debido a su proximidad a la placa Arduino. Sin embargo, parece funcionar bien.
Paso 7: pargos magnéticos (opcional)
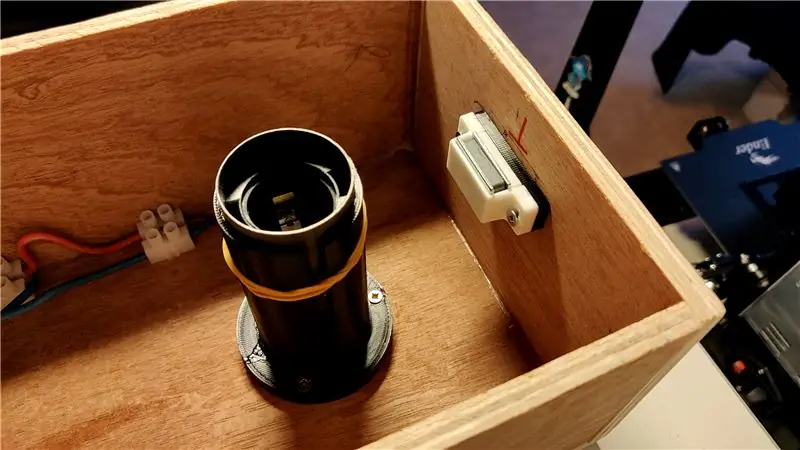
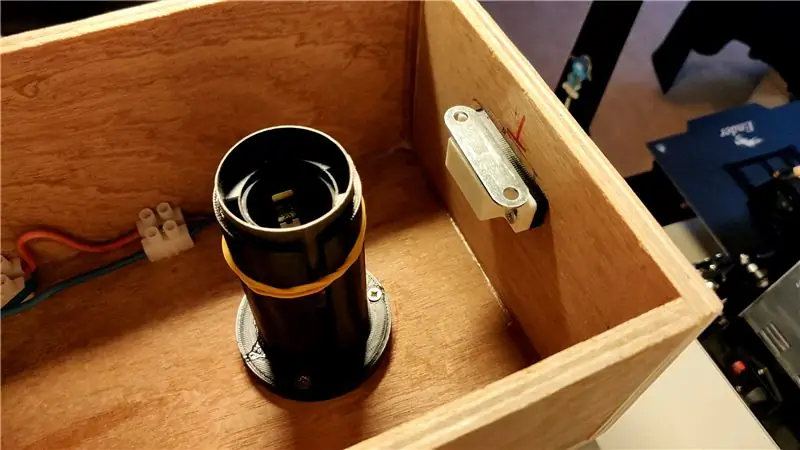
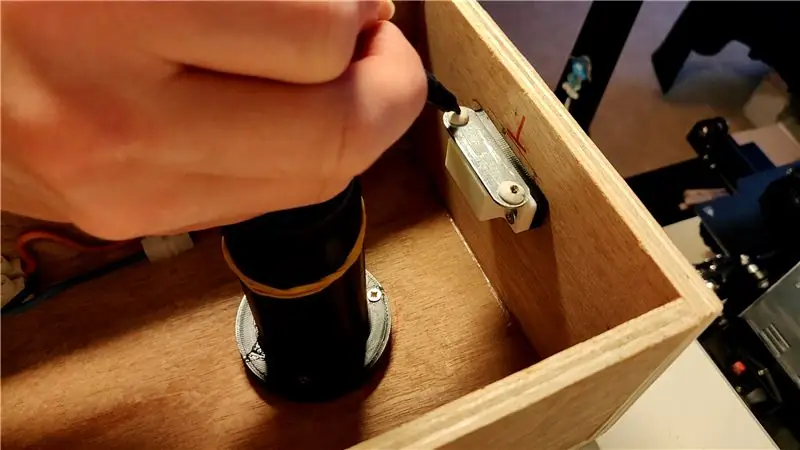
Este paso es completamente opcional, ya que las guías del panel frontal sujetan suficientemente la placa frontal solo por fricción. Decidí incluir los pargos solo como una característica de seguridad, para que el panel frontal no se soltara sin que yo quisiera que se soltara
Me quedé despierto muchas noches pensando en cuál sería el mejor método para sostener el panel frontal de la caja en su lugar. Al final, se me ocurrió usar cierrapuertas magnéticos. Dudo que sea el término oficial para estos ingeniosos dispositivos, pero los reconocerá de inmediato. Los pargos magnéticos se utilizan con mayor frecuencia para mantener cerradas las puertas de los armarios sin usar un candado.
Adjunté la parte magnética a la carcasa exterior del medidor de aplausos (panel superior, inferior, izquierdo o derecho). Esto se hizo mediante espaciadores y tornillos personalizados impresos en 3D (yadda yadda yadda, tornillos largos, madera delgada, ya conoces la historia ☺)
Las placas de metal se atornillaron a la madera de las guías. Esta fue también la primera vez que la madera fue lo suficientemente gruesa como para no usar ningún espacio (yay). Sin embargo, tuve algunos problemas para determinar la posición de las placas de metal. He encontrado una solución:
- Coloque la parte magnética en la caja.
- coloque la placa de metal en el imán en su posición perfecta
- en los orificios del plato, coloque una bolita de "Pritt-buddy" (una especie de goma de mascar como pegamento para pegar carteles a las paredes sin alfileres; probablemente también funcionaría la goma de mascar normal)
- con un marcador de alcohol haga un punto en la bola Pritt-buddy en el lugar donde están los agujeros
- cerrar la tapa, transfiriendo así parte de la tinta del marcador a la madera
- ¡Levanta la tapa y tadaa! Ha hecho una pequeña marca donde deben ir sus tornillos
- Retire los amigos y la placa y atorníllelo en su posición correcta, primero intente
- paso 8: beneficio
Coloqué cuatro pargos magnéticos en la caja: uno en la parte inferior, uno en la parte superior, uno en el medio a la izquierda, uno en el medio a la derecha.
Los pargos que elegí tenían una fuerza de sujeción de 6 kg. Con cuatro de ellos, proporcionaron suficiente fuerza para levantar casi toda la caja solo por el panel frontal.
Paso 8: Qué haría de otra manera
Mientras hacía este medidor de aplausos, a menudo maldije a mi pasado por tomar decisiones tontas, enumeraré aquí las lecciones más importantes que aprendí:
-
USE MADERA CONTRACHAPADA MÁS GRUESA. En serio, es posible hacer una caja de madera contrachapada de 8 mm, pero plantea muchos desafíos y obliga a hacer algunos compromisos.
- Primero, la perforación piloto de todos los orificios para los tornillos es un desafío porque no hay tolerancia para las brocas con un ángulo incorrecto.
- En segundo lugar, los tornillos que tenía eran de 16 mm (¿he mencionado esto antes?). Esto me obligó a hacer algunas distancias al atornillar la madera para evitar que los tornillos salieran por el otro lado, pero al mismo tiempo esto significó que los tornillos no penetraban lo suficientemente profundo como para obtener suficiente tracción para sujetar algunos componentes.
- ….
- solo usa madera más gruesa
Recomendado:
Circuito de aplausos de bricolaje: 5 pasos
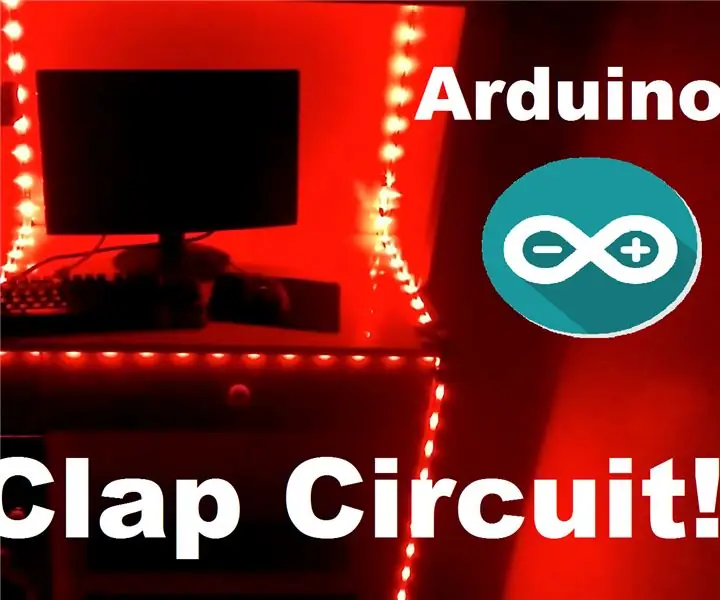
Circuito de aplausos de bricolaje: ¡Hola chicos! Bienvenido de nuevo a otros instructivos de Let's Innovate. En esta ocasión te mostraré cómo hacer un circuito simple que te permita encender o apagar tus electrodomésticos con tan solo 3 palmadas bien sincronizadas. Tengo un video sobre el tema, que brinda todo lo
Bricolaje -- Luz ambiente controlada por aplausos: 3 pasos
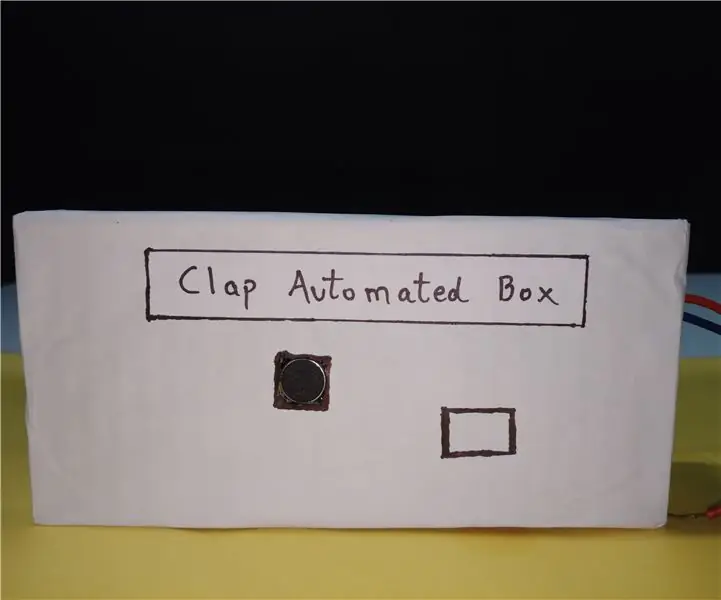
Bricolaje || Luz de habitación controlada por clap: ¿Alguna vez se ha preguntado cómo controlar sus electrodomésticos con un CLAP? ¡Entonces está en el lugar correcto! Aquí, le mostraré cómo puede controlar cualquier electrodoméstico, ya sea: luces de habitación, ventilador, televisión o sistema de audio con solo un aplauso. Este proyecto se basa en
Cómo hacer un circuito de interruptor de aplausos: 12 pasos (con imágenes)
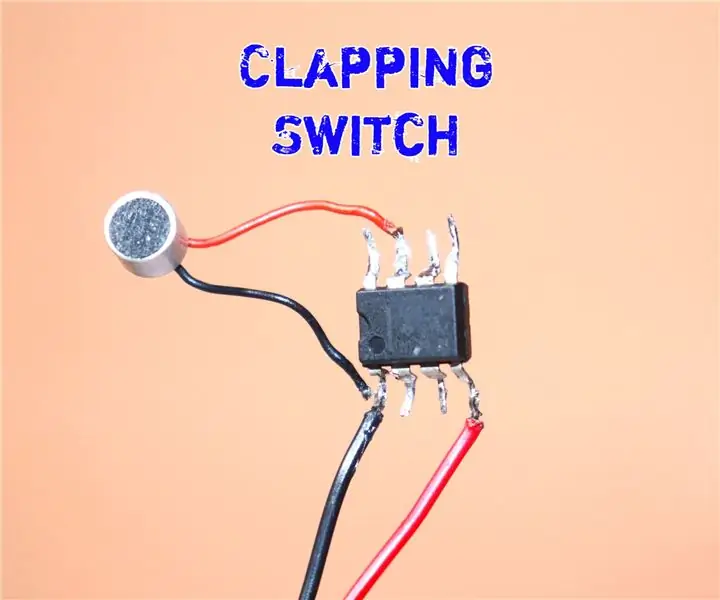
Cómo hacer un circuito de interruptor de aplausos: Hola amigo, hoy voy a hacer un circuito de interruptor de aplausos. Cuando aplaudamos, el LED se iluminará. Este circuito es increíble. Para hacer este circuito, usaré el transistor LM555 IC y C945. Empezar
Matriz de LED activados por aplausos: 4 pasos
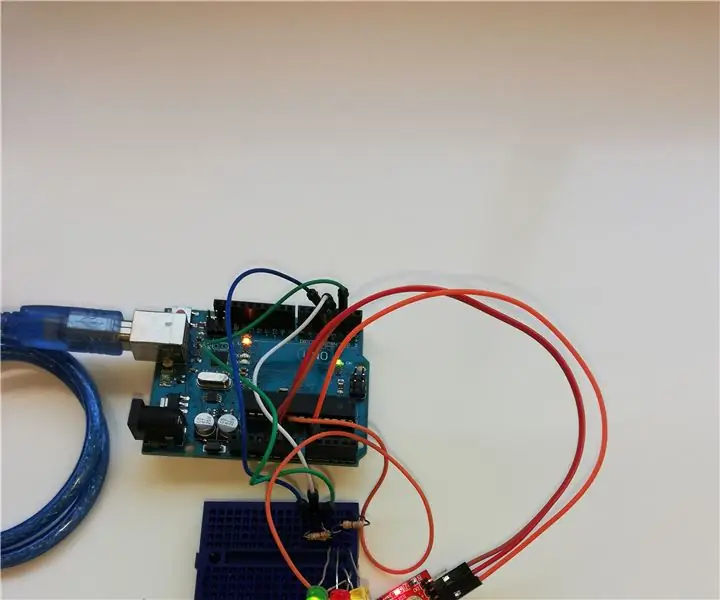
Matriz de LED activados por aplausos: al final de este instructivo, podrá construir un dispositivo que escuche ruidos fuertes como aplausos y responda a ellos encendiendo o apagando 3 LED. Arriba hay una imagen del resultado final
Interruptor de aplausos (40 aplausos en 5 segundos): 4 pasos (con imágenes)
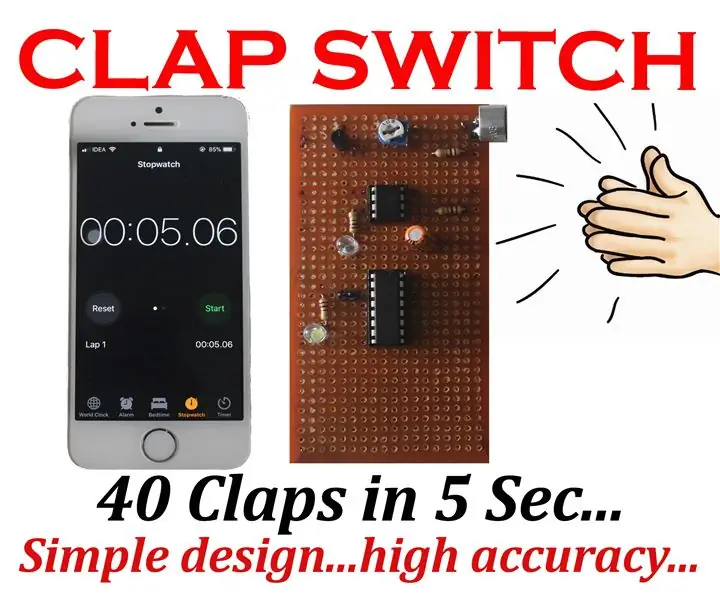
Clap Switch (40 Claps en 5 segundos): Clap Switch tiene la capacidad de encender / apagar cualquier componente eléctrico conectando la salida del circuito a un interruptor de relé. Aquí vamos a hacer un cambio de aplauso con pocos componentes con muy buenas explicaciones. Comparado con todos los demás interruptores de aplauso