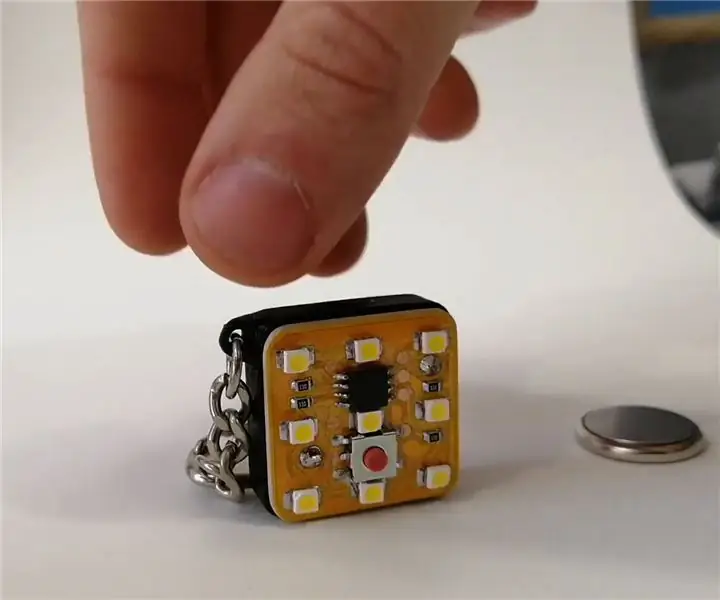
Tabla de contenido:
- Paso 1: Materiales, suministros y herramientas
- Paso 2: prepara todas las pegatinas
- Paso 3: Grabe el revestimiento de cobre
- Paso 4: cortar y lijar los dados
- Paso 5: Aplicación de las pegatinas Kapton Soldermask
- Paso 6: Ensamble los dados: Aplicación de pasta de soldadura
- Paso 7: soldadura por reflujo y población
- Paso 8: Imprima en 3D los estuches del llavero
- Paso 9: haga una plantilla de programación
- Paso 10: Programando los dados
2025 Autor: John Day | [email protected]. Última modificación: 2025-01-23 14:39
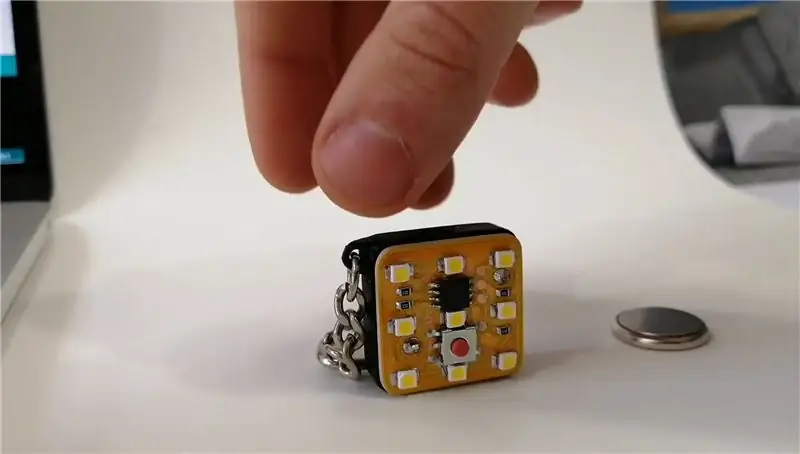
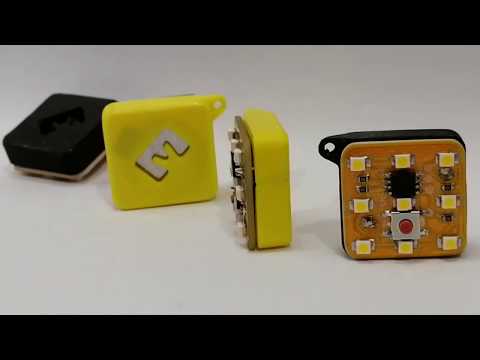
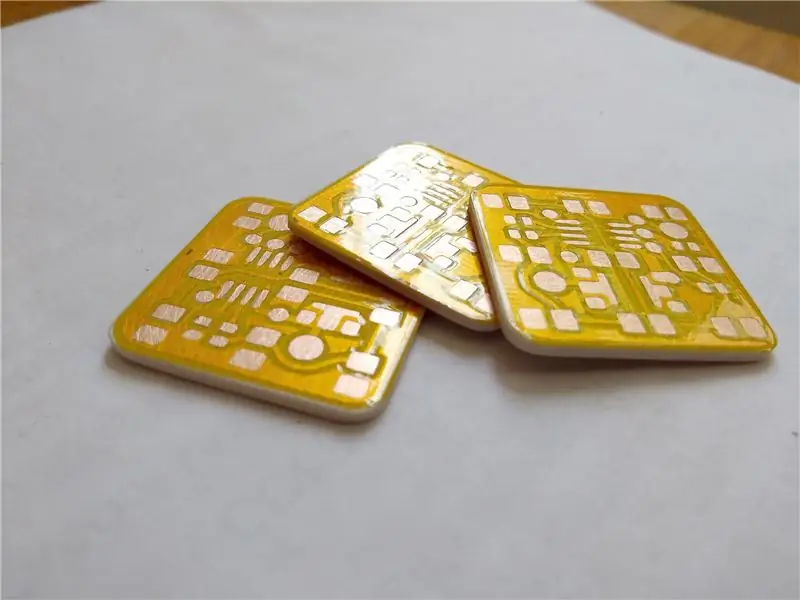
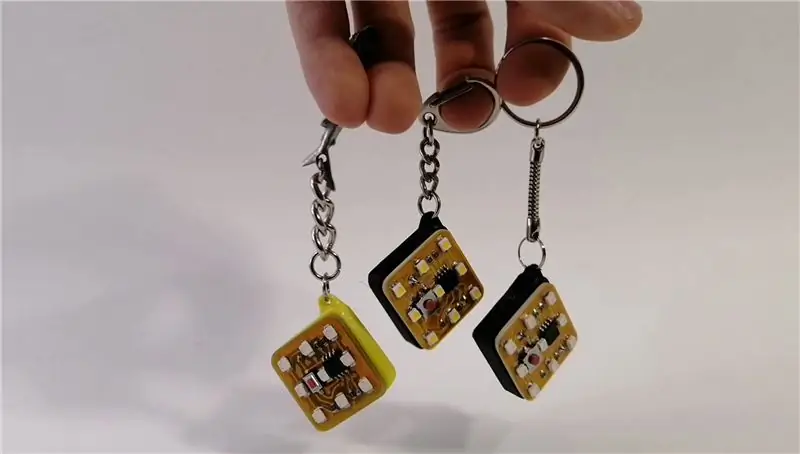
Este instructivo consiste en una guía paso a paso que documenta un método de fabricación de PCB de calidad profesional en el hogar mediante el uso de un cortador de vinilo, de una manera confiable, simple y eficiente. Este método permite la producción de PCB consistentes y de alta calidad en el hogar con pocos materiales comunes y en un período de tiempo muy corto. Con todos los archivos listos, todo el proceso se puede realizar en unas pocas horas.
Asunto de la guía, tinyDice:
A los efectos de esta guía, el proceso se ilustrará con la producción de un lote de 3 tinyDice, un dado electrónico basado en el microcontrolador atTiny85 con software charlieplexing, que permite el control de 9 LED con solo 4 pines y 4 resistencias. Es una versión mejorada de mi tinyDice original (2014), y todos los archivos fuente necesarios para este Instructable están disponibles para descargar como un paquete comprimido en el paso de suministros.
Origen del método:
Como entusiasta de la electrónica, he tenido bastante experiencia en la fabricación de PCB en el pasado, pero la mayoría de los métodos domésticos son excesivamente poco fiables, como el método de transferencia de tóner, o excesivamente complejos y laboriosos, como el método de enrutador CNC o el UV. método de fotorresistencia (que he cubierto en el pasado en el tinyDice original). Además, la calidad final de los productos tiende a ser bastante mala, especialmente si intenta implementar máscaras de soldadura UV.
A partir de estas experiencias insatisfactorias, decidí explorar métodos alternativos para crear PCB en casa. Como recientemente comencé a experimentar con un cortador de vinilo de escritorio, se me ocurrió que un sello de vinilo podría ser una máscara excelente y confiable para el grabado de PCB. En la investigación inicial en línea, no encontré ninguna referencia de personas que usaran sellos de vinilo para fabricar PCB, lo que me sorprendió porque parece muy plausible. Esto me motivó a experimentar con el proceso y descubrir si podía funcionar de manera confiable y eficiente para transferir trazas de PCB de la computadora al cobre.
Desarrollo de los procesos:
Hacer trazos de cobre limpios y consistentes en una PCB doméstica es en sí mismo un logro, pero para que las PCB funcionen correctamente y duren mucho, requieren algún tipo de máscara de soldadura, que evita puentes de soldadura no deseados y protege las trazas de cobre de la corrosión. Tradicionalmente, la máscara de soldadura utilizada está en forma de resina curable por UV, con la que en la práctica es bastante difícil trabajar.
Originalmente, tenía la intención de usar maceradores de vinilo indirectamente como una máscara para curar la máscara de soldadura UV. Sin embargo, en varios intentos, no pude lograr que la máscara de soldadura UV se curara de manera confiable solo en los lugares previstos, y nunca pude hacer una capa lo suficientemente delgada y uniforme, lo que finalmente resultó en un montón de tablas arruinadas. Por lo tanto, descarté esa idea y se me ocurrió que quizás algún tipo de sello también podría usarse directamente como máscara de soldadura, aunque ciertamente no podría ser de vinilo, ya que no resistiría el calor de la soldadura por reflujo.
Con esto en mente, miré a la cinta Kapton, que es autoadhesiva, delgada y promete resistir temperaturas lo suficientemente altas para soldar. La cinta Kapton se vende en rollos, pero se me ocurrió que si se aplicara sobre el respaldo de vinilo convencional, podría cortarse directamente en el cortador de vinilo y usarse directamente como sello. Desde la primera prueba de esto, fue evidente que la cinta Kapton se comportó de manera bastante prometedora en el cortador de vinilo, aunque todos los cortes que pasaban por pequeñas burbujas eran irregulares o incompletos, por lo que la clave para perfeccionar los sellos de Kapton fue aplicar la cinta perfectamente en el respaldo de vinilo sin permitir que el aire quede atrapado debajo. Inicialmente, esto resultó bastante complicado, ya que Kapton es excesivamente delgado y pegajoso, pero al tratar de colocarlo con una tarjeta de plástico estándar, me di cuenta de que se podía hacer perfecta y fácilmente de esta manera.
A través de estas pruebas iterativas, también observé algunas de las limitaciones prácticas del proceso, que mailny tiene que ver con la máscara de cobre como originalmente un sello. Estas limitaciones se convirtieron en un conjunto de pautas de diseño para hacer que este proceso sea confiable.
Paso 1: Materiales, suministros y herramientas
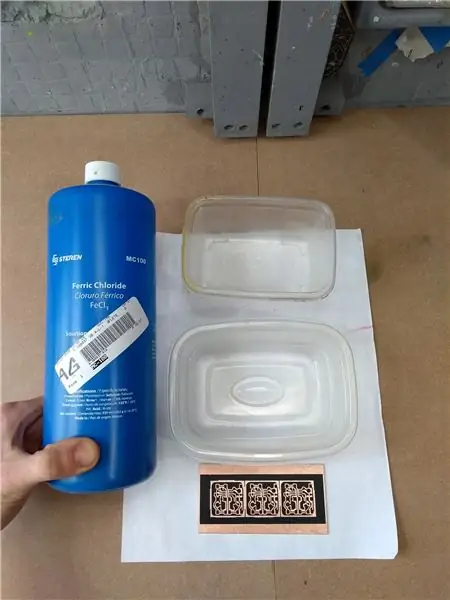
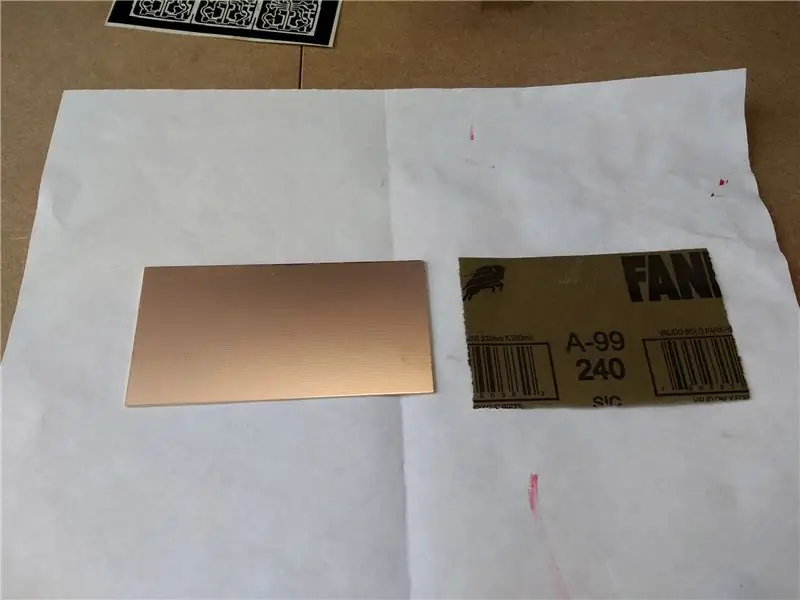
Materiales:
- PCB en blanco de 5 x 10 cm
- Vinilo autoadhesivo de 10 x 15 cm
- Cinta Kapton de 50 mm de ancho
- Película de transferencia de vinilo de 10 x 15 cm
Suministros:
- Grabador de cloruro férrico
- Alcohol isopropílico
- Pasta de soldadura
- Filamento PETG (para la caja del llavero)
Instrumentos:
- cortadora de vinilo de escritorio (yo uso el Silhouette Cameo 3, pero cualquier máquina básica funcionará)
- Estación de reparación de aire caliente (no indispensable pero útil)
- soldador
- tarjeta de plástico (identificación antigua o de cualquier tipo)
- USBtinyISP o Arduino como ISP
- cortador de acrílico manual (se puede hacer en casa a partir de una sección de una hoja de sierra vieja)
- Papel de lija de grano 220 y 400
- Impresora 3D (opcional, solo para hacer el estuche del llavero)
Software:
- Silhouette Studio (o equivalente para otras marcas de cortadores de vinilo)
- EAGLE CAD (no es necesario si no tiene la intención de modificar el diseño)
- Photoshop o cualquier editor de imágenes (no es necesario si no tiene la intención de modificar el diseño)
- Arduino IDE + atTinyCore
- AVRDUDESS
- Slic3r o cualquier otro software de impresión 3D.
-
paquete de recursos tinyDice, (disponible para descargar en este paso como un archivo RAR)
Componentes:
para cada tinyDice85:
- 9 LEDs SMD 3528 (cualquier color, recomendado de todos modos)
- 1x attiny85 (SOIC)
- 4 resistencias de 33 ohmios 0805 (el valor exacto no es crítico, use cualquier valor similar pero de todos modos)
- 1x pulsador SMD
- 1x clip de batería CR20XX
- 1x batería CR2032
Para la plantilla de programación:
- 6x pines pogo
- 1x conector macho 2x3 (para ISP)
- 1 conector macho 2x1 (para fuente VCC externa)
- 1x regulador AMS1117 3.3v LDO (SOT-23)
Paso 2: prepara todas las pegatinas
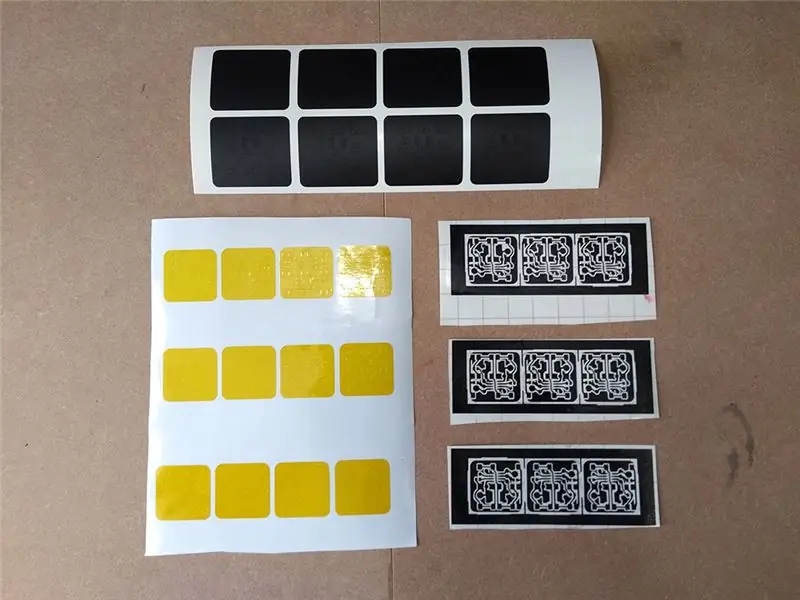
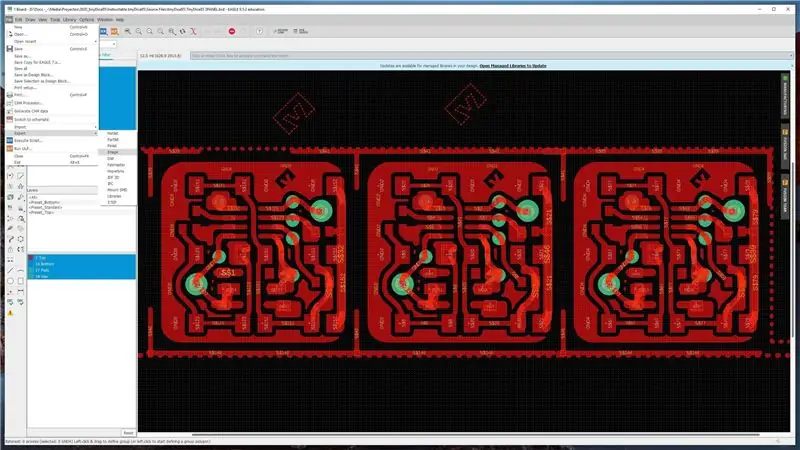
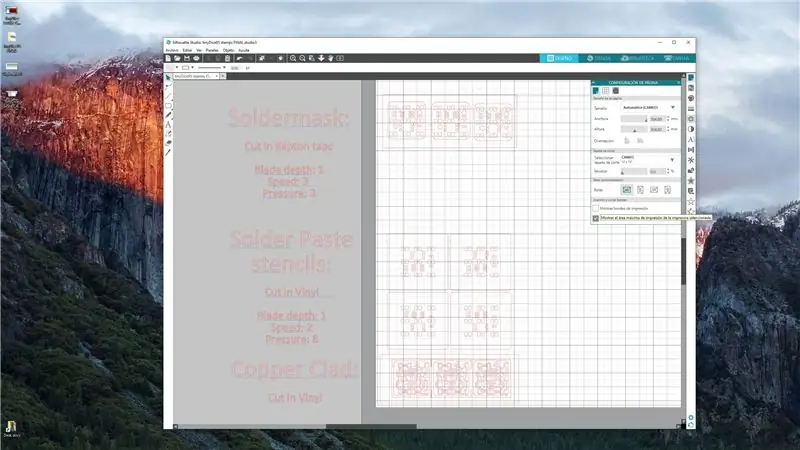
Para este proceso de fabricación de PCB en el hogar, las pegatinas están involucradas en tres etapas; Como máscara para grabar el revestimiento de cobre, como máscara de soldadura para proteger los rastros y restringir la soldadura, y como plantilla para aplicar pasta de soldadura en las almohadillas. Para optimizar al máximo el proceso, todas las pegatinas se pueden preparar en un solo asiento.
Preparando los archivos para cortar:
Si no tiene la intención de modificar el diseño, puede usar directamente las imágenes preparadas o el archivo de Silhouette Studio con todas las pegatinas. Si usa otro diseño, haga lo siguiente para preparar el archivo para cortarlo:
Como la mayoría de los programas de corte de vinilo gratuitos funcionan con imágenes, debemos exportar el diseño de EAGLE como una imagen de alta resolución. Para esto, primero oculte toda la capa menos TOP y VIAS, luego exporte el panel como una imagen en MONOCROMO y al menos 1500 dpi. A continuación, repita el proceso pero solo con la capa Tstop, para obtener solo las almohadillas.
Una vez que exportas las imágenes, es recomendable hacer un poco de limpieza en Photoshop para aumentar la confiabilidad del proceso. Para la imagen revestida de cobre, esto consiste en borrar las pequeñas áreas de cobre aisladas o conectarlas a áreas más grandes, borrando el centro de todos los orificios pasantes y aumentando el espacio libre alrededor de las térmicas. Para la imagen de las almohadillas, debe colocarlas sobre una forma negra que desborde un poco todo el revestimiento de cobre.
A continuación, importe las imágenes en el software de corte de vinilo, trácelas y escale a un tamaño de 100 x 100 mm. Una ventaja de panelar los PCB es que tiene una referencia consistente para escalarlos correctamente independientemente de la resolución.
Preparación de la cinta Kapton para cortar:
La cinta Kapton es un gran material, sin embargo, para utilizarla como adhesivo, primero debemos colocarla sobre un soporte plano. Para esto utilizaremos el respaldo de la cinta de transferencia de vinilo, así que despegue el paté y déjelo a un lado temporalmente, teniendo cuidado de mantenerlo limpio. A continuación, desenrolle un segmento de cinta y aplíquelo con cuidado sobre el respaldo del papel encerado usando una tarjeta de plástico como escobilla de goma para asegurarse de que no queden burbujas atrapadas debajo. Recomiendo prepararse más de lo que espera utilizar, ya que es posible que algunas pegatinas no salgan perfectamente.
Cortar las pegatinas:
Una vez que haya trazado y escalado todas las pegatinas en el software del cortador de vinilo, proceda a colocar el material de vinilo autoadhesivo en una esquina del tapete de corte y coloque la cinta Kapton con respaldo en otra esquina.
A continuación, en el software, coloque solo los diseños de la plantilla con revestimiento de cobre y pasta de soldadura sobre el área correspondiente al vinilo y establezca los parámetros de corte en: Velocidad 3, Profundidad de la hoja 1, Presión 8. Envíe el trabajo a cortar y deje que la máquina lo haga. es cosa.
Finalmente, deje a un lado los diseños utilizados anteriormente y coloque solo el diseño de la máscara de soldadura sobre el área correspondiente a la cinta Kapton. Establezca los parámetros de corte en: Velocidad 1, Profundidad de la hoja 1, Presión 3. Proceda a enviar el trabajo a la máquina y una vez terminado retire con cuidado tanto el vinilo autoadhesivo como los materiales Kapton del tapete de corte. Tenga cuidado de no hacer pliegues agudos al despegarlos.
Deshierbe de las pegatinas:
Para transferir las pegatinas de vinilo a la PCB, debemos utilizar una película de transferencia de vinilo para garantizar que todas las regiones se transfieran en su lugar. Para poder transferir solo los segmentos previstos del sello, debemos eliminar todas las áreas no deseadas antes de aplicar la película de transferencia. Para ello, utilice un cortador y levante con cuidado una esquina del área no deseada. Empuja el cortador debajo y presiona el vinilo sobre la cuchilla para que se pegue. A continuación, retire el cortador y el exceso debería comenzar a pelarse. Dependiendo del diseño, todas las áreas no deseadas pueden salir como una sola pieza. Una vez desyerbado, coloque la película de transferencia SOLAMENTE sobre las pegatinas revestidas de cobre y deseche todo el exceso. En este punto, las pegatinas de vinilo están listas para su uso. Las pegatinas de cinta Kapton son de una sola pieza, por lo que se pueden transferir directamente sin la película de transferencia.
Paso 3: Grabe el revestimiento de cobre
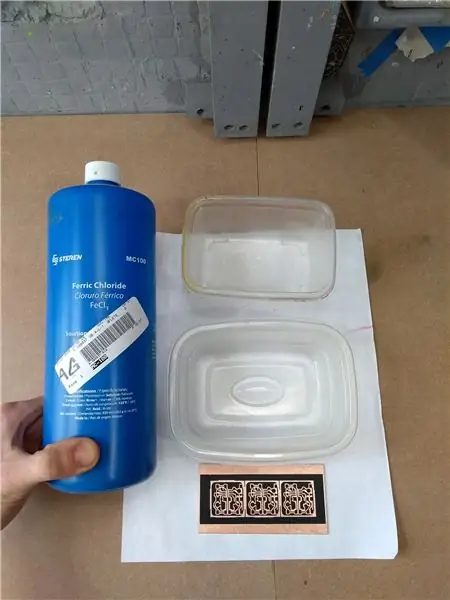
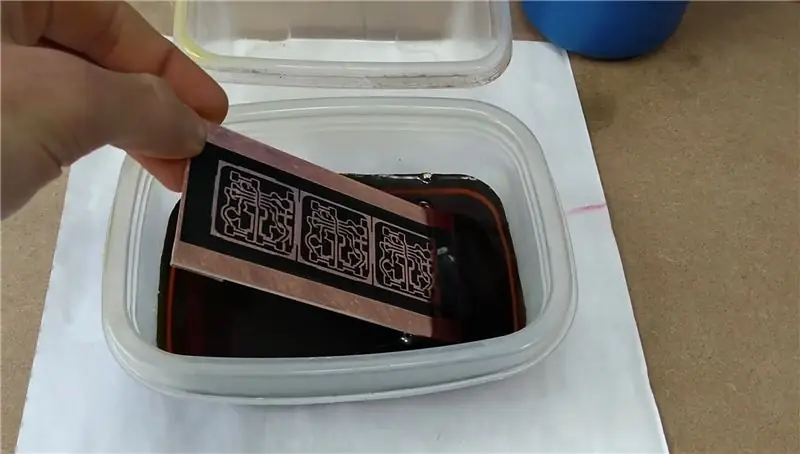
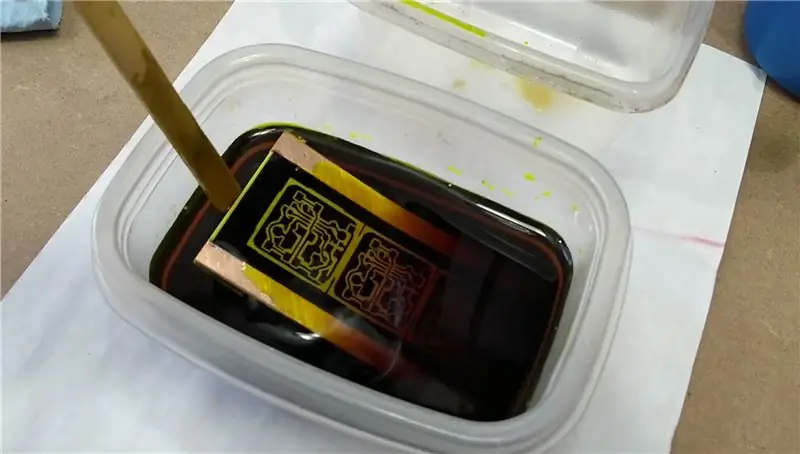
Este es el paso más importante del proceso, ya que la calidad de las trazas de cobre determinará la tasa de éxito de los productos finales. Si se hace con cuidado, puede llegar al 100%.
Transfiriendo la pegatina CLAD al cobre:
Para garantizar resultados limpios y fiables, primero debe desengrasar la placa de circuito impreso en blanco con alcohol isopropílico. Si la pieza en bruto es vieja, se recomienda lijar bien la superficie con papel de lija de grano 320-400 haciendo pequeños círculos por todo el tablero.
Una vez que esté completamente limpio, es hora de transferir la pegatina al cobre. Para ello, primero despegue una esquina de la película de transferencia y luego coloque la pegatina boca abajo sobre una mesa limpia. A continuación, proceda a despegar lentamente el papel de la transferencia haciendo un pliegue agudo y tirando a lo largo de la mesa. De esta manera, incluso las almohadillas pequeñas deben adherirse a la transferencia y no permanecer en el papel. Sin embargo, no se preocupe si una o dos almohadillas se quedan atrás, puede colocarlas manualmente más tarde.
A continuación, sostenga la transferencia de vinilo con la pegatina con las puntas de los dedos (péguelas ligeramente hasta el borde) y alinee lentamente la pegatina sobre el tablero antes de colocarla. Una vez alineado, colócalo sobre el cobre y presiónalo suavemente hacia abajo con los dedos FORMAR EL CENTRO HACIA FUERA, para evitar burbujas atrapadas. A continuación, utilice una tarjeta de plástico para limpiar toda la superficie para asegurarse de que el vinilo se adhiera con fuerza al cobre. Proceda a despegar la película de transferencia de vinilo del revestimiento de cobre de la misma manera que despegó el respaldo de papel y coloque manualmente las almohadillas que quedaron atrás. Si la pegatina no cubre todo el espacio en blanco, puede cubrir cualquier área restante con cinta transparente para evitar grabar el exceso de cobre y abusar de sus suministros.
Grabado del revestimiento de cobre:
Para el proceso de grabado, necesitará 2 recipientes rectangulares estilo Tupperware, un pequeño palito de madera y el grabador de cloruro férrico.
El tablero preparado con el sello CLAD está casi listo para grabar, pero es muy importante limpiarlo una vez más con alcohol isopropílico para eliminar cualquier residuo de la película de transferencia y asegurar un grabado uniforme y completo, sin restos de cobre no deseado.
Para preparar el cloruro férrico para el grabado, viértalo en uno de los recipientes hasta aproximadamente la mitad y agregue alrededor de un 30% más de agua. En este punto, la solución está lista para el grabado, sin embargo, opcionalmente puede calentarla en el horno de microondas. durante 15 segundos ANTES de colocarlo en la PCB para acelerar el proceso de grabado.
Finalmente, coloca la tabla en el cloruro férrico y deja que se hunda. El proceso puede llevar un tiempo, pero es importante volver cada 10 a 15 minutos para remover la solución y verificar el progreso. Para esto, simplemente use un pequeño trozo de madera para alcanzar la tabla e inclínela hacia adentro y hacia afuera de la solución unas cuantas veces. Esto moverá la solución para asegurarse de que reaccione de manera uniforme y le permitirá ver cuánto cobre se ha eliminado. Siga haciendo esto hasta que no vea más cobre expuesto, pero no lo deje más tiempo, ya que el grabador puede comenzar a romperse debajo de la etiqueta y dañar las huellas. Mientras tanto, deje la barra en el otro recipiente para evitar manchar cualquier cosa con la solución de grabado, ya que es muy propensa a las manchas y también tiene un olor ferroso muy fuerte.
Una vez hecho esto, retira la tabla del grabador y enjuaga bien con abundante agua y jabón. Después de esto, tome un embudo o haga uno con una lámina de plástico y fíjelo sobre una botella de PP vacía para recuperar y almacenar el grabador. NUNCA deseche el cloruro férrico usado por el desagüe, reutilícelo tanto como sea posible y deséchelo dejándolo secar y luego deséchelo como un sólido.
El grabado es el paso del proceso que lleva más tiempo. Si se hace con cloruro férrico fresco, se puede lograr en menos de una hora, sin embargo, con los suministros reutilizados, puede tardar más de 4 horas en completarse, así que tenga paciencia y verifique periódicamente.
Paso 4: cortar y lijar los dados
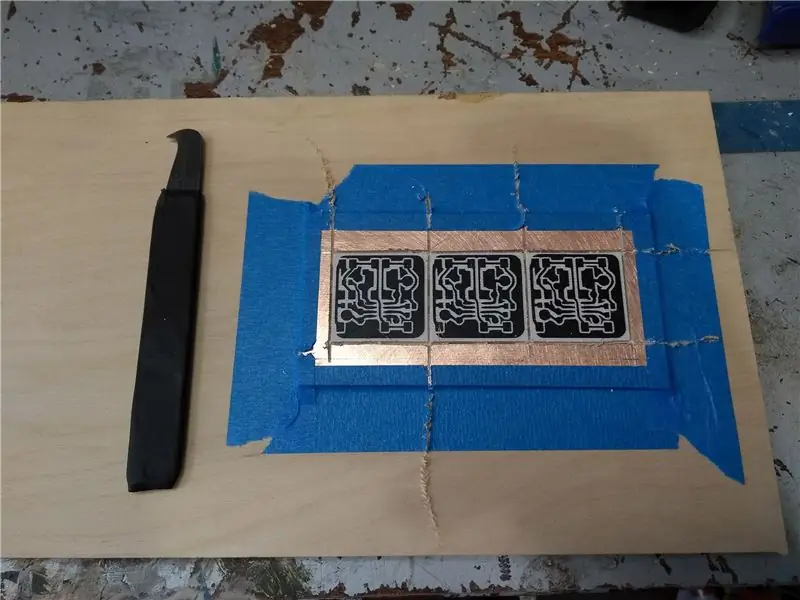
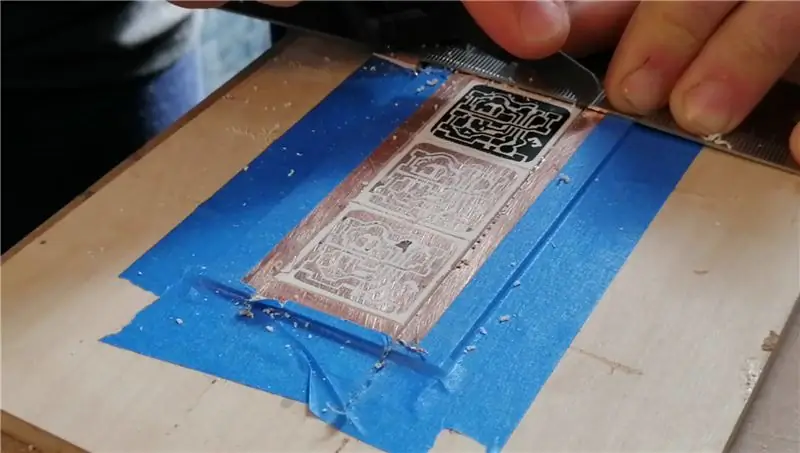
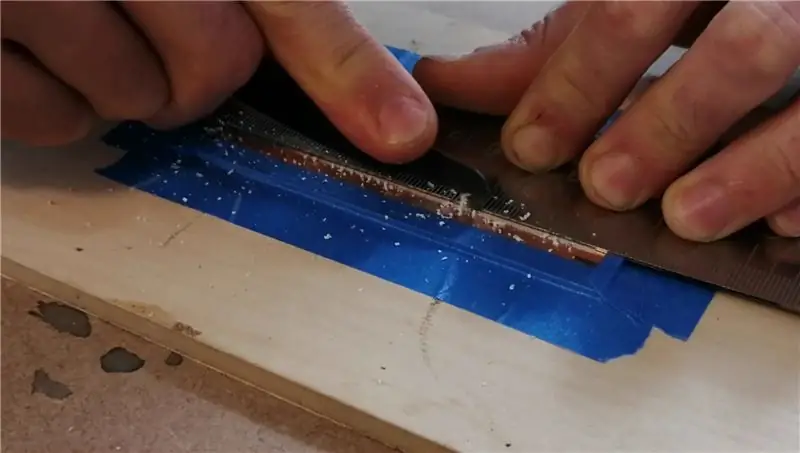
Una ventaja de los paneles de circuito impreso es que puede utilizar el panel como guía para el corte, además de que es más fácil manipular una placa más grande. Para poder separar las tablas y darles un acabado adecuado, primero debemos cortarlas y lijar los bordes y esquinas.
El corte de la PCB no se puede hacer con un cortador normal, tijeras o sierras, ya que estos procesos casi con seguridad fallarían o dañarían las placas. Para cortar, utilizaremos una herramienta de garra simple que raspa gradualmente las capas en cada pasada, haciendo una ranura en todo el camino. Estas hojas se venden comercialmente como cortadores acrílicos, pero también pueden fabricarse en casa con algunas hojas de sierra para metales rotas. Es aconsejable volver a afilar la hoja durante el proceso, ya que las tablas de fibra de vidrio desgastan el borde rápidamente. No es necesario cortar completamente, solo la mayor parte, y luego, simplemente desprenda cada pieza.
Después de cortar, los bordes quedan bastante rugosos y desiguales, por lo que debemos lijarlos a fondo primero con papel de lija de grano 240 y después con un grano de 400 para una mayor suavidad. Asegúrese también de redondear las esquinas siguiendo la forma del revestimiento de cobre.
Finalmente, utilice un cortador para despegar con cuidado las pegatinas de las tablas. Esto se puede hacer antes de cortar, pero las pegatinas ayudan a proteger el cobre durante el proceso de corte.
Paso 5: Aplicación de las pegatinas Kapton Soldermask
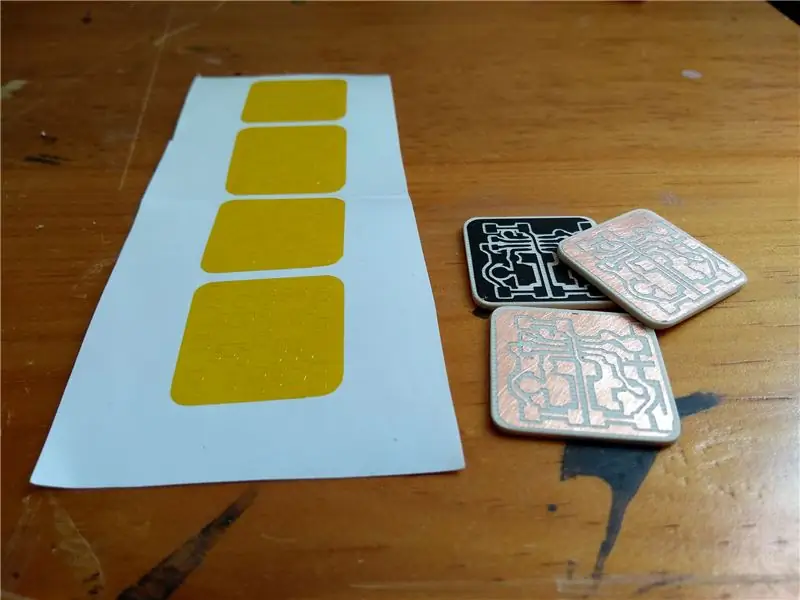
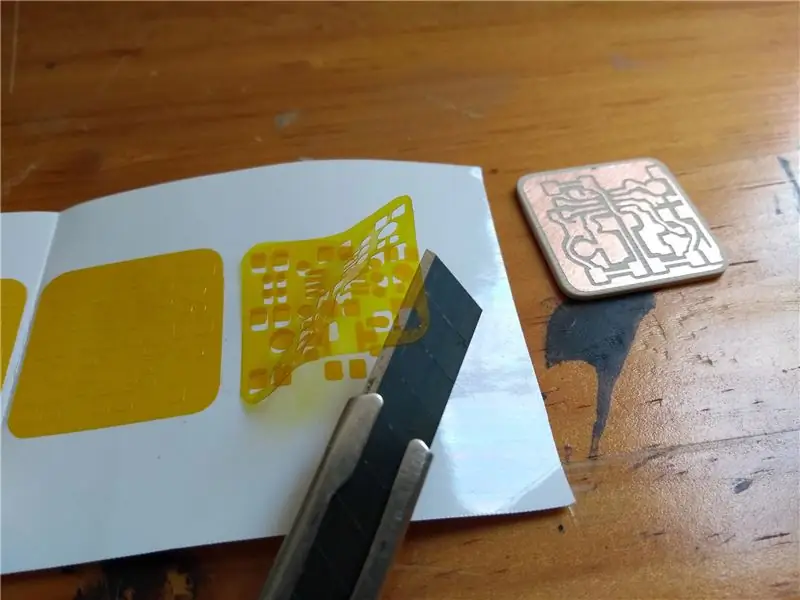
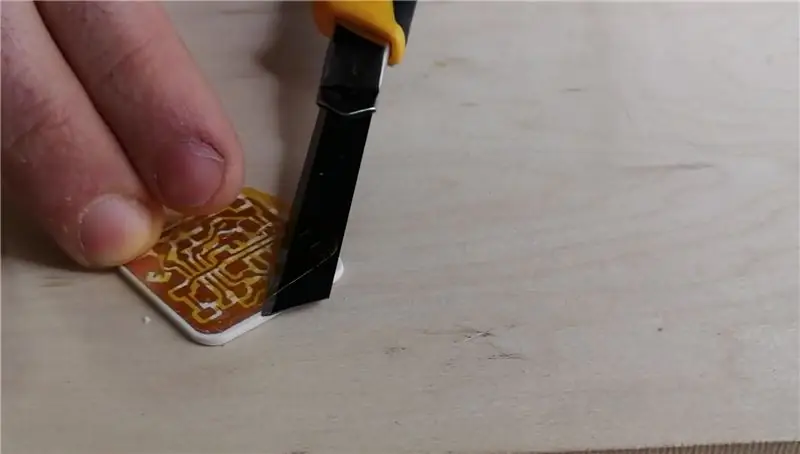
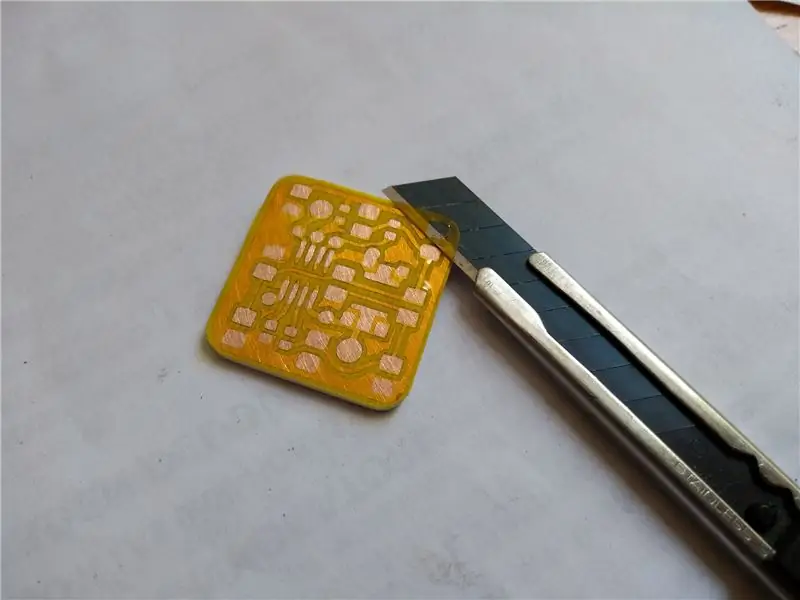
Ahora, con las placas cortadas, estamos casi listos para ensamblar el circuito, sin embargo, para asegurar que las trazas de cobre estén protegidas a largo plazo y la soldadura permanezca solo donde debería, necesitamos una máscara de soldadura, que se fabrica convencionalmente con resinas de curado UV.. El proceso tradicional es bastante tóxico, desordenado y poco confiable, por lo que se necesita una alternativa más práctica para la fabricación casera.
En este caso, aprovechamos la cinta Kapton como máscara de soldadura debido a su resistencia a altas temperaturas y propiedades autoadhesivas. Para transferir las pegatinas a las placas de circuito impreso utilizaremos nuevamente el cortador como soporte. Antes de transferir las pegatinas, limpie las placas de circuito impreso a fondo con alcohol isopropílico para eliminar la grasa o los residuos del vinilo. A continuación, proceda a levantar con cuidado la pegatina Kapton del papel de respaldo con el cortador (ver imagen 2). Para ello, primero levante una pequeña esquina de la pegatina con el cortador y presiónela contra la hoja para que se pegue, luego retire lentamente el cortador del papel sin hacer un pliegue en el borde afilado hasta que toda la pegatina se desprenda del papel. y se queda pegado a la hoja.
Finalmente, es importante asegurarse de que la pegatina esté correctamente alineada con las almohadillas antes de colocarla en su lugar, por lo tanto, póngala suavemente sobre la PCB con el cortador y cepíllela ligeramente sobre la placa unas cuantas veces, esto la cargará con estática y hará una especie de flotador en la superficie, lo que le permitirá ajustar la ubicación antes de presionarlo en su lugar. Si el sello se pega prematuramente, quítelo con cuidado del tablero mientras lo despega del papel y repita la alineación. Una vez alineado correctamente, presiónelo firmemente sobre la PCB con los dedos y retire con cuidado el cortador de la pegatina para terminar de colocarlo. A continuación, vuelva a limpiar las placas con alcohol y ahora los PCB están oficialmente terminados. Pueden usarse de inmediato o almacenarse para más adelante.
Paso 6: Ensamble los dados: Aplicación de pasta de soldadura
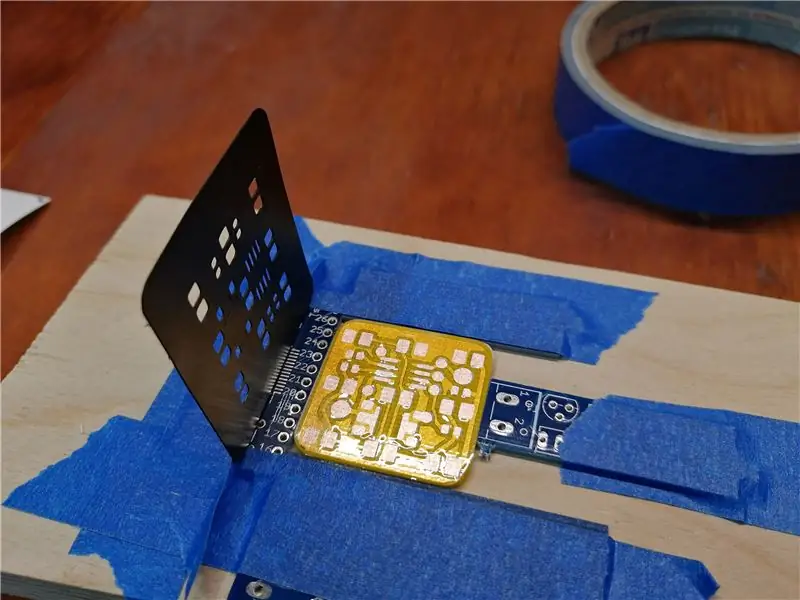
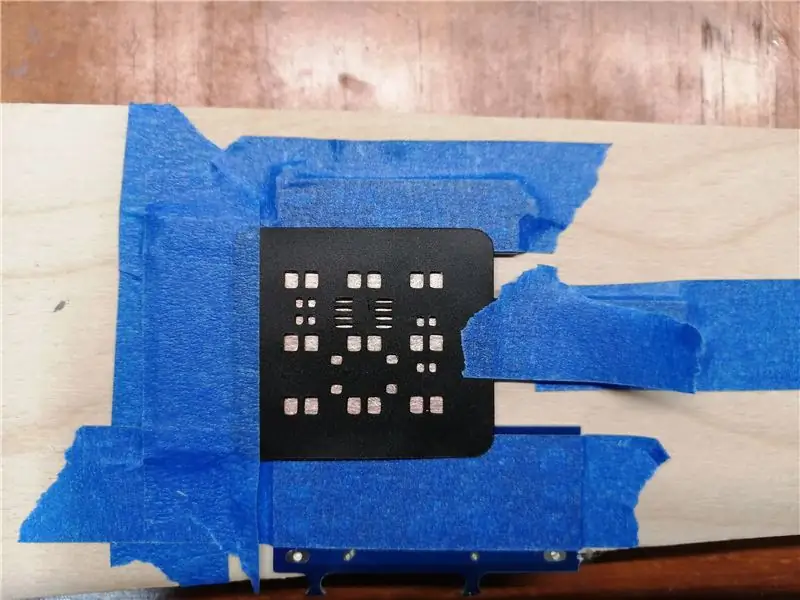
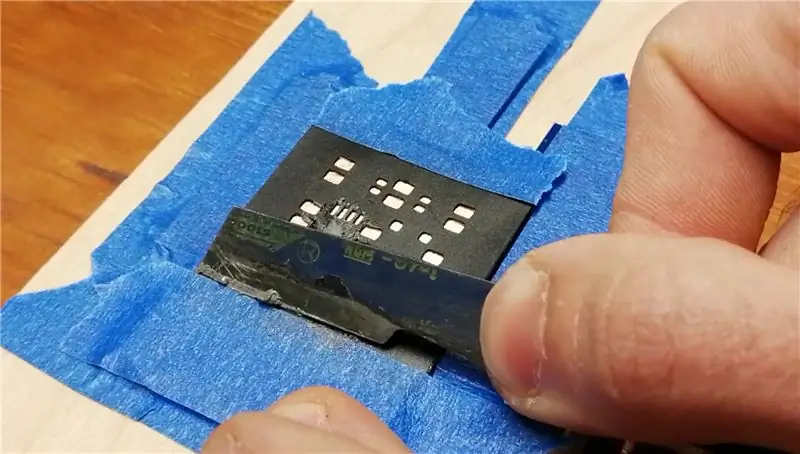
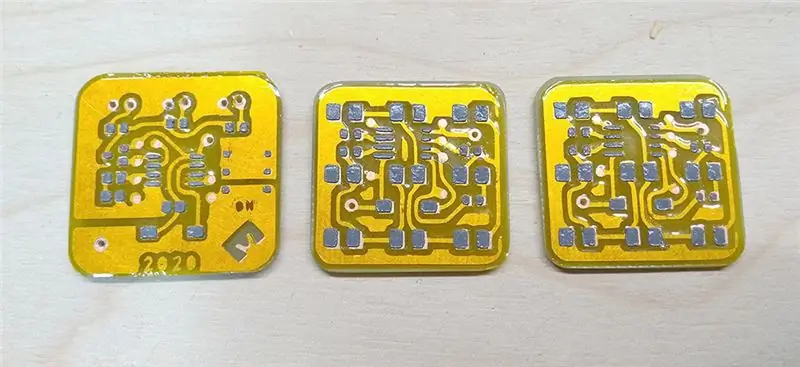
Una ventaja de los circuitos SMD es que se pueden soldar con pasta de una manera muy confiable y rápida utilizando una plantilla simple para aplicarla solo en las almohadillas, que se puede reutilizar para cualquier cantidad de unidades. Las plantillas SMD convencionales se fabrican en acero, por lo que son bastante caras y poco prácticas para la creación de prototipos, sin embargo, la plantilla también puede estar hecha de pegatinas de vinilo. Para ello, utilizamos tanto la versión original como la versión espejo de la pegatina para crear una plantilla de plástico que no sea autoadhesiva.
La pasta de soldadura contiene una gran cantidad de fundente, por lo que se reduce significativamente al refluir. Por lo tanto, necesitamos aplicar una capa lo suficientemente gruesa para asegurarnos de que las juntas se llenen correctamente con soldadura. Para hacer la plantilla del grosor adecuado, debemos colocar 4 pegatinas de vinilo juntas. Haga esto con cuidado para asegurarse de que los orificios estén perfectamente alineados por completo.
A continuación, construya un pequeño borde alrededor de una placa con PCB de desecho o cualquier otro material del mismo grosor y fije la plantilla en su lugar por un solo lado para que sirva como bisagra, asegurando la alineación adecuada de la plantilla sobre las almohadillas (consulte la imagen 2).).
Finalmente, usando cualquier tipo de herramienta de borde recto, agarre un poco de pasta de soldadura y comience a esparcirla sobre la plantilla hasta que todos los agujeros estén llenos, y raspe el resto en la botella con la misma herramienta. No toque la pasta de soldadura directamente, ya que contiene plomo, que es mejor evitarlo. No se preocupe si lo toca, simplemente límpielo a fondo.
Levante la plantilla y retire la tabla de la plantilla. Repita el proceso para todas las tablas que desee ensamblar. Ahora las placas están listas para poblar y soldar.
Paso 7: soldadura por reflujo y población
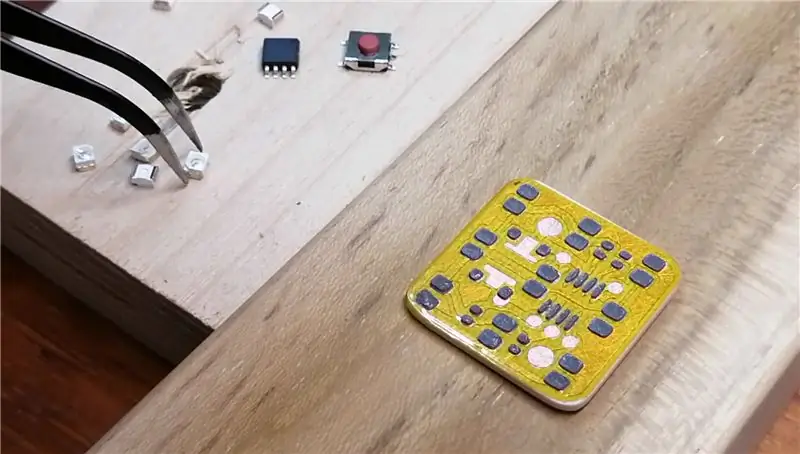
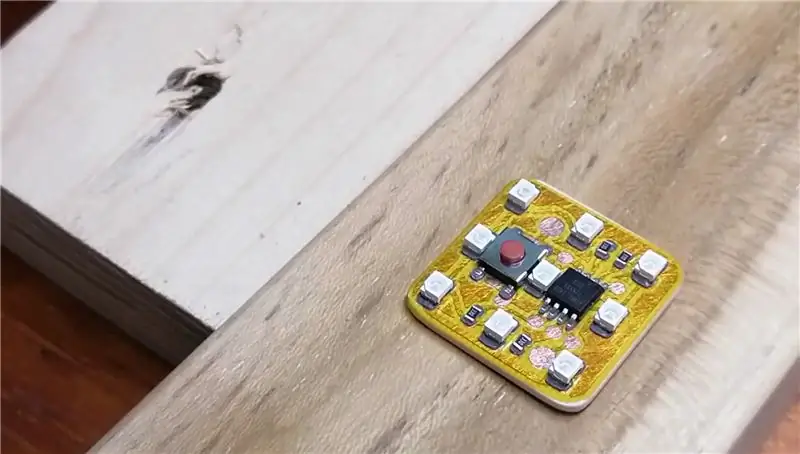
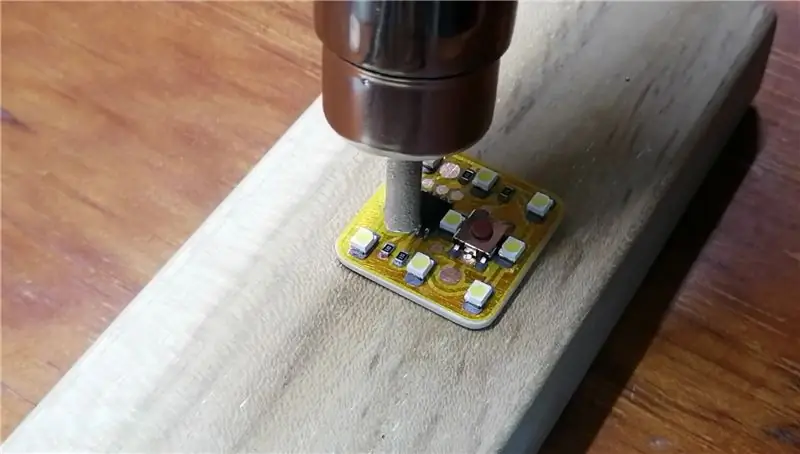
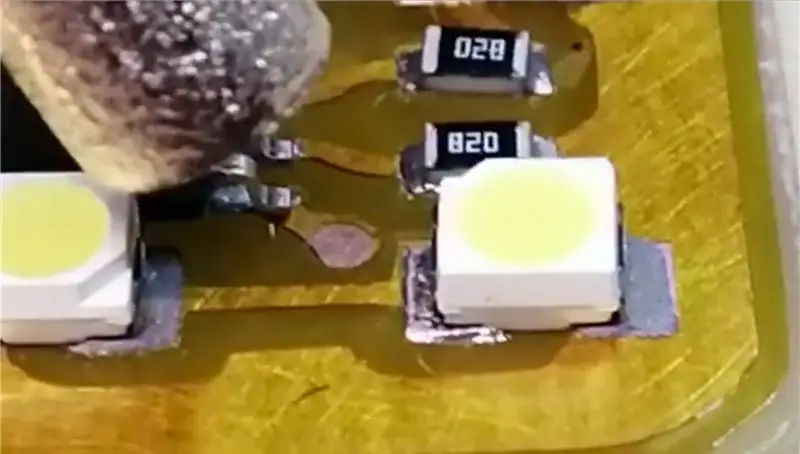
Con la pasta de soldadura en las placas, es hora de rellenar todos los componentes. Para esto, use unas pinzas de punta fina y coloque con cuidado cada componente en sus almohadillas, asegurando una orientación y alineación adecuadas (ver imagen 2). Tómese su tiempo para hacer esto y corregir cualquier error. Una vez que se hayan colocado todos los componentes, encienda la herramienta de reflujo de aire y comience a precalentar gradualmente toda la placa colocando el cursor sobre ella en círculos (ver imagen 3). A continuación, proceda a dirigir el aire caliente directamente sobre cada almohadilla hasta que refluyan por completo (imagen 4). Cuando termine de refluir, es hora de agregar el clip de la batería. Para ello, taladre los centros de las 2 almohadillas redondas más grandes y coloque el clip de la batería en la parte inferior de la tabla. También es aconsejable pegar el clip de la batería a la placa con epoxi para aliviar la tensión de los pines de alimentación, ya que el clip sujetará la placa a la carcasa. En este punto, la PCB está completamente ensamblada y lista para la programación.
Paso 8: Imprima en 3D los estuches del llavero
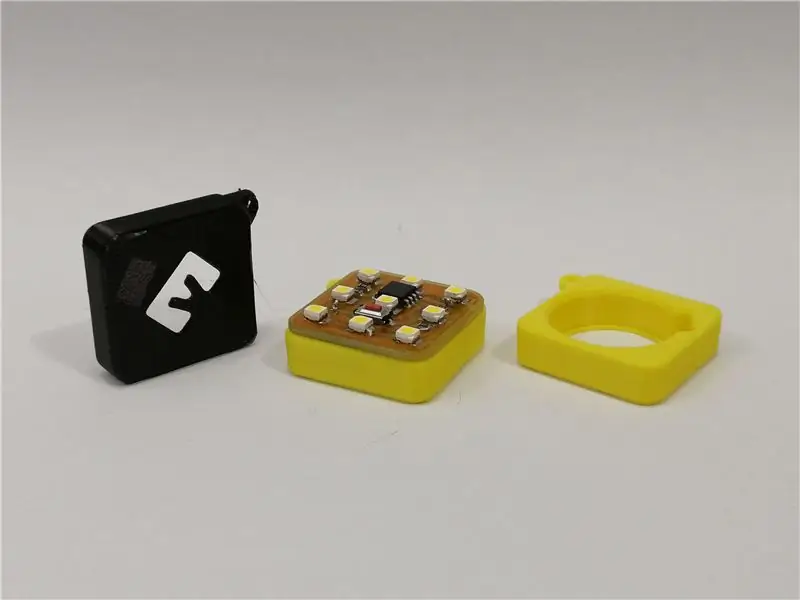

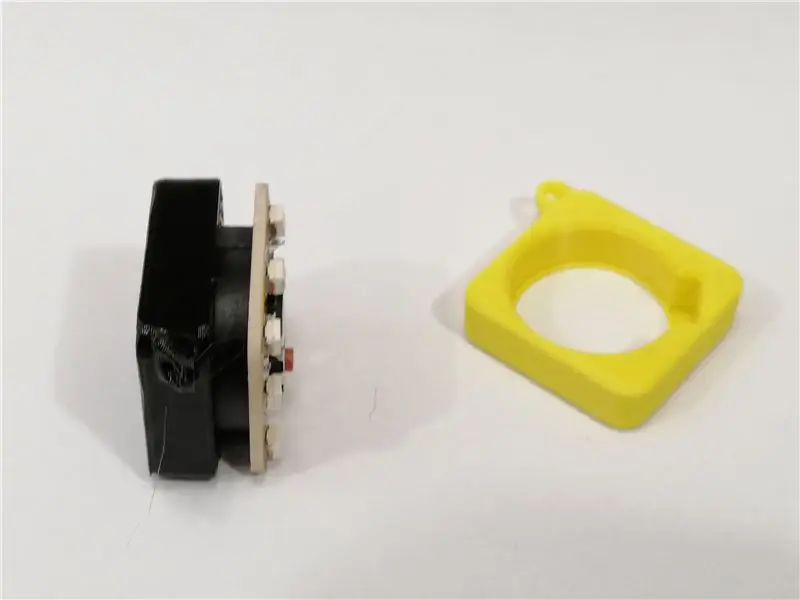
Los estuches impresos en 3D son opcionales pero muy recomendables, ya que agregan mucho carácter al objeto al convertirlo en un llavero, al mismo tiempo que protegen el troquel. Es obligatorio imprimirlos en PETG para garantizar una alta durabilidad, ya que lo más probable es que el PLA se rompa muy rápidamente. Hice dos versiones del estuche, uno con un respaldo hueco para quitar la batería y otro con mi logo en la parte posterior, lo que mantiene la batería segura y oculta. Como el circuito consume muy poca energía, la batería puede quedar atrapada dentro del estuche. Sin ningún problema.
Para ensamblar la caja, simplemente coloque el clip de la batería en la impresión 3D hasta que el tablero esté al ras con el borde. Dependiendo de su clip de batería exacto, es posible que deba lijarlo ligeramente o aumentar la altura de la caja para asegurarse de que encaje completamente, así que asegúrese de verificar antes de ensamblar. Sin embargo, si es necesario, la caja se puede abrir tirando lentamente de la tabla alrededor del borde.
Paso 9: haga una plantilla de programación
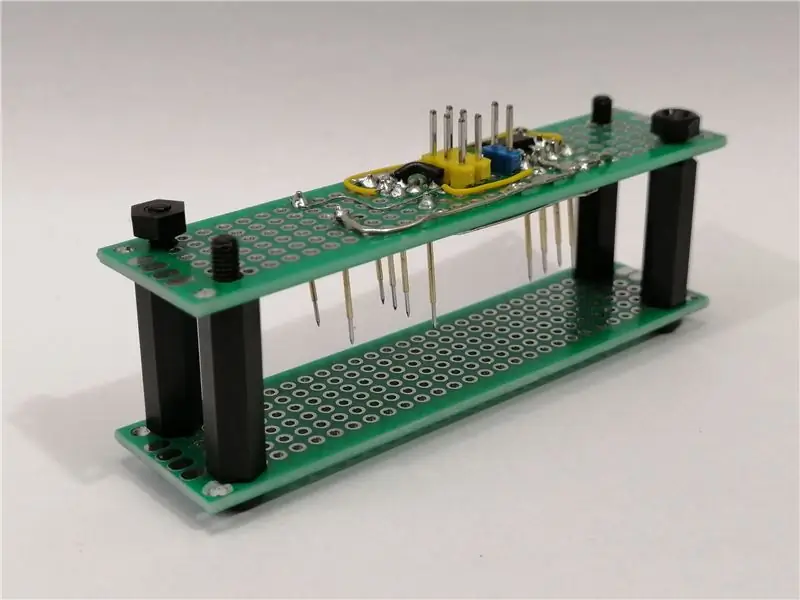
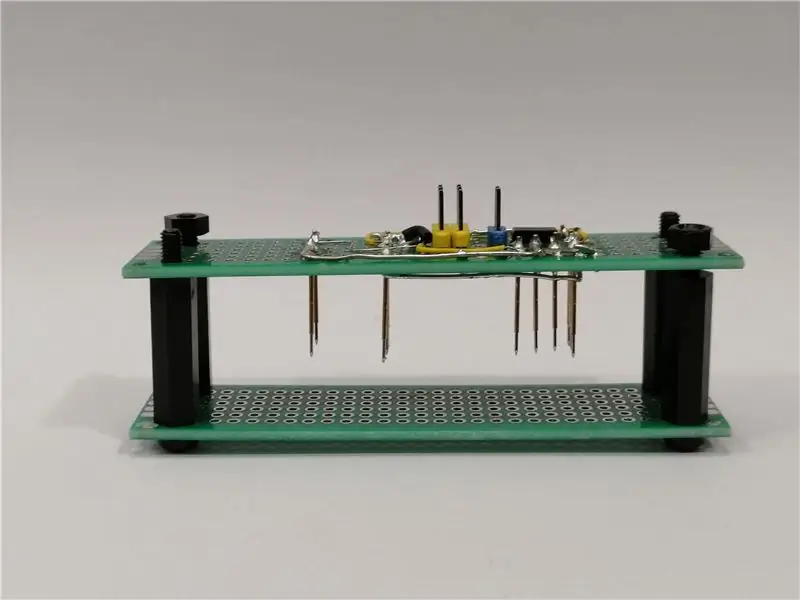
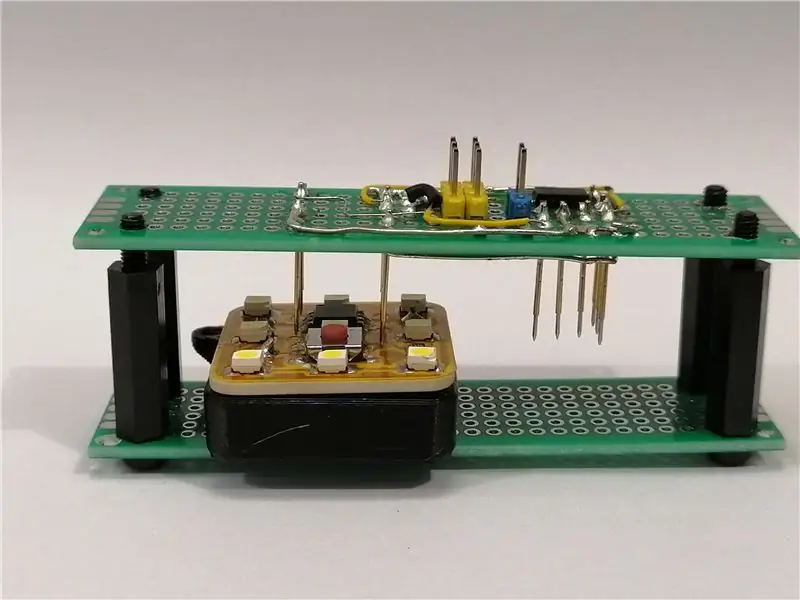
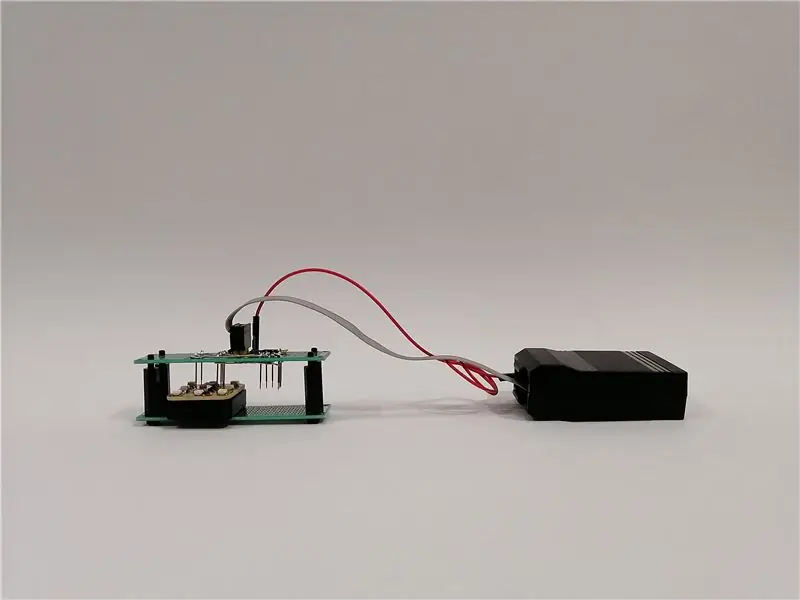
Ahora los tinyDice están completamente ensamblados, sin embargo, debemos programarlos para que funcionen como deberían. Para ello, utilizamos un pogo pin jig que contacta con todos los pads de programación de la placa y se conecta a un programador ISP, que puede ser un USBtinyISP o cualquier Arduino como ISP. El tinyDice tiene todos los pines de programación disponibles en pads con un espaciado estándar de 100 mil (2,54 mm), para permitir el montaje de la plantilla en una placa perforada estándar. Siga el diagrama de conexión para vincular cada pin pogo al encabezado del ISP. Para propósitos de desarrollo, hice una plantilla doble que también sirve para otra placa en la que estoy trabajando e incorporé un regulador LDO para evitar agotar las baterías durante la prueba, pero para una programación única podemos utilizar la energía directamente de la batería.
tinyDice están diseñados para funcionar a 3 voltios, por lo que programarlos a 5 voltios plantea el riesgo de dañar los pines de E / S del microcontrolador, los LED o incluso el programador, ya que se pasaría demasiada corriente a través de las resistencias limitadoras de corriente del LED. Entonces, para programar el chip sin dañar nada, debemos utilizar su voltaje nativo de la batería. Si usa un USBtinyISP, simplemente retire su puente de alimentación, que alimentará la palanca de cambio lógica interna de la batería del tinyDice, y si usa un Arduino, simplemente deje la energía desconectada para alimentar solo los dados con la batería, y agregue una resistencia de la serie 5k a cada línea de datos.
Paso 10: Programando los dados
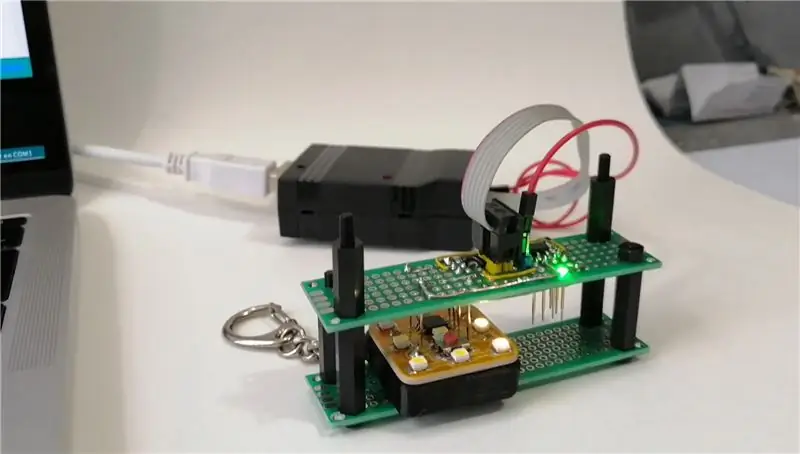
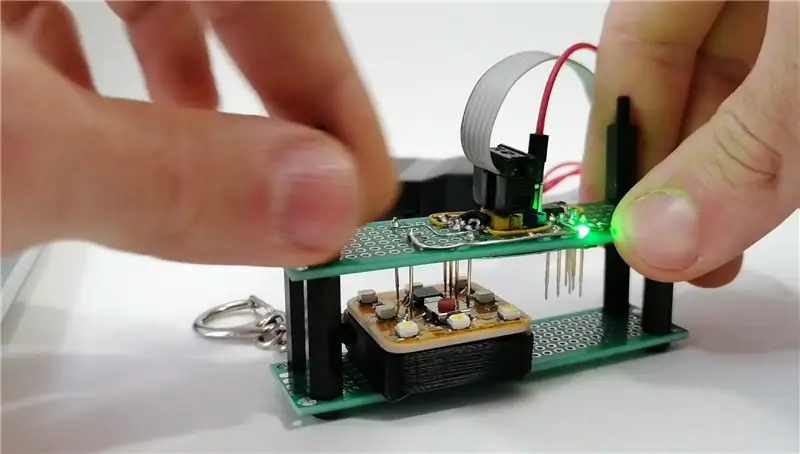
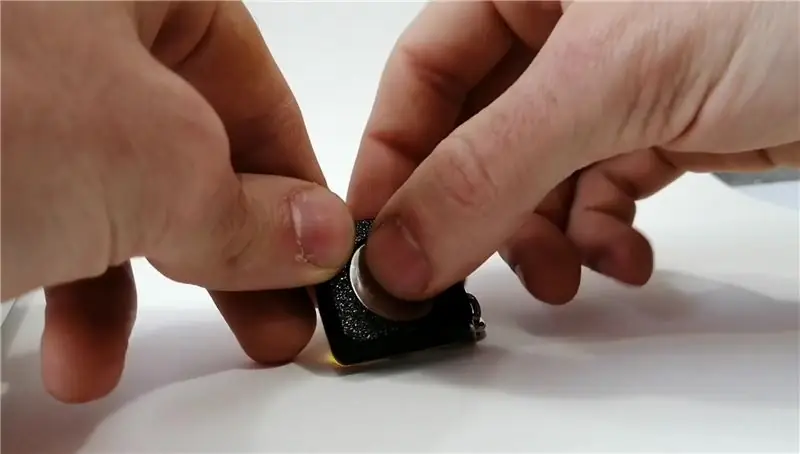
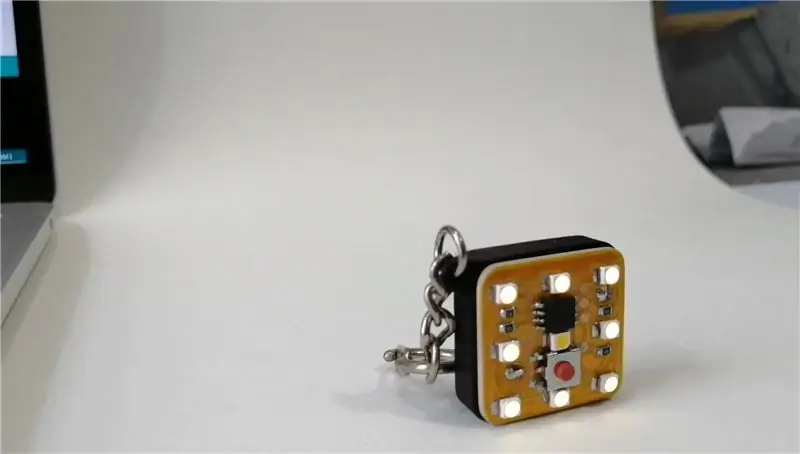
Para el proceso de programación, ensamble cuidadosamente la plantilla sobre los dados usando separadores y asegúrese de que todos los pines de pogo presionen correctamente sobre las almohadillas correspondientes. Tenga cuidado y no deslice el dado debajo de los pasadores, ya que es muy fácil romperlos. A continuación, conecte el USBtinyISP a la plantilla y a la computadora.
Abra el IDE de Arduino, cargue el boceto de tinyDice y seleccione el chip atTiny85 con el USBtinyISP como programador. Presione el botón de carga y verifique los dados, 2 LED deberían comenzar a parpadear por un tiempo. Si todo tiene éxito, ahora el tinyDice está programado, terminado y listo para usar. Repita el proceso de programación para todas las unidades que hizo y luego guarde la plantilla completamente ensamblada para proteger los pines de pogo.
El código:
El programa de tinyDice es tal que primero muestra una animación de "pensamiento" y luego genera un número aleatorio entre 0 y 9 que se muestra durante unos segundos. Todas las transiciones se realizan con PWM para cada LED para permitir los desvanecimientos. Después de mostrar el número y desvanecerse, el procesador entra en modo de suspensión que esencialmente detiene el consumo de batería, por lo que la batería debería durar teóricamente alrededor de 6, 000 "tiradas" de los dados.
Todo el código está estructurado alrededor de una interrupción del temporizador de 8 Khz que maneja el charlieplexing y el PWM de 10 pasos para cada LED, así como el avance de las animaciones. Las explicaciones más detalladas de cada función se comentan en el boceto de Arduino.
Conclusiones:
Los resultados de este método para la fabricación de PCB en el hogar superaron con creces mis expectativas iniciales, ya que descubrí que puede ser extremadamente confiable y producir resultados de muy alta calidad para la creación de prototipos fácil y rápida de circuitos SMD y de orificios pasantes. Debido a esto, animo a los aficionados al bricolaje a que prueben este método para sus propios diseños y compartan sus resultados y hallazgos con la comunidad.
Esta nueva versión de tinyDice es en sí misma un objeto muy agradable y divertido para tener y compartir con amigos, ya que las animaciones y el estuche del llavero lo hacen bastante único e interesante. Espero que les haya gustado este instructivo y por favor compartan sus comentarios y experiencias sobre el tema para que el método continúe evolucionando. Además, siéntase libre de experimentar con el código y compartir cualquier variación interesante para que otros la prueben.
Esta guía está en el concurso de diseño de PCB, así que vote por ella si la considera digna y compártala con sus amigos y entusiastas de la electrónica por igual.
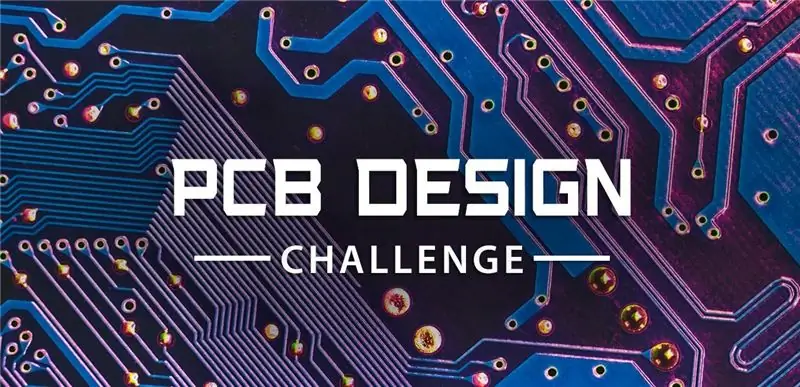
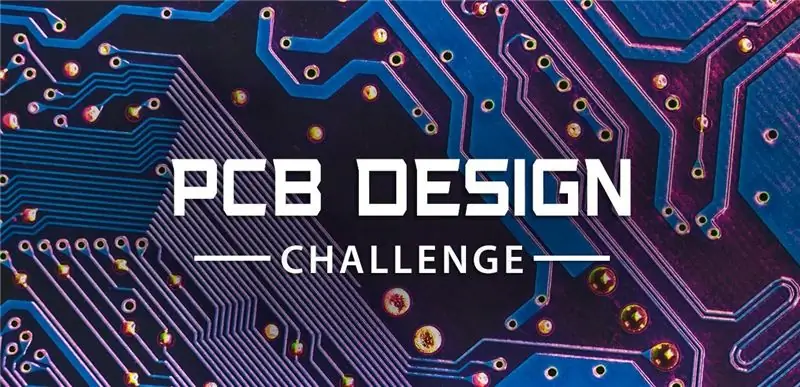
Segundo premio en el PCB Design Challenge
Recomendado:
Instrucciones sobre cómo usar un cortador de vinilo MH871-MK2: 11 pasos
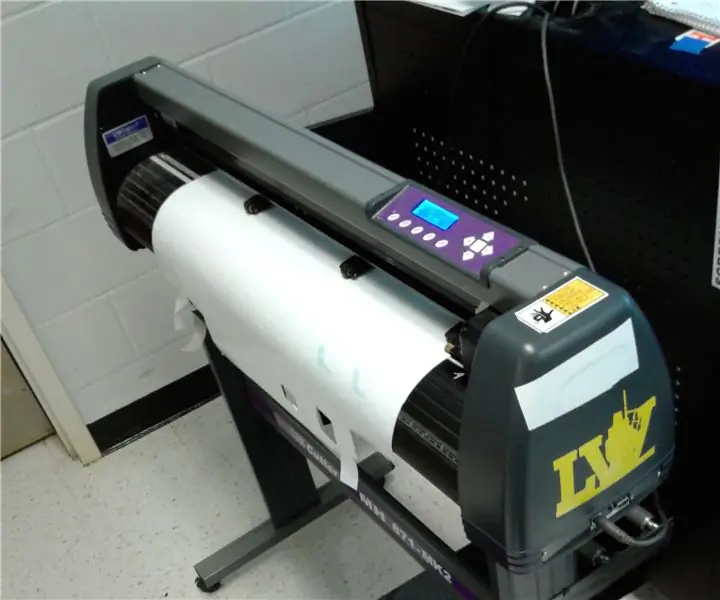
Instrucciones sobre cómo usar un cortador de vinilo MH871-MK2: Hola, mi nombre es Ricardo Greene e hice instrucciones sobre cómo usar un cortador de vinilo MH871-MK2
Usar un cortador de vinilo para hacer una plantilla con aerógrafo: 5 pasos
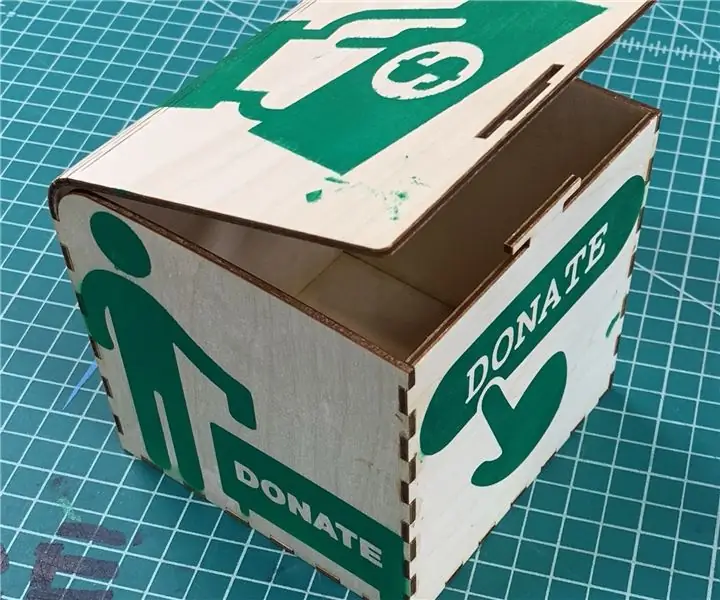
Uso de un cortador de vinilo para hacer una plantilla de aerógrafo: en este instructivo, daré una breve introducción al proceso de usar un cortador de vinilo para hacer plantillas que puede usar para pintar con una configuración de aerógrafo o, en realidad, con casi cualquier tipo de pintura. En estas fotos, usé un boo con aerógrafo
Cree PCB para aficionados con herramientas CAD profesionales modificando " Reglas de diseño ": 15 pasos (con imágenes)
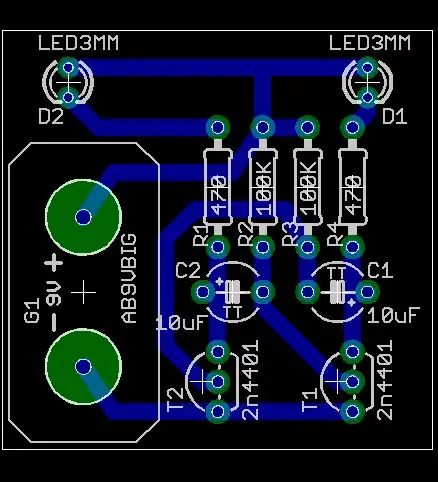
Cree PCB para aficionados con herramientas CAD profesionales modificando las " Reglas de diseño ": Es bueno que haya algunas herramientas de placa de circuito profesionales disponibles para los aficionados. Aquí hay algunos consejos para usarlos para diseñar tableros que no necesitan un fabricante profesional para HACERlos realmente
PCB profesionales casi más baratos que fabricarlos en casa: 14 pasos
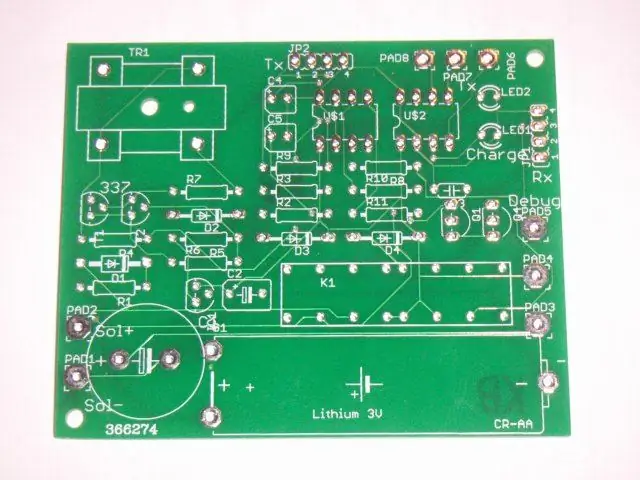
PCB profesionales casi más baratos que fabricarlos en casa: si bien hay una gran satisfacción en los PCB para la construcción de viviendas, la suma del costo de la PCB en blanco, el grabador y las brocas asciende a más de $ 4 por placa. Pero por $ 6.25 la tabla, todo se puede hacer profesionalmente. Este Instructable te lleva por
Ball of Death: o cómo aprendí a dejar de preocuparme y amar los altavoces profesionales de Apple: 11 pasos (con imágenes)
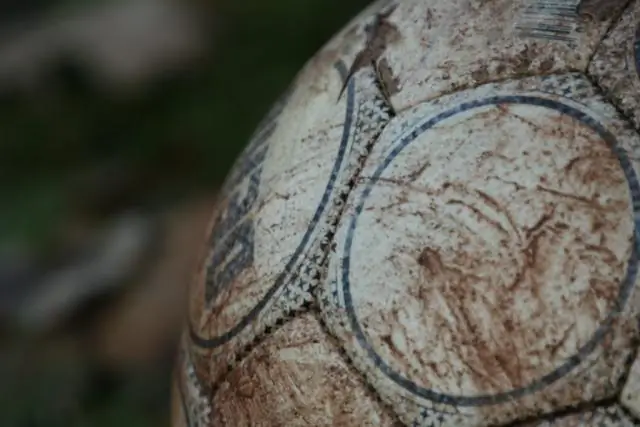
Ball of Death: o Cómo aprendí a dejar de preocuparme y amar los altavoces profesionales de Apple: Siempre he dicho que desde que deseché la " caja beige ", Apple siempre ha liderado en el área del diseño industrial. La integración de forma y función no puede ser tocada por ningún otro fabricante en ninguna industria (Porsche se acerca). Su