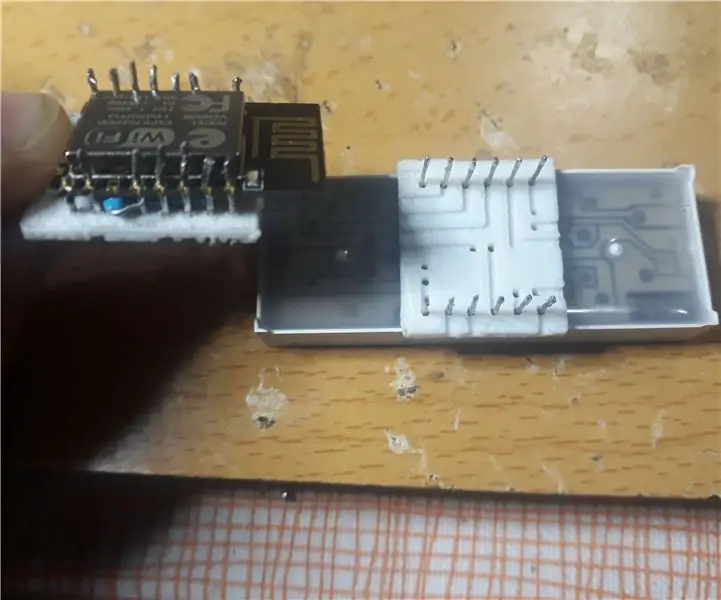
Tabla de contenido:
2025 Autor: John Day | [email protected]. Última modificación: 2025-01-23 14:39
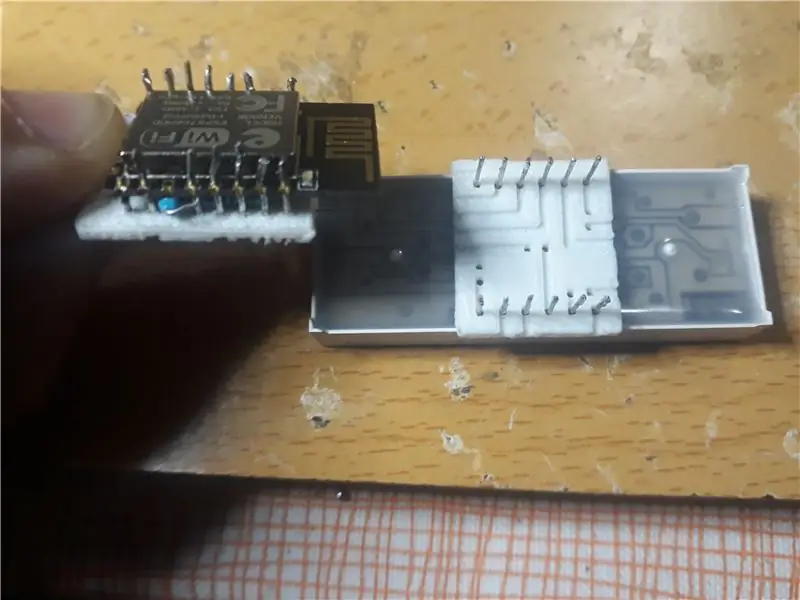
Cuando pude conectar una pantalla de 4 dígitos y 7 segmentos a mi Teensy, decidí que tenía que comenzar a investigar sobre la fabricación de PCB en casa de una manera sencilla. El grabado tradicional es bastante tedioso y peligroso, así que lo descarté rápidamente. Una buena idea que he visto son los tableros impresos en 3D que funcionan agregando pintura conductora a sus canales, pero esto parece bastante errático para la conductividad. También hay filamentos conductores especiales que podría usar en una impresora de doble extrusión, pero estoy buscando algo básico y efectivo para el equipo estándar que tengo.
Así que he pensado en soldar y colocar directamente componentes y conectores en impresiones 3D.
Antes de empezar, ten cuidado: estaremos imprimiendo con ABS ya que puede soportar + 200ºC antes de deformarse (por lo que podemos aplicarle con cuidado un poco de soldadura). Imprimir con ABS no es tan simple como lo es con PLA, necesita una impresora cerrada y muchas calibraciones de configuraciones, pero una vez que lo hace bien, el resultado marca la diferencia.
Para agregar algo de contexto, en los ejemplos estoy creando una PCB para la placa wifi ESP8266 12E para poder conectarla fácilmente a cualquier otra cosa más adelante (el objetivo final es una pantalla 4d7seg).
La PCB me permitirá usar todos sus pines disponibles, mientras que la mayoría de los módulos tienen muy pocos pines de repuesto o tienen demasiadas características adicionales que realmente no quiero (como el NodeMCU).
Suministros
- Software de diseño de PCB (aquí KiCad, gratis). Nivel de iniciación.
- Software de modelado 3D (Blender aquí, gratis). Nivel de usuario.
- Una impresora 3D (aquí Creality 3D Ender 3 Pro, unos 200 €). Nivel de usuario.
- Se recomienda encarecidamente un recinto para su impresora cuando utilice ABS: asegúrese de que puede imprimir ABS correctamente antes de continuar con este instructivo.
- Filamento ABS (Smartfil ABS, unos 20 € / Kg). 3-15 gramos por PCB.
- Agujas de coser (solo consigue algunas de mamá). El tamaño dependerá del diámetro de los pines de sus componentes. Por lo general, 0,5 mm o 1 mm de diámetro.
- Soldador de estaño y soldador (unos 15 € en una tienda local). Además de todos los accesorios adecuados para soldar: soporte para soldador, lámpara, tabla, pinzas, gafas protectoras, máscara… los accesorios dependen del usuario, ¡solo asegúrate de sentirte cómodo y seguro mientras elaboras!
- Mucha paciencia, mente creativa fuera de la caja y una buena base (intente buscar en Google y estudiar mucho antes de tenerlo en sus manos).
Paso 1: prototipo y esquema
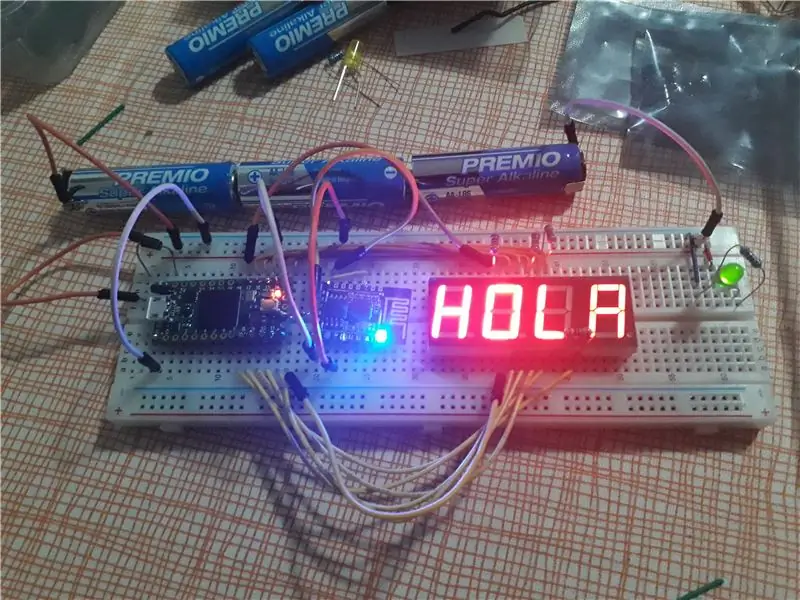
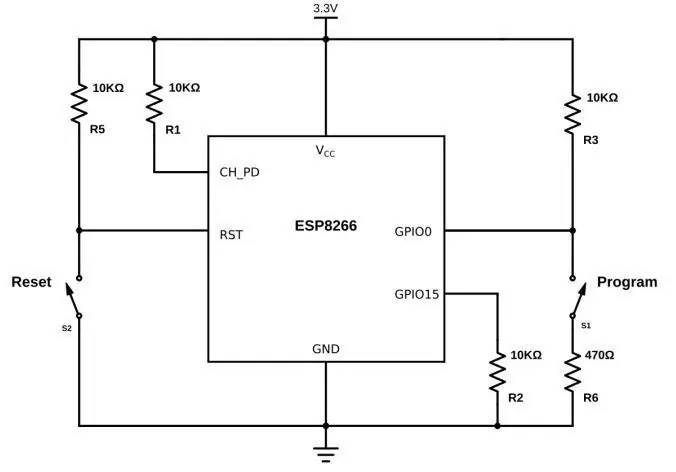
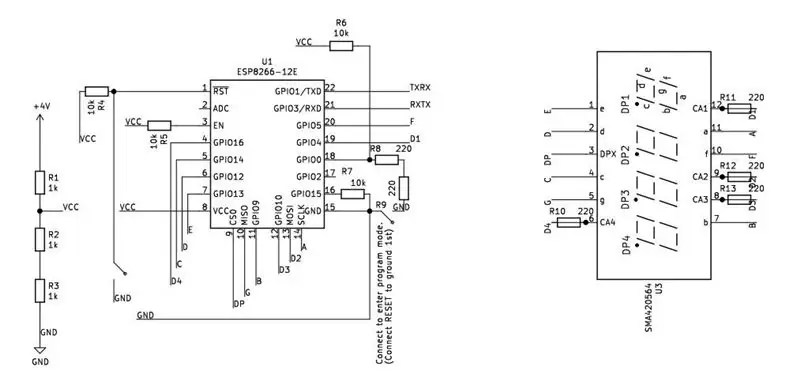
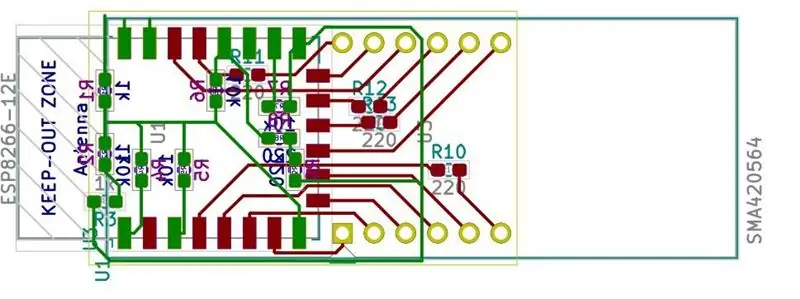
A menos que esté siguiendo el esquema de otra persona, debe construir su circuito eléctrico siguiendo las especificaciones del fabricante. Pruebe un circuito prototipo y, una vez que lo tenga funcionando, dibuje todas las conexiones y componentes.
Una vez que tenga un boceto y se sienta cómodo con una comprensión clara de su circuito, consígalo detallado en su software EDA preferido. Esto ayudará a optimizar y verificar su diseño.
Dibuje su esquema y utilícelo como guía para el diseño de su PCB. El software EDA como Eagle o KiCad le permitirá agregar sus componentes específicos, con pines y dimensiones realistas, para que pueda diseñar su circuito eléctrico con precisión alrededor de ellos.
Estoy usando KiCad, que es gratis y bastante fácil de entender para empezar. Todo lo que sé es gracias a Brian Benchoff @ https://hackaday.com/2016/11/17/creating-a-pcb-in… y algunas publicaciones relacionadas, así que siga sus pautas para terminar con un bonito diseño de PCB.
Las imágenes de esta sección se refieren a:
- Prototipo de prueba para el ESP8266 y una pantalla de 7 segmentos de 4 dígitos (adjunta a un Teensy 4).
- Un diagrama de cableado de referencia para una placa wifi ESP8266 12E.
- Un esquema de KiCad para una pantalla de 7 segmentos de 4 dígitos que funciona a través del ESP8266 y un divisor de voltaje (este es mi objetivo final).
- Una salida de diseño de PCB KiCad.
Paso 2: modelo 3D
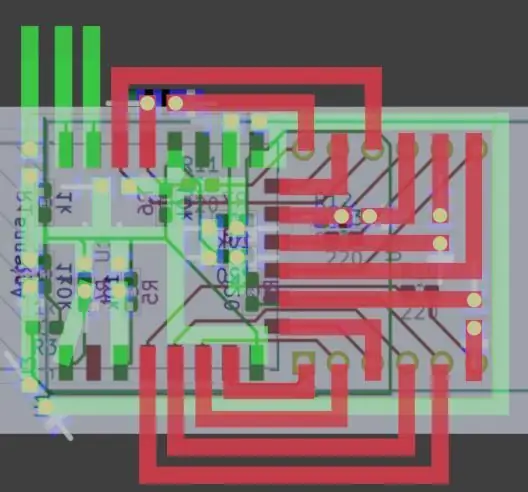

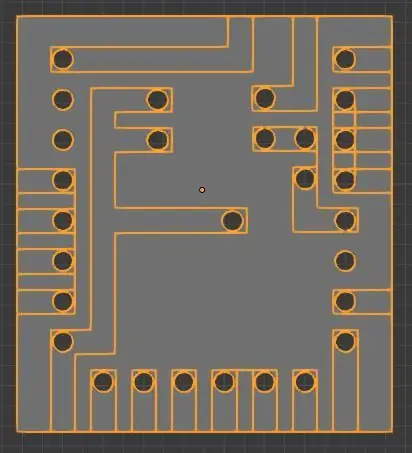
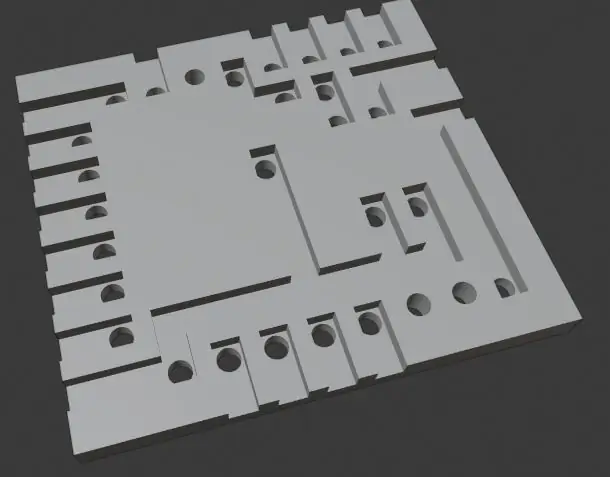
Una vez que tenga un diseño de PCB en papel, debe darle más realismo en un software de modelado 3D. Esto también preparará su archivo para su impresora 3D. Así es como lo hago en Blender:
- Cree una malla plana y agregue su imagen de diseño de PCB sobre ella. Asegúrese de que esté a escala y de que las dimensiones sean realistas, ya que esto servirá como "papel de calco".
-
Cree componentes simplificados prestando especial atención a la ubicación exacta y el tamaño de los PINS que se conectan a su PCB. Obtenga las especificaciones del fabricante en línea o mídalas usted mismo para obtener la precisión necesaria. Tenga en cuenta algunas atenuaciones estándar que puede usar como referencia:
- Para tablas use aviones. Para una placa de circuito impreso de un solo lado, utilizo un grosor de 1,5 mm, ya que es más delgado que este y no obtuve buenos detalles al imprimir (también se debe a la configuración y las capacidades de su impresora, pero llegaremos a eso más adelante). Para una PCB de doble cara utilicé un grosor de 2,5 mm.
-
Para las clavijas, utilice cilindros de un diámetro mínimo de 1 mm para que la impresora lo capture.
- Para los canales, utilice cubos de un mínimo de 1,2 mm de ancho. Simplemente extruirá caras para obtener sus canales.
- Ubique sus componentes de acuerdo con el diseño de su PCB. Si sus componentes son lo suficientemente realistas, puede usar esto para verificar si hay choques, pero siempre deje espacio adicional alrededor de cada elemento.
- Rastrea tu circuito eléctrico. Coloque una malla de cubo en la ubicación del primer alfiler. Luego, en el modo de edición, extruya las caras en línea recta siguiendo el diseño. Nuevamente, manténgalo simple, use líneas de 90º y use tantos canales como considere. Además, permita una separación de al menos 0,8 mm entre las paredes o de lo contrario se perderán al imprimir. La imagen 1 a continuación muestra algunas rutas modificadas después del modelado con dimensiones reales, ya que la ruta ideal era demasiado delgada para ser posible.
- Cree su PCB agregando un cubo plano (se atenúa como se muestra arriba).
- Grabe sus canales y agujeros en la placa agregando modificadores booleanos a su objeto PCB. Esto recortará la parte del tablero que se cruza con el objeto de destino del modificador booleano.
Las imágenes 3 y 4 muestran el resultado final de la placa ESP8266 (modelo 3D en la imagen 2).
Después de esto, debería ver una impresión 3D de su PCB.
El último paso es exportar el modelo correctamente.
- Asegúrese de que todas las caras apunten hacia afuera ("Modo de edición - Seleccionar todo" Luego "Malla - Normales - Recalcular afuera").
- Asegúrese de que todas sean caras individuales ("Modo de edición - Seleccionar todo" Luego "Borde - División de borde"). Si omite estos dos pasos, es posible que falten detalles en su software Slicer.
- Exportar como. STL ("Solo selección" para exportar solo el PCB final y "Unidades de escena" para mantener la escala de las cosas).
Paso 3: software de la cortadora
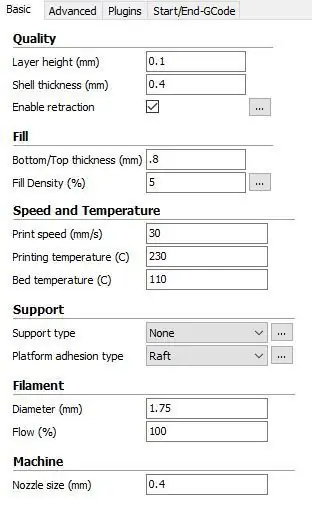
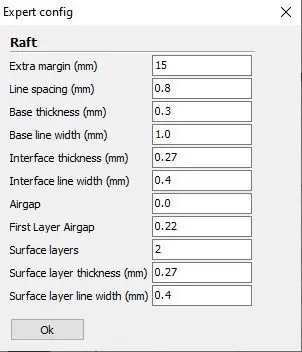
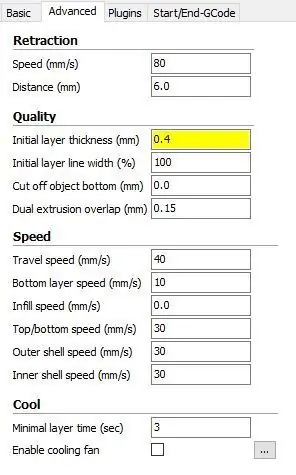
Las impresoras 3D suelen proporcionar un software "Slicer" para procesar los modelos 3D (en.stl u otros formatos) y calcular la ruta necesaria para imprimirlos (normalmente en formato.gcode). Tengo una Creality Ender 3 y no me he movido de la Creality Slicer proporcionada, pero puede aplicar esta configuración a cualquier otro software.
Dedico una sección completa a la configuración de la cortadora, ya que son muy importantes al imprimir ABS, lo cual es bastante complicado debido a la deformación, la contracción y el agrietamiento. La impresión de una PCB también está en el límite de las impresoras 3D estándar debido a la precisión requerida.
A continuación, comparto la configuración que utilizo en Creality Slicer para la impresión detallada de PCB de ABS. Se diferencian de la configuración estándar en:
- Paredes y capas delgadas (para proporcionar suficientes detalles; esto puede requerir un par de iteraciones para obtener el resultado deseado, a menos que esté satisfecho con mi configuración).
- Usa una balsa. La llave está en la base, a la que debes tener especial cuidado. (Permito un desplazamiento de 10 mm del modelo para evitar que cualquier deformación mínima afecte la impresión). Además, no hay separaciones entre las líneas de la balsa para lograr una buena base sólida. Si obtiene su base correctamente, todo estará listo. Si ve alguna esquina doblada en su base, seguramente está condenado.
- Velocidad lenta. Estoy usando aproximadamente 1/4 de la velocidad estándar (esto permite una buena colocación del filamento y, por lo tanto, la adherencia y la calidad general).
- Temperaturas ABS (lecho: 110ºC, boquilla: 230ºC)
- Ventilador desactivado (recomendado para mantener la temperatura constante para ABS).
Paso 4: Imprimir
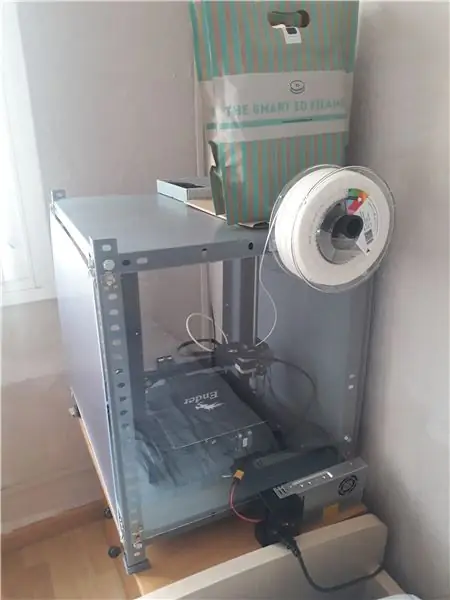
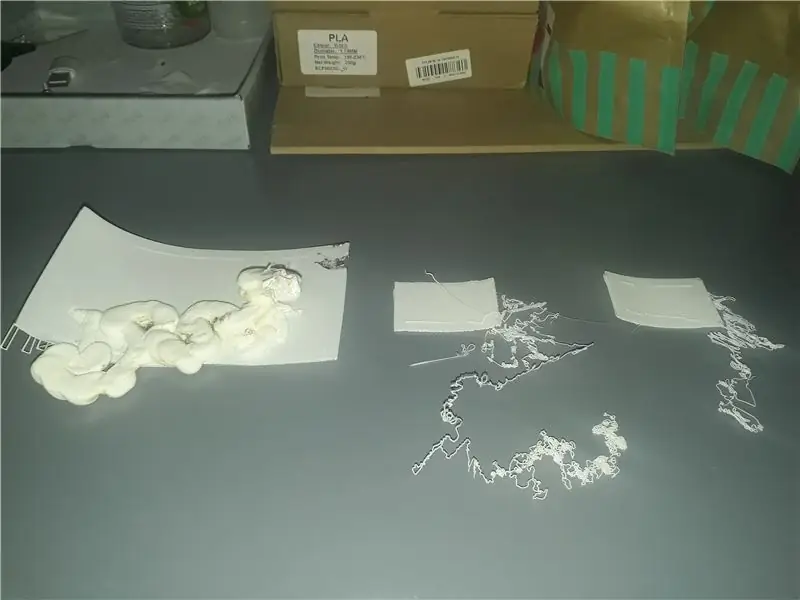
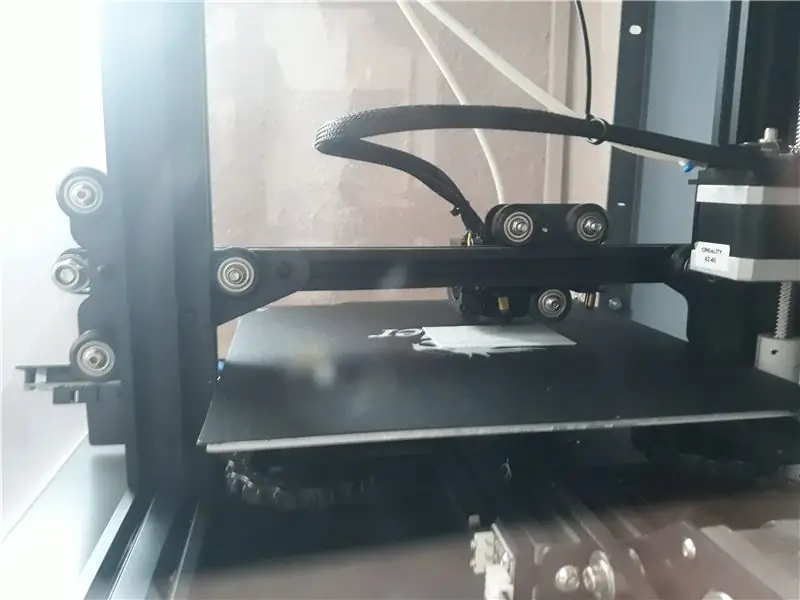
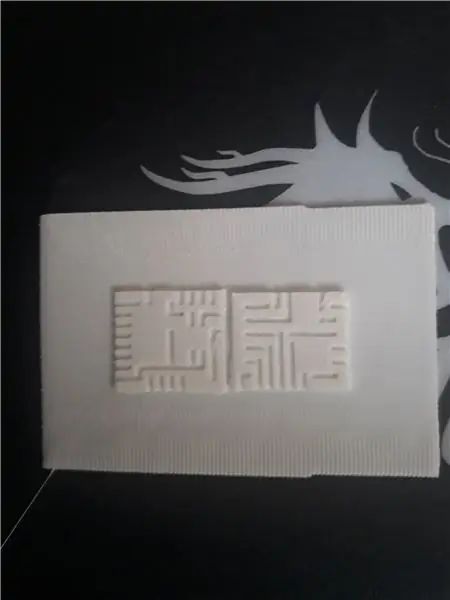
Finalmente, envíe su.gcode a su impresora y haga que su PCB se fabrique. Algunos consejos que debes seguir:
- Cubra su impresora 3D. Un gabinete mantendrá su temperatura mucho más estable, lo cual es un requisito importante para la impresión ABS. Asegúrese de mantener la CPU y la fuente de alimentación fuera del gabinete, así como su filamento. Si logra imprimir ABS sin una carcasa, comparta su truco, ya que me ha vuelto loco.
- Precaliente su impresora por un tiempo. En PLA puede imprimir de inmediato, pero con ABS mi consejo es precalentar con ajustes de ABS (cama: 110ºC, boquilla: 230ºC) durante 10-15 minutos para crear la atmósfera adecuada antes de continuar y comenzar a imprimir.
- Imprima de forma lenta pero segura. Como se mencionó anteriormente, reduje la velocidad de impresión estándar a 1/4 en el archivo de configuración. Esto parece ser lo suficientemente lento como para tener un buen resultado, pero puede administrar la velocidad de impresión mientras imprime regulando la velocidad de alimentación si desea optimizarla un poco más. Solo tenga en cuenta que las altas velocidades darán lugar a movimientos muy repentinos que no colocarán el filamento de manera efectiva o podrían colisionar con la malla y despegarla.
- Construye una buena base. La clave del ABS es lograr una base bien fija. Si la base falla y se despega, el modelo desaparecerá (vea algunos intentos desastrosos a continuación). Con los consejos anteriores (encapsulado, precalentamiento y baja velocidad) deberías conseguir una buena base y un buen acabado. Pero a diferencia del PLA, que dejo desatendido durante horas, el ABS necesita más atención.
- Esté atento, especialmente al principio. Reiterando lo anterior, la clave es la base. Asegúrese de que el primer contorno exterior esté bien trazado. Esto impulsará el resto de la adhesión de la primera capa. A veces, el filamento no se pega de inmediato o se arrastra desde su ubicación. Debe detectar esto lo suficientemente pronto para corregir cualquier nivelación o limpieza de la placa base. Siempre esté atento a la deformación, si ve que las esquinas se elevan, probablemente terminarán despegando toda la base y estropeando toda la impresión. Incluso si la base se mantiene en su lugar, la deformación hará que esta esquina se deforme.
Paso 5: alambre y soldadura
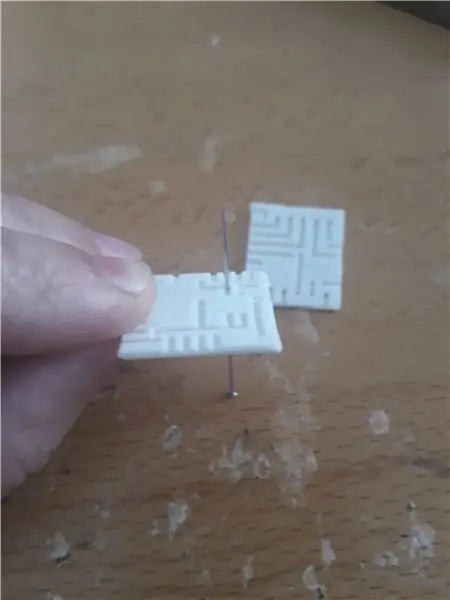
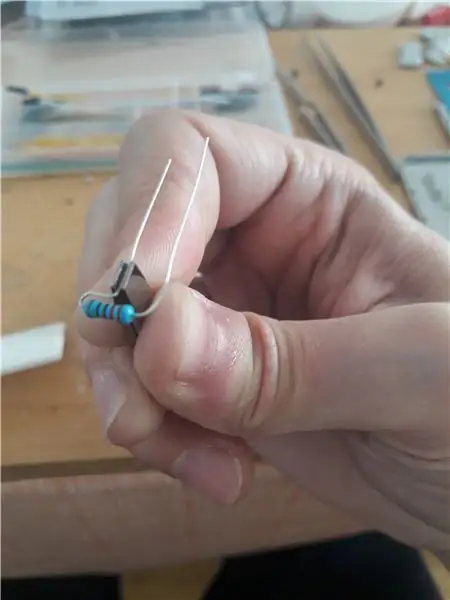
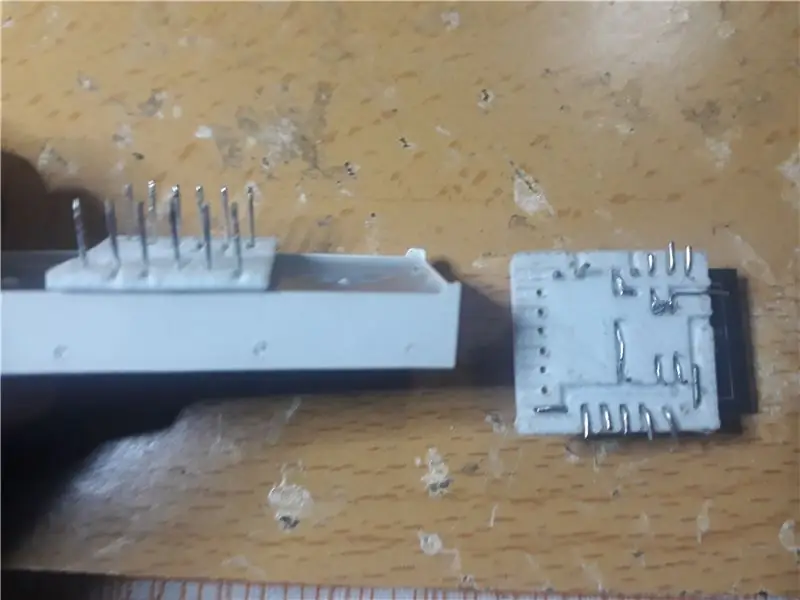
Ahora es el momento de ponerlo todo en su lugar:
- Verifique el acabado de canales y agujeros. Especialmente los agujeros suelen pasar desapercibidos o superpuestos por la impresora. Use una aguja de coser si necesita volver a abrir algunos de estos. Por supuesto, si no obtuvo una impresión plana debido a la deformación, o no obtuvo el detalle que esperaba, verifique la configuración de la impresora, o incluso su modelo 3D para las dimensiones.
- Coloque sus componentes. Los módulos, resistencias, condensadores o leds que tienen sus propios pines se pueden colocar fácilmente. Puede doblar un poco su propio cable para introducirlo en los canales, de modo que sea más fácil atarlos más tarde.
- Agregue alambre y suelde. Use cualquier alfiler o puente que encaje en el canal y córtelos a lo largo para que solo necesite soldar en puntos de unión específicos. No deberíamos necesitar soldar todo, aunque suelo hacerlo cuando las cosas no se iluminan. En mi caso, tuve que cablear todos los pines del ESP8266, y aquí es donde era clave tener buenas habilidades para soldar (que no tengo). El resto del tablero fue bastante simple de hacer.
Paso 6: prueba tu tablero
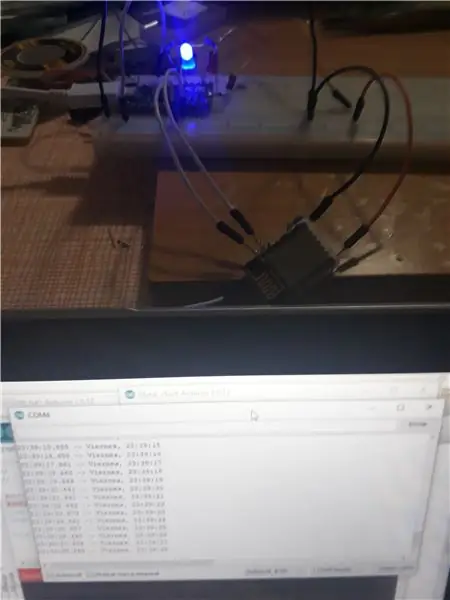
Si está seguro de que ha hecho todo bien, conéctelo.
Para la creación de prototipos, estoy ejecutando el ESP8266 en la conexión en serie Teensy 4.
Mientras hacía las pruebas en el tablero, cargué un programa que cargaba la hora local a través de wifi. Como puede ver, todo estaba funcionando bien. Espero que también hayas obtenido un buen resultado con esta técnica.
Recomendado:
Árbol de Navidad impreso en 3D con LED integrado: 10 pasos (con imágenes)
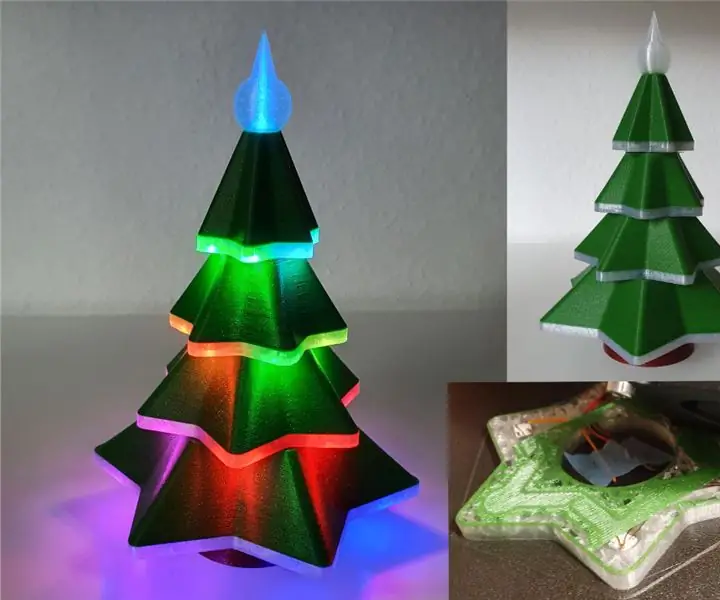
Árbol de Navidad impreso en 3D con LED integrado: este es un árbol de Navidad impreso en 3D con LED direccionables integrados en el interior. Por lo tanto, es posible programar los LED para obtener buenos efectos de luz y utilizar la estructura impresa en 3D como difusor. El árbol se divide en 4 etapas y un elemento base (el árbol
Control deslizante de la cámara de seguimiento de objetos con eje de rotación. Impreso en 3D y construido en el controlador de motor de CC RoboClaw y Arduino: 5 pasos (con imágenes
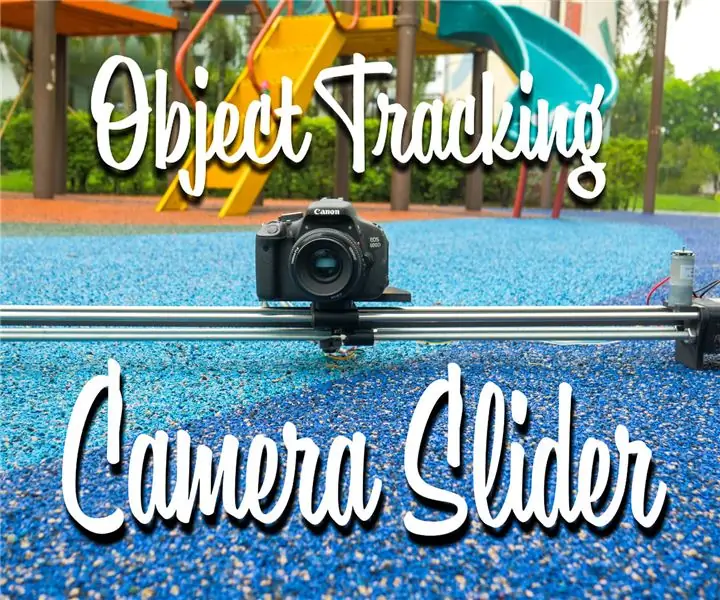
Control deslizante de la cámara de seguimiento de objetos con eje de rotación. Impreso en 3D y construido en el controlador de motor de CC RoboClaw y Arduino: este proyecto ha sido uno de mis proyectos favoritos desde que combiné mi interés por la creación de videos con el bricolaje. Siempre he mirado y he querido emular esas tomas cinematográficas en películas en las que una cámara se mueve a través de una pantalla mientras se desplaza para seguir el
OAREE - Impreso en 3D - Robot para evitar obstáculos para la educación en ingeniería (OAREE) con Arduino: 5 pasos (con imágenes)
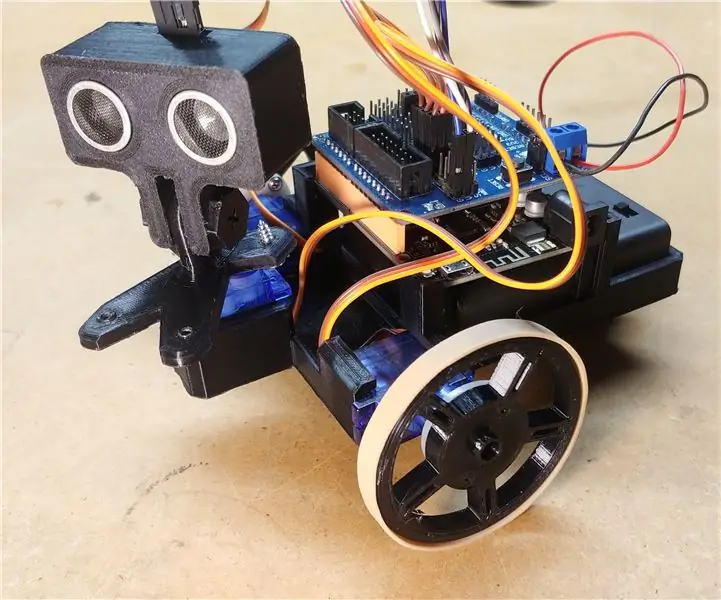
OAREE - Impreso en 3D - Robot para evitar obstáculos para la educación en ingeniería (OAREE) Con Arduino: Diseño OAREE (Robot para evitar obstáculos para la educación en ingeniería): El objetivo de este instructivo era diseñar un robot OAR (Robot para evitar obstáculos) que fuera simple / compacto, Imprimible en 3D, fácil de montar, utiliza servos de rotación continua para movem
DESLIZADOR DE CÁMARA MOTORIZADO Con SISTEMA DE SEGUIMIENTO (Impreso en 3D): 7 pasos (con imágenes)
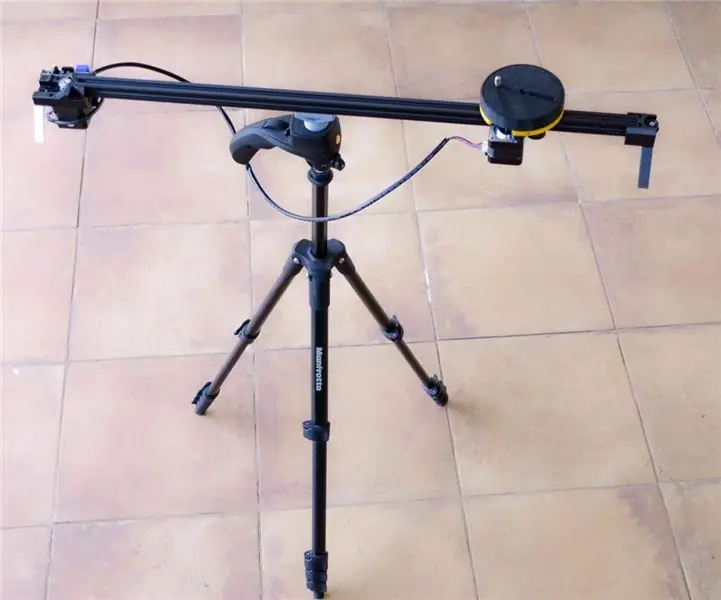
DESLIZADOR DE CÁMARA MOTORIZADO Con SISTEMA DE SEGUIMIENTO (Impreso en 3D): Básicamente, este robot moverá una cámara / teléfono inteligente en un riel y “rastreará” un objeto. El robot ya conoce la ubicación del objeto objetivo. La matemática detrás de este sistema de seguimiento es bastante simple. Hemos creado una simulación del proceso de seguimiento
Coche impreso en 3D inalámbrico con control remoto de Play Station: 7 pasos (con imágenes)
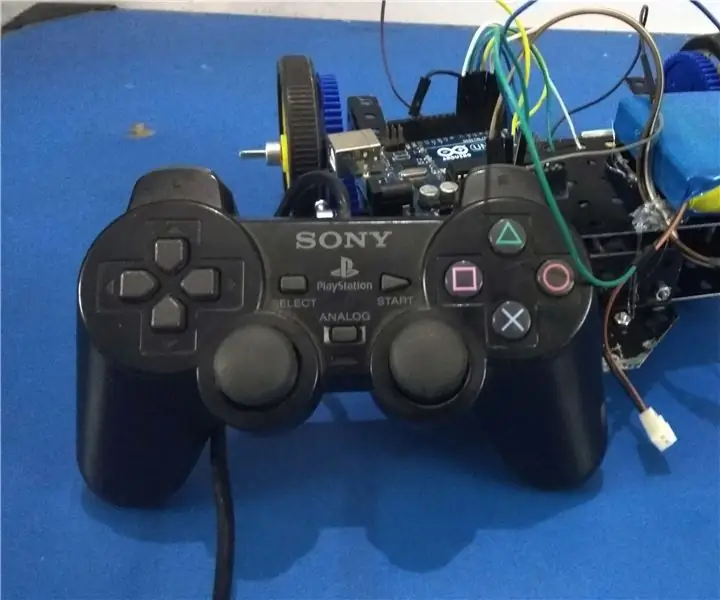
Coche impreso en 3D inalámbrico con control remoto de Play Station: ¿Quién no ama los juegos? ¡¡Carreras y peleas en el mundo virtual de Play Station y Xbox !! Entonces, para llevar esa diversión a la vida real, hice este Instructable en el que te mostraré cómo puedes usar cualquier control remoto de Play Station (cableado